How Can Copper Annealing Simulation Software Shorten R&D Cycles with Digital Twins?
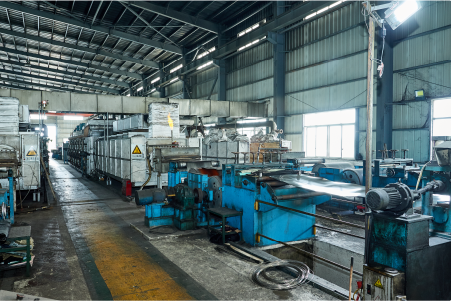
Are you struggling with long and costly R&D cycles for new copper products? The endless loop of physical prototyping, testing, and refining eats into your budget and delays your time-to-market. Imagine being able to perfect your annealing process virtually, eliminating guesswork and waste.
Copper annealing simulation software shortens R&D cycles by using digital twins—virtual replicas of your physical process. This allows for rapid virtual experimentation, prediction of material properties, and process optimization without the time, cost, and material waste of repeated physical trials, accelerating innovation significantly.
This isn't just about futuristic technology; it's a practical tool that is reshaping how leading manufacturers approach product development. By creating a virtual mirror of your annealing furnace and materials, you unlock an unprecedented level of insight and control. Let's explore how this digital revolution can directly impact your operations, making them faster, smarter, and more competitive in today's demanding market.
The leap from traditional, experience-based annealing to a data-driven, simulated approach represents a fundamental shift in manufacturing philosophy. It's about moving from reacting to problems to proactively predicting and preventing them. This requires a deeper understanding of not just the software, but the intricate interplay between the virtual model and the physical world. For instance, the accuracy of a digital twin is entirely dependent on the quality of the data it's fed—from the precise thermal dynamics of your furnace to the specific metallurgical properties of the copper alloy you're using. At AKS, we've seen firsthand that companies achieving the best results are those who view the digital twin not as a replacement for expertise, but as a powerful amplifier of it. They combine the insights from the simulation with the practical knowledge of their engineers and the real-world performance of a high-quality furnace.
What are digital twins in copper annealing simulation software?
Does the term "digital twin" sound like another abstract tech buzzword? Many companies hear the term but struggle to grasp its practical application in an industrial setting like copper annealing. This confusion can lead to missed opportunities for significant process improvements and cost savings.
In copper annealing, a digital twin is a dynamic, virtual model of a physical annealing furnace and the copper material being processed. It uses real-world data to simulate the entire heat treatment cycle, accurately predicting metallurgical outcomes like grain size, hardness, and ductility.
Moving beyond a simple definition, understanding the components and functionality of a digital twin is crucial for appreciating its transformative potential. It's not merely a 3D drawing; it's a living, data-driven replica that mirrors your actual production environment. This virtual counterpart allows your R&D team to ask "what if?" and get immediate, scientifically-backed answers. For example, a client of ours in the automotive sector was developing a new copper component that required a very specific tensile strength. Instead of spending weeks on physical trials in their Bogie Hearth Furnace, they were able to model the process. They simulated dozens of temperature and time variations in a single afternoon, identifying the optimal parameters before ever turning on the furnace for a production run1. This fusion of real-world equipment knowledge and virtual testing is where the true power lies, bridging the gap between design and flawless execution. This approach enables a level of precision and speed that traditional methods simply cannot match, giving you a decisive competitive edge.
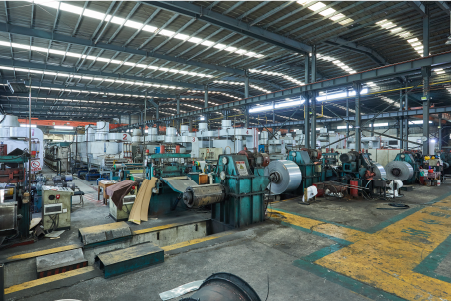
To truly grasp the concept, we must dissect the digital twin into its core components and understand how they interact to create a predictive and responsive system. It's an ecosystem of data, physics, and machine learning working in concert. The fidelity of this virtual model directly correlates with its ability to provide actionable insights, making the initial setup and data integration a critical phase. For manufacturers, this means the digital twin is not a one-size-fits-all solution but a tailored model that evolves with your physical operations.
From Blueprint to Virtual Powerhouse: The Anatomy of a Digital Twin
A digital twin begins with a high-fidelity 3D CAD model of the physical asset—in this case, an industrial furnace like our AKS Bell-Type Annealing Furnace. But this is just the skeleton. The real power comes from layering it with physical data and behavioral models. This includes the furnace's thermal properties, the location and specifications of heating elements, the precise mechanics of the cooling system, and the flow dynamics of the protective atmosphere. We provide our clients with extensive technical specifications to ensure this foundational model is as accurate as possible.
The second critical element is the material model. For copper annealing, this means a comprehensive database of the specific copper alloy's properties: its thermal conductivity, specific heat, emissivity, and—most importantly—how its microstructure evolves in response to heat. This data, often sourced from academic research and internal testing, allows the simulation to accurately predict changes in grain size, hardness, and residual stress.
Finally, a physics-based simulation engine ties it all together. This engine solves complex heat transfer and metallurgical phase transformation equations in real-time. It calculates how heat radiates from the elements, conducts through the furnace structure and the copper coil, and is removed by the cooling system. This multi-physics approach is what allows the twin to behave just like its real-world counterpart, providing a reliable platform for virtual experimentation.
The Live Connection: How Real-Time Data Creates a "Living" Model
A static model is useful, but a living digital twin is revolutionary. This is achieved by integrating the virtual model with the physical furnace through Industrial Internet of Things (IIoT) sensors. Temperature probes, gas flow meters, and pressure sensors on the actual furnace continuously stream operational data to the digital twin. This real-time feedback loop allows the twin to do two things: calibrate itself for greater accuracy and reflect the current state of the physical asset.
Consider a client producing high-frequency copper strips for the electronics industry using one of our Bright Annealing Furnaces. Sensors on the furnace track the strip's temperature profile as it moves through the heating and cooling zones. This data is fed back to the digital twin, which compares the simulated temperature profile to the actual one. If there's a discrepancy, the model can be fine-tuned.
Over time, this continuous synchronization allows the digital twin to account for real-world factors that are difficult to model from theory alone, such as minor heat loss from aging insulation or slight variations in protective atmosphere composition. The twin becomes an ever-more-accurate mirror of reality, learning and adapting alongside the physical furnace.
Predictive vs. Operational Twins: A Functional Comparison
It's important to distinguish between the two primary applications of digital twins in this context: predictive twins for R&D and operational twins for production optimization. While they share the same core technology, their objectives and data flows differ significantly. The predictive twin is the R&D engineer's sandbox, while the operational twin is the plant manager's co-pilot.
A predictive twin is used before production. Its main goal is to simulate new processes, test different copper alloys, and optimize parameters for a product that hasn't been made yet. It relies heavily on theoretical models and material property databases. An operational twin, by contrast, is used during production. It uses live sensor data to monitor the ongoing process, predict outcomes for the batch currently in the furnace, and suggest real-time adjustments to maintain quality and efficiency.
Here’s a breakdown of the key differences:
Feature | Predictive Digital Twin (R&D) | Operational Digital Twin (Production) |
---|---|---|
Primary Goal | Process Design & Optimization | Process Monitoring & Real-Time Control |
Key Users | R&D Engineers, Metallurgists | Plant Managers, Process Engineers |
Primary Data Input | Material Properties, CAD Models | Live Sensor Data, Production Schedule |
Typical Output | Optimized Process Parameters | Quality Predictions, Control Adjustments |
Use Case Example | Developing an annealing cycle for a new alloy | Adjusting furnace temperature for a current batch |
Understanding this distinction helps a company deploy the right type of digital twin for the right task, maximizing the return on their technology investment.
Digital twins reduce R&D costsTrue
By simulating annealing processes virtually, companies avoid the material waste and repeated physical trials of traditional R&D.
Digital twins replace human expertiseFalse
Digital twins amplify rather than replace engineering expertise, combining simulation insights with practical furnace knowledge.
How do digital twins impact the efficiency of R&D cycles?
Is your R&D team stuck in a frustrating cycle of endless physical prototypes? The "build, test, fail, repeat" method is not only slow but also incredibly wasteful, consuming valuable materials, energy, and man-hours. This inefficiency directly impacts your ability to innovate and compete.
Digital twins dramatically improve R&D efficiency by replacing most physical trials with rapid virtual simulations. This allows for parallel testing of numerous variables, accurate prediction of outcomes, and early identification of potential failures, ultimately slashing development timelines and reducing material waste.
The impact of this shift from physical to virtual testing is profound. It’s about compressing a development timeline that once took months into a matter of weeks, or even days. By creating a virtual sandbox, you empower your engineers to experiment boldly without the fear of costly failures. I recall working with a manufacturer of specialized copper wiring. They were tasked with developing a product that could withstand higher temperatures for a new generation of electric vehicle motors. The alloy was new and its annealing behavior was unknown. Using a digital twin of their continuous annealing line, they were able to simulate over 200 different heating and cooling profiles2 in a week. To perform the same number of tests physically would have been unthinkable—it would have taken over a year and generated tons of scrap material. This is the kind of step-change in efficiency that digital twins deliver, transforming R&D from a bottleneck into a strategic advantage.
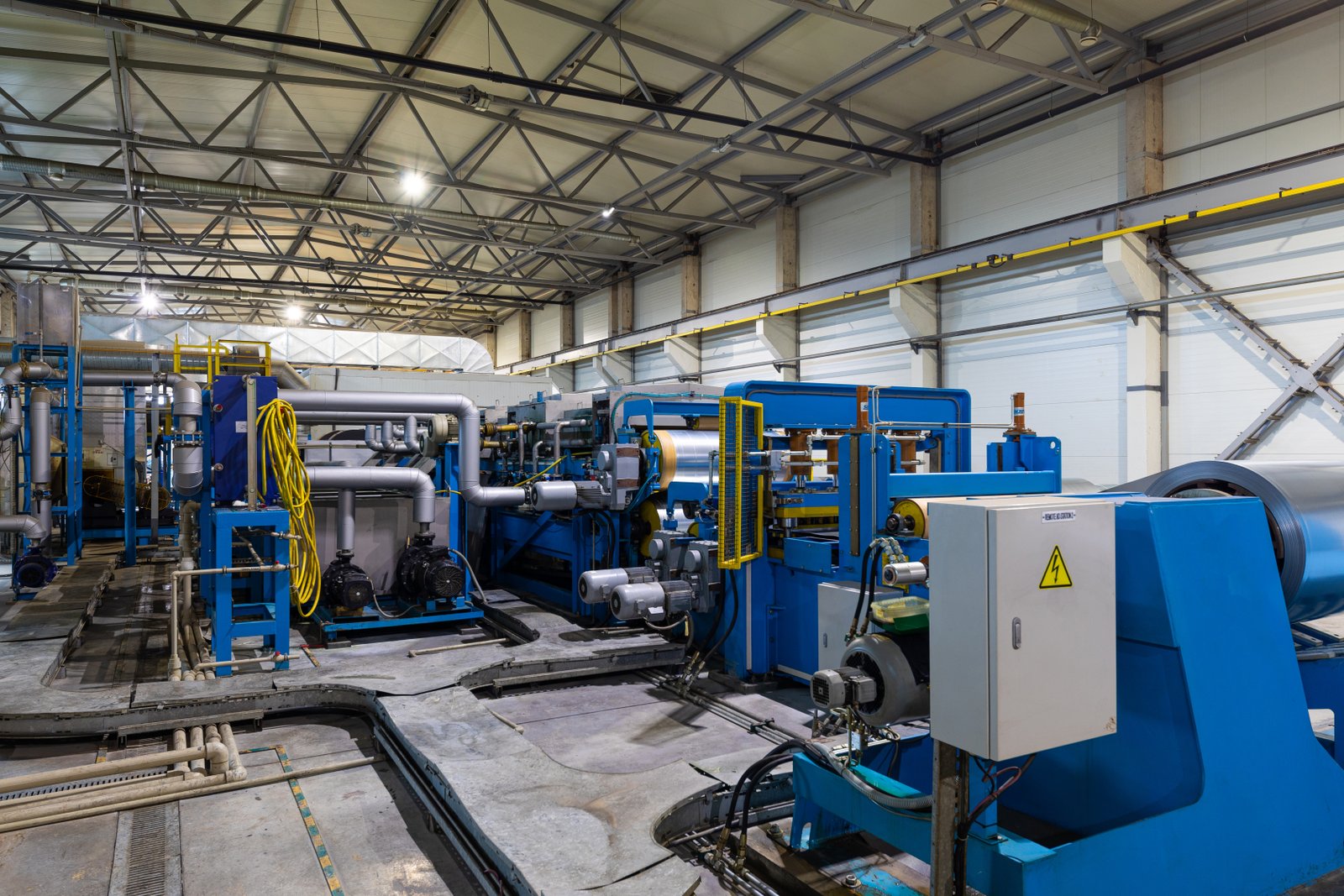
The efficiency gains from implementing digital twins in R&D are not incremental; they are transformative. This technology fundamentally alters the workflow, economics, and speed of product development. By virtualizing the most time-consuming and resource-intensive stages of R&D, companies can reallocate resources from repetitive testing to genuine innovation3. This acceleration is achieved through a multi-faceted impact on the entire development lifecycle, from initial concept validation to final parameter optimization, de-risking the entire process.
The Demise of Trial-and-Error: Virtual Prototyping in Action
The traditional R&D process for a new copper product is inherently linear and slow. An engineer proposes a set of annealing parameters, a physical sample is prepared, it runs through the furnace, and then it undergoes extensive metallurgical testing. If it fails, the entire cycle repeats. A digital twin shatters this linear model by enabling massive parallel experimentation. Your team can simultaneously test hundreds of virtual prototypes, each with slightly different parameters.
Imagine a client using an AKS Mesh Belt Furnace4 to anneal small copper connectors for the 5G telecom industry. The client needs to achieve a precise balance of conductivity and springiness. Using a digital twin, they can create a virtual test matrix. Axis one could be furnace temperature (from 400°C to 700°C in 10° increments), axis two could be belt speed (from 1m/min to 5m/min), and axis three could be the protective atmosphere composition. The software can run all these combinations overnight.
The result is a comprehensive performance map that shows exactly how each parameter affects the final product properties. Instead of a few data points from a handful of physical tests, the engineers get a complete picture of the process window5. This allows them to confidently select the optimal parameters on the first try, reducing physical prototype iterations by what some studies suggest can be as much as 70-80%.
De-Risking Innovation: Predicting Material Failures Before They Occur
One of the biggest hidden costs in R&D is the "unknown unknown"—the unexpected failure that sends you back to the drawing board. Digital twins act as an early warning system, predicting potential issues like uneven grain growth, surface oxidation, or excessive residual stress long before you commit to a physical run. The simulation's physics engine can forecast how heat will be distributed throughout a complex part or a tightly wound coil.
For instance, a customer using one of our large Bogie Hearth Furnaces for annealing heavy copper busbars faced a challenge with thermal uniformity. The thick cross-section of the busbars meant the core would heat up much slower than the surface. A traditional approach would involve extensive, costly trials with thermocouples embedded in the product.
With a digital twin, they could visualize the heat distribution in 3D over time. The simulation predicted that their proposed heating cycle would result in a coarse grain structure at the surface and an under-annealed core, leading to inconsistent mechanical and electrical properties. By visualizing this failure virtually, they were able to redesign the heating and soaking stages of the cycle, ensuring uniform properties throughout the final product and completely avoiding the production of expensive, non-conforming material.
Accelerating Parameter Optimization with Data-Driven Certainty
Once a basic process is established, the final stage of R&D is often a painstaking optimization process. This involves making small tweaks to find the absolute best settings for quality and throughput. This phase can be incredibly time-consuming. A digital twin transforms this process from an art into a science, using data to pinpoint the optimal operating window with mathematical precision.
This is especially valuable when balancing competing objectives, a common scenario in manufacturing. For example, a producer of bright annealed stainless steel (a process for which our furnaces are well-known, and the principles are similar for copper) wants to maximize throughput (higher belt speed) while minimizing energy consumption (lower temperature) and ensuring a specific surface brightness (requiring a precise atmosphere). These goals are often in conflict.
A digital twin can run an optimization algorithm to navigate these trade-offs. By simulating thousands of combinations, it can generate a "Pareto front," a curve showing the optimal set of solutions where you can't improve one objective without worsening another. This gives engineers a clear, data-backed choice. Below is a simplified comparison of a traditional R&D timeline versus one augmented with a digital twin for a new copper alloy.
R&D Stage | Traditional Timeline (Weeks) | Digital Twin Timeline (Weeks) |
---|---|---|
Initial Parameter Hypothesis | 1 | 0.5 |
Physical Prototyping (Est. 10 iterations) | 10 | 2 (for validation only) |
Metallurgical Testing & Analysis | 5 | 1 |
Process Optimization & Refinement | 4 | 1 |
Total R&D Cycle Time | 20 Weeks | 4.5 Weeks |
This dramatic compression of the R&D timeline is the ultimate competitive advantage, allowing companies to respond to market demands and launch new products faster than their rivals.
Digital twins enable parallel testingTrue
Digital twins allow simultaneous testing of hundreds of parameter combinations, unlike sequential physical prototyping.
Physical prototypes are more accurateFalse
Modern digital twins with physics engines can predict material behaviors with equal or greater accuracy than physical tests.
What are the key benefits of using simulation software for copper annealing?
Are you looking for ways to gain a real competitive advantage? Simply having a good furnace isn't always enough in a market that demands constant innovation and efficiency. Relying on old methods can leave you falling behind competitors who are adopting smarter technologies.
The key benefits include drastically reduced R&D costs and time-to-market by minimizing physical trials. It also leads to improved product quality and consistency through precise process control, increased energy efficiency by optimizing furnace settings, and enhanced operator knowledge through visualization.
These benefits create a powerful ripple effect across your entire operation, touching everything from your bottom line to your product's performance in the field. It’s about more than just saving money on scrap material; it's about building a more resilient, intelligent, and agile manufacturing process. When you can precisely predict how a specific copper coil will behave in one of our Bell-Type Annealing Furnaces6, for instance, you're not just annealing metal—you're engineering certainty. You're guaranteeing that the material you ship to your customer meets their exact specifications every single time. This level of quality control and predictability elevates your brand and builds lasting customer trust, which is the ultimate goal of any manufacturing enterprise. The software acts as a bridge, translating your design intent into a tangible, high-quality product with maximum efficiency.
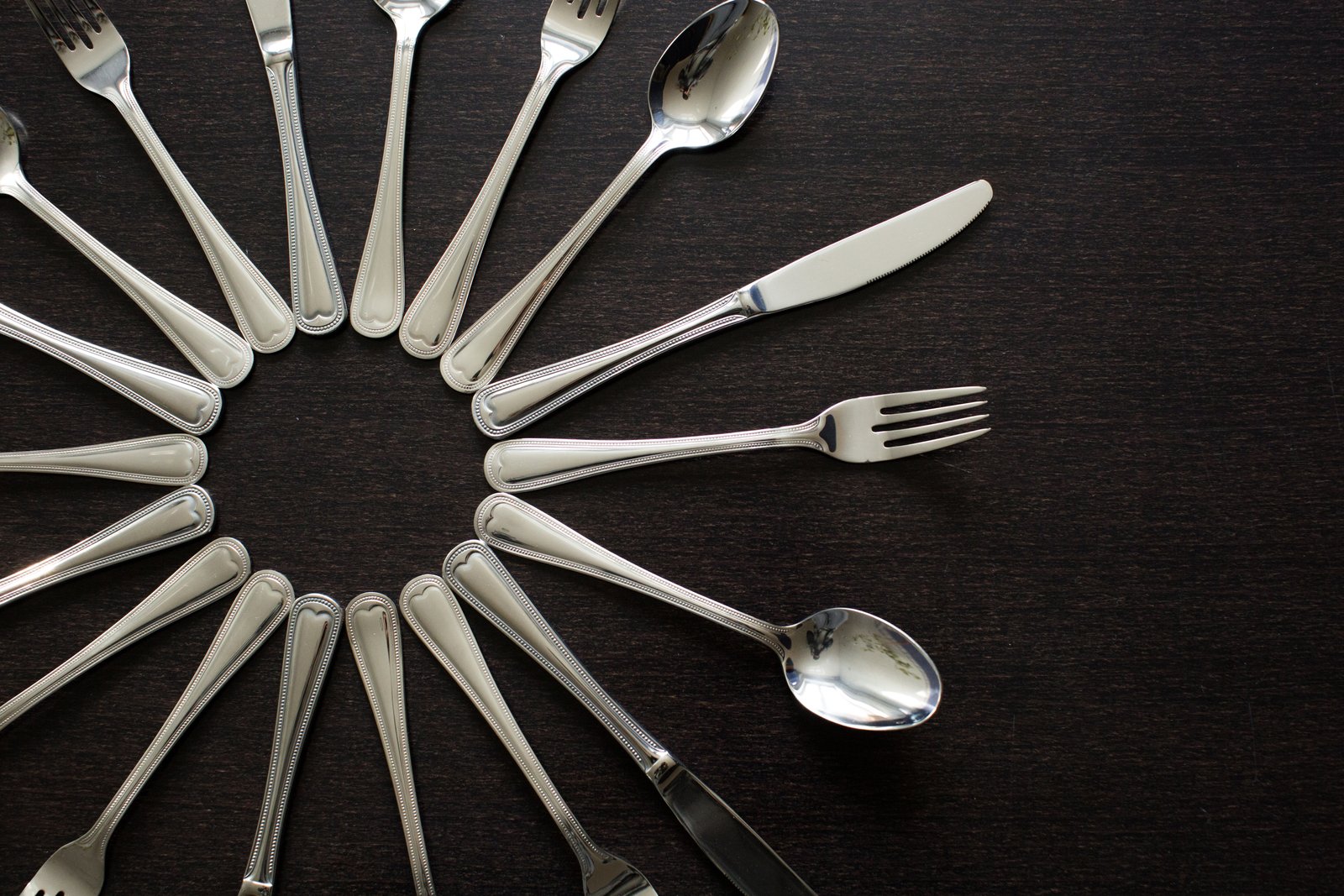
The adoption of copper annealing simulation software7 offers a suite of strategic advantages that extend far beyond the R&D lab. These benefits compound over time, leading to a more robust and profitable operation. By leveraging predictive analytics, companies can optimize every facet of the annealing process, from resource consumption to final product quality. This holistic improvement is what makes simulation a cornerstone of modern, competitive manufacturing, creating a virtuous cycle of efficiency and innovation.
Financial Gains: A Drastic Reduction in Operational and R&D Costs
The most immediate and quantifiable benefit of simulation software lies in cost reduction. The first area of savings is raw materials. Every failed physical trial results in scrap copper, which, while recyclable, represents a significant loss in terms of the energy and labor already invested. By getting the process right virtually, the number of physical trials can be cut by over 70%, leading to a direct and substantial reduction in material waste.
The second major financial benefit comes from energy savings. Our AKS furnaces are designed with advanced energy-saving systems, but simulation software can optimize their use even further. By simulating different heating cycles, a company can identify the most energy-efficient temperature profile that still achieves the desired metallurgical properties. This might involve finding the lowest possible annealing temperature or the shortest possible soaking time, trimming kilowatt-hours off every single production run. Over a year, these energy savings can amount to a significant figure.
ly, there's the reduction in labor and machine time costs associated with R&D. An annealing furnace is a key production asset. When it's being used for R&D trials, it's not producing saleable products. Simulation frees up your valuable furnace capacity for revenue-generating activities, directly boosting your operational efficiency and profitability.
Quality and Consistency: Engineering the Perfect Microstructure
Product quality is paramount in the copper industry, where even slight deviations in mechanical or electrical properties can lead to component failure. Simulation software provides an unprecedented level of control over the final product quality by allowing engineers to precisely target and achieve the desired microstructure. They can visualize and quantify the effects of process changes on grain size, which is a key determinant of hardness, ductility, and formability.
Consider a client manufacturing copper foil for lithium-ion batteries. The consistency of the foil's grain structure is critical for battery performance and safety. Using a digital twin of their AKS Bright Annealing Furnace, they can simulate the process to ensure a uniform, fine-grain structure across the entire width and length of the foil coil. The simulation can predict and help mitigate issues like "edge effect," where the edges of the coil heat or cool at a different rate than the center.
This ability to engineer the microstructure with precision leads to a more consistent product, batch after batch. This reduces quality-related rejections, enhances customer satisfaction, and builds a reputation for reliability. It transforms quality control from a reactive inspection process into a proactive design parameter.
Strategic Advantage: Unlocking Innovation and Speed-to-Market
In today's fast-paced markets, being first is often as important as being best. Simulation software provides a critical strategic advantage by dramatically accelerating the speed-to-market for new products. As demonstrated in the R&D efficiency section, development cycles can be shortened from many months to just a few weeks. This agility allows a company to respond rapidly to new customer requirements or emerging market trends.
This speed also fosters a culture of innovation. When the cost and time associated with experimentation are low, engineers are more likely to explore novel ideas and push the boundaries of what's possible. They can test unconventional alloys or ambitious process parameters without risking expensive equipment or materials. This freedom to innovate is essential for long-term growth and market leadership.
The table below quantifies the typical performance improvements observed by manufacturers after implementing annealing simulation software, based on industry reports and our client feedback.
Performance Metric | Traditional Process (Baseline) | Process with Simulation Software | Improvement |
---|---|---|---|
Time-to-Market for New Product | 9 Months | 2 Months | -78% |
R&D Physical Trials | 15-20 | 2-3 (for validation) | -85% |
Scrap Rate from R&D | 5-8% of material used | <1% of material used | -90% |
Energy Consumption per Ton | 380 kWh | 350 kWh (Optimized Cycle) | -8% |
Product Rejection Rate | 2.5% | <0.5% | -80% |
These figures clearly illustrate that simulation is not just an R&D tool but a comprehensive business optimization strategy that delivers tangible results across the board.
Simulation reduces physical trials by 70%True
The article states that simulation can cut physical trials by over 70%, drastically reducing material waste and R&D costs.
Simulation increases energy consumptionFalse
The text explains simulation optimizes furnace settings, reducing energy consumption by 8% per ton through efficient temperature profiles.
How can companies effectively implement digital twins in their R&D processes?
Are you convinced of the power of digital twins but unsure where to start? The prospect of implementing such a sophisticated technology can be daunting, and a poor strategy can lead to wasted investment and frustration, preventing you from realizing the promised benefits.
Effective implementation requires a phased approach. Start with a pilot project on a single, well-understood process. Ensure high-quality data collection from the physical asset, invest in training your team, and foster collaboration between your R&D, operations, and IT departments.
Successfully integrating a digital twin is as much about people and processes as it is about technology. It’s a cultural shift towards data-driven decision-making. At AKS8, we guide our clients to see this not as a single, massive overhaul, but as an incremental journey. It begins with identifying a high-impact, manageable problem to solve—for example, reducing variability in a specific product line run on a Vacuum Annealing Furnace9. By focusing on a clear goal, you can demonstrate value quickly, build momentum, and secure buy-in for broader adoption. This methodical approach de-risks the implementation process and ensures that the technology is tailored to solve your specific challenges, rather than creating new ones. It’s about building a solid foundation of data, skills, and collaborative workflows that will support your digital transformation for years to come.
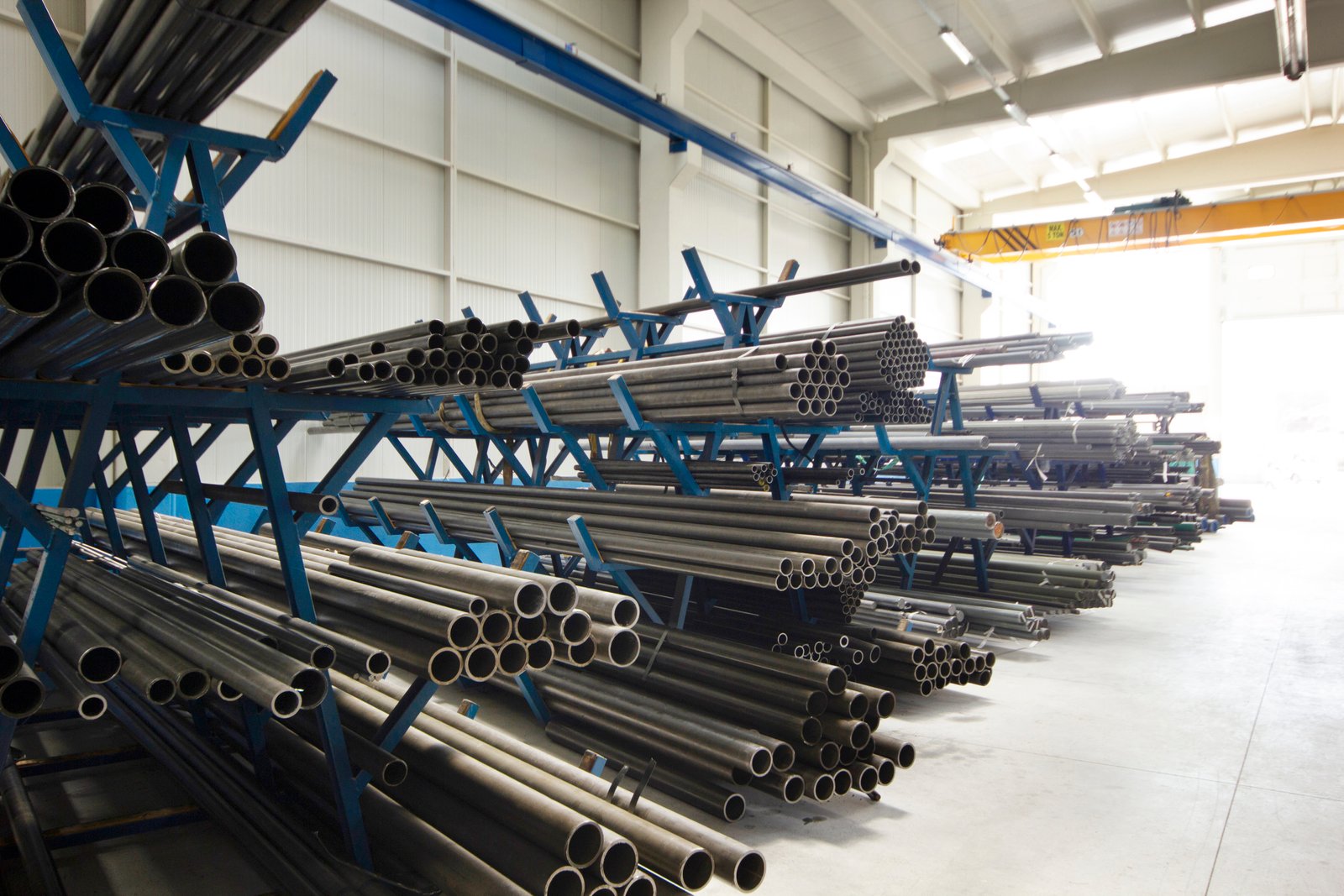
The path to successful digital twin implementation is a strategic one, requiring careful planning, cross-functional alignment, and a commitment to data quality. Simply purchasing software is not enough; companies must build a supportive ecosystem around it to unlock its full potential. This involves a clear-eyed assessment of current capabilities, a structured approach to deployment, and a long-term vision for how the technology will integrate with and enhance existing workflows. A misstep in the early stages can compromise the accuracy of the model and erode trust in the system, so a methodical, well-thought-out plan is essential.
Phase 1: Strategy, Scoping, and Data Foundation
The first and most critical step is to define a clear strategy. Don't try to boil the ocean. Instead of aiming to create a digital twin of your entire factory at once, start small. Select a single value-driving process for a pilot project. This could be your most problematic product, your most energy-intensive furnace, or the product line with the most stringent quality requirements. The ideal pilot project has a clear, measurable objective, such as "reduce cycle time by 15% for Alloy X in Furnace Y."
Once the scope is defined, the focus shifts to the data foundation. A digital twin is only as good as the data it's built on. This involves a two-pronged effort. First, gather all existing engineering data: the CAD drawings of your furnace (we provide detailed models for our AKS furnaces), the documented material properties of your copper alloys, and historical process data from your manufacturing execution system (MES).
Second, assess your live data collection capabilities. This means auditing the sensors on your physical furnace. Are the temperature, pressure, and atmosphere sensors calibrated and reliable? Is the data collected at a high enough frequency? You may need to invest in upgrading your IIoT infrastructure to ensure a steady stream of high-fidelity data that can be used to build and later validate the twin. Without a rock-solid data foundation, any subsequent steps will be built on sand.
Phase 2: Model Development, Validation, and Team Training
With the data foundation in place, the development of the virtual model can begin. This is typically done in collaboration with the simulation software provider or a specialized consultant. The process involves configuring the software to represent the geometry and physics of your specific furnace and materials. This is where the detailed technical specifications of your equipment, like an AKS Bright Annealing Furnace's advanced cooling system or waste heat recovery features, become critically important for model accuracy.
The most crucial part of this phase is validation. You cannot blindly trust the simulation's output. The model must be rigorously tested against reality. This is done by running a well-documented physical annealing cycle and comparing the results—such as the measured temperature profile and final material hardness—with the predictions from the digital twin. The model is then calibrated and tuned until its predictions reliably match the real-world outcomes within an acceptable margin of error. This validation step is what builds trust in the digital twin across the organization.
Concurrently, you must invest in your people. Your R&D engineers, metallurgists, and process operators need to be trained on how to use the software and, more importantly, how to interpret its results. This isn't just about learning which buttons to press. It's about developing "digital literacy"—the ability to think critically about the simulation's output, understand its limitations, and use it as a tool to augment their own expertise.
Phase 3: Integration, Scaling, and Continuous Improvement
Once the pilot project has been validated and has demonstrated clear value, the final phase is about integration and scaling. The digital twin should not remain a standalone tool used only by a few experts in the R&D lab. It needs to be integrated into the daily workflows of the engineering and operations teams. The insights from the simulation should become a standard part of process design reviews and production planning meetings.
Scaling involves strategically expanding the use of digital twins to other production lines or factory processes based on the lessons learned from the pilot. This creates a scalable framework for digital transformation. Perhaps the next step is to create an operational twin for real-time process control for the furnace that was the subject of the R&D pilot, or to begin a new R&D twin project for a different furnace type, like a Bell-Type furnace.
Finally, a digital twin is not a static, one-time creation. It must be part of a continuous improvement loop. As you process new alloys, as the furnace ages, or as you gather more data, the twin should be updated and re-validated to maintain its accuracy. This creates a living model that evolves with your physical operations, delivering ever-increasing value over time.
Implementation Phase | Key Objective | Critical Activities | Common Pitfall to Avoid |
---|---|---|---|
Phase 1: Foundation | Define scope and ensure data quality. | Select a pilot project, audit sensors, consolidate engineering data. | An overly ambitious scope ("boil the ocean"). |
Phase 2: Development | Build a trusted, accurate model. | Configure software, run validation tests, calibrate the model, train the team. | Insufficient validation, leading to lack of trust. |
Phase 3: Integration | Embed the twin into daily workflows. | Develop new standard operating procedures, scale to other lines, update the model. | Leaving the twin as a siloed "expert tool." |
By following this structured, three-phase approach, companies can navigate the complexities of implementation and successfully harness the power of digital twins to revolutionize their R&D processes.
Digital twins require high-quality dataTrue
The accuracy of a digital twin depends on reliable, high-fidelity data from physical assets and sensors.
Digital twins are one-time projectsFalse
Digital twins require continuous updates and validation to remain accurate as physical systems evolve.
What best practices should be followed when utilizing copper annealing simulation software?
You've invested in the software and are ready to go, but how do you ensure you're getting the absolute most out of it? Using powerful software without a clear set of best practices can lead to inconsistent results and missed opportunities for optimization.
Best practices include starting with accurate material data, rigorously validating the simulation against real-world results, and fostering a collaborative environment where engineers and operators trust the data. It's also vital to use the software for continuous improvement, not just one-off projects.
Adhering to these principles transforms the software from a simple predictive tool into a cornerstone of your operational excellence strategy10. It's about creating a disciplined, scientific approach to a process that was once considered an art. For example, one of our clients, a top-tier supplier of copper components, established a "digital twin committee" that meets weekly. This group, composed of R&D engineers, furnace operators, and quality managers, reviews the simulation results against actual production data from their AKS furnaces. This practice not only ensures the model's accuracy remains high but also fosters a culture of shared ownership and continuous learning. It breaks down silos and ensures that the insights generated by the software11 are immediately translated into real-world process improvements, maximizing the return on their technology investment.
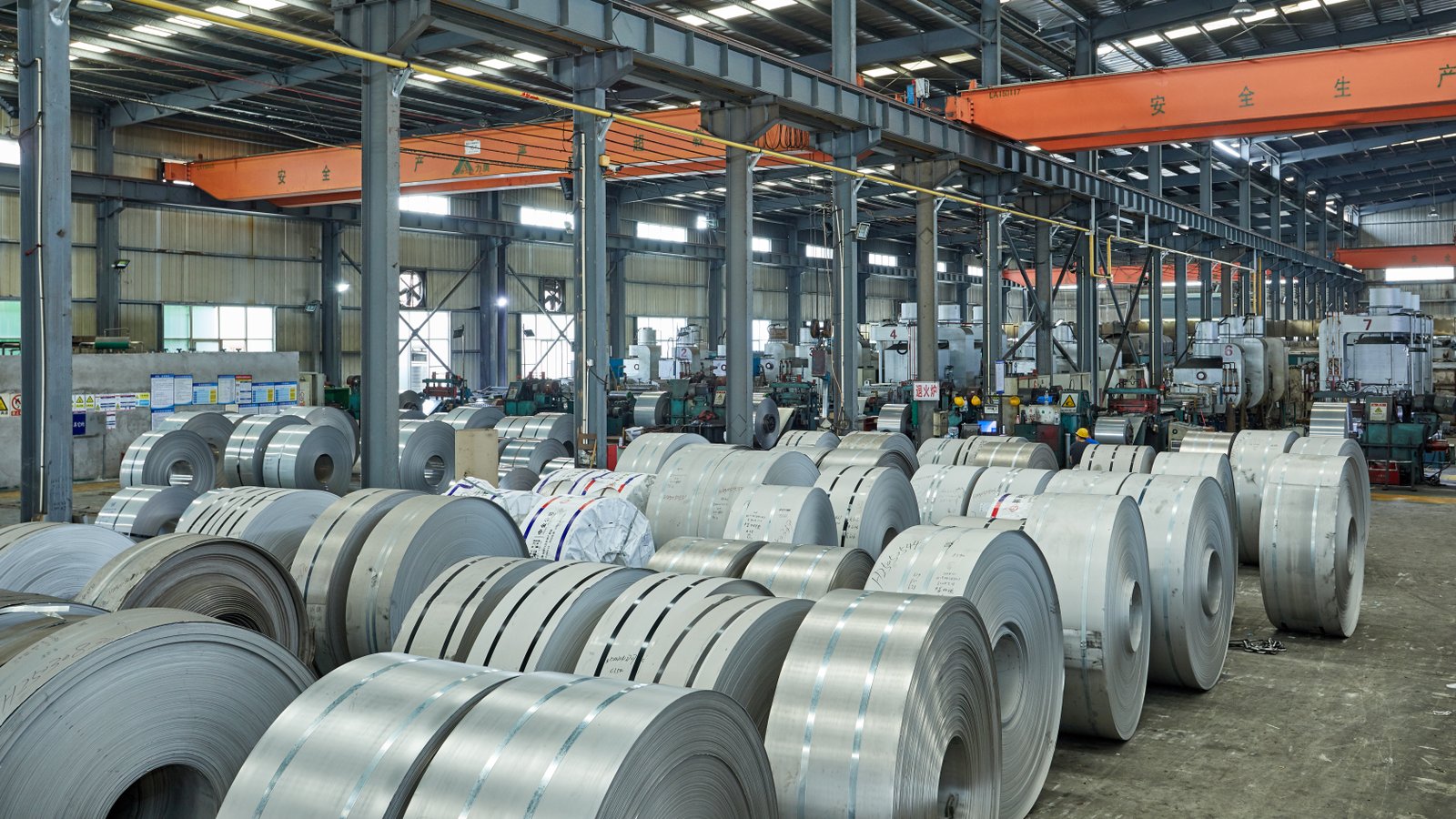
To truly master copper annealing simulation, companies must adopt a set of best practices that govern how the technology is used, maintained, and integrated into the corporate culture. These practices ensure that the simulation's results are reliable, the insights are actionable, and the benefits are sustained over the long term. It's about building a robust framework of procedures and standards that maximize the value derived from this powerful tool, turning it into a lasting competitive advantage.
Garbage In, Gospel Out: The Primacy of Data Integrity
The single most important best practice is an unwavering commitment to data quality. The adage "garbage in, garbage out" has never been more relevant. A simulation's predictions are entirely dependent on the accuracy of the data it is fed. This starts with the material properties. Don't rely on generic, textbook values for your specific copper alloy. Invest in proper characterization to get precise data for thermal conductivity, specific heat, and stress-strain behavior at different temperatures.
This principle extends to the physical asset's data. The CAD model of the furnace must be an exact match of the real thing, including the precise location of heating elements, thermocouples, and gas inlets. For our AKS furnace clients, we provide detailed engineering drawings to facilitate this. Furthermore, the live data from sensors must be constantly monitored for drift or error. A regular calibration schedule for all instrumentation is not just good practice—it's essential for the digital twin's continued reliability.
Lastly, maintain a centralized and version-controlled database for all this information. When an engineer starts a new simulation, they should be drawing from a trusted, up-to-date library of material and asset data, ensuring consistency and comparability across all projects.
Trust but Verify: The Discipline of Model Validation
A simulation should never be trusted blindly. The second core best practice is to establish a rigorous and continuous validation protocol. The initial validation, where the model is calibrated against a baseline physical test, is just the beginning. This process should be repeated periodically and whenever a significant change is made—for instance, if a new batch of raw material with slightly different chemistry is introduced, or after major furnace maintenance.
This process builds and maintains trust in the model. When operators and engineers see for themselves that the twin's predictions consistently match reality, they will be more likely to rely on its guidance for critical decisions. One effective method is to "blind-test" the model. Have the simulation predict the outcome of a new annealing cycle, run the physical test without the operator knowing the prediction, and then compare the results. Consistent success in these blind tests provides the ultimate proof of the model's value.
This discipline also helps in understanding the model's boundaries. No simulation is perfect. The validation process will help you define the operating window within which the model is highly accurate and identify scenarios where its predictions might be less reliable. This knowledge is crucial for using the tool responsibly.
Beyond the Lab: Fostering a Culture of Collaboration
For simulation software to be truly effective, it cannot be the exclusive domain of a few PhDs in the R&D department. The insights it generates must be shared, understood, and utilized across functions. This requires fostering a culture of collaboration between R&D, operations, and quality control.
R&D engineers can use the simulation to design a new process, but it's the furnace operators who have the hands-on experience to know if that process is practical on the factory floor. Create formal channels for feedback. Operators should be encouraged to report any discrepancies they observe between the simulation's predictions and what they see happening in the furnace. This real-world feedback is invaluable for refining the model.
Similarly, the quality department's data on final product properties is the ultimate measure of success. This data should be systematically fed back into the continuous improvement loop for the digital twin. The table below outlines a simple RACI (Responsible, Accountable, Consulted, Informed) chart for managing the digital twin, a useful tool for formalizing this collaboration.
Activity | R&D Engineer | Furnace Operator | Quality Manager | IT Department |
---|---|---|---|---|
Running New Simulations | R | A | C | I |
Initial Model Validation | R | C | A | I |
Routine Data Calibration | I | A | C | R |
Updating Material Database | A | I | C | R |
Interpreting Results | A | C | C | I |
By establishing clear roles and encouraging open communication, you ensure that the digital twin becomes a shared asset that drives collective success, rather than a siloed tool that creates friction. This collaborative approach is the key to unlocking its full, transformative potential.
Material data must be accurateTrue
Simulation accuracy depends on precise material properties like thermal conductivity and specific heat.
Generic textbook values are sufficientFalse
Each copper alloy requires specific characterization - textbook values lack necessary precision.
Conclusion
Ultimately, integrating copper annealing simulation software with digital twins is a strategic imperative for modern manufacturers. It transforms R&D from a slow, costly process into a rapid, data-driven engine for innovation, directly leading to better products, lower costs, and a faster time-to-market.
-
Explore advantages of using digital twins for optimizing copper production processes ↩
-
Learn how heating and cooling profiles aid in efficient virtual testing ↩
-
Discover the transformative impact of digital twins on R&D innovation ↩
-
Understand how the AKS Mesh Belt Furnace enhances annealing efficiency ↩
-
Find out how process window mapping helps in optimizing manufacturing parameters ↩
-
Learn how Bell-Type Annealing Furnaces improve metal treatment precision ↩
-
Discover how simulation software boosts efficiency and product quality in annealing processes ↩
-
Learn how AKS integrates digital twins into their manufacturing strategies ↩
-
Discover the advantages Vacuum Annealing Furnaces bring to production efficiency ↩
-
Learn how simulation tools can enhance operational efficiency and achieve excellence in engineering processes. ↩
-
Discover the benefits of integrating simulation insights for manufacturing process improvements. ↩