Как обеспечить безопасное обращение с водородом и обнаружение утечек в процессах отжига нержавеющей стали?

Are you looking to achieve that perfect, mirror-bright finish on stainless steel using a hydrogen atmosphere, but the inherent safety risks are holding you back? The fear of leaks and potential combustion is a major concern for any plant manager, impacting both safety and operational uptime. At AKS, we believe that with robust engineering and smart protocols, you can harness hydrogen's benefits without compromising safety.
Ensuring safety in hydrogen-based bright annealing involves a multi-layered strategy. This includes advanced furnace design with high-integrity seals, continuous atmospheric monitoring with precision sensors, maintaining positive furnace pressure to prevent air ingress, implementing automated emergency shutdown systems, and enforcing strict operational and maintenance protocols for all personnel.
For years, I’ve spoken with plant managers who are hesitant to fully adopt pure hydrogen atmospheres, despite knowing it yields the best surface quality for high-value products. They worry about the invisible, odorless nature of hydrogen and its wide flammability range. This concern is valid, but it shouldn't be a barrier. Let's move beyond fear and into a space of controlled, confident operation by breaking down the risks and the proven solutions available today.
The conversation around hydrogen safety in thermal processing often simplifies it to a binary choice: avoid it or accept massive risk. The reality is far more nuanced. The industry's evolution, guided by standards like the NFPA 861, proves that hydrogen can be managed with exceptional reliability. For instance, a study of industrial gas incidents shows that failures are overwhelmingly linked to procedural gaps or equipment degradation, not inherent flaws in the technology itself. At AKS, we've engineered solutions for clients processing everything from delicate automotive sensor sleeves to robust stainless steel coils, demonstrating that a proactive, system-wide approach to safety is not just possible, but practical and cost-effective.
What are the safety concerns in hydrogen handling during bright annealing?
The primary concern with using hydrogen in bright annealing is its high flammability and the immense energy it releases upon combustion. When mixed with oxygen from the air, it creates a potent explosive risk that can be ignited by a simple spark, threatening personnel and equipment. This challenge demands more than just caution; it requires systemic engineering controls.
Key safety concerns for hydrogen in bright annealing include its wide flammability range (4-75% in air), low ignition energy, and the invisible, odorless nature of its flame. The risk of leaks from furnace seals, piping, or valves can lead to explosive atmospheres, posing a severe hazard to personnel, equipment, and production continuity.
When I visit metal processing facilities, the conversation inevitably turns to the "what-ifs" of hydrogen use. What if a seal fails? What if a valve is left open? These are not just hypothetical questions; they are the core risks we must engineer against. The invisible nature of a hydrogen leak means you can't see the danger accumulating. Its wide flammability range, from 4% to 75% concentration in air, means that even small leaks can create a hazardous condition quickly. This isn't like handling natural gas, which has a much narrower flammable range. Furthermore, the energy required to ignite a hydrogen-air mixture is incredibly low—about one-tenth that of natural gas. This means that a tiny static spark, a hot surface, or a faulty electrical component could be enough to trigger a devastating incident. Understanding these properties isn't about fear-mongering; it's about respecting the material and building a fortress of safety measures around the process. It forces us to think beyond simple detection and consider the entire ecosystem, from storage to furnace chamber and back again. The goal is to make the risk statistically insignificant through layers of redundant, automated, and procedural safeguards.
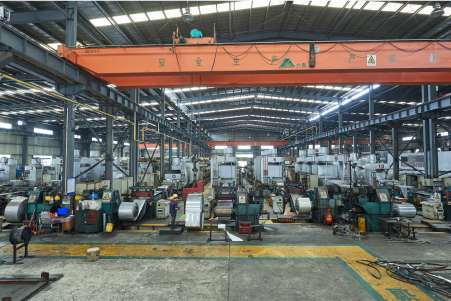
A deep dive into hydrogen safety reveals that the concerns extend beyond simple flammability into the very materials and design of the furnace system. The challenge is multifaceted, requiring a holistic understanding of chemical, physical, and human factors to build a truly resilient safety infrastructure. This is where we, as furnace manufacturers, must apply rigorous engineering principles to protect our clients' most valuable assets: their people and their production capabilities. The stakes are simply too high for a "one-size-fits-all" approach.
The Chemical & Physical Risks of Hydrogen
Hydrogen's unique properties make it an excellent reducing agent for bright annealing, but they are also the source of its primary hazards. Its flammability range of 4-75% in air2 is exceptionally wide, as documented by AIChE's Center for Chemical Process Safety. This means that from a very lean to a very rich mixture, the potential for combustion exists. Compare this to methane (natural gas), which has a flammability range of only 5-15%. This property alone means that containment is absolutely critical, as any leak is highly likely to result in a flammable mixture.
Furthermore, hydrogen possesses a very low minimum ignition energy (MIE), approximately 0.02 millijoules. This is an order of magnitude lower than most hydrocarbons. In a practical sense, this means that ignition sources we might consider benign in other environments—such as a static discharge from clothing, a non-intrinsically safe tool, or a hot bearing—can be sufficient to initiate a hydrogen fire or explosion. The flame itself is nearly invisible in daylight, making a fire difficult to detect visually, which can delay response and suppression efforts significantly.
Lastly, a phenomenon known as hydrogen embrittlement poses a long-term risk to equipment integrity. Over time, atomic hydrogen can diffuse into the metallic structure of pipes, valves, and even the furnace shell, especially at high temperatures and pressures. This can reduce the ductility of the steel, making it brittle and susceptible to cracking and failure. This is why material selection is critical; using materials not rated for hydrogen service, like standard cast iron fittings as prohibited by OSHA 1910.103, is a direct path to catastrophic failure.
The Operational & Human Factor Risks
Beyond the inherent properties of hydrogen, the operational environment introduces another layer of risk. In any industrial setting, human error is an unavoidable variable. An operator forgetting to close a purge valve, a maintenance technician improperly tightening a flange, or a procedural shortcut taken to save time can all bypass sophisticated engineering controls. For instance, a client in the automotive parts sector once shared an incident where a third-party contractor, unfamiliar with their hydrogen protocols, used a standard power tool near a supply line during maintenance, fortunately without incident, but highlighting a critical training gap.
Procedural drift is another significant concern. A facility may start with robust, well-defined Standard Operating Procedures (SOPs), but over months and years, small, unapproved deviations can creep in. These minor changes might seem harmless in isolation but can collectively erode the layers of safety designed into the system. This is why regular audits, continuous training, and a strong safety culture, championed from the management level down, are just as important as the physical hardware.
The complexity of the system itself can also be a risk factor. A bright annealing line is not just a furnace; it's an integrated system of gas storage, purifiers, complex piping, flow controls, sensors, and emergency vents. A failure in any one of these subsystems can have cascading effects. A malfunctioning pressure regulator, for example, could over-pressurize a section of the line, leading to a seal failure downstream. This interconnectedness demands a holistic approach to risk assessment and maintenance, rather than treating each component in isolation.
The Consequence of Failure: Beyond the Initial Event
The impact of a hydrogen-related incident extends far beyond the immediate explosion or fire. The primary consequence is, of course, the risk to human life and the potential for serious injury. However, the business ramifications are equally severe and long-lasting. A significant event can lead to a complete production halt for weeks or even months, resulting in massive financial losses from lost orders, contract penalties, and the cost of rebuilding.
A case in point involves a metal strip processor that experienced a minor hydrogen fire due to a faulty seal. While no one was injured, the incident triggered a full-scale safety audit by regulatory bodies and their own corporate parent. The resulting shutdown for investigation and mandated upgrades cost them nearly a quarter of their annual production volume. The damage to the company's reputation was also significant, making it harder to attract top talent and instilling a sense of fear among the existing workforce.
Furthermore, insurance premiums are likely to skyrocket after such an incident, and the company may face legal liability and hefty fines for safety violations. The ripple effect can even impact the supply chain, as customers who rely on the processed materials are forced to find alternative suppliers, some of whom may never return. Therefore, investing in comprehensive hydrogen safety is not merely an operational expense; it is a fundamental investment in business continuity and long-term viability.
Hydrogen has a wide flammability rangeПравда
Hydrogen's flammability range of 4-75% in air makes it more dangerous than natural gas (5-15%).
Hydrogen flames are easily visibleЛожь
Hydrogen burns with a nearly invisible flame in daylight, making detection difficult without sensors.
How can hydrogen leaks occur in stainless steel annealing processes?
Concerned about where a dangerous hydrogen leak might originate in your annealing line? Leaks are not random events; they happen at predictable weak points. From worn-out seals and failed gaskets to cracked welds and loose fittings, every component in the gas delivery system is a potential failure point. Understanding these vulnerabilities is the first step to preventing them.
Hydrogen leaks in annealing furnaces typically occur at mechanical joints and seals. Common failure points include degraded door seals, faulty pipe fittings and valve packings, cracked welds due to thermal stress or vibration, and material failures like hydrogen embrittlement in components not specified for hydrogen service.
In my experience, the integrity of a hydrogen-based annealing line is only as strong as its weakest link. Over the years, I've helped clients troubleshoot leaks that stemmed from the most seemingly insignificant places. One client, a producer of high-grade stainless steel wire, was losing a significant amount of hydrogen, creating both a cost and safety issue. The culprit wasn't a major rupture but a series of minuscule leaks from the graphite packing in several manually operated valves that were decades old. Thermal cycling—the constant heating and cooling of the furnace—is a major stressor. It causes materials to expand and contract at different rates. The robust steel shell of the furnace moves differently than the ceramic fiber insulation or the alloy fittings. Over thousands of cycles, this movement can work connections loose, fatigue metal components, and degrade sealing gaskets. Vibration from nearby machinery or from the furnace fans themselves can also exacerbate these issues, slowly loosening threaded fittings over time. Therefore, a proactive leak prevention strategy must be grounded in the reality of this dynamic, high-temperature environment.
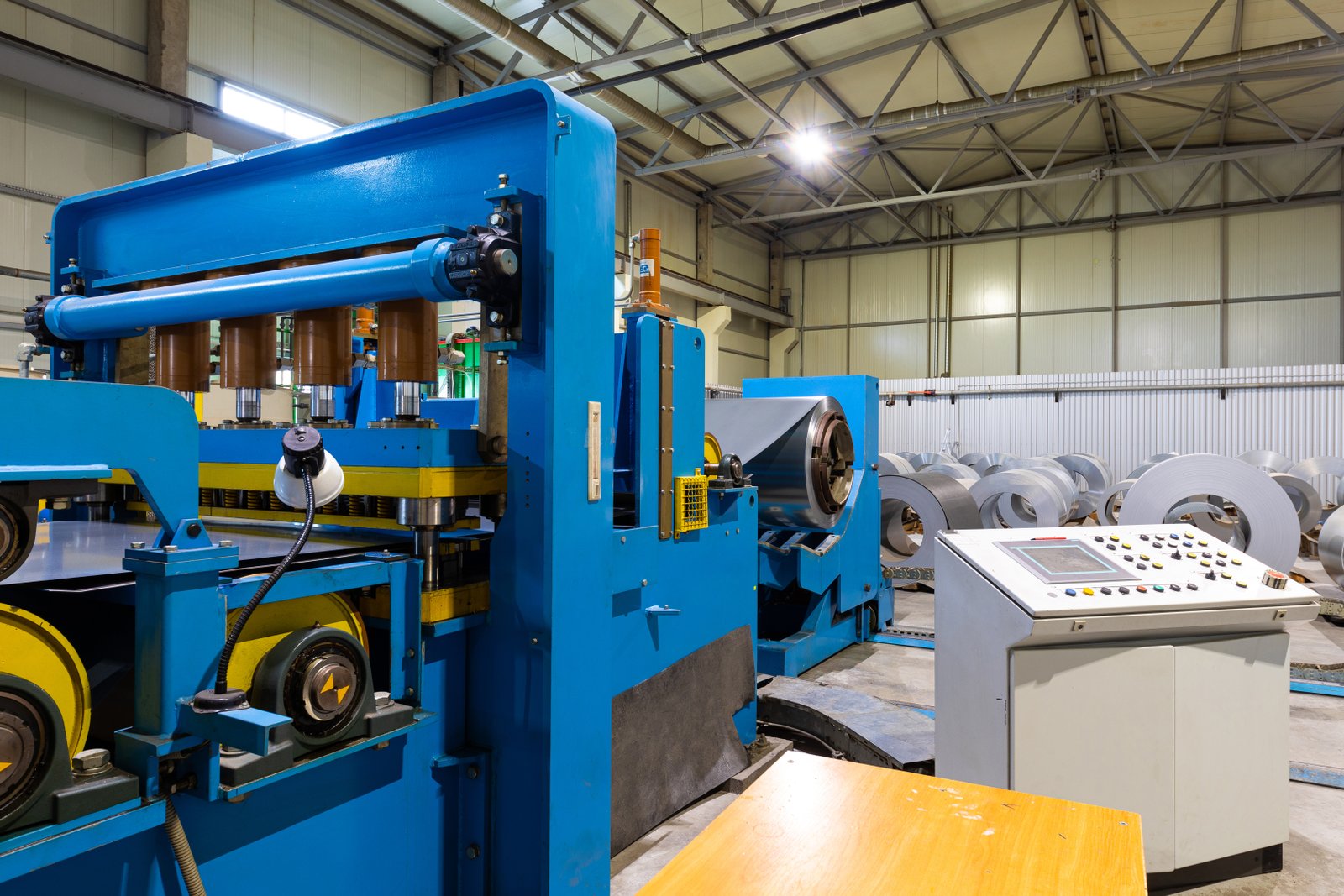
When we analyze the root causes of hydrogen leaks in an industrial setting, they can broadly be categorized into three areas: degradation of mechanical components, failures in system design or material selection, and deficiencies in maintenance or operational procedures. Each of these areas contains multiple potential failure points that must be addressed systematically. A comprehensive safety audit, which we conduct as part of our initial consultation with new clients, always involves a detailed inspection and analysis of these three domains. Merely reacting to leaks is a failing strategy; the goal must be to predict and prevent them through superior design, diligent upkeep, and rigorous protocols.
Mechanical Component Degradation and Failure
The most common source of hydrogen leaks is the gradual degradation of mechanical components that form the containment barrier. The furnace door seal is a prime suspect. Whether it's a silicone, fiber, or water-cooled seal, it is subjected to intense thermal cycling, physical compression, and potential damage from misalignment. Over time, these seals lose their elasticity, become brittle, and develop cracks, creating a direct path for hydrogen to escape or, just as dangerously, for air to enter. At AKS, our furnace designs incorporate double-sealing systems with an inert gas purge in between, providing a crucial layer of redundancy.
Pipe fittings, valve stems, and instrumentation ports are other critical points. Gaskets and packing materials, such as graphite or PTFE, degrade over time. A study by the Materials Technology Institute found that in chemical plants, over 60% of fugitive emissions (unintended leaks) originated from valves, while another 20% came from flanges and connectors. While this data covers various chemicals, the principle holds true for hydrogen. Vibration and thermal cycling can cause threaded connections to loosen. Welds, especially those not performed to the highest standards or on materials susceptible to embrittlement, can develop micro-cracks that propagate over time, leading to a sudden failure.
ly, the furnace muffle or retort itself, the very chamber containing the hydrogen atmosphere, can fail. These components, often made of high-nickel alloys like Inconel or 310S stainless steel, operate at extreme temperatures. Over thousands of hours, they are subject to creep (slow deformation under stress) and oxidation, which can lead to cracks and ruptures. A failure here is often the most dangerous, as it can release a large volume of hydrogen directly into the hot furnace insulation, a potent ignition source.
System Design and Material Incompatibility
Flaws in the initial design of the furnace and its gas delivery system can create built-in failure points. A classic example is the improper selection of materials. As mentioned, using metals susceptible to hydrogen embrittlement is a critical error. Standard carbon steel, for instance, can become brittle and fail catastrophically when used for high-pressure hydrogen piping. According to safety code NFPA 2, all materials in a hydrogen system must be certified as compatible, which is a core principle in our design philosophy at AKS. We exclusively use materials like 316L stainless steel for our hydrogen piping, which offers excellent resistance to embrittlement.
The design of the pressure control system is another critical area. A bright annealing furnace should always operate at a slight positive pressure relative to the outside atmosphere. This ensures that if a minor leak does occur, hydrogen will leak out rather than air leaking in, which would create an explosive mixture inside the hot furnace. However, a poorly designed control system that allows for large pressure swings can stress the furnace structure. For example, if the hydrogen supply regulator fails or is improperly sized, it could cause a sudden pressure spike that could rupture a seal or a weak point in the furnace muffle.
The layout of the piping system also matters. Long, unsupported pipe runs can be subject to vibration and stress. The absence of proper expansion joints or loops can lead to immense stress on fittings and welds as pipes expand and contract with ambient temperature changes. We once consulted for a facility where a recurring leak at a flange was traced back to a poorly supported pipe run over 10 meters long that was putting constant torque on the connection.
Inadequate Maintenance and Operational Errors
Even the best-designed furnace system can be compromised by poor maintenance and operational mistakes. A lack of a proactive, preventative maintenance schedule is a leading cause of leaks. Waiting for a component to fail before replacing it is a reactive stance that is simply not acceptable when dealing with hydrogen. A comprehensive maintenance plan should include regular, scheduled inspections and replacements of high-wear items like door seals, valve packings, and flexible hoses.
For a client manufacturing stainless steel tubing in Southeast Asia, we helped implement a digital maintenance schedule. It flags components for inspection based on operational hours rather than a simple calendar date. This "condition-based" maintenance approach led to a 40% reduction in unplanned downtime and a verifiable decrease in fugitive hydrogen emissions over the first year. The plan includes using a portable hydrogen detector to "sniff" for leaks around all joints and seals on a weekly basis, a simple but highly effective practice.
Operational errors are another significant risk. An operator might accidentally open a bypass valve, cross-connect a low-pressure line to a high-pressure source, or fail to follow the correct startup/shutdown purging sequence. Purging is critical. Before introducing hydrogen, the furnace must be thoroughly purged with an inert gas like nitrogen to remove all oxygen. Similarly, before opening the furnace door after a cycle, the hydrogen must be purged with nitrogen. Failure to do so at either end of the process guarantees the creation of an explosive hydrogen-air mixture. This is why we automate the purging sequence in our AKS furnaces, removing the potential for human error from this critical safety step.
Hydrogen leaks occur at mechanical jointsПравда
Most hydrogen leaks in annealing furnaces originate from degraded seals, gaskets, and pipe fittings due to thermal cycling and vibration.
Carbon steel is ideal for hydrogen pipingЛожь
Carbon steel is prone to hydrogen embrittlement; 316L stainless steel is the recommended material for hydrogen service piping.
What impact do hydrogen leaks have on annealing safety?
Wondering about the real consequences of a hydrogen leak? It’s not just a minor issue. A leak directly creates a fire and explosion hazard, the most severe safety risk in any heat treatment plant. This immediate danger can lead to catastrophic equipment failure, severe injuries, and prolonged operational shutdowns, turning a process issue into a business crisis.
A hydrogen leak's primary impact on annealing safety is the creation of a flammable or explosive atmosphere. This elevates the risk of ignition from furnace hot spots or electrical sparks, potentially causing catastrophic explosions that endanger personnel, destroy equipment, and can lead to extended, costly plant shutdowns.Hydrogen safety standards
The impact of a hydrogen leak is a cascade of escalating risks. It starts silently, with gas accumulating in an enclosed space. Because hydrogen is 14 times lighter than air, it will rise and collect near the ceiling or in poorly ventilated pockets, forming a hidden threat. The danger zone isn't just near the furnace; it can be anywhere the gas travels. I recall a safety bulletin from an industry association detailing an incident where a leak from a furnace's supply line traveled along a ceiling conduit and was ignited by a standard light fixture 20 meters away. This illustrates that the hazard is not localized. The immediate consequence is, of course, fire or explosion, which carries the highest risk of injury or death. Beyond that, even a small, non-explosive fire can damage critical control wiring, sensors, and plumbing, leading to a loss of control over the entire annealing process. This secondary failure can then lead to other problems, like overheating the furnace or creating off-spec products. The financial and operational fallout from even a "minor" incident can be staggering, making leak prevention the single most important safety objective.
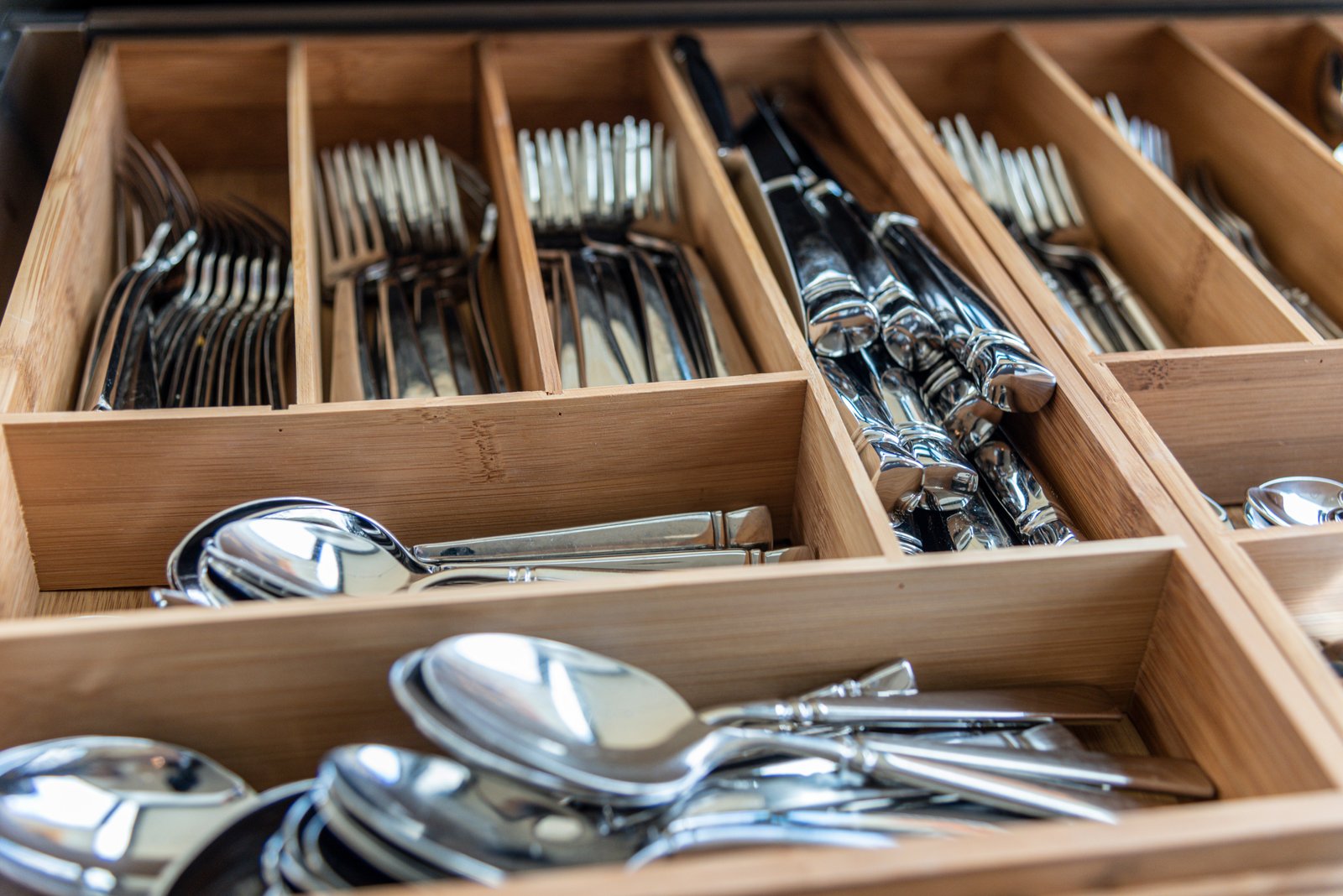
When a hydrogen leak occurs, its impact on safety is not a single event but a chain reaction of physical hazards, operational disruptions, and long-term consequences. Understanding the full spectrum of these impacts is essential for appreciating why a multi-layered safety approach is non-negotiable. The focus must shift from simply meeting minimum compliance to building a resilient system that anticipates and neutralizes these threats proactively. At AKS, our design philosophy is built around containing these impacts at the earliest possible stage, often through automated systems that act faster than any human operator could.
Immediate Safety Hazard: Fire and Explosion
The most immediate and severe impact of a hydrogen leak is the risk of combustion. As established, hydrogen's wide flammability range and low ignition energy mean that a hazardous atmosphere can form and ignite with frightening ease. An explosion within the furnace itself, caused by air ingress mixing with the hydrogen atmosphere, can rupture the furnace body, sending shrapnel and a fireball into the plant. An external leak that finds an ignition source can cause a flash fire or, if confined within a building, a deflagration or detonation that can level structures BS EN 60079-10-1:2020 guidelines3.
Consider a typical continuous bright annealing line for stainless steel strips, which can be over 50 meters long. The volume of hydrogen within the furnace at any given time can be substantial. A catastrophic failure and ignition could be devastating. Industry data from organizations like the Chemical Safety Board (CSB) in the United States repeatedly highlights incidents where gas leaks in industrial facilities led to explosions with tragic consequences. While not all are hydrogen-specific, the physics are the same. For example, the CSB investigation into the 2005 BP Texas City refinery explosion4 found that a release of flammable liquid and vapor led to a blast that killed 15 workers and injured 180 more. This serves as a stark reminder of the energy potential stored in flammable materials.
The immediate risk to personnel is paramount. Burns from a flash fire, injuries from flying debris, or death from the blast wave are the primary concerns. This is why modern safety protocols, such as those outlined in NFPA standards, mandate specific exclusion zones, ventilation requirements, and the use of explosion-proof (Class I, Division 2) electrical fittings in areas where hydrogen may be present.
Secondary Impact: Equipment Damage and Production Loss
Assuming an incident does not result in a catastrophic explosion, the secondary impacts are still severe. A hydrogen fire, even a small one, can cause immense damage. The high temperature of a hydrogen flame can melt control cables, destroy sensitive electronics in control panels, and damage pneumatic or hydraulic lines. This can lead to a complete loss of furnace control, requiring a total shutdown and extensive, costly repairs.
Let's imagine a scenario for a client producing high-end kitchenware. A minor leak from a valve packing ignites. The fire is quickly extinguished, and no one is hurt. However, the flame impinged on a nearby control cabinet for 30 seconds. This was enough to melt the insulation on the wiring for the furnace's main heating elements and the speed controller for the conveyor belt. The furnace is now inoperable. Sourcing a new, custom-programmed control panel could take weeks. In the meantime, production is at a standstill. Orders are delayed, penalties are incurred, and customer confidence is eroded.
The cost of this downtime often dwarfs the cost of the physical repairs. For a medium-sized stainless steel strip plant, lost production can amount to tens or even hundreds of thousands of dollars per day. This is a powerful financial argument for investing in preventative measures like advanced leak detection and automated shutoff valves, which can isolate a leak and shut down the system before a fire can even start.
Long-Term Consequences: Regulatory, Financial, and Reputational Damage
The long-term fallout from a hydrogen safety incident can be the most damaging of all. Following any fire or explosion, a rigorous investigation by regulatory bodies like OSHA in the U.S. or equivalent authorities in other countries is guaranteed. If they find evidence of negligence, inadequate training, or non-compliance with safety standards, the company can face crippling fines and mandated operational changes.
One of our clients, before they partnered with us, faced such a scenario. A small, contained incident led to an audit that uncovered systemic issues in their safety protocols and record-keeping. The fines were substantial, but the mandated remediation plan was even more costly, requiring them to retrofit their entire gas handling system and retrain their entire workforce under regulatory supervision. This process took nearly six months and severely impacted their market position.
The reputational damage can be permanent. In today's interconnected world, news of a major industrial accident spreads instantly. This can damage a company's brand, making it difficult to secure new business, especially with large, safety-conscious international clients. Internally, it can destroy morale and create a culture of fear, leading to higher employee turnover and difficulty in recruiting skilled engineers and operators. The cost of safety is always less than the cost of an accident.
Hydrogen leaks create explosion risksПравда
Hydrogen's wide flammability range and low ignition energy make leaks extremely dangerous, capable of causing catastrophic explosions.
Hydrogen leaks only affect furnace areasЛожь
Hydrogen can travel far from the leak source due to its lightness, creating hazards in unexpected locations like ceiling conduits.
What solutions exist for effective hydrogen leak detection and management?
Ready to move from worrying about leaks to actively preventing them? Effective management isn't just about hoping for the best. It's about implementing a robust system of advanced sensors, intelligent furnace design, and automated safety interlocks that detect and control leaks before they become a critical threat, ensuring operational safety and peace of mind.
Effective solutions include installing a network of fixed hydrogen sensors (catalytic, electrochemical, or thermal conductivity) at potential leak points. These are integrated with a central control system that triggers audible/visual alarms and automated emergency shutdowns. Robust furnace design with high-integrity seals and positive pressure control is also crucial.
The modern approach to hydrogen safety is built on the principle of "defense in depth." This means we don't rely on a single solution but instead create multiple, overlapping layers of protection. When I work with a client to design a new bright annealing line, our conversation about safety focuses on three core pillars: Detection, Engineering Controls, and Administrative Procedures. Detection is about finding a leak as early as possible. Engineering Controls are about designing the furnace and its systems to prevent leaks from occurring in the first place and to contain them if they do. Administrative Procedures are about ensuring the human element—the operators and maintenance teams—are a strength, not a weakness. It’s the seamless integration of these three pillars that transforms a potentially hazardous process into a safe, reliable, and highly efficient operation. We can't eliminate the hazard of hydrogen, but we can, and must, manage the risk down to a negligible level. This comprehensive strategy is the only way to operate with confidence and unlock the full quality benefits of hydrogen annealing.
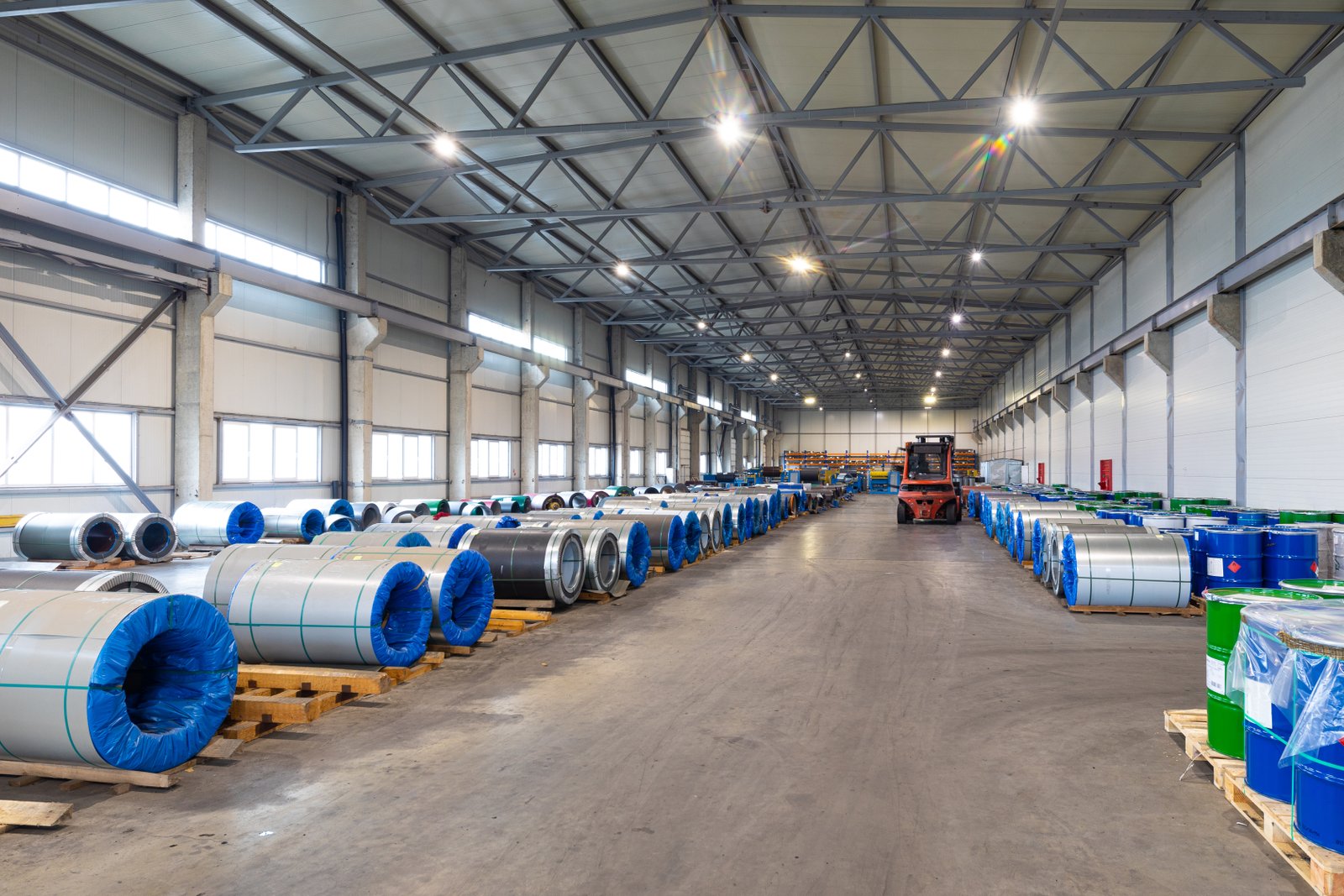
To build a truly resilient hydrogen safety system, we must move beyond a simple "install a detector" mindset. A holistic solution integrates advanced technology with fundamental engineering principles and rigorous human protocols. It's an ecosystem where each part supports the others. For example, a state-of-the-art sensor is of little use if the furnace seals are poorly designed and leak constantly. Likewise, a perfectly engineered furnace can be compromised by an untrained operator. At AKS, we champion an integrated approach, ensuring that the technology, the hardware, and the personnel are all aligned towards the single goal of safe and uninterrupted operation.
Advanced Sensor Technologies for Real-Time Monitoring
The first line of active defense is a network of strategically placed hydrogen detectors. There is no single "best" sensor type; the choice depends on the specific location and application. For general area monitoring in open, well-ventilated spaces around the furnace, catalytic bead sensors are a cost-effective choice. They are robust and reliably detect hydrogen as a percentage of its Lower Explosive Limit (%LEL). Typically, an alarm will be triggered at 10-20% LEL (which corresponds to 0.4%-0.8% hydrogen in air), providing a very early warning long before a dangerous concentration is reached.
For more sensitive locations, such as inside enclosed cabinets or near critical valve manifolds, electrochemical sensors are often preferred. They can detect hydrogen at much lower, parts-per-million (ppm) concentrations and are less prone to being "poisoned" by other chemicals in the atmosphere. For monitoring the purity of the atmosphere inside the furnace or in a vent stack, where concentrations are expected to be high, thermal conductivity (TC) sensors are used. They work on the principle that hydrogen has a much higher thermal conductivity than air or nitrogen and are excellent for process control and high-concentration leak detection.
A typical AKS furnace installation for a client processing automotive exhaust components would feature a combination of these sensors. Catalytic sensors would be placed above the furnace entry and exit points. Electrochemical sensors would monitor the valve train enclosure. A TC sensor would continuously analyze the furnace atmosphere to ensure hydrogen purity and detect any significant air ingress. All these sensors are wired back to a central safety PLC (Programmable Logic Controller)5 that initiates automated responses.
Integrated Furnace Design and Engineering Controls
Sensor technology is reactive; superior engineering is proactive. The most fundamental engineering control is the integrity of the furnace itself. The furnace muffle and all connecting pipework must be 100% gas-tight. This is verified through pressure decay testing and helium leak checks during commissioning. The design of the furnace seals is paramount. At AKS, we have moved beyond simple fiber ropes to sophisticated, multi-layer sealing systems. For our premium Bright Annealing Furnaces, we often use a combination of a water-cooled jacket, a primary silicone or graphite seal, and a secondary fiber seal, with the space between them purged with nitrogen. This creates a virtually impenetrable barrier.
Maintaining a slight positive pressure ($>50$ Pascals) inside the furnace is a critical, yet simple, engineering control. Our control systems use precision mass flow controllers and back-pressure regulators to keep the internal furnace pressure just above ambient atmospheric pressure. This ensures that if any microscopic leak path were to develop, clean hydrogen would flow out, rather than oxygen-rich air flowing in. This single principle prevents the formation of an explosive mixture inside the hottest, most dangerous part of the system.
Furthermore, we design for failure. This means including engineered safety features like emergency purge systems and pressure relief valves. If the main control system fails or a blockage occurs, a rupture disc or safety valve will safely vent excess pressure to a designated, safe location outside the building, preventing a catastrophic over-pressurization of the furnace body.
Sealing Mechanism | Типовое применение | Преимущества | Недостатки |
---|---|---|---|
Fiber Rope Seal | Basic batch furnaces, low pressure | Low cost, simple to install | Degrades with use, prone to leaks |
Silicone/Rubber Seal | Furnace doors, inspection ports | Excellent sealing when new, flexible | Limited temperature range, ages poorly |
Water-Cooled Seal | Continuous furnace entry/exit | Cools the seal area, extends life | Complex, requires water supply |
Nitrogen Purge Box | High-end continuous furnaces | Creates inert barrier, double protection | Higher inert gas consumption |
Double Seal w/ Purge | Premium/High-Safety Furnaces | Redundant safety, highest integrity | Highest initial cost and complexity |
Administrative Controls and Proactive Maintenance
The final layer of protection is the human system. This includes comprehensive training, strict Standard Operating Procedures (SOPs), and a robust preventative maintenance program. Every operator and maintenance technician must be trained on the properties of hydrogen, the specific design of their furnace, and the emergency procedures. This training should not be a one-time event but a continuous process with regular refreshers and drills. For a large stainless steel coil processor in India, we helped develop a "lock-out, tag-out" (LOTO) procedure specifically for their hydrogen system, ensuring that lines are safely isolated and purged before any maintenance work begins.
SOPs must cover every phase of operation: startup, normal operation, shutdown, and emergency response. The startup and shutdown sequences are particularly critical to ensure proper purging of oxygen before introducing hydrogen and purging of hydrogen before introducing air. Automating these critical sequences, as we do in our AKS furnace control systems, is the best way to ensure they are followed perfectly every single time, removing the risk of human error.
Preventative maintenance must be diligent and well-documented. This includes a regular schedule for inspecting and replacing high-wear items like seals, gaskets, and flexible hoses. It also involves periodically using a portable leak detector to survey the entire gas delivery system, from the storage tanks to the furnace. By finding and fixing small leaks before they grow, you not only enhance safety but also reduce the operational cost of wasted hydrogen. This proactive approach turns maintenance from a cost center into a critical risk management function.
Multiple sensor types are usedПравда
Different hydrogen sensors (catalytic, electrochemical, thermal conductivity) are strategically placed based on location needs.
One sensor type fits all locationsЛожь
Sensor selection depends on environment - catalytic for open areas, electrochemical for enclosed spaces, TC for high concentrations.
What are the best practices for maintaining safety during bright annealing of stainless steel?
Are you aiming for a zero-incident safety record in your annealing operations? The best practices go beyond the furnace itself. They encompass a holistic safety culture, starting from how you store hydrogen to the rigorous training of your team and the implementation of automated, failsafe shutdown procedures. It's about creating an inherently safe system.
Best practices include implementing a multi-layered safety system: robust furnace engineering with automated purging, a network of fixed and portable hydrogen detectors, strict adherence to Standard Operating Procedures (SOPs), comprehensive operator training on hydrogen hazards, and a rigorous preventative maintenance schedule for all gas-handling components.
Over my career, I've seen that the safest plants are not necessarily the ones with the newest equipment, but the ones with the strongest safety culture. Best practices are not a checklist to be completed; they are a mindset that permeates every level of the organization. It starts with the storage and handling of hydrogen long before it even reaches the furnace. It extends to the detailed design of the control system's logic and alarms. And most importantly, it resides in the minds of the people who run and maintain the equipment every day. When a new client in North America was looking to build a state-of-the-art facility for processing high-strength steel strips, their primary concern was integrating world-class safety from the ground up. We worked with them to develop a comprehensive plan that treated the annealing line not as a standalone machine, but as a critical part of a larger, integrated factory ecosystem. This holistic view, which combines engineering, procedures, and people, is the true hallmark of best-in-class safety.
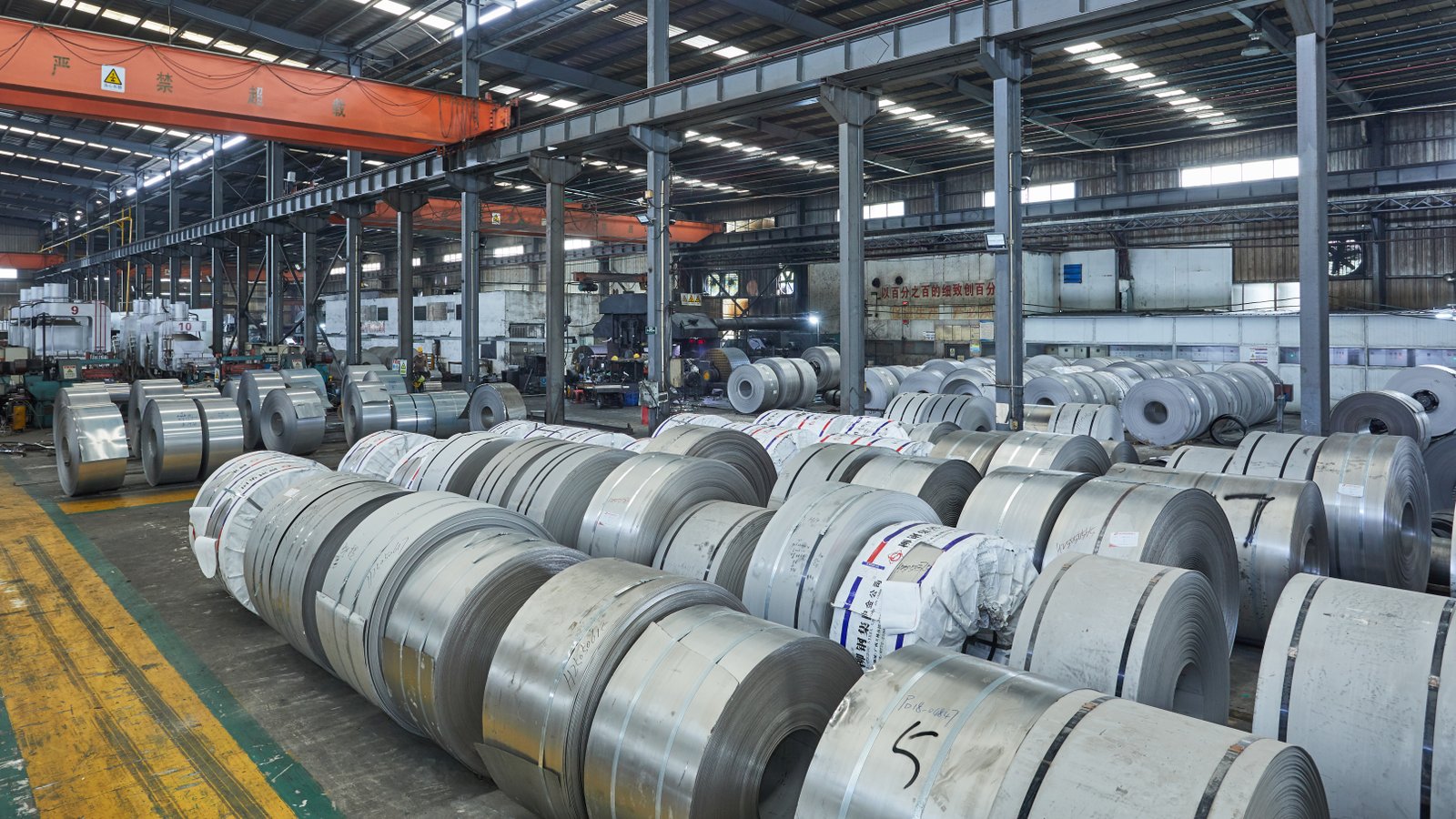
Achieving excellence in safety during the bright annealing of stainless steel requires a commitment to a systematic, multi-faceted strategy. It's a continuous cycle of design, implementation, training, and improvement. The "best practices" are not static; they evolve with technology and our understanding of risk. However, they are founded on unchanging principles: control the substance, detect any deviation, and prepare for any contingency. This framework ensures that safety is not just an add-on feature but is woven into the very fabric of the manufacturing process, protecting personnel, assets, and the company's future.
The Three Pillars of Hydrogen Safety Management
The foundation of best practices can be structured around three core pillars: Asset Integrity, Process Control, and Human Factors. Asset Integrity refers to the physical equipment—the storage, the piping, and the furnace itself. It must be designed, built, and maintained to be fundamentally sound and resistant to failure. This starts with proper hydrogen storage6. According to NFPA 2 guidelines, bulk hydrogen should be stored outdoors, with adequate separation distances from buildings, ignition sources, and process equipment. The piping that transfers the gas must be of a compatible material (e.g., 316L Stainless Steel), with all-welded joints where possible to minimize potential leak points from mechanical fittings.
The furnace itself is the most critical asset. As we've discussed, this involves robust, gas-tight construction, high-integrity seals, and materials resistant to hydrogen embrittlement. A key best practice that we champion at AKS is the incorporation of a formal preventative maintenance program tied to operational hours. For instance, a door seal might be visually inspected weekly, leak-checked monthly, and automatically scheduled for replacement after every 2,000 hours of operation, regardless of its apparent condition. This data-driven approach prevents failures before they happen.
Process Control is the second pillar. This is the domain of automation and instrumentation. The system must be able to automatically maintain safe conditions and take corrective action if they deviate. A key practice is the full automation of startup and shutdown purging sequences. The control system should prevent the flow of hydrogen until a sensor confirms that the oxygen level inside the furnace is below a safe threshold (typically <1%). Similarly, it should prevent the furnace door from being opened until the hydrogen has been purged and replaced with an inert atmosphere. This removes the single greatest opportunity for human error in the process. Another critical practice is the integration of leak detectors with an Emergency Shutdown System (ESD). Upon detection of a leak (e.g., at 20% LEL), the ESD should automatically close the main hydrogen supply valve, activate the nitrogen emergency purge, and sound a plant-wide alarm.
Human Factors: Training and Procedural Discipline
The third pillar, Human Factors, is arguably the most important and the most challenging. Even the most advanced system can be defeated by a lack of awareness or discipline. A best-in-class safety program invests heavily in training. Every person who interacts with the furnace, from operators to maintenance staff to plant managers, must receive role-specific training on the risks of hydrogen and the established safety procedures. This training should be documented, and competency should be regularly assessed. We often work with clients to develop custom training modules, including simulated emergency drills, to ensure the response to an alarm is automatic and correct.
Procedural discipline is the cornerstone of managing human factors. Standard Operating Procedures (SOPs) must be clear, concise, and readily available. They must be strictly enforced. A "permit to work" system for all non-routine maintenance is a crucial best practice. Before any work begins on the hydrogen system, a formal permit must be issued, which confirms that all isolation and safety procedures (like LOTO) have been correctly implemented.
Lastly, fostering a strong safety culture is essential. This is a culture where every employee feels empowered and responsible for safety. It means encouraging the reporting of near-misses and unsafe conditions without fear of blame. Management must lead by example, consistently prioritizing safety over production speed. When a plant manager puts on their safety glasses before entering the shop floor, it sends a more powerful message than any memo ever could. This cultural commitment is the glue that holds all other best practices together.
Continuous Improvement and Auditing
Safety is not a destination; it's a journey. A world-class safety program embraces continuous improvement. This means regularly reviewing and updating procedures based on new technology, industry incident reports, and internal experience. Regular safety audits, performed by both internal teams and qualified third-party experts, are essential. These audits provide a fresh perspective and can identify gaps or instances of "procedural drift" that internal teams may have become accustomed to.
For a major steel processor in Europe, we participate in their annual safety audit of the annealing line we installed. This collaborative review has led to several enhancements over the years, including upgrading their initial point detectors to a more advanced ultrasonic leak detection system that can "hear" the high-frequency sound of a gas leak, providing even faster detection. It also led to software logic updates to further optimize the purge cycle, saving them nitrogen while enhancing safety. This commitment to iterative improvement is what distinguishes an adequate safety program from an excellent one. It ensures the system remains robust and resilient against risks for the entire life of the asset.
Hydrogen storage requires outdoor placementПравда
NFPA 2 guidelines mandate outdoor hydrogen storage with proper spacing from buildings and ignition sources for safety.
Door seals should only be replaced when visibly damagedЛожь
Preventative maintenance schedules require periodic replacement of door seals based on operational hours, regardless of visible condition.
Заключение
Ultimately, ensuring hydrogen safety is not about a single gadget but a total system. It integrates robust engineering like our AKS furnaces, diligent leak detection, and rigorous, well-practiced safety protocols. This holistic approach is how you confidently achieve superior stainless steel quality.
-
Learn about NFPA 86 standards for hydrogen safety in industrial applications ↩
-
Understand hydrogen's wide flammability range and safety implications ↩
-
Discover guidelines for explosion prevention in hydrogen-enriched environments. ↩
-
Understand the incident for insights into industrial safety and accident prevention. ↩
-
Discover the role of safety PLCs in automating safety responses in furnace operations. ↩
-
Understand safety standards for storing hydrogen in industrial applications ↩