How Can Low-Carbon Heating Technologies Make Copper Annealing More Sustainable?
The copper industry is under immense pressure to decarbonize, yet traditional annealing processes remain heavily reliant on fossil fuels. This dependence creates a significant carbon footprint, drives up energy costs, and exposes businesses to regulatory risks. What if you could adopt low-carbon technologies that boost sustainability and profitability simultaneously?
Low-carbon heating technologies make copper annealing more sustainable by replacing fossil fuel combustion with cleaner alternatives like electrification or green hydrogen. Advanced furnace designs further enhance this by integrating superior insulation and waste heat recovery systems, drastically reducing energy consumption and eliminating direct CO2 emissions at the source.
Transitioning to sustainable practices can feel daunting, but it's a journey that begins with understanding the available pathways. It’s not merely about meeting new regulations; it’s about building a more resilient, efficient, and competitive operation for the future. In my years of experience, I’ve seen how strategic investments in modern heating technology can transform a business's environmental and financial performance.
The shift toward sustainability presents a classic industrial dilemma: balancing immediate operational needs and capital constraints against long-term environmental goals and market pressures. Many manufacturers I speak with are caught between the proven reliability of their legacy gas-fired furnaces and the perceived complexities of adopting new technologies. However, data from industry leaders and reports from organizations like the International Copper Association1 show a clear trend. A 2022 study highlighted that industrial heat processes account for nearly two-thirds of industrial energy demand, with the majority sourced from fossil fuels. By engineering solutions that bridge this gap—like hybrid furnaces or retrofittable waste heat recovery systems—we at AKS are proving that sustainability and practicality are not mutually exclusive. This isn't an abstract environmental debate; it's a strategic business decision that directly impacts everything from energy bills to a company’s ability to compete in a global market that increasingly values green credentials.
What is the current state of copper annealing in terms of sustainability?
Many copper producers I talk to believe their annealing processes are efficient enough, often unaware of the hidden costs accumulating from energy waste and carbon emissions. This complacency can be costly, leading to unnecessarily high operational expenses and leaving them vulnerable as competitors gain a market edge by innovating. By taking a clear-eyed look at the current state of your annealing process, you can uncover powerful opportunities to improve both sustainability and your bottom line.
Currently, the copper annealing industry largely relies on natural gas-fired furnaces, a practice that results in significant direct CO2 emissions and high energy consumption. While this traditional method is well-established, it is increasingly misaligned with global sustainability goals, pushing the industry towards a critical transition to electrification and advanced efficiency technologies.
This industry-wide reliance on legacy systems has created a powerful inertia. For decades, the mantra has been, "If it ain't broke, don't fix it." But from the perspective of modern energy costs and environmental stewardship, the old system is broken. I recall visiting a prospective client, a well-established copper tube manufacturer in Southeast Asia. They were struggling with skyrocketing energy bills and assumed it was just a consequence of volatile market prices. After a thorough audit of their facility, we pinpointed the real culprit: a 25-year-old annealing furnace that was hemorrhaging heat. Its insulation was degraded, and it lacked any form of heat recovery. They were essentially paying to heat the factory air. This experience highlights a crucial point: understanding the "current state" of sustainability is not just about acknowledging fossil fuel use. It requires a detailed, honest assessment of your specific operational inefficiencies. This diagnostic phase is the bedrock of any successful transition, and it's precisely where our team at AKS begins when helping clients forge a path toward a more sustainable and profitable future.
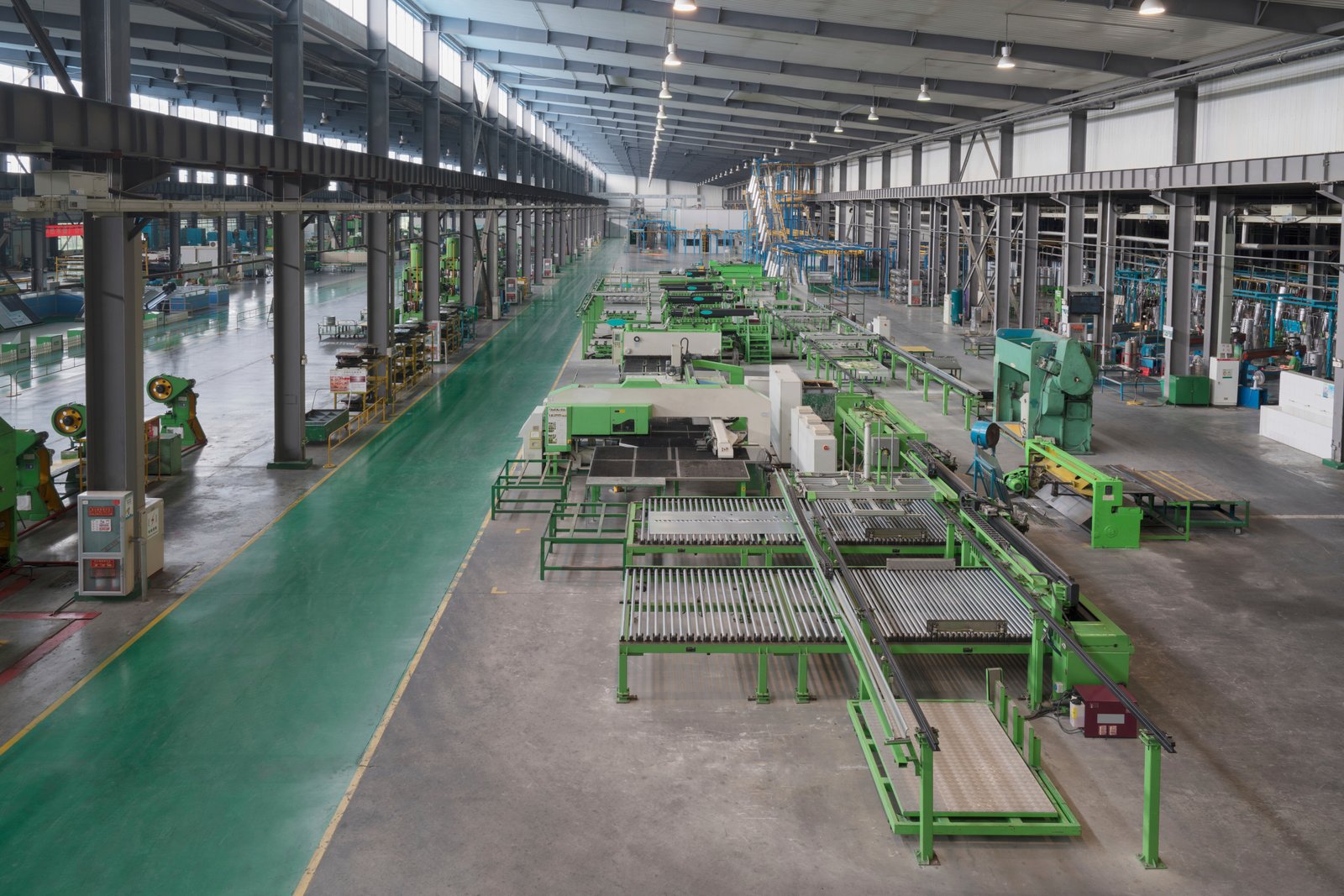
The Dominance of Fossil Fuels and Its Economic Implications
The backbone of traditional copper annealing has long been the natural gas-fired furnace. Its historical prevalence is easy to understand; natural gas was, for many years, an inexpensive, reliable, and readily available fuel source. The technology is mature, and operators are familiar with its nuances. However, this dependence has become a significant liability. The industrial sector is a colossal energy consumer, and heat treatment processes like annealing are among the most intensive. A standard, older furnace can consume upwards of 400-500 kWh of energy equivalent per ton of copper processed, directly linking production volume to substantial fossil fuel consumption.
This direct link now translates into severe economic pressure. In recent years, global natural gas prices have experienced unprecedented volatility, and carbon pricing mechanisms are expanding across jurisdictions. For many of our clients, energy has transformed from a predictable operational cost into a major financial variable that erodes profitability. I worked with a company in India that produces high-quality copper strips for the electronics sector. A cost analysis revealed that their energy expenditure for annealing had ballooned to become their second-highest operational cost, right after the raw copper itself. This made it incredibly difficult to maintain competitive pricing on their products, forcing them to confront the inefficiency of their legacy heating systems.
The story is the same across many industries: what was once an economic advantage has become a significant risk. The reliance on fossil fuels is no longer just an environmental concern; it is a direct threat to financial stability and market competitiveness. Companies that fail to address this dependency risk being priced out of the market by more forward-thinking competitors who have already begun the transition to more efficient, cost-stable heating technologies. This economic reality is often the most powerful catalyst for change.
Assessing Energy Inefficiency in Legacy Systems
Legacy annealing furnaces are often rife with inefficiencies that go unnoticed in day-to-day operations. The primary culprit is heat loss. This occurs through inadequate insulation, poorly sealed furnace doors, and, most significantly, hot flue gases vented directly into the atmosphere. In many older designs, the combustion process itself is inefficient, with poor air-to-fuel ratio control leading to incomplete combustion and wasted fuel. These systems were designed in an era when energy was cheap, so maximizing thermal efficiency was not a primary design consideration.
The contrast with modern furnace design is stark. To illustrate this, we often present clients with a comparative analysis. A legacy furnace might operate at a thermal efficiency of 45%, meaning more than half the energy purchased is lost. A modern AKS Bright Annealing Furnace, equipped with multi-layered ceramic fiber insulation and a sophisticated waste heat recovery system, can achieve thermal efficiencies exceeding 80%. This isn't just an incremental improvement; it's a fundamental change in performance.
Характеристика | Legacy Gas Furnace | AKS Modern Bright Annealing Furnace |
---|---|---|
Тепловая эффективность | 40-55% | > 80% |
Primary Heat Loss Source | Flue gas exhaust, poor insulation | Minimal through-wall loss |
Energy Consumption | High (e.g., 450 kWh/ton) | Low (e.g., < 250 kWh/ton) |
Рекуперация отработанного тепла | None | Integrated system preheats air/strip |
CO2 Emissions | High (Direct Combustion) | Zero (Electric) or Low (Optimized Gas) |
A case in point is a European manufacturer of automotive components we partnered with. Their old batch-annealing furnace had a measured thermal efficiency below 50%. By replacing it with one of our continuous Mesh Belt Furnaces featuring a dual-layer chamber with heat exchange capabilities, they reduced their natural gas consumption by over 40%. The energy saved within the first two years alone was enough to offset a significant portion of the initial capital investment, demonstrating a clear and rapid return on investment.
The Emerging Role of Regulatory and Market Pressures
The final piece of the puzzle forcing a re-evaluation of the status quo is the convergence of regulatory and market forces. Governments worldwide are implementing stricter environmental standards. For exporters, mechanisms like the European Union's Carbon Border Adjustment Mechanism (CBAM)2 are game-changers. Under CBAM, the carbon footprint of imported goods is taxed at the border, meaning a company's inefficient, high-emission furnace in China or Southeast Asia directly impacts the final cost and competitiveness of its products in the European market.
Simultaneously, the market itself is demanding greater sustainability. Large original equipment manufacturers (OEMs) in sectors like electric vehicles, renewable energy, and consumer electronics are under pressure from their own customers and investors to decarbonize their supply chains. As a result, they are cascading these requirements down to their suppliers. We have clients who are now required to provide detailed reports on their Scope 1 and Scope 2 emissions as a condition of their contracts. A low-sustainability profile is rapidly becoming a significant commercial disadvantage.
At AKS, we see our role as more than just a furnace manufacturer; we are a strategic partner in our clients' decarbonization journey. Our R&D efforts are laser-focused on addressing these interconnected challenges. Features like our precision gas-to-air ratio control system are designed not only to save fuel but also to minimize emissions of pollutants like NOx. Our development of fully electric and hydrogen-ready furnaces is a direct response to the global push for net-zero emissions. We are building the technology that will empower our clients to navigate the evolving regulatory landscape and meet the stringent demands of the modern marketplace.
Electrification reduces CO2 emissionsПравда
Replacing fossil fuel combustion with electrification in copper annealing eliminates direct CO2 emissions at the source.
Legacy furnaces are 80% efficientЛожь
Most legacy gas furnaces operate at 40-55% efficiency, while modern designs can exceed 80%.
How are traditional copper annealing methods impacting the environment?
The environmental toll of an industrial furnace can often feel like a distant, abstract problem buried in compliance paperwork. But the reality is that direct CO2 emissions, harmful NOx pollutants, and sheer energy waste are actively contributing to climate change and can tarnish your brand's reputation with eco-conscious customers. Recognizing these specific impacts is the critical first step toward adopting cleaner technologies that protect both the planet and your business’s long-term viability.
Traditional copper annealing, which primarily uses the combustion of fossil fuels, directly releases large volumes of carbon dioxide (CO2), a primary greenhouse gas. It also generates harmful air pollutants like nitrogen oxides (NOx) and consumes vast quantities of non-renewable energy, contributing to resource depletion and air quality degradation.
The impact is more tangible than you might think. I once walked through a potential client's facility where the air around their aging annealing line was thick with a hazy shimmer, and the immense heat radiating from the furnace was palpable from meters away. This wasn't just an audit finding on a piece of paper; it was a sensory confirmation of waste. That heat represented wasted fuel, and the haze represented unchecked emissions. It was a clear sign that the process was harming not only the global environment but also the immediate workplace. This experience crystallized for me that the environmental "impact" is not an abstract concept. It affects employee health, local air quality, and the company's relationship with its community. At AKS, our entire design philosophy is built around containing these impacts at the source. We believe that a well-engineered furnace should be efficient and clean, protecting both the product inside and the world outside. This principle guides us as we explore the specific environmental burdens of traditional methods and engineer the solutions to mitigate them.
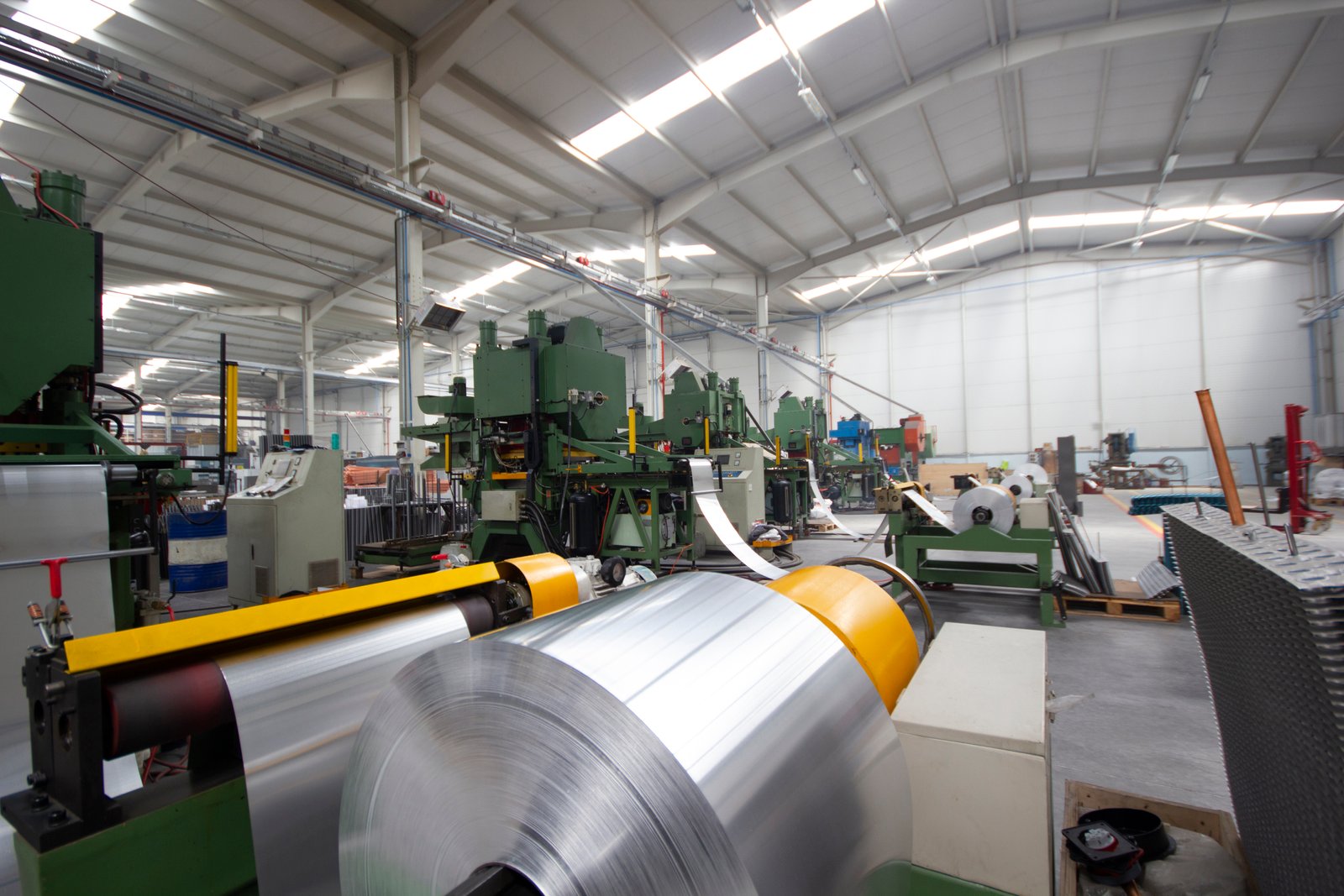
Greenhouse Gas Emissions: The Carbon Footprint of Combustion
The most direct environmental impact of traditional copper annealing is the emission of greenhouse gases, primarily carbon dioxide (CO2). The process relies on the combustion of natural gas, which is mostly methane (CH4). The basic chemical reaction—CH4 + 2O2 → CO2 + 2H2O—shows that for every molecule of methane burned, a molecule of carbon dioxide is released directly into the atmosphere. When you scale this up to an industrial level, the numbers become staggering. According to the U.S. Environmental Protection Agency (EPA)3, burning one million British thermal units (MMBtu) of natural gas produces approximately 53 kilograms of CO2.
Consider a medium-sized copper strip processing plant that anneals 15,000 tons of material annually. Using a traditional furnace with average efficiency, its annual CO2 emissions from the annealing process alone can easily exceed 2,000 metric tons. This is equivalent to the annual emissions of over 400 gasoline-powered passenger vehicles. This calculation doesn't even account for methane leaks (a far more potent greenhouse gas) that can occur during the extraction and transportation of natural gas, adding to the overall "well-to-wheel" environmental burden of the fuel.
This factory-level footprint is a microcosm of a global issue. The industrial sector is a primary contributor to global CO2 emissions, and high-temperature processes are a major reason why. By continuing to operate legacy combustion furnaces, companies are not just impacting their own sustainability reports; they are contributing to the cumulative concentration of greenhouse gases that drive climate change. This positions them on the wrong side of international efforts like the Paris Agreement and makes them vulnerable to the increasing global momentum towards carbon neutrality.
Air Quality and Secondary Pollutants (NOx, SOx)
Beyond the global impact of CO2, traditional combustion processes have a significant and localized effect on air quality. High-temperature combustion of fuel in the presence of atmospheric nitrogen (which is 78% of the air) inevitably creates nitrogen oxides (NOx). NOx is a family of poisonous, highly reactive gases that are major contributors to smog, acid rain, and the formation of fine particulate matter (PM2.5). These pollutants can cause severe respiratory problems, damage ecosystems, and are strictly regulated by environmental agencies in most countries.
I worked with a client located in a densely populated industrial park in India. They were facing mounting pressure from local environmental authorities and community groups over their plant's emissions. While their CO2 footprint was a concern, the more immediate threat was a citation for exceeding local NOx limits. Their old furnaces were the primary source. The solution was a strategic upgrade to one of our electrically heated Bright Annealing Furnaces. By eliminating combustion entirely, they eradicated 100% of the NOx and SOx emissions from the annealing process. This not only brought them into immediate compliance but also significantly improved their local corporate image, turning a regulatory threat into a public relations win.
This highlights the critical advantage of electrification. It shifts the emission source from the factory floor to the power plant, where emissions are more easily controlled and captured at a large scale. Furthermore, as the energy grid becomes greener with the addition of renewable sources like solar and wind, the overall carbon footprint of electric heating diminishes, a benefit that combustion technology can never achieve. Even in our advanced gas furnaces, we use precision air-to-fuel controls to optimize the flame and lower combustion temperatures where possible, which helps to minimize NOx formation, but complete elimination is only possible by removing the flame itself.
Energy Waste as an Environmental Burden
Finally, it is crucial to reframe energy inefficiency itself as a primary environmental impact. Every kilowatt-hour of energy wasted through poor furnace design is a direct and unnecessary environmental burden. This waste represents fossil fuels that were extracted, processed, and transported, with all the associated ecological disruption and emissions, only to be vented as useless heat into the atmosphere. An inefficient furnace doesn't just cost more to run; it has a larger upstream environmental footprint.
A legacy furnace with a thermal efficiency of 50% effectively doubles the environmental impact of its energy consumption compared to a furnace that is 100% efficient. When we design a system like our Печь для отжига колокольного типа4 with advanced waste heat recovery, our goal is to close this efficiency gap. These systems capture the high-temperature exhaust gases and use a heat exchanger to preheat the incoming combustion air or even the protective atmosphere. This single feature can boost the overall thermal efficiency by 15-20 percentage points, leading to a direct and equivalent reduction in fuel consumption and associated emissions.
To make this tangible for clients, we often model the energy journey. For every 100 units of energy that enter a legacy furnace, perhaps 50 units do useful work on the copper, while 50 units are lost. In an AKS furnace with integrated heat recovery, 85 of those 100 units perform useful work, and only 15 are lost. This 35-unit difference represents a direct reduction in the amount of natural gas that needs to be burned, a direct reduction in CO2 and NOx emissions, and a direct reduction in the environmental strain of energy production. Improving efficiency is the most immediate and often most cost-effective way to reduce environmental impact.
Traditional annealing emits CO2Правда
Burning natural gas in copper annealing directly releases carbon dioxide as shown in the CH4 + 2O2 → CO2 reaction.
NOx only affects global climateЛожь
NOx primarily damages local air quality by contributing to smog and respiratory issues, though it has secondary climate effects.
What challenges does the industry face in transitioning to low-carbon heating technologies?
While the destination of a low-carbon future is clear, the path for many manufacturers is filled with obstacles. You know you need to change, but the high initial cost of new equipment, concerns about operational disruption, and a lack of clear technical guidance can create significant hesitation. Addressing these challenges head-on is the only way to move from ambition to action and secure a sustainable future.
The primary challenges in transitioning to low-carbon heating include the high initial capital investment (CAPEX) for new furnaces, the need for robust electrical infrastructure to support electrification, and the operational hurdles of process validation, retraining staff, and ensuring consistent product quality during the switch.
The decision to overhaul a core industrial process like annealing is never taken lightly. It’s a complex equation of risk and reward. I often hear from plant managers who are intrigued by the promise of electric or hydrogen-ready furnaces but are constrained by a tight annual budget. They ask, "How can I justify a multi-million dollar investment when my current furnace, despite its inefficiencies, is still operational?" This is the fundamental challenge: bridging the gap between long-term strategic goals and short-term financial realities. It requires a shift in mindset, from viewing a new furnace as a simple replacement cost to seeing it as a strategic investment in future profitability and resilience. Our role at AKS is to help clients build this business case. We work with them to model the long-term energy savings, reduced carbon taxes, and increased market access that a modern furnace provides, demonstrating how the initial investment can deliver a powerful and predictable return over the equipment's lifespan.
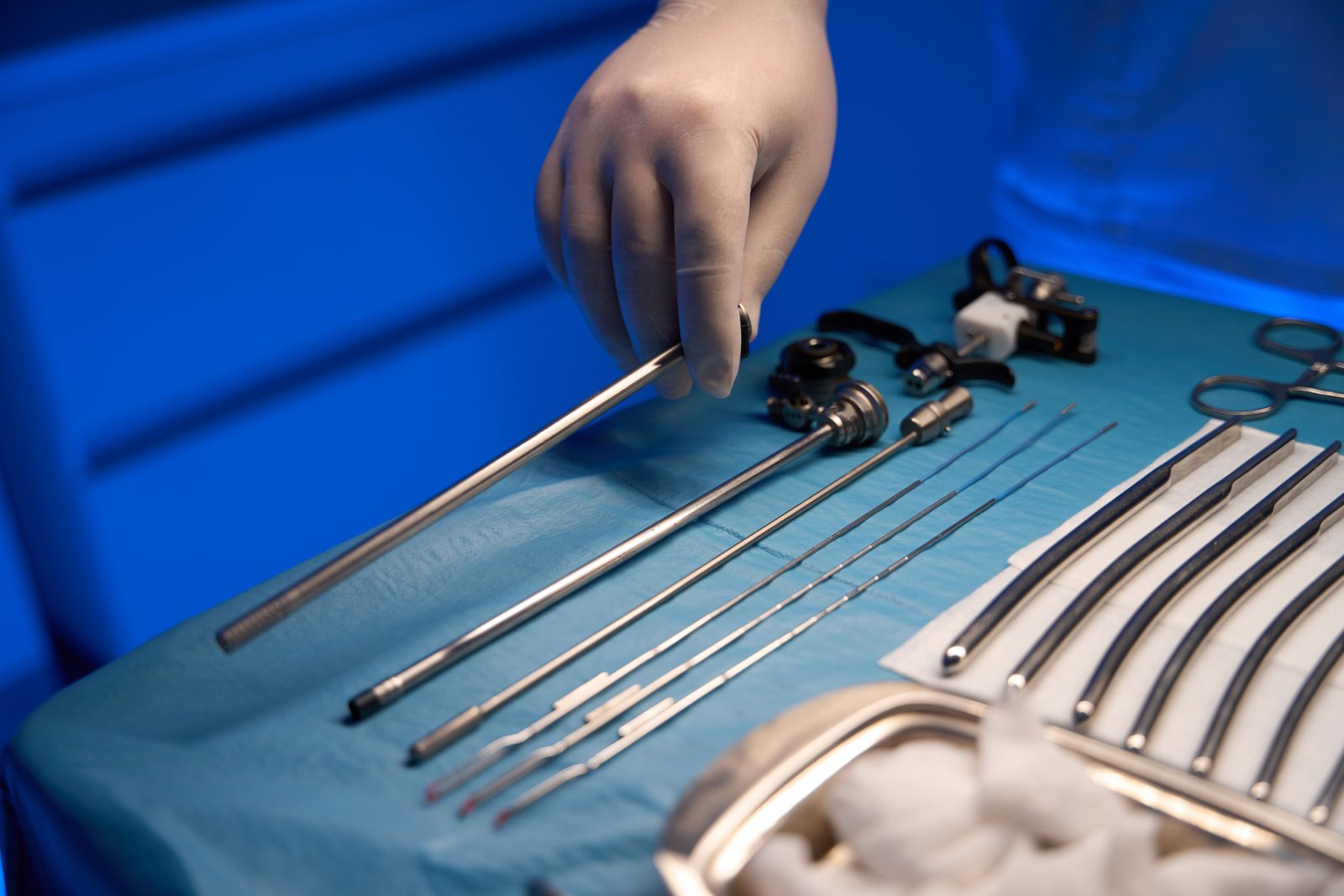
High Initial Capital Investment (CAPEX)
The most significant and immediate barrier to adopting low-carbon annealing technology is the substantial upfront capital expenditure. A new industrial furnace, whether it's an advanced electric Bright Annealing Furnace or a hydrogen-ready Bell-Type Furnace, represents a major investment that can run into hundreds of thousands, if not millions, of dollars. For many companies, especially small to medium-sized enterprises (SMEs), securing this level of capital can be a formidable challenge. Financial decision-makers are often focused on short-term payback periods, and an investment in sustainability can be perceived as a cost center rather than a value driver.
To overcome this, the conversation must shift from cost to total cost of ownership (TCO) and return on investment (ROI). I recently worked with a mid-sized copper wire producer who was hesitant to replace their two aging gas furnaces. We collaborated with their finance team to build a detailed 10-year TCO model. The model factored in not only the purchase price of a new, highly efficient AKS furnace but also projected energy savings based on rising utility costs, eliminated carbon tax liabilities under a new regional scheme, reduced maintenance expenses, and lower material scrappage rates due to improved process control.
The analysis showed a projected payback period of just under four years. When presented with this data-driven forecast, the investment was no longer an expense but a clear strategic move to reduce future operational volatility and boost long-term profitability. Furthermore, we helped them explore green financing options and government incentives for energy-efficient capital equipment, which further eased the initial financial burden. Overcoming the CAPEX challenge requires building a robust, undeniable business case that resonates with financial stakeholders.
Infrastructure and Energy Grid Limitations
The second major challenge lies in the supporting infrastructure, particularly for companies considering a full transition to electric heating. Electrifying a large-scale heat treatment process requires a significant amount of power. A bank of large annealing furnaces can easily add several megawatts to a facility's peak electricity demand. This often necessitates a substantial and costly upgrade to the plant's internal electrical systems, including transformers, switchgear, and cabling.
Beyond the factory walls, the reliability and capacity of the local energy grid become critical factors. In many developing regions or even in older industrial zones in developed countries, the grid may not be stable enough to support the large, fluctuating loads of industrial electric heating without risking power dips or outages that could ruin product batches and halt production. I encountered this issue with a client in Southeast Asia who was eager to electrify. A preliminary assessment revealed that the local substation was already at capacity. The transition had to be paused until a grid upgrade could be coordinated with the local utility provider, a process that added more than a year to the project timeline.
This is why a thorough infrastructure audit is a non-negotiable first step in our project planning at AKS. We assess the client's current electrical capacity and work with local energy experts to understand the grid's capabilities and limitations. In cases where the grid is a constraint, we explore alternative or interim solutions, such as hybrid gas/electric furnaces or implementing our most energy-efficient gas furnaces first. This pragmatic approach ensures that the transition to low-carbon technology is paced appropriately and aligned with infrastructural realities.
Technical and Operational Hurdles
The third set of challenges is technical and operational. Annealing is a precise metallurgical process, and any change in the heating method requires careful validation to ensure that the final product quality—in terms of grain structure, tensile strength, and surface finish—remains consistent or is improved. Operators and engineers who have spent their careers working with gas furnaces may be unfamiliar with the control systems and operational parameters of electric or hydrogen-based systems. This creates a skills gap that must be addressed through comprehensive training.
A key concern we often hear is about process replication. A client producing high-specification copper foil for the electronics industry, for example, cannot afford any deviation in material properties. To de-risk this transition, our process involves running extensive material trials at our own R&D facility or in a pilot line. We work with the client's quality control team to anneal samples of their specific alloys in our proposed furnace, followed by rigorous testing and analysis to certify that the results meet their exact specifications before the new equipment is even built.
Furthermore, we design our furnace control systems to be as intuitive as possible, with advanced automation and PLC-based interfaces that simplify operation and reduce the chance of human error. Our service model includes on-site commissioning and in-depth training for the client's operational and maintenance teams. We don't just deliver a piece of equipment; we ensure a seamless integration into the client's production ecosystem, providing the technical support needed to manage the change effectively and build confidence in the new technology. Addressing these operational hurdles is just as important as engineering the furnace itself.
CAPEX is the biggest transition barrierПравда
The high initial capital investment for new furnaces is consistently cited as the most immediate challenge for manufacturers.
Grid upgrades are optional for electrificationЛожь
Most facilities require substantial electrical infrastructure upgrades to support electric furnace loads, as existing grids often lack capacity.
What are effective strategies for integrating sustainable heating practices in copper annealing?
Knowing you need to change is one thing; having a practical roadmap is another. Many manufacturers get stuck in analysis paralysis, overwhelmed by the options. The key is to stop thinking of it as a single leap and instead see it as a series of strategic, manageable steps. By focusing on a phased approach, from immediate efficiency gains to long-term technological shifts, you can build momentum and transform your operations sustainably.
Effective strategies for integration include a phased approach starting with maximizing the efficiency of existing systems through retrofits and waste heat recovery. This is followed by investing in new, highly efficient electric or hydrogen-ready furnaces and leveraging data-driven process optimization to ensure continuous improvement in energy use.
The most successful transitions I've been a part of were not sudden, radical overhauls but carefully planned evolutions. A "go big or go home" mentality can be intimidating and financially impractical. A smarter approach is to secure immediate wins that build both capital and confidence for bigger changes down the line. I often advise clients to start with the "low-hanging fruit." Can we retrofit your current furnace line with a modern waste heat recovery system? Can we use advanced sensors and data analytics to optimize your existing cycle times for energy efficiency? These initial steps can often yield significant savings—sometimes reducing energy consumption by 15-20% on their own. This success creates a powerful internal narrative of progress and provides a tangible, data-backed justification for the next phase of investment, such as the purchase of a new, state-of-the-art AKS furnace. This methodical, step-by-step strategy de-risks the entire process and makes the journey to sustainability achievable for any organization.
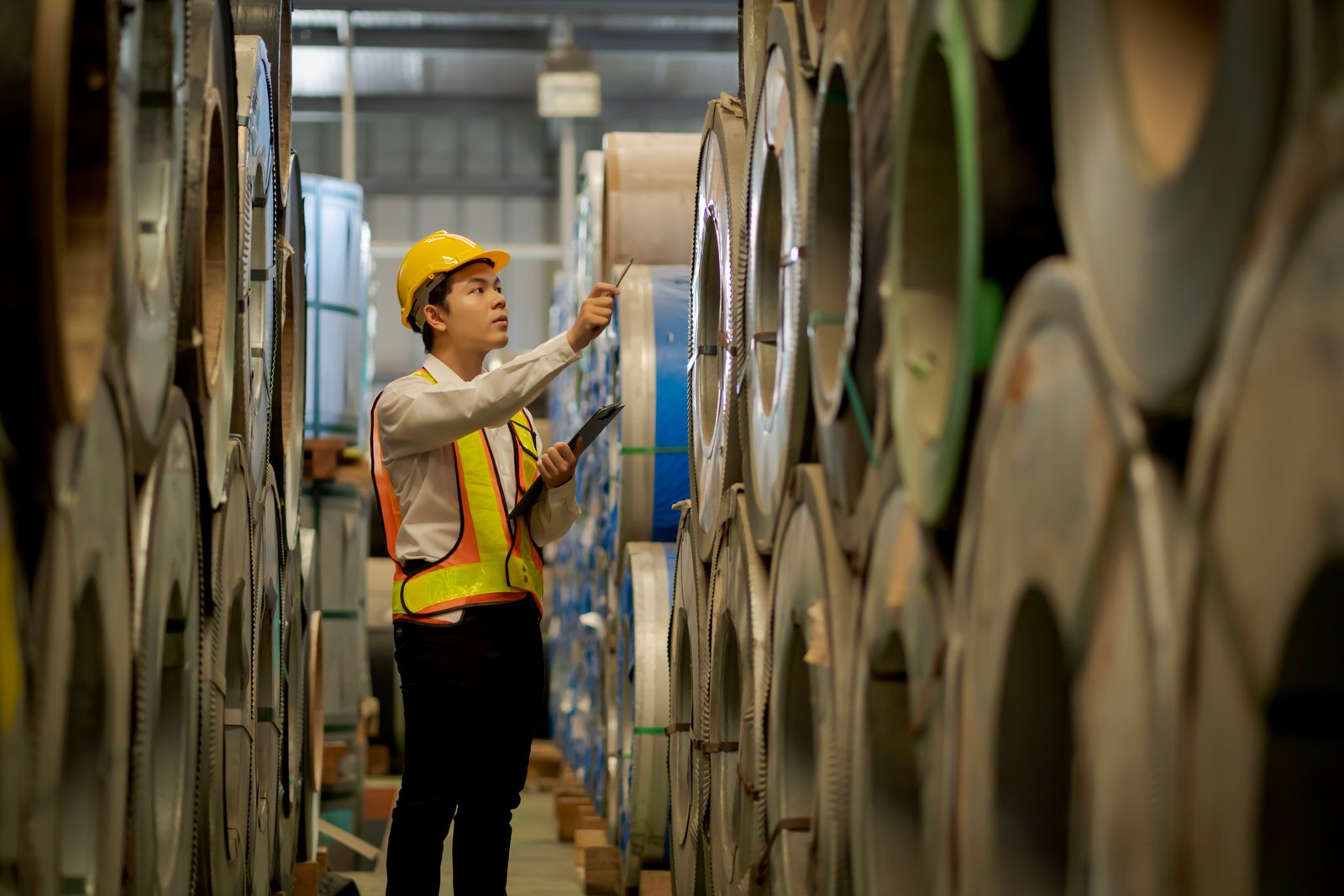
A Phased Approach: From Efficiency Gains to Full Electrification
The most pragmatic and effective strategy for integration is a phased approach that aligns with a company's financial and operational realities. This journey typically begins not with replacing equipment, but with maximizing the efficiency of what is already there. This is Phase One: Optimization. It involves a detailed energy audit to identify sources of heat loss and inefficiency. Simple measures like improving insulation, fixing door seals, and upgrading to more efficient burners can yield surprising results. This phase is low-cost, low-risk, and delivers immediate returns, making it an ideal starting point.
Phase Two involves a more significant upgrade: retrofitting existing furnaces with advanced, energy-saving technologies. At AKS, we often propose adding our external waste heat recovery systems to a client's existing furnace line. This technology captures hot exhaust gases and uses them to preheat combustion air, effectively recycling energy that would otherwise be lost. This single upgrade can cut fuel consumption by a substantial margin without requiring the replacement of the entire furnace. This step serves as a bridge, dramatically improving the sustainability of current operations while the company plans for its next major capital investment.
Phase Three is the ultimate goal: the transition to fundamentally low-carbon heating technology. This involves the planned replacement of aging gas furnaces with state-of-the-art electric or hydrogen-ready systems, such as our Vacuum Annealing Furnaces for specialty metals or our continuous Bright Annealing lines. Because the company has already reaped the financial benefits from the first two phases, the business case for this final step is much stronger. This phased strategy transforms the daunting challenge of decarbonization into a manageable, logical progression of value-adding investments.
Leveraging Hybrid Technologies as a Transitional Bridge
For many companies, an immediate, full-scale jump to 100% electric heating may not be feasible due to infrastructure constraints or concerns about the intermittent nature of renewable energy sources. In these scenarios, hybrid heating technology offers an intelligent and flexible transitional strategy. A hybrid furnace can operate using either natural gas or electricity, allowing a company to take advantage of the most cost-effective or greenest energy source available at any given time.
This approach offers several key advantages. First, it provides operational resilience. If there is an electrical grid outage or a spike in electricity prices, the furnace can seamlessly switch over to natural gas, ensuring production continuity. We designed a Bogie Hearth Annealing Furnace for a client in North America with this dual-fuel capability. They run it on electricity overnight when prices are low and the grid is powered by renewables, but switch to their gas backup during peak daytime hours to control costs.
Second, a hybrid system future-proofs the investment. A company can install a hybrid furnace today and run it primarily on gas, but they are already equipped to increase their electricity usage as their site infrastructure is upgraded or as the grid becomes cleaner and more reliable. This avoids the risk of investing in a single-fuel technology that may become obsolete or uneconomical in the future. Hybrid technology is not a compromise; it is a strategic choice that provides flexibility and de-risks the long-term energy transition.
Data-Driven Process Optimization for Continuous Improvement
Regardless of the heating technology used, the foundation of sustainable operation is data. Modern industrial furnaces should be viewed not just as heating chambers, but as sophisticated data-generation hubs. Integrating advanced sensors to monitor temperature, atmosphere composition, energy consumption, and gas flow in real-time is essential. This data, when fed into a central PLC or SCADA system, provides an unprecedented level of insight into the annealing process.
At AKS, we equip our furnaces with comprehensive sensor packages and control systems that enable this data-driven approach. By analyzing this data, operators can move beyond fixed, predetermined annealing cycles and toward dynamic, optimized process control. For instance, the system can learn the precise amount of energy required to bring a specific coil mass to the target temperature and hold it there, avoiding the energy waste associated with "one-size-fits-all" heating profiles. We worked with a client to analyze their annealing data over three months and discovered they could shorten their average cycle time by 12% without any impact on metallurgical quality, resulting in significant energy savings and increased throughput.
This commitment to data establishes a cycle of continuous improvement. The insights gained from today's production runs are used to refine the control parameters for tomorrow. This strategy transforms sustainability from a one-time project into an ongoing operational discipline. By leveraging data, a company can ensure that its annealing process is not only efficient on day one but continues to become more efficient over the entire lifespan of the equipment.
Phased approach reduces transition riskПравда
The article emphasizes that a phased strategy makes sustainability transitions more manageable by starting with low-cost efficiency improvements before major equipment upgrades.
Hybrid furnaces use only electricityЛожь
Hybrid furnaces are designed to switch between electricity and natural gas, providing operational flexibility during energy transitions.
How can low-carbon technologies help achieve net-zero goals in the copper industry?
Reaching net-zero emissions can feel like a monumental, almost abstract, corporate goal. But for the copper industry, the path to this goal runs directly through the factory floor. The technology choices you make for core processes like annealing are not just operational decisions; they are the tangible actions that will collectively determine whether the industry can achieve its ambitious climate targets.
Low-carbon technologies are fundamental to achieving net-zero goals by directly eliminating CO2 emissions from the annealing process through electrification and green hydrogen. This shift also enhances energy efficiency, supports a circular economy through cleaner metal recycling, and builds a resilient, sustainable supply chain for the future.
Transition paragraph: The push for net-zero is reshaping global supply chains. Increasingly, your company's carbon footprint is becoming as important as your product's quality and price. For export-oriented manufacturers, this is already a reality. I've seen clients win major contracts specifically because they could demonstrate a lower carbon footprint than their competitors, thanks to their investment in electric annealing technology5. This is the new competitive landscape. Achieving net-zero is not just about environmental responsibility; it's about securing your place in the green economy of the future. The technologies we integrate today, like the advanced systems in our AKS furnaces, are the building blocks that will make this ambitious goal a tangible reality for the copper industry.
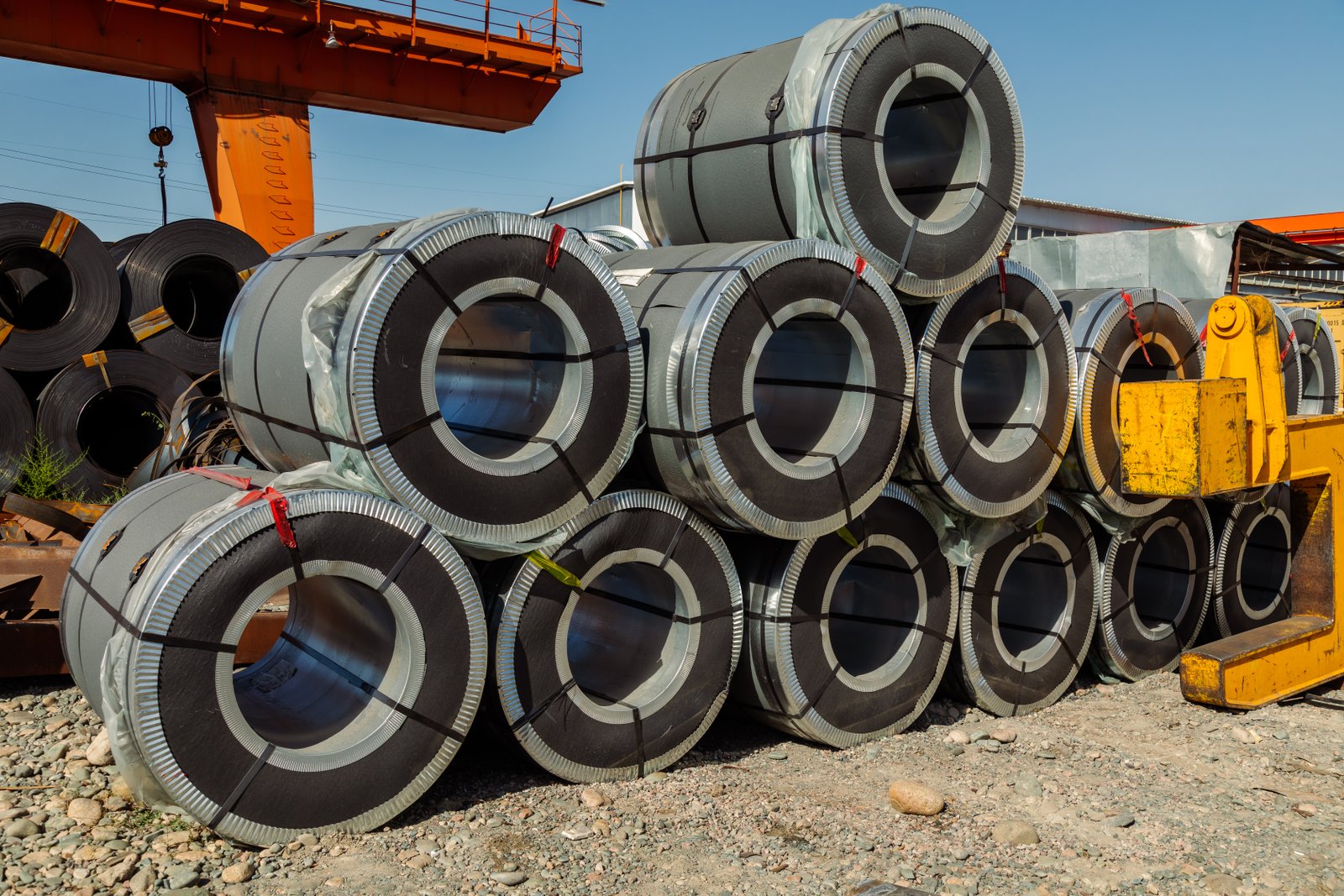
Direct Emission Abatement via Electrification and Green Hydrogen
The most powerful way low-carbon technologies contribute to net-zero goals is through the direct and total abatement of on-site greenhouse gas emissions. When a copper annealing furnace is powered by electricity generated from renewable sources (like solar, wind, or hydro), the process itself becomes effectively carbon-free. This shift moves the carbon accounting from Scope 1 emissions (direct emissions from owned or controlled sources) to Scope 2 (indirect emissions from the purchase of electricity). As the global energy grid continues to decarbonize, the Scope 2 emissions associated with electric furnaces will progressively fall to zero, providing a clear and permanent pathway to net-zero for the annealing process.
The next frontier, for which we are already preparing, is green hydrogen. Hydrogen, when used as a fuel, produces only water as a byproduct, completely eliminating carbon emissions. A furnace designed to run on green hydrogen6 (produced via electrolysis powered by renewables) would have a true zero-carbon footprint. At AKS, we are actively developing and testing hydrogen-ready furnaces. A client in Europe, with access to a developing hydrogen pipeline, is partnering with us to install a pilot Bell-Type furnace that can co-fire a blend of natural gas and hydrogen, with the goal of transitioning to 100% hydrogen as the supply becomes reliable. This represents a definitive step towards a net-zero industrial heating process.
This technological shift is not incremental; it is transformational. It fundamentally decouples the manufacturing process from fossil fuel combustion. For the copper industry, which produces a material essential for the green energy transition (used in everything from wind turbines to electric vehicles), aligning its own production methods with net-zero principles is a critical step in establishing a truly sustainable, end-to-end value chain.
Enabling a Circular Economy through Efficient Recycling
The concept of a circular economy—where resources are reused and recycled rather than being extracted, used, and discarded—is central to long-term sustainability. Copper is infinitely recyclable without any loss of quality, making it a perfect material for a circular model. However, the recycling process itself, particularly the re-melting and annealing of scrap copper, is energy-intensive. If this recycling process is powered by fossil fuels, a significant portion of the environmental benefit is negated by the emissions generated.
Low-carbon heating technologies are essential to closing this loop cleanly. By using highly efficient electric furnaces to anneal recycled copper, manufacturers can produce high-quality, secondary-source material with a minimal carbon footprint. This makes recycled copper not just an economically viable alternative to primary copper, but a genuinely green one. The precision control offered by our Vacuum Annealing Furnaces, for instance, is ideal for processing high-purity recycled copper for demanding applications in electronics and aerospace, ensuring that the quality of the recycled material is identical to that of virgin material.
A thriving, low-carbon circular economy for copper reduces the need for energy-intensive mining and smelting of new ore, preserves natural resources, and drastically lowers the overall environmental impact of the industry. By providing the clean heating technology required for efficient recycling, advanced furnaces act as a critical enabler of this circular model, moving the entire industry closer to its net-zero and sustainability goals.
Building a Resilient, Future-Proofed Supply Chain
Ultimately, achieving net-zero is about building a resilient and future-proof business. A company that remains dependent on volatile fossil fuel markets and is exposed to ever-tightening carbon regulations is inherently fragile. Its profitability can be wiped out by a sudden spike in gas prices or the introduction of a new carbon tax. Conversely, a company that has invested in low-carbon, high-efficiency technology is insulated from these risks. Its energy costs are more stable and predictable, and its operations are already aligned with the direction of future environmental policy.
This resilience extends to the marketplace. As major global brands commit to net-zero supply chains, they are actively seeking out and prioritizing suppliers who can meet these stringent environmental standards. We have seen this firsthand. An AKS client who supplies bright-annealed stainless steel components to a major European appliance manufacturer recently won a larger share of their business. The deciding factor was their ability to provide third-party verified data showing the low carbon footprint of their production process, which was made possible by their modern electric annealing line. Their competitor, still using older gas-fired technology, could not provide the same level of assurance and was deemed a higher-risk supplier.
Investing in low-carbon technology is therefore not just an environmental or operational decision; it is a profound strategic choice. It is a declaration that a company is prepared for the economy of the future. By helping our clients in the copper industry make this transition, we are not only contributing to the global net-zero ambition but also empowering them to build stronger, more competitive, and more enduring businesses.
Electric furnaces eliminate Scope 1 emissionsПравда
Electrifying copper annealing shifts emissions from direct (Scope 1) to indirect (Scope 2) sources, enabling full decarbonization as grids transition to renewables.
Recycled copper requires more energy than virgin copperЛожь
While recycling is energy-intensive, it uses 85-90% less energy than primary copper production when powered by clean electricity.
Заключение
Transitioning to low-carbon copper annealing is no longer just an option but a strategic imperative. By embracing advanced electric furnaces, waste heat recovery, and data-driven optimization, your company can decisively cut emissions, lower energy costs, and secure a vital competitive advantage in the global shift toward sustainability.
-
Learn about initiatives promoting sustainability in the copper industry ↩
-
Understand how CBAM affects global trade for high-emission industries ↩
-
Access data on CO2 emissions from natural gas combustion ↩
-
Understand how heat recovery technology boosts furnace efficiency ↩
-
Learn about the benefits of electric annealing in lowering carbon emissions and improving energy efficiency ↩
-
Explore the potential of green hydrogen to revolutionize industrial heating with zero carbon emissions ↩
У вас есть вопросы или нужна дополнительная информация?
Свяжитесь с нами, чтобы получить индивидуальную помощь и квалифицированный совет.