Когда следует модернизировать процесс отжига, включив в него рециркуляцию водорода?
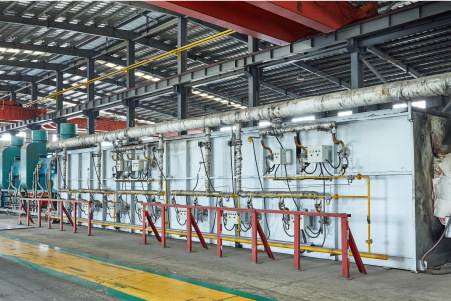
Are you watching your operational costs climb, driven by the relentless consumption of hydrogen in your annealing furnaces? This constant expense eats directly into your profit margins and leaves your business vulnerable to volatile gas prices. An upgrade to a hydrogen recycling system can be the strategic shift you need.
Upgrading your annealing process to include hydrogen recycling is advisable when you face high hydrogen consumption costs, aim to meet stringent sustainability goals, or require enhanced process consistency for superior product quality. It's a strategic move for businesses seeking long-term operational efficiency and cost control.
The idea of another capital investment might seem daunting at first. However, the long-term benefits often far outweigh the initial outlay. It’s not just about saving money on gas; it’s about creating a more resilient, efficient, and higher-quality production line. We need to look past the price tag and analyze the full scope of returns that such an upgrade can deliver to your entire operation.
This isn't merely a conversation about adding a piece of equipment; it's about fundamentally rethinking resource management within your heat treatment process. In an era where both economic and environmental pressures are mounting, viewing hydrogen as a recyclable asset rather than a disposable consumable is a critical strategic pivot. Industry leaders are no longer asking если they should optimize resource use, but как и how quickly. At AKS, we've seen firsthand how integrating advanced systems like hydrogen recycling, often as part of a comprehensive furnace design, aligns with Industry 4.0 principles. It future-proofs your operations against market volatility and regulatory shifts, with some of our clients cutting hydrogen consumption by over 90%.
What are the key benefits of hydrogen recycling in the annealing process?
Are you constantly battling high operational expenses from your annealing line, with hydrogen costs being a major, uncontrollable factor? This spending directly reduces your profit margins and exposes your business to supply chain vulnerabilities for industrial gases. Implementing a hydrogen recycling system offers substantial, measurable benefits beyond simple cost savings.
The key benefits of hydrogen recycling in the annealing process include a dramatic reduction in operational costs by minimizing hydrogen consumption, enhanced metallurgical consistency due to a stable furnace atmosphere, and a significantly improved environmental footprint. It also boosts operational autonomy by reducing reliance on external gas suppliers.
These advantages might seem straightforward on paper, but their real-world impact on a manufacturing floor is transformative. I recall working with a major stainless steel strip processor in Southeast Asia who was struggling with razor-thin margins. Their monthly hydrogen bill was one of their top three operational expenditures, a constant source of financial pressure. Initially, they were hesitant about the capital investment required for an integrated recycling unit. They questioned whether the returns would justify the cost. However, as we walked them through the data and projected the long-term impact, the conversation shifted. It became clear that this wasn't an expense, but an investment in resilience and quality. Over the next few sections, I'll use their journey to illustrate how each benefit—cost savings, process stability, and sustainability—translates into tangible operational improvements and a more robust bottom line. Their story is a powerful testament to how strategic technology adoption can redefine a company's competitive edge.
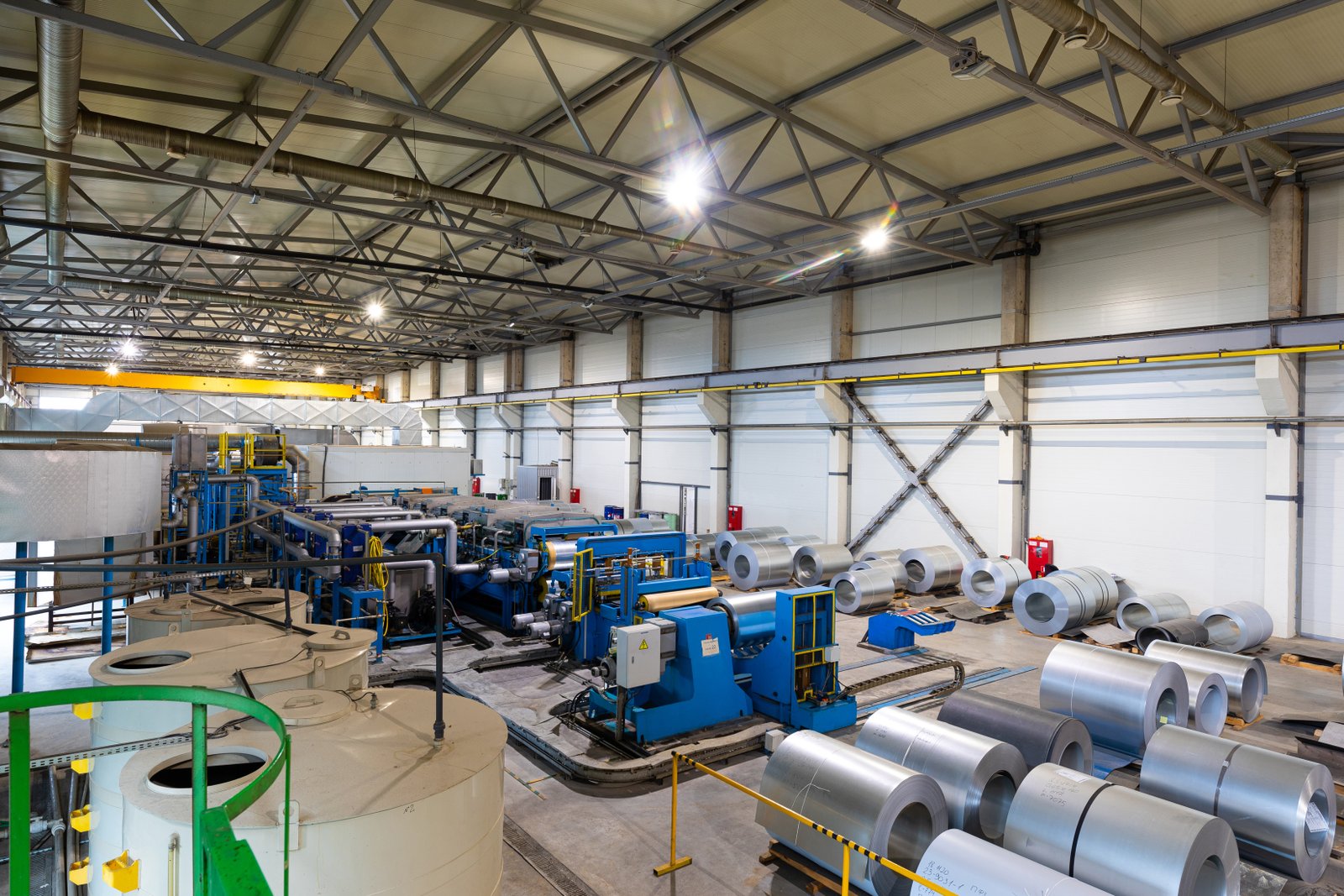
Achieving Radical Cost Reduction and Supply Chain Independence
The most immediate and quantifiable benefit of installing a hydrogen recycling system is the drastic reduction in operational expenditure (OPEX). For many metal processors, particularly those running continuous bright annealing furnaces, hydrogen is a significant and recurring cost. A standard annealing process consumes a continuous flow of hydrogen to maintain a protective atmosphere, with the vast majority of this gas being vented as waste. A recycling system captures this vented hydrogen, purifies it, and returns it to the furnace, effectively creating a closed-loop process. This can reduce the need for new hydrogen purchases by up to 95%, a figure we've seen consistently achieved by our clients.
To put this into perspective, consider a medium-sized facility processing stainless steel strips. They might consume thousands of cubic meters of hydrogen every month. With fluctuating market prices for industrial gas, this represents a massive and unpredictable financial liability. By recycling the hydrogen, the company only needs to purchase a small amount of "makeup" gas to compensate for minor losses in the system. The savings are direct, substantial, and immediate, flowing directly to the company's bottom line and freeing up capital for other strategic investments, such as R&D or market expansion.
I worked closely with a manufacturer of automotive exhaust components in India who faced this exact challenge. Intense price pressure in their market meant that every rupee saved was critical. Their AKS bright annealing furnace was efficient, but their hydrogen consumption was a major pain point. After we integrated one of our hydrogen recycling systems into their existing line, they documented a 92% reduction in new hydrogen purchases within the first six months. This wasn't just a number on a spreadsheet; it was the financial leverage they needed to fund a new product line, ultimately strengthening their position against competitors. Beyond cost, they gained crucial independence from their local gas supplier, insulating them from price hikes and delivery disruptions that had previously halted production.
Enhancing Metallurgical Consistency and Product Quality
While cost savings are compelling, the impact of hydrogen recycling on product quality and process stability is equally significant. In bright annealing, the primary goal is to produce a clean, oxide-free surface finish. This requires an incredibly stable and pure furnace atmosphere. Any fluctuation in the composition or pressure of the protective gas can introduce oxygen or water vapor, leading to surface oxidation, discoloration, and inconsistent metallurgical properties. These defects can result in entire batches being rejected, leading to wasted material, time, and energy.
A hydrogen recycling system inherently enhances stability. By creating a closed loop, it provides a continuous supply of purified hydrogen at a constant pressure and flow rate. This eliminates the variables introduced when switching between gas cylinders or tanks, which can differ slightly in purity and pressure. The purification unit within the recycling system actively removes contaminants like oxygen and moisture that could compromise the annealing atmosphere, ensuring that the hydrogen returning to the furnace is of consistently high quality. This level of control is critical for manufacturers of high-value products, such as electronics hardware or premium stainless steel kitchenware, where a flawless finish is non-negotiable.
A client in the electronics sector, a producer of high-precision connectors, was experiencing a frustratingly high rejection rate. Their components required a perfectly bright finish for subsequent plating processes. Our analysis revealed that minor atmospheric inconsistencies during the annealing cycle were the culprit. After upgrading their line with an AKS furnace featuring an integrated hydrogen recycling system, they achieved a level of atmospheric stability they couldn't before. Their rejection rate due to surface defects dropped by over 15% in the first quarter. This not only saved them money on scrap but also enhanced their reputation with their customers for delivering consistently superior quality.
Meeting Sustainability Goals and Boosting Brand Image
In today's global market, sustainability is no longer a niche concern; it's a core business imperative. Customers, especially those in European and North American markets, are increasingly scrutinizing the environmental credentials of their suppliers. A company's carbon footprint and resource management practices can directly impact its ability to win and retain business. Implementing a hydrogen recycling system is a powerful and demonstrable step towards environmental responsibility. By drastically reducing hydrogen consumption, a company also reduces the significant energy and carbon footprint associated with producing and transporting that hydrogen.
This commitment to sustainability becomes a valuable asset for a company's brand image and market positioning. It allows them to meet the stringent Environmental, Social, and Governance (ESG) criteria set by many large corporations and investment funds. For export-oriented manufacturers, being able to provide clear data on reduced environmental impact can be a decisive competitive advantage, opening doors to new markets and premium customers who prioritize sustainable sourcing. It transforms an operational detail into a compelling marketing story.
The table below provides a clear comparison of the two approaches, which we often use to help clients visualize the impact. This data is crucial for both internal decision-making and external communication. For an OEM/ODM factory producing stainless steel sinks, being able to show a major European home appliance brand that their manufacturing process is verifiably "greener" is a powerful selling point. It elevates the conversation from price per unit to partnership in sustainable value creation, strengthening business relationships and securing long-term contracts.
Характеристика | Traditional Process (No Recycling) | Process with Hydrogen Recycling |
---|---|---|
Hydrogen Consumption | 100% (Continuous Feed) | 5-10% (Makeup Gas Only) |
Воздействие на окружающую среду | High (Energy for H2 production & transport) | Low (Reduced consumption & transport) |
Operational Cost | High and Variable | Low and Predictable |
Стабильность процесса | Susceptible to supply fluctuations | High (Closed-loop consistency) |
Hydrogen recycling reduces operational costsПравда
Implementing hydrogen recycling can cut new hydrogen purchases by up to 95%, significantly lowering operational expenses.
Hydrogen recycling decreases product qualityЛожь
Hydrogen recycling actually improves product quality by maintaining a more stable and pure furnace atmosphere.
How does hydrogen recycling impact the ROI of the annealing process?
Are you concerned that the upfront cost of a hydrogen recycling system will negatively impact your company's finances? It's a valid question, as any capital expenditure must be justified by clear and compelling returns. However, viewing it solely as a cost overlooks its powerful potential as a revenue-generating investment. The ROI of hydrogen recycling is multifaceted and deeply impactful.
Hydrogen recycling directly boosts the ROI of the annealing process by drastically cutting operational expenses on gas, reducing product rejection rates, and lowering labor costs. This combination of savings accelerates the payback period and increases the overall profitability and net present value of the annealing line.
The financial case for hydrogen recycling is one of the strongest I've seen for any furnace upgrade. The savings aren't marginal; they are substantial and begin accumulating from day one of operation. To understand the full picture, we need to move beyond a simple cost-benefit glance and dig into the specific financial metrics that define a successful investment. It’s about calculating the payback period, understanding the Net Present Value (NPV) of the investment1 over its lifecycle, and even accounting for the intangible returns like improved brand image and market access. A client in the carbon steel strip industry initially focused only on the purchase price. But when we broke down their annual hydrogen expenditure—a figure that ran into hundreds of thousands of dollars—and modeled the ROI, they saw the upgrade not as a purchase, but as a high-yield investment in their own operational efficiency.
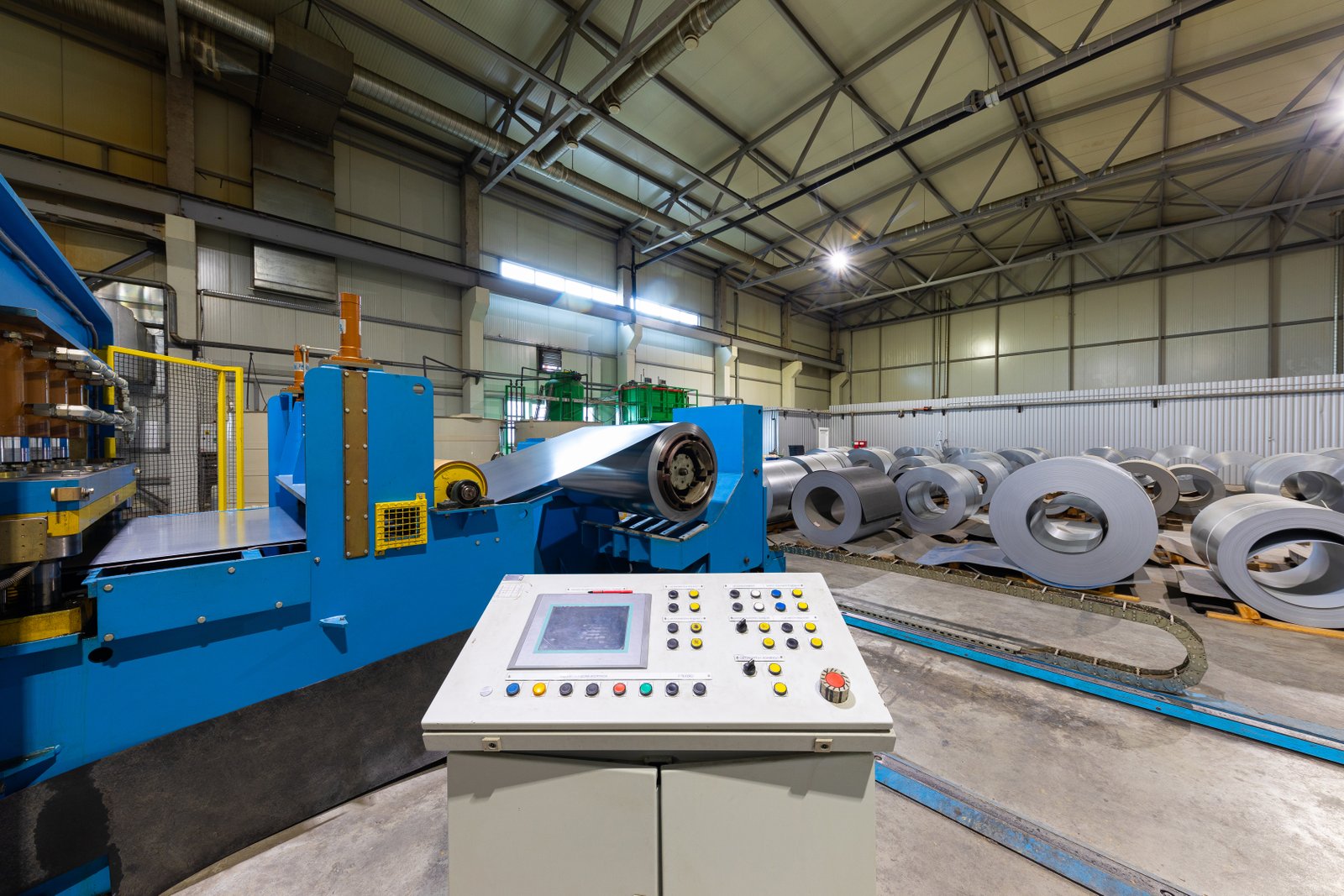
Deconstructing the Payback Period
The payback period is the most straightforward metric for evaluating the ROI of a hydrogen recycling system. It answers a simple question: "How long will it take for the investment to pay for itself?" The calculation is direct: divide the total initial investment (CAPEX) by the annual savings generated (OPEX reduction). The initial investment includes the cost of the recycling unit, installation, and any necessary modifications to your existing furnace line. At AKS, we often design furnaces with recycling systems fully integrated, which can streamline this process and reduce installation complexity.
The annual savings are primarily driven by the massive reduction in hydrogen purchases2. If a plant spends $200,000 annually on hydrogen and the recycling system cuts that by 90%, the direct saving is $180,000 per year. Additional savings come from reduced labor associated with handling and changing gas cylinders, lower transportation and storage costs, and decreased administrative overhead for procurement. For many of our medium-to-large scale clients, the payback period for a hydrogen recycling unit is surprisingly short, often falling within 12 to 24 months.
A producer of copper strips for the electronics industry provides a compelling case. Their initial investment in an AKS recycling system was approximately $250,000. Their audited savings on hydrogen, labor, and logistics in the first year totaled over $190,000. This resulted in a payback period of just under 16 months. After this point, the system transitioned from paying for itself to generating a significant positive cash flow for the company every single year, directly increasing the profitability of their entire annealing operation. This rapid return is a key reason why the adoption of this technology is accelerating globally.
Analyzing Long-Term Value with Net Present Value (NPV)
While the payback period is useful, a more sophisticated analysis involves calculating the Net Present Value (NPV) of the investment. NPV accounts for the time value of money, recognizing that a dollar saved today is worth more than a dollar saved in the future. This method projects the cash flows (the annual savings) generated by the recycling system over its entire operational lifespan—typically 10-15 years—and discounts them back to their present value. A positive NPV indicates that the investment's projected earnings, in today's dollars, exceed the initial cost.
Calculating NPV provides a much clearer picture of long-term profitability. It forces a strategic view, moving the conversation beyond a quick payback to the sustained value the asset will create over many years. The key inputs are the initial investment, the expected annual savings, the lifespan of the equipment, and a discount rate (which typically represents the company's cost of capital or a target rate of return). In virtually every scenario we've modeled for clients, the NPV of a hydrogen recycling system is overwhelmingly positive, often by a factor of three to five times the initial investment.
Consider our previous example of the copper strip producer. While their 16-month payback was impressive, the NPV analysis was even more so. Assuming a 10-year lifespan and a conservative discount rate of 8%, the NPV of their $250,000 investment was calculated to be over $900,000. This demonstrated to their executive team that the project wasn't just operationally sound; it was a powerful financial instrument that would create significant shareholder value for a decade or more. This type of analysis is crucial for securing internal buy-in for capital-intensive projects.
The Critical Role of Intangible and Qualitative Returns
A complete ROI analysis cannot ignore the intangible benefits, even if they are harder to quantify in dollars and cents. These qualitative returns often have a profound strategic impact on the business. For instance, enhanced product quality and consistency directly lead to increased customer satisfaction and loyalty. A reputation for flawless quality is a priceless asset that can command premium pricing and secure long-term contracts, creating a virtuous cycle of profitability. How much is it worth to eliminate a customer complaint about surface finish?
Furthermore, supply chain resilience is a critical intangible benefit. By becoming nearly self-sufficient in its hydrogen supply, a company shields itself from market shocks, such as gas shortages or sudden, steep price increases. This stability allows for more accurate production planning and financial forecasting. This reliability is highly valued by customers, particularly in industries like automotive and aerospace where supply chain disruptions can have cascading and costly effects. This makes the company a more dependable—and therefore more attractive—partner.
Crucially, the value of an enhanced brand image driven by a demonstrable commitment to sustainability should not be underestimated. This can be a key differentiator in a crowded market. We've seen clients leverage their "green" credentials to win contracts with large, multinational corporations that have strict ESG mandates for their suppliers. While you may not be able to put a precise dollar value on it initially, the access to new markets and premium customers that it unlocks contributes significantly to the overall ROI. When you combine these powerful intangibles with the hard financial data from payback and NPV calculations, the case for hydrogen recycling becomes not just strong, but strategically essential.
Financial Metric | Описание | Typical Result for H2 Recycling | Strategic Implication |
---|---|---|---|
Payback Period | Time required for savings to offset the initial investment. | 12-24 Months | Rapid return of capital, quick path to profitability. |
Net Present Value (NPV) | The total long-term value of the investment in today's dollars. | Highly Positive (3-5x CAPEX) | Creates significant, sustained shareholder value. |
Intangible Returns | Benefits like quality improvement, brand image, and supply chain resilience. | Высокий | Strengthens competitive position and market access. |
Hydrogen recycling reduces operational costsПравда
The text clearly states hydrogen recycling cuts gas purchases by 90%, reduces labor costs, and eliminates logistics expenses.
NPV ignores intangible benefitsЛожь
While NPV focuses on quantifiable cash flows, the text emphasizes that a complete ROI analysis must also consider intangible benefits like brand image and supply chain resilience.
What are the indicators that suggest it's time to upgrade to hydrogen recycling?
Are you wondering if your operation has reached the tipping point where investing in hydrogen recycling makes strategic sense? The decision to upgrade is often driven by a combination of clear financial, operational, and market signals. Ignoring these indicators can mean leaving significant savings and competitive advantages on the table.
Key indicators that it's time to upgrade to hydrogen recycling include consistently high and rising hydrogen expenditures, increased production volumes that amplify gas consumption, stringent customer requirements for product quality and consistency, and growing pressure to meet corporate or regulatory sustainability targets.
Recognizing these signs early is crucial for proactive management. It’s about shifting from a reactive stance—where you're simply paying the monthly gas bill—to a strategic one where you actively control and optimize one of your key process inputs. I often speak with plant managers who have normalized high hydrogen costs as a "cost of doing business." However, once we start analyzing their operational data3 together, a clear picture emerges. The indicators point towards an opportunity for transformative change. Let’s explore these signals in detail, so you can confidently assess whether now is the right time for your business to make the upgrade.
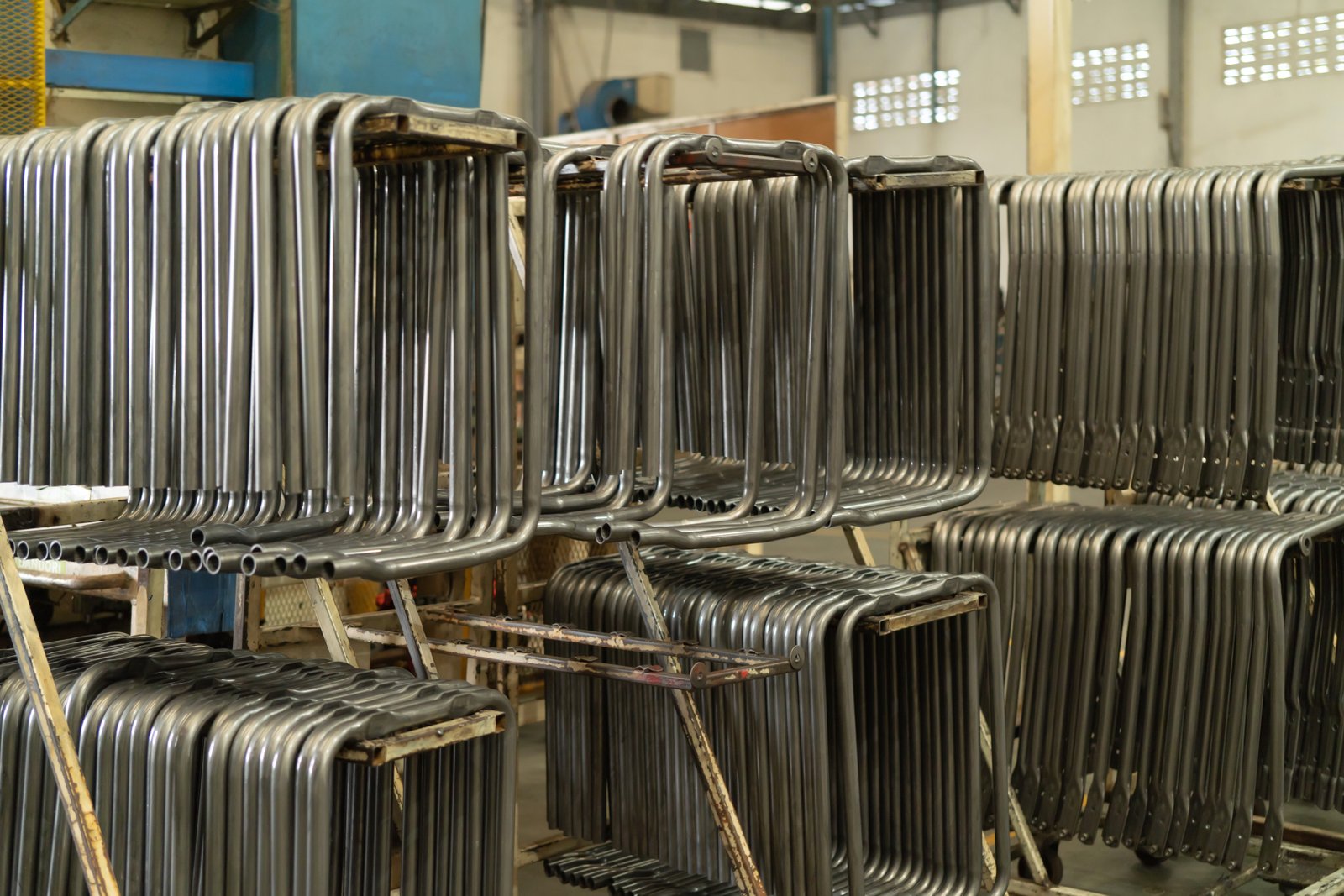
Analyzing Your Financial and Operational Metrics
The most obvious indicator is found in your accounting records and operational logs. Start by tracking your hydrogen consumption and expenditure over the last 12-24 months. Is the cost consistently high? More importantly, is it trending upward? Volatility in the industrial gas market can wreak havoc on budgeting and forecasting. If your monthly hydrogen bill is a significant line item that you have little control over, it's a primary signal that a closed-loop recycling system is needed. This moves the cost from a variable operational expense to a predictable, fixed capital amortization.
Next, look at your operational logistics. Are your teams frequently handling and changing heavy, high-pressure gas cylinders or managing bulk liquid hydrogen deliveries? This process is not only labor-intensive but also carries inherent safety risks. An increase in production throughput naturally leads to an increase in this handling activity. If you are planning to scale up your production, the logistical burden and associated costs of hydrogen supply will scale up as well. Upgrading to a recycling system can eliminate the vast majority of this manual handling, freeing up your workforce for more value-added tasks and improving overall plant safety.
Finally, perform a simple calculation: multiply your average monthly hydrogen cost by 24. This two-year figure often represents a substantial portion, if not all, of the investment required for a recycling system. I had a client, a manufacturer of stainless steel wire, who was shocked to realize they had spent nearly half a million dollars on hydrogen over three years. When they saw that number, the decision to invest in a system that would pay for itself in under two years became self-evident. The financial data, when clearly laid out, often makes the most compelling case for an upgrade.
Assessing Product Quality and Rejection Rates
Financial metrics are just one part of the story; your quality control data provides another set of critical indicators. Are you experiencing issues with inconsistent surface brightness, intermittent oxidation, or other defects on your annealed products? Inconsistent quality can often be traced back to instability in the furnace atmosphere. As mentioned earlier, relying on a continuous feed of new hydrogen from cylinders or tanks can introduce subtle variations in purity and pressure, especially during changeovers. These small dips in atmospheric integrity are enough to impact sensitive materials.
If your internal rejection rate or, even worse, your customer return rate due to quality issues is unacceptably high, it's time to investigate your atmosphere control. A hydrogen recycling and purification system provides a far more stable and consistent atmosphere than a total-loss system. By continuously purifying the gas, it removes contaminants that build up over time, ensuring a consistently high-purity environment. This leads directly to more uniform product quality, fewer rejects, and higher customer satisfaction.
A great example comes from a producer of high-end white goods that we work with. They required a flawless, mirror-like finish on stainless steel components. They were plagued by a low but persistent rate of cosmetic defects that led to costly rework. After installing an AKS mesh belt furnace with an integrated recycling system, they tracked a 70% reduction in atmosphere-related defects. The upgrade wasn't just about saving on gas; it was about protecting their brand's reputation for premium quality and reducing the hidden costs associated with scrap and rework.
Evaluating Market and Regulatory Pressures
The final set of indicators comes from outside your factory walls. The market and regulatory landscape is evolving rapidly. Are your key customers starting to ask questions about your environmental footprint or your ESG policies? Large manufacturers and retailers, particularly in Europe and North America, are implementing stringent supplier codes of conduct that include sustainability metrics. Your ability to provide data on reduced energy and resource consumption can become a condition for doing business.
Simultaneously, governments worldwide are introducing carbon taxes, emissions trading schemes, and other environmental regulations. While hydrogen itself may not be the primary target, the energy-intensive process of producing it (especially non-green hydrogen) carries a significant carbon footprint. Reducing your consumption via recycling preemptively positions your company to comply with future regulations and avoid potential carbon penalties. This proactive stance is far more strategic than waiting for regulations to be imposed.
Take a look at your key competitors. Are they already marketing their "green" manufacturing processes? If they are using technology like hydrogen recycling to lower their costs and appeal to environmentally conscious customers, they are building a competitive advantage that can erode your market share. In this context, upgrading is not just an optimization; it's a defensive and strategic necessity. A client in the metal fasteners industry decided to upgrade specifically to win a contract with a major European automotive firm. Their ability to demonstrate a lower carbon footprint per unit was the deciding factor that set them apart from their competitors.
Indicator Type | Signal to Watch For | Why It Matters |
---|---|---|
Financial | High or rising monthly hydrogen costs. | Direct impact on profitability; indicates significant potential savings. |
Operational | Increased production volume and gas cylinder handling. | Logistical burdens and safety risks will grow without an upgrade. |
Quality | Inconsistent surface finish, high rejection/rework rates. | Suggests atmospheric instability that recycling can solve. |
Market | Customers asking for ESG data; competitors marketing "green" processes. | Sustainability is becoming a key competitive differentiator and market access requirement. |
High hydrogen costs signal upgrade needПравда
Consistently high and rising hydrogen expenditures are a primary indicator that investing in recycling technology would be financially beneficial.
Hydrogen purity doesn't affect product qualityЛожь
Variations in hydrogen purity during cylinder changes can directly cause surface defects and inconsistent product quality.
How can businesses calculate the ROI of upgrading to hydrogen recycling in their annealing processes?
Are you ready to move from concept to calculation, but unsure how to build a solid financial case for the upgrade? Calculating the Return on Investment (ROI) for a hydrogen recycling system is a straightforward process. It empowers you to make a data-driven decision by clearly forecasting the financial impact on your business.
To calculate the ROI of upgrading to hydrogen recycling, a business must first quantify the total upfront investment Capital Expenditure (CAPEX), then calculate the total annual operational savings Operational Expenditure (OPEX), and finally use these figures to determine the payback period and long-term value through metrics like Net Present Value (NPV).
This calculation is something I walk through with almost every client, as it transforms an abstract benefit into a concrete business case. The goal is to create a clear, conservative, and defensible financial projection that your entire management team can stand behind. It’s not about using overly optimistic numbers; it’s about using your own historical data to build a realistic forecast. Let's break this down into a simple, step-by-step guide to ensure you capture all the critical variables and build a compelling justification for the investment.
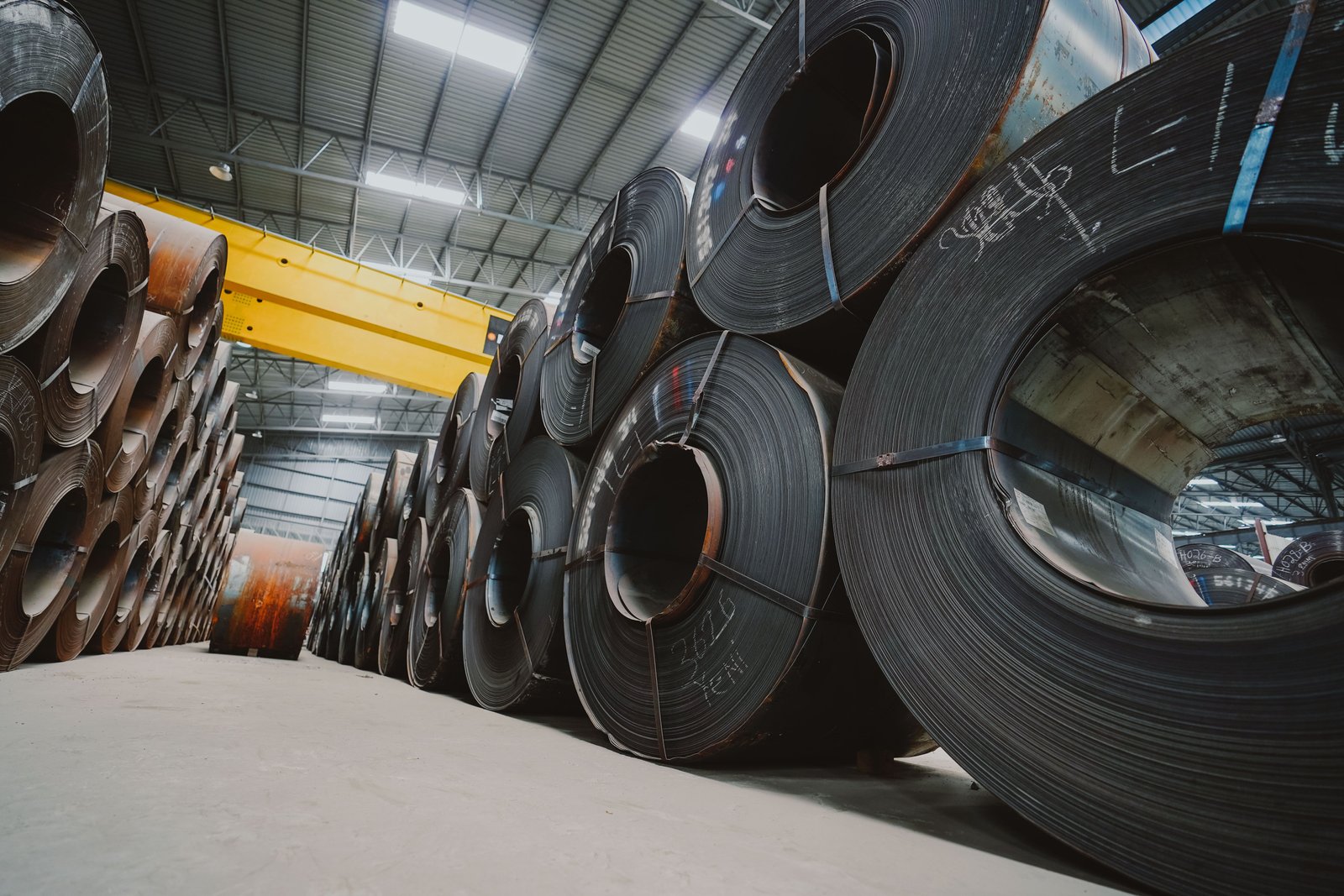
Step 1: Quantifying Your Initial Investment (CAPEX)
The first step in any ROI calculation is to determine the total initial investment, also known as Capital Expenditure (CAPEX). This is more than just the sticker price of the hydrogen recycling unit itself. A thorough calculation must include all associated costs to get the system fully operational. The primary cost is, of course, the recycling equipment. The capacity and sophistication of the unit will depend on the volume of hydrogen your furnace consumes, so it's essential to work with a knowledgeable supplier like AKS to specify the correct size for your needs.
Beyond the hardware, you must account for "soft costs." This includes shipping and logistics to get the equipment to your facility. Installation and integration costs are also critical. Will the system be installed on a new furnace line, or will it be a retrofit to an existing one? Retrofitting may require custom piping, electrical work, and PLC programming to ensure the recycling unit communicates seamlessly with your furnace controls. At AKS, we often recommend integrating recycling systems from the outset in a new furnace design, as this is typically the most efficient and cost-effective approach.
Finally, don't forget to budget for commissioning and training. Proper commissioning by the manufacturer's technicians ensures the system is calibrated for optimal performance and safety from day one. You should also invest in training for your operators and maintenance staff. A well-trained team can operate the system efficiently, perform routine maintenance, and troubleshoot minor issues, maximizing uptime and the lifespan of the equipment. Summing up these costs—equipment, shipping, installation, and training—will give you the total CAPEX figure for your ROI calculation.
Step 2: Calculating Your Annual Operational Savings (OPEX Reduction)
With the total investment quantified, the next step is to calculate the annual savings the system will generate. This is the most compelling part of the business case. The largest and most easily calculated saving is the reduction in hydrogen purchases. Start by gathering your purchasing records for the last 12 months to find your total annual expenditure on hydrogen. Based on a typical efficiency of 90-95% for recycling systems, you can calculate your expected annual savings. For example, an annual hydrogen spend of $150,000 would be reduced to just $7,500-$15,000, yielding a savings of $135,000 to $142,500 per year.
Next, quantify the "softer" operational savings. Estimate the number of labor hours your team spends each week on tasks related to gas supply, such as receiving deliveries, moving cylinders, connecting and disconnecting them, and handling the associated paperwork. Multiply these hours by your average burdened labor rate to find the annual savings in labor cost. While this might seem small on a weekly basis, it can add up to thousands of dollars over a year.
Finally, factor in the savings from improved quality and reduced waste. Analyze your quality control data to determine the cost of scrap and rework associated with annealing defects. If you can realistically expect the new system's atmospheric stability to reduce these defects by a certain percentage (e.g., 50%), you can add that figure to your annual savings. For a client of ours manufacturing precision tubes, this saving from reduced scrap was nearly as significant as their saving on gas, as their material was a high-value alloy. Summing up the savings from gas, labor, and quality gives you the total annual OPEX reduction.
Step 3: Determining the Payback Period and Long-Term Value
Now you have the two key components for your ROI analysis: the total investment (CAPEX) and the annual savings (OPEX reduction). The simplest ROI metric is the Simple Payback Period, calculated as: $$ \text{Payback Period (in years)} = \frac{\text{Total CAPEX}}{\text{Annual OPEX Reduction}} $$ This gives you a quick measure of how long it will take to recoup your initial investment. For many of our clients, this period is often between 1.5 and 2.5 years, a very attractive timeframe for an industrial equipment investment.
For a more financially rigorous analysis, you should also consider the Net Present Value (NPV), as we discussed earlier. While this calculation is more complex, it provides a powerful view of the investment's long-term contribution to your company's value. Using a standard spreadsheet or financial calculator, you can input the initial investment (as a negative cash flow) and the projected annual savings for the expected life of the equipment (e.g., 10-15 years). By applying a discount rate, you can see the total value of the project in today's money, giving your finance team the robust data they need.
The table below shows a sample ROI calculation for a mid-sized manufacturing plant. This kind of clear, transparent breakdown is exactly what you need to build a rock-solid business case. It moves the discussion from "it feels like a good idea" to "the data proves this is a financially sound strategic investment."
Item | Calculation/Value | Amount |
---|---|---|
A. Initial Investment (CAPEX) | ||
Hydrogen Recycling Unit | Equipment Cost | ($180,000) |
Installation & Integration | Labor & Materials | ($15,000) |
Training & Commissioning | Manufacturer Services | ($5,000) |
Total CAPEX | ($200,000) | |
B. Annual Savings (OPEX) | ||
Hydrogen Cost Reduction | $150,000 (Annual Cost) x 90% (Recycling Rate) | $135,000 |
Labor Savings | 5 hours/week x $30/hr x 50 weeks | $7,500 |
Reduced Rejection Costs | 50% reduction on $20,000 annual scrap cost | $10,000 |
Total Annual OPEX Savings | $152,500 | |
C. ROI Metrics | ||
Simple Payback Period | ($200,000 CAPEX) / ($152,500 Savings) | 1.31 Years |
CAPEX includes installation costsПравда
The total initial investment must account for installation and integration costs, not just equipment price.
Payback period exceeds 5 yearsЛожь
Typical payback periods range between 1.5-2.5 years due to significant OPEX savings.
What are the industry recommendations for optimizing annealing processes with hydrogen recycling?
So, you've decided that a hydrogen recycling system is the right move for your operation. How do you ensure you get the maximum benefit from your investment? Simply installing the equipment is not enough. To truly optimize your process, you must adopt a holistic approach that integrates technology, monitoring, and best practices.
Industry recommendations for optimizing annealing with hydrogen recycling focus on three key areas: integrating the system into the furnace design from the start, implementing robust real-time monitoring and control systems, and establishing a comprehensive maintenance and safety protocol to ensure long-term reliability and performance.
Following these recommendations, which have been honed over years of practical application in factories worldwide4, is the difference between simply having a recycling system and running a world-class, optimized annealing operation. It's about creating a process that is not only efficient and cost-effective but also reliable, safe, and capable of producing the highest quality products consistently. As a furnace manufacturer, we see our role as not just supplying equipment, but partnering with our clients to implement these best practices for long-term success.
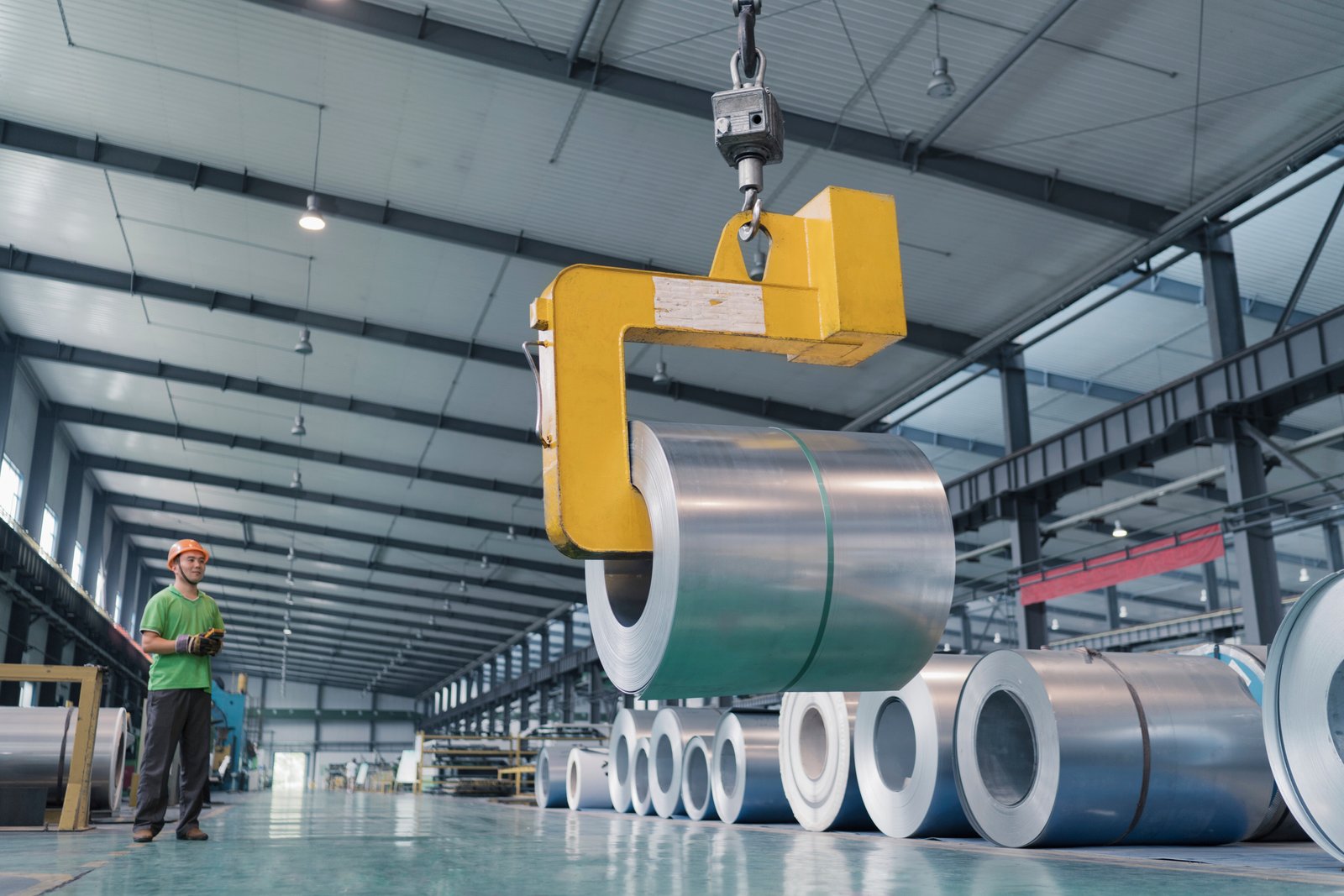
Integrating Recycling into Furnace Design from the Start
The most effective way to optimize a hydrogen recycling system is to plan for it from the very beginning. While retrofitting a recycling unit to an existing furnace is certainly feasible and often provides excellent ROI, designing a new furnace with an integrated system offers distinct advantages. When the furnace and the recycling unit are designed by the same engineering team, they can be perfectly matched to work in harmony. This is a core philosophy behind our furnace designs at AKS. We treat the recycling system not as an accessory, but as an integral part of the furnace's atmospheric control loop.
An integrated design ensures optimal gas flow dynamics. The piping, valves, and flow paths can be engineered for maximum efficiency and minimal pressure drop, reducing the energy consumption of the recycling unit's circulation pumps. The control systems can be unified into a single PLC and HMI interface, providing operators with a seamless and intuitive user experience. This avoids the complexity of trying to make two separate control systems from different manufacturers communicate with each other, which can be a common pain point in retrofit projects.
Furthermore, an integrated approach allows for a more compact physical footprint and streamlined installation. The entire system can often be pre-assembled and tested at the manufacturer's facility before shipping, reducing on-site installation time and potential for errors. I recall a project with a large automotive supplier where we replaced their aging furnace with a new AKS bright annealing line. By designing the hydrogen recycling system as part of the core package, we were able to reduce the overall footprint by 20% compared to their previous setup with a third-party retrofit, freeing up valuable floor space in their crowded facility.
Implementing Robust Monitoring and Control Systems
You cannot optimize what you cannot measure. A state-of-the-art hydrogen recycling system should be equipped with a suite of sensors for real-time monitoring of key process parameters. The most critical of these is an in-line hydrogen purity analyzer. This sensor continuously measures the purity of the gas being returned to the furnace, ensuring it always meets the process specification (e.g., >99.9%). If the purity starts to drop, the system can automatically take corrective action, such as increasing the flow to the purification bed or alerting an operator.
In addition to purity, the system should monitor pressure, temperature, and flow rate throughout the recycling loop. This data provides a complete picture of the system's health and performance. Advanced systems, like those we integrate at AKS, log this data continuously and display it on the central HMI with trend charts. This allows process engineers to analyze performance over time, identify subtle shifts, and optimize parameters for different products or alloys. For example, they might find that a slightly lower flow rate can be used for less sensitive materials without compromising quality, resulting in further energy savings.
This data-rich environment is a cornerstone of Industry 4.0 and smart manufacturing5. By connecting the furnace's control system to a plant-wide SCADA or MES system, this performance data can be correlated with production schedules and quality control results. This enables a higher level of process optimization and predictive maintenance. For instance, the system might be able to predict when the catalyst in the purification unit needs to be replaced based on a gradual decline in efficiency, allowing maintenance to be scheduled proactively before it impacts production.
Establishing a Comprehensive Maintenance and Safety Protocol
Like any critical piece of industrial equipment, a hydrogen recycling system requires a robust maintenance and safety protocol to ensure its long-term reliability and performance. While modern systems are designed for high uptime and low maintenance, they are not "fit and forget" devices. Establishing a clear schedule for routine checks and preventative maintenance is essential. This includes tasks like inspecting for leaks, checking the performance of pumps and valves, and calibrating sensors.
The most critical maintenance item in a hydrogen recycling system is the purification media or catalyst. This material has a finite lifespan and its ability to remove contaminants like oxygen and moisture degrades over time. The manufacturer will provide clear guidelines on the expected lifespan and replacement procedure. Following this schedule is non-negotiable for maintaining gas purity and protecting the quality of your products. Trying to extend the life of the catalyst beyond its recommended limit is a false economy that will inevitably lead to quality problems.
Safety is, of course, paramount when dealing with hydrogen. Your protocol must include regular checks of all safety interlocks and leak detection systems. Operators and maintenance staff must be thoroughly trained on both the normal operating procedures and the emergency shutdown protocols. At AKS, our commissioning process always includes comprehensive on-site safety training. We work with the client's team to ensure they understand the system's safety features, the properties of hydrogen, and the correct procedures for any eventuality. A well-maintained system operated by a well-trained team is a safe and highly efficient asset for any manufacturing plant.
Integrated design improves efficiencyПравда
Designing the furnace and recycling system together optimizes gas flow and reduces energy consumption.
Retrofitting is always betterЛожь
While retrofitting is feasible, integrated designs from the start offer superior performance and efficiency.
Заключение
Ultimately, the decision to upgrade your annealing process with hydrogen recycling is a strategic one. It's a move that transcends simple cost-cutting, offering a powerful combination of financial returns, superior product quality, operational resilience, and a verifiable commitment to sustainable manufacturing for your business's future.
-
Learn the financial benefits and method to evaluate investment profits over time ↩
-
Discover potential savings and economic impacts of hydrogen recycling in industry ↩
-
Gain insights into cost and efficiency improvements through recycling systems ↩
-
See case studies and examples of global applications of hydrogen recycling. ↩
-
Understand how data integration enhances manufacturing processes. ↩