Какие этапы включает в себя отжиг нержавеющей стали?
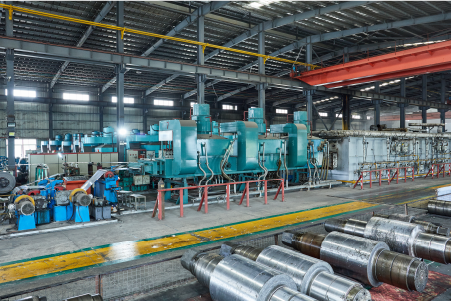
Пытаетесь добиться идеальной зеркальной поверхности изделий из нержавеющей стали, не прибегая к дорогостоящей и трудоемкой вторичной полировке? Разочарование, связанное с окислением и дефектами поверхности после термообработки, может привести к значительным отходам материала и бракованным партиям, что негативно скажется на вашей прибыли. Решение заключается в освоении яркий отжиг1точная термическая обработка, которая защищает и улучшает первозданную поверхность стали с самого начала.
Отжиг - это специализированная термическая обработка, которая заключается в нагреве нержавеющей стали в печи с контролируемой атмосферой для снятия внутренних напряжений и улучшения металлургических свойств, не вызывая окисления поверхности. Основные этапы включают тщательную подготовку поверхности, точный контроль температуры и атмосферы в течение циклов нагрева и охлаждения, а также тщательную обработку после обработки для получения яркой, чистой и устойчивой к коррозии поверхности.
Работая в компании AKS Furnace, я на собственном опыте убедился, как хорошо выполненный процесс отжига может изменить производительность и эффективность производителя. Это не просто нагрев металла; это наука, сочетающая металлургию с передовыми инженерными разработками. При правильном подходе можно отказаться от целых этапов последующей обработки, таких как химическое травление, что позволяет не только сэкономить деньги, но и снизить воздействие на окружающую среду. Давайте пройдемся по важнейшим этапам, которые гарантируют безупречный яркий отжиг каждый раз.
Понимание этих этапов крайне важно для любого обработчика металла, стремящегося к превосходному качеству. Каждый этап, от начальной очистки до финальной стадии охлаждения, играет важную роль в конечном результате. Мы рассмотрим, как точный контроль над такими переменными, как температура и атмосфера, является не просто рекомендацией, а необходимостью для достижения успеха на современном конкурентном рынке, где стандарты качества высоки как никогда.
Что такое отжиг и почему он используется при обработке нержавеющей стали?
Ваши детали из нержавеющей стали после отжига тускнеют, покрываются окалиной и окисляются? Эта распространенная проблема вынуждает вас прибегать к дополнительным дорогостоящим операциям, таким как кислотное травление и полировка, только для того, чтобы восстановить отделку. Решением проблемы является отжиг в светлых тонах - процесс, в котором используется защитная атмосфера для предотвращения окисления, что позволяет сохранить присущий стали блеск и сэкономить значительное время и деньги на последующей обработке.
Отжиг - это высокотемпературная термическая обработка, проводимая в контролируемой атмосфере, обычно состоящей из водорода и азота. Он используется для смягчения нержавеющей стали, снятия внутренних напряжений, возникающих при холодной обработке, и уточнения ее зернистой структуры без окисления поверхности, в результате чего получается чистая, зеркальная поверхность.
Переход от обычного отжига к яркому отжигу представляет собой значительный скачок в эффективности производства и качестве продукции. Предотвращая образование оксидного слоя, вы избавляетесь от необходимости использовать жесткие химические процессы очистки. Это не только экономия средств, но и значительный экологический эффект, поскольку сокращается использование и утилизация опасных кислот. Кроме того, полученная поверхность не только блестит, но и более устойчива к коррозии, поскольку защитный слой оксида хрома остается нетронутым и неповрежденным. За годы работы в компании AKS я помог бесчисленному количеству клиентов осуществить этот переход. Запомнился случай с производителем элитной кухонной утвари в Юго-Восточной Азии. После традиционного отжига и последующей полировки они теряли около 15% своей продукции из-за дефектов поверхности. Ручной процесс полировки также требовал больших трудозатрат. Интегрировав одну из наших печей непрерывного отжига, они не только устранили процент брака, но и перераспределили команду полировщиков на выполнение более важных задач, что значительно улучшило их рабочий процесс и конкурентоспособность на рынке. Ключевой вывод, который они сделали, заключается в том, что отжиг - это не просто термическая обработка; это стратегическое усовершенствование процесса, которое приносит дивиденды на всей производственной линии.
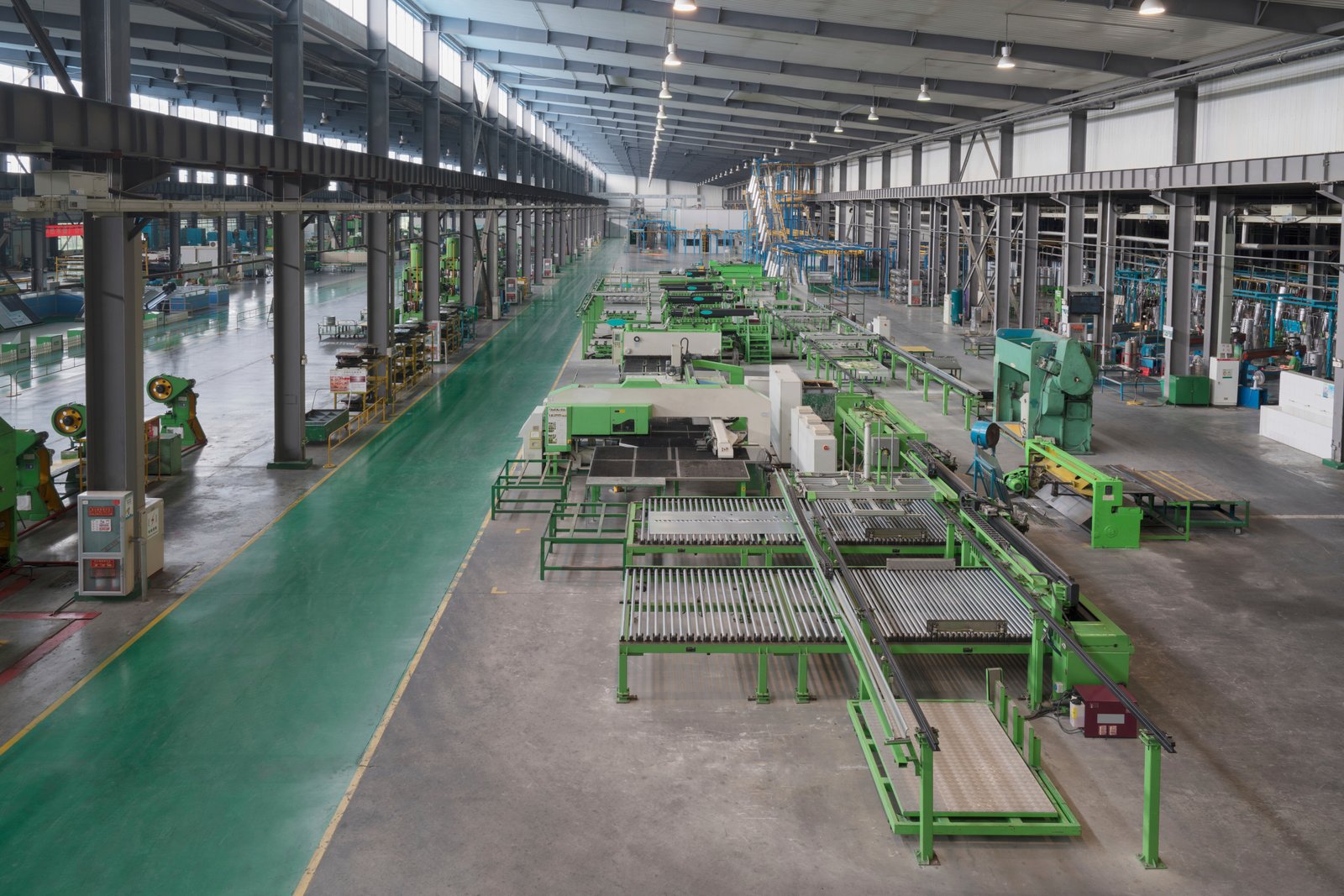
Решение о применении блестящего отжига часто обусловлено необходимостью обеспечить как эстетическое превосходство, так и металлургическую целостность. Для таких отраслей, как автомобилестроение, электроника и медицинское оборудование, где компоненты не только видны, но и должны работать под нагрузкой, чистота и структурная целостность материала не является обязательным условием. Светлый отжиг обеспечивает обе эти цели. Он обеспечивает восстановление механических свойств, таких как пластичность и формуемость, после холодной прокатки или волочения, в то время как поверхность остается чистой и готовой к следующему этапу производства без промежуточной очистки. Такая интеграция улучшения свойств и финишной обработки поверхности в один эффективный этап является основным ценностным предложением технологии. Она упрощает цепочку поставок, сокращает время выполнения заказа и в конечном итоге позволяет получить более надежный и визуально привлекательный конечный продукт.
Металлургическое назначение отжига
Основная причина отжига любого металла, включая нержавеющую сталь, заключается в том, чтобы обратить вспять последствия закалки. Такие процессы, как прокатка, волочение или штамповка, делают сталь более твердой и хрупкой, удлиняя ее кристаллическую структуру. Отжиг нагревает металл до температуры рекристаллизации, позволяя образоваться новым зернам без напряжения. Этот процесс, известный как рекристаллизация, восстанавливает пластичность и мягкость металла, делая его пригодным для дальнейшей формовки или для конечного применения, где он должен быть прочным, но не хрупким.
По моему опыту, многие производители, особенно в отрасли производства труб и полос из нержавеющей стали, полагаются на этот процесс, чтобы добиться точных механических характеристик, требуемых их клиентами. Например, клиенту, производящему гидравлические трубы, необходимо, чтобы материал был достаточно мягким, чтобы его можно было сгибать и развальцовывать без образования трещин, но при этом достаточно прочным, чтобы выдерживать высокое давление. Яркий отжиг позволяет достичь этого тонкого баланса путем тщательного контроля цикла термообработки. Аспект "яркости" гарантирует, что это будет сделано без ущерба для поверхности материала, что очень важно для применений, где чистота и коррозионная стойкость имеют первостепенное значение.
Этот процесс улучшает структуру зерна, что напрямую влияет на физические свойства материала. Более мелкая и равномерная зерновая структура, достигаемая путем оптимизированного отжига, обычно приводит к повышению прочности и усталостной прочности. Наши печи в AKS оснащены многозонными системами нагрева и охлаждения специально для того, чтобы операторы могли точно контролировать процесс измельчения зерна, обеспечивая стабильные результаты от партии к партии. Именно такой уровень контроля отличает высококачественную нержавеющую сталь от стандартных сортов.
"Яркое" преимущество: Предотвращение окисления
При повышенных температурах хром, содержащийся в нержавеющей стали, легко вступает в реакцию с любым доступный кислород2 образуется тусклый, сероватый слой оксида хрома. В то время как тонкий, пассивный слой оксида хрома придает нержавеющей стали коррозионную стойкость при комнатной температуре, толстый, неконтролируемый оксидный налет, образующийся при обычном отжиге, нежелателен. Он разрушает поверхность и должен быть удален. Светлый отжиг решает эту проблему, заменяя воздух в печи защитной атмосферой. Эта атмосфера обычно представляет собой смесь водорода и азота, созданную из диссоциированного аммиака, или, в некоторых случаях, чистый водород для наиболее требовательных применений.
Этот защитный газ создает восстановительную среду. Вместо того чтобы кислород вступал в реакцию со сталью, водород активно уничтожает все присутствующие в печи молекулы кислорода, образуя водяной пар, который
Какие этапы включает в себя отжиг нержавеющей стали?
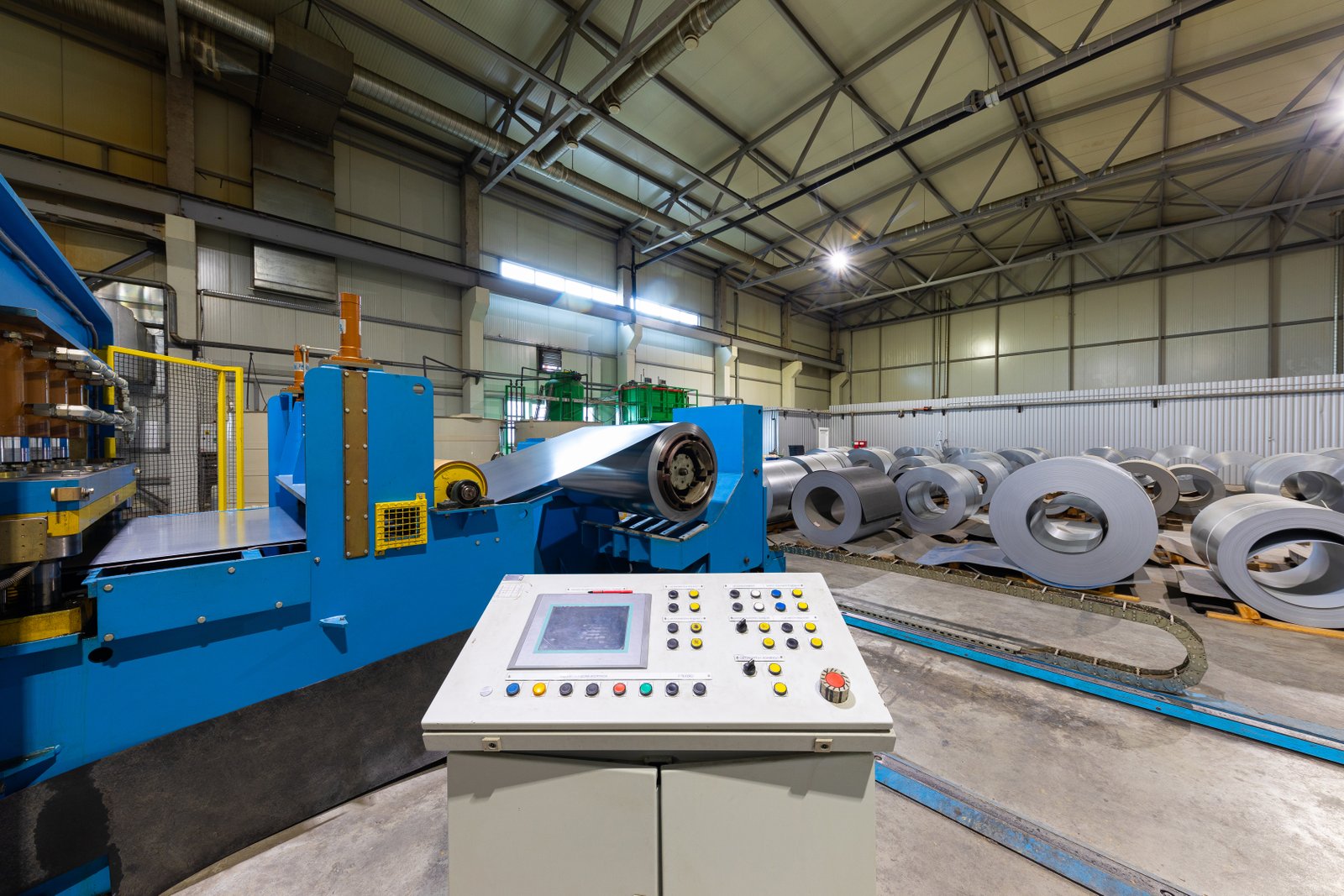
Вы пытаетесь добиться идеального зеркального блеска изделий из нержавеющей стали? Непоследовательный отжиг приводит к обесцвечиванию, образованию окалины и дорогостоящей доработке, что подрывает ценность вашего материала. Освоение этапов отжига - это ключ к достижению неизменно безупречных результатов.
Основные этапы отжига нержавеющей стали включают тщательную подготовку и очистку поверхности, а затем нагрев до определенной температуры отжига в контролируемой бескислородной атмосфере. Сталь выдерживается при этой температуре (выдержка), а затем охлаждается с контролируемой скоростью перед отделкой и проверкой.
Этот процесс может показаться простым рецептом нагрева, но это тонкий танец металлургии, термодинамики и передового управления процессом. Правильное выполнение этого процесса отделяет продукцию стандартного качества от продукции премиум-класса, которая на конкурентных рынках стоит дороже. Как человек, потративший годы на разработку и внедрение таких систем, я на собственном опыте убедился, что освоение каждого этапа может преобразить производственную линию.
Если копнуть глубже, то путь к идеальному блестящему покрытию - это не просто последовательность операций, это целостный подход к качеству. Он требует критического понимания того, как взаимодействует каждый параметр - от чистоты сырья до точки росы в атмосфере печи. Например, профиль отжига для аустенитной нержавеющей стали 304, используемой для изготовления кухонной посуды, значительно отличается от профиля отжига для ферритной стали 430, используемой для отделки автомобилей. Именно поэтому универсальный подход часто оказывается несостоятельным. В компании AKS мы не просто продаем печи; мы сотрудничаем с клиентами для разработки процесса, учитывающего особенности их сплава, требования к конечному продукту и производственные цели, гарантируя, что конечный продукт будет не просто ярким, а металлургически обоснованным и неизменно превосходным.
Яркий отжиг предотвращает окислениеПравда
Контролируемая атмосфера в печах для отжига яркой стали не позволяет кислороду вступать в реакцию с поверхностью стали, сохраняя содержание хрома и коррозионную стойкость.
Яркий отжиг требует травленияЛожь
Ключевым преимуществом отжига в светлых тонах является отсутствие необходимости в последующих процессах травления, поскольку поверхность остается свободной от оксидов на протяжении всего термического цикла.
Что необходимо подготовить перед началом процесса яркого отжига?
Вы готовы к нагреву нержавеющей стали, надеясь на идеальный результат? Поспешное обращение с печью может стать дорогостоящей ошибкой. Любые остатки масел, грязи или смазки на поверхности стали сгорят во время нагрева, что приведет к образованию стойких пятен, нагара и неприятных дефектов.
Перед отжигом поверхность нержавеющей стали должна быть тщательно очищена и обезжирена для удаления всех загрязнений, таких как масла, волочильные составы, пыль и металлические частицы. Такая подготовка гарантирует, что никакие посторонние остатки не вступят в реакцию с атмосферой печи, что в противном случае может привести к дефектам поверхности.
Переходный абзац: Я часто говорю своим клиентам, что этап очистки и подготовки - это самый упускаемый из виду, но в то же время самый важный этап во всем процессе яркого отжига. Он работает по простому принципу "мусор внутрь, мусор наружу". Печь, какой бы совершенной она ни была, не может решить проблему, которая в нее попала. Цель состоит в том, чтобы предоставить хирургически чистую поверхность контролируемой атмосфере, позволяя ей выполнять свою работу по защите стали. Любой компромисс здесь неизбежно отразится на конечном продукте. Однажды я посетил завод одного из клиентов в Индия3 В компанию поступило сообщение о постоянном появлении черных пятен на отожженных трубах из нержавеющей стали. Первоначально они предположили, что причина кроется в атмосфере печи. Однако после тщательного аудита процесса мы установили, что проблема связана с неэффективной системой обезжиривания, которая не справлялась с удалением богатой серой вытяжной смазки. Помогая им модернизировать систему предварительной очистки, мы полностью устранили дефект. Этот опыт укрепил мою веру в то, что подготовка - это не просто предварительная работа; это основополагающий первый шаг к качеству, и наша роль как поставщика печей часто распространяется на помощь клиентам в совершенствовании всей их технологической цепочки.
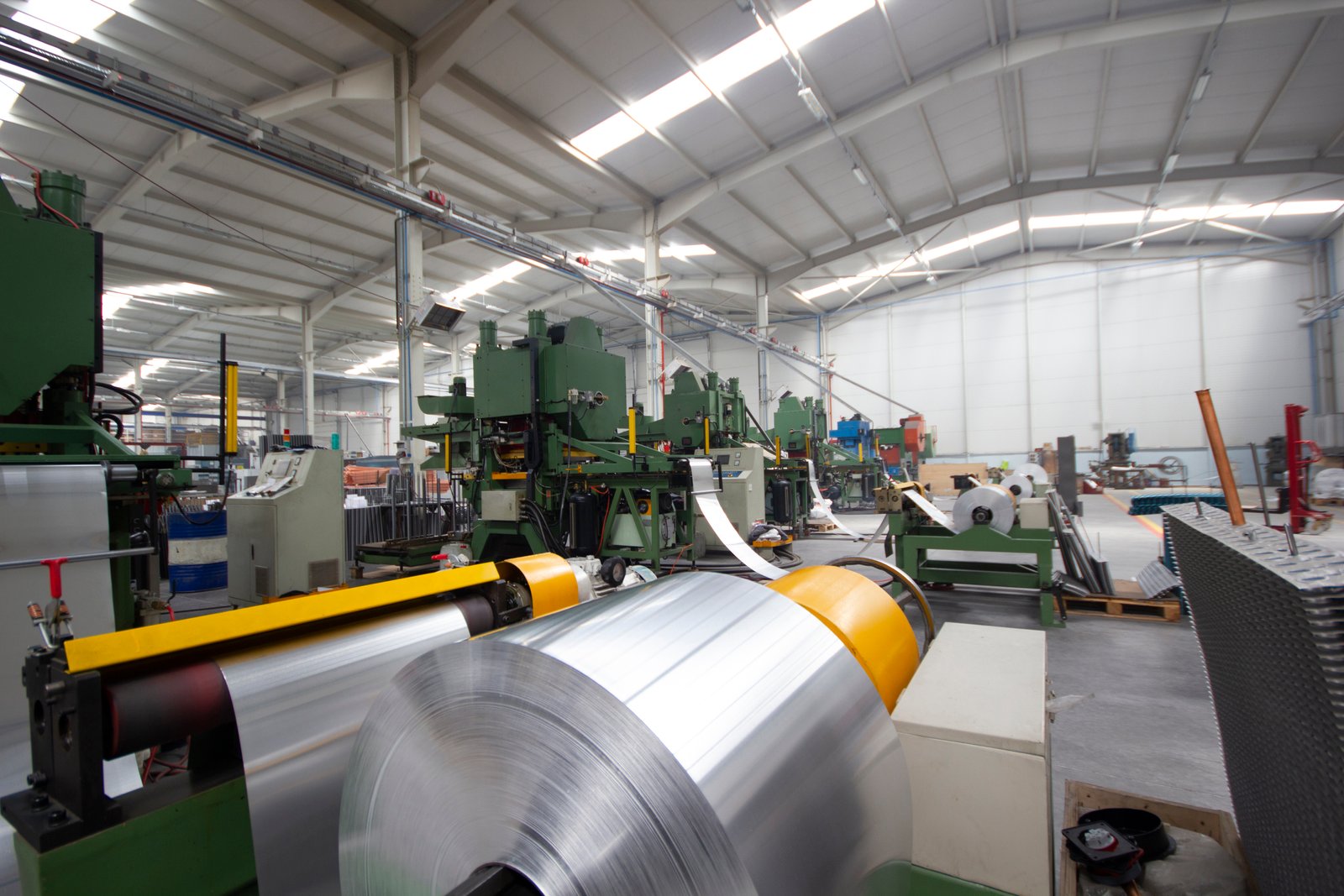
Обеспечение идеальной подготовки нержавеющей стали к яркому отжигу включает в себя многогранный подход, направленный на обеспечение химической чистоты, механической целостности и последовательной обработки. Этот этап - не просто промывка стали; это систематический процесс, направленный на устранение любых факторов, которые могут повлиять на конечный результат. Неудачу на этой ранней стадии невозможно исправить на более поздних этапах процесса, что делает ее критически важной точкой контроля для любого высококачественного производства. Вникая в химия очистки4Механика обработки и реальное воздействие этих подготовительных работ позволяют понять, что безупречная отделка рождается задолго до того, как сталь почувствует жар печи.
Химия чистой поверхности
Поверхность рулона нержавеющей стали или детали, поступающей на отжиг, никогда не бывает по-настоящему чистой. Она покрыта различными остатками предыдущих этапов производства. К ним относятся смазочные материалы для прокатки на основе минеральных масел, водорастворимые составы для волочения, металлическая мелочь, образующаяся при резке или формовке, а также общая пыль и мусор из окружающей среды завода. Каждый из этих загрязнителей представляет собой особую угрозу внутри печи. Масла и смазки, представляющие собой сложные углеводороды, "трескаются" при высоких температурах, откладывая слой углеродной сажи на стальной поверхности, что приводит к образованию черных или серых пятен.
Для борьбы с этим необходим надежный процесс химической очистки. Наиболее распространенным методом для непрерывных полосовых линий является многоступенчатая щелочная система обезжиривания. Полоса проходит через горячий щелочной раствор, который омыляет масла (превращает их в мыло) и эмульгирует грязь, удаляя ее с поверхности. За этим часто следует механическая чистка поверхности щеткой, серия промывок горячей водой, чтобы удалить все следы чистящего раствора, и, наконец, высокоскоростная сушка воздухом. Эффективность этой системы зависит от концентрации химикатов, температуры раствора и времени, которое полоса проводит на каждом этапе.
Для серийных процессов или сложных деталей используются другие методы, например обезжиривание растворителями или ультразвуковая очистка. Ультразвуковые системы используют высокочастотные звуковые волны для создания микроскопических кавитационных пузырьков в чистящем растворе. Раздувание этих пузырьков создает мощное скребущее действие, способное удалить даже самые стойкие загрязнения из сложных геометрических форм. Выбор чистящего средства и метода должен соответствовать конкретному типу удаляемой смазки и загрязнений, чтобы обеспечить химически чистую поверхность, готовую к отжигу.
Механическая обработка и целостность поверхности
Помимо химической чистоты, не менее важна и физическая подготовка. Цель отжига - сохранить и улучшить поверхность, а это значит, что любые царапины, вмятины или выбоины, имеющиеся на материале до попадания его в печь, останутся и после - и зачастую они будут еще более заметны на высокоотражающей поверхности. Поэтому весь процесс обработки материала до печи должен быть рассчитан на бережную эксплуатацию.
На непрерывной линии это начинается с разматывателя и входной секции. Ролики и направляющие должны быть гладкими, чистыми и изготовленными из неабразивных материалов, чтобы не поцарапать полосу при ее подаче в линию. Контроль натяжения в этой секции очень важен; неправильное натяжение может привести к проскальзыванию и царапинам или даже к растяжению и деформации материала. Часто используется входной накопитель или петлеобразователь, позволяющий менять рулоны без остановки печной секции, обеспечивая непрерывный и плавный поток материала.
Для клиента, производящего элитные декоративные панели, мы разработали систему входа с полированными, хромированными роликами и сложной системой контроля натяжения, использующей бесконтактные лазерные датчики для измерения формы полосы. Эти инвестиции в безупречную механическую обработку были так же важны, как и сама печь, для достижения поверхности "класса А", которую требовал рынок. Любая ошибка оператора или недостаток оборудования, которые приводят к физическим дефектам на этом этапе, являются неисправимыми ошибками.
Пример из практики: Отслеживание дефектов до их источника
Чтобы проиллюстрировать критический характер подготовки, давайте вернемся к примеру индийского завода по производству труб из нержавеющей стали, о котором я упоминал ранее. Они производили трубы для медицинской и гидравлической промышленности, где чистота поверхности имеет первостепенное значение. Несмотря на наличие новой печи для отжига в светлых тонах, они страдали от брака, который составлял около 15%, из-за черных полос и пятен на их продукции. Это приводило к значительным финансовым потерям и ставило под угрозу контракт с ключевым клиентом. Наша команда технического обслуживания была вызвана для проведения расследования.
Первым делом мы провели комплексный аудит технологического процесса, начиная с самого начала: трубоформовочного стана. Мы взяли образцы смазки для волочения, используемой при формовке труб, и образцы "черной сажи", соскобленной с бракованных отожженных труб. Лабораторный анализ подтвердил наши подозрения: сажа имела химический состав, особенно с высоким содержанием серы и углерода, который соответствовал смазочному материалу. Одноступенчатый бак для обезжиривания был просто недостаточно мощным, чтобы полностью удалить это вязкое соединение до того, как трубки попадут в печь.
Совместно с командой мы рекомендовали и помогли им внедрить трехступенчатую систему ультразвуковой очистки. На первом этапе использовался агрессивный щелочной раствор для разрушения основной массы смазки, на втором - первичное ополаскивание, а на третьем - окончательное ополаскивание деионизированной водой, чтобы после сушки не оставалось минеральных пятен. Результаты были получены незамедлительно и впечатляюще. В течение первой недели после ввода в эксплуатацию новой линии очистки процент брака по поверхностным дефектам снизился со 15% до менее чем 1%. Этот случай служит убедительным напоминанием о том, что печь - это только одна часть уравнения качества; тщательная и проверенная подготовка - вот истинная основа успешного отжига.
Очистка поверхности предотвращает дефекты печиПравда
Тщательная очистка удаляет загрязнения, которые в противном случае могли бы привести к образованию стойких пятен и углеродистых отложений при отжиге.
Механическая обработка не влияет на качество поверхностиЛожь
Царапины и вмятины от неправильного обращения остаются заметными после отжига, поэтому механическая подготовка не менее важна, чем химическая очистка.
Как контроль температуры влияет на отжиг нержавеющей стали?
Ваш процесс отжига - это игра в угадайку с настройками температуры? Слишком низкая температура приводит к неполному отжигу и хрупкости материала, а слишком высокая может разрушить зернистую структуру или даже повредить сталь. Отсутствие контроля приводит к нестабильному качеству и высокому проценту брака.
Точный контроль температуры имеет первостепенное значение. Сталь должна быть равномерно нагрета до заданной температуры отжига (например, 1040-1150°C для аустенитных марок, выдержана в течение определенного времени (выдержка) для полной рекристаллизации, а затем охлаждена с контролируемой скоростью для обеспечения конечных металлургических свойств.
По моему опыту, температура - это самый мощный рычаг, которым мы располагаем при термообработке. Она диктует окончательную микроструктуру, а значит, и механические свойства нержавеющей стали. Достичь нужной температуры не так просто, как установить циферблат. Настоящей проблемой, особенно на непрерывной линии, является обеспечение того, чтобы каждый квадратный миллиметр стальной полосы - края и центр - достигал одинаковой температуры в одно и то же время и следовал идентичному термическому профилю. Эта однородность - разница между рулоном с неизменными свойствами из конца в конец и рулоном с твердыми и мягкими участками и непредсказуемыми характеристиками. Именно здесь передовая конструкция печи приобретает решающее значение. В наших печах AKS, например, используется многозонная система управления, в которой разные секции печи могут быть настроены на разные температуры. Это позволяет нам создать точный профиль наращивания, выдержки и охлаждения, соответствующий конкретной марке и толщине обрабатываемой стали. Мы используем массив термопар для мониторинга температуры полосы в режиме реального времени, а ПИД-контур управления осуществляет постоянную, ежеминутную регулировку нагревательных элементов или горелок для поддержания тепловой однородности в пределах ±3°C. Такой уровень точности - не роскошь, а необходимость для производства высококачественной и надежной нержавеющей стали.
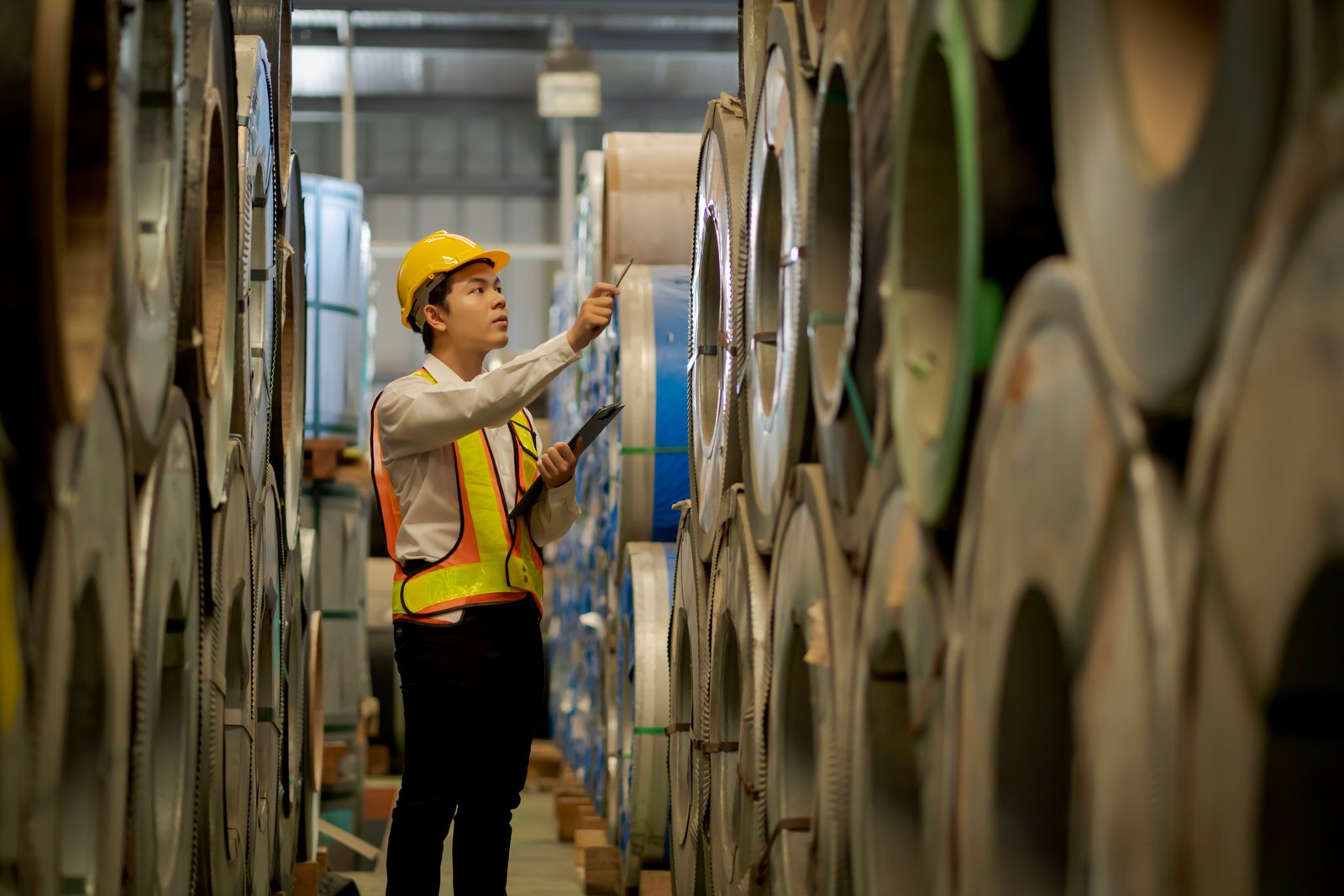
Влияние температурного контроля на отжиг блестящей стали очень велико и определяет успех процесса с точки зрения металлургии, качества и эффективности. Печь в конечном итоге является инструментом для точной подачи тепловой энергии, и ее способность управлять этой энергией определяет ее производительность. Оптимальный термический цикл - это тщательно выверенная последовательность нагревания, выдержки и охлаждения, каждая из которых имеет свою цель. Понимание нюансов этого термического профилирования, технологии, необходимой для его достижения, и необходимости адаптировать его для различных материалов является ключом к овладению искусством и наукой яркого отжига. Без этого понимания производители остаются с непоследовательными результатами, напрасно потраченной энергией и ухудшенным качеством материала.
Три фазы термопрофилирования
Процесс прохождения стали через печь отжига можно разделить на три отдельные термические фазы: наращивание, выдержка и охлаждение. Каждая фаза играет важную роль. Первая - это наращивание или фаза нагрева, когда температура стали повышается от окружающей среды до целевой температуры отжига. Цель состоит в том, чтобы нагреть материал как можно быстрее для обеспечения эффективности, но без превышения заданной температуры или создания теплового напряжения. Нагрев должен быть абсолютно равномерным по всей ширине материала, чтобы предотвратить деформацию, например коробление или изгиб полосы.
Далее замачивание фаза. После достижения заданной температуры сталь выдерживается в течение определенного времени. Это не простое время: именно на этом этапе происходит металлургическая магия рекристаллизации. Новым, свободным от деформации зернам нужно время, чтобы зародиться и вырасти, полностью заменив старую, деформированную структуру зерен. Сочетание температуры и времени выдержки определяет конечный размер зерна, который, в свою очередь, влияет на пластичность материала и внешний вид поверхности. Слишком короткая выдержка приводит к неполному преобразованию. Слишком длительная выдержка или слишком высокая температура приводят к чрезмерному росту зерна, что может привести к грубой текстуре поверхности "апельсиновой корки" после формования.
Заключительный этап охлаждениеДля аустенитных нержавеющих сталей это, пожалуй, самая важная часть. Сталь должна быть быстро охлаждена в определенном температурном диапазоне (примерно 850°C до 450°C или 1550°F до 840°F)5. В этом диапазоне "сенсибилизации" карбиды хрома могут осаждаться на границах зерен, если охлаждение происходит слишком медленно. Это приводит к истощению хрома в окружающем пространстве, что значительно ухудшает "нержавеющие" антикоррозийные свойства стали. Поэтому охлаждающая секция печи должна быть спроектирована для эффективного и быстрого отвода тепла при сохранении защитной атмосферы.
Технология печи для равномерного нагрева
Для достижения точного теплового профиля, описанного выше, требуется сложная технология изготовления печей. Метод нагрева является основным выбором при проектировании. Печи могут нагреваться электричеством с помощью высокоэффективных элементов сопротивления или газом с помощью излучающих труб. В наших печах AKS мы часто используем электрический нагрев благодаря его чистоте работы и исключительно тонкому контролю. Мы располагаем нагревательные элементы в нескольких независимо управляемых зонах по всей длине печи. В печи может быть от 6 до 12 и более зон, каждая со своей термопарой и специальным регулятором мощности.
Такая многозональная конфигурация обеспечивает точное профилирование. Мы можем запрограммировать первые зоны для быстрого наращивания, средние зоны для поддержания стабильной температуры выдержки с непревзойденной точностью, а последние зоны для начала перехода к охлаждению. Чтобы обеспечить равномерность по всей ширине полосы, элементы стратегически расположены как над, так и под полосой. Для газовых конструкций мы используем высокоскоростные горелки, которые способствуют интенсивной циркуляции внутренней атмосферы, устраняя горячие и холодные зоны.
Мозгом системы является программируемый логический контроллер (ПЛК), работающий по алгоритму пропорционально-интегрально-деривативного (ПИД) управления. Эта система постоянно сравнивает фактические показания температуры с термопар с желаемой уставкой и производит непрерывную, прогнозируемую корректировку выходной мощности. Этот замкнутый цикл управления позволяет нашим системам поддерживать стабильность температуры на уровне ±3°C или выше, что очень важно для получения стабильных металлургических свойств, необходимых в таких требовательных областях, как автомобилестроение и аэрокосмическая промышленность.
Адаптация к различным сплавам и калибрам
Ключевой проблемой любого производства является гибкость процесса. Обработчику стали может потребоваться отжечь тонкий (например, 0,2 мм) рулон нержавеющей стали 304 утром и более толстый (например, 2,0 мм) рулон нержавеющей стали 430 во второй половине дня. Эти два продукта имеют совершенно разные тепловые требования. Более тонкий материал нагревается и остывает гораздо быстрее, что требует более высокой скорости линии для предотвращения перегрева. Более толстый материал требует больше энергии и более медленной скорости линии, чтобы его сердцевина достигла полной температуры отжига.
Кроме того, целевая температура отжига для разных сплавов существенно различается. Аустенитные марки, такие как 304 и 3166 требуют высокой температуры отжига (около 1050°C) с последующим быстрым охлаждением. Ферритные марки, такие как 430, отжигаются при более низкой температуре (около 850°C) и имеют другие требования к охлаждению. Современная печь для отжига должна быть способна легко адаптироваться к такому сочетанию продуктов.
Именно здесь неоценимую помощь оказывает система управления рецептами, интегрированная в ПЛК печи. Как поставщик, мы работаем с нашими клиентами над разработкой и хранением десятков запрограммированных рецептов. Оператор может просто выбрать рецепт "0,5 мм 316L" на экране HMI, и печь автоматически настроит температурные уставки для всех зон, скорость линии и контроль атмосферы. Такая автоматизация не только упрощает работу и снижает вероятность человеческой ошибки, но и гарантирует, что каждый рулон будет обработан в точных, оптимальных условиях, необходимых для удовлетворения его спецификации, гарантируя повторяемость процесса и неизменное качество разнообразной продукции.
Равномерность температуры имеет решающее значениеПравда
Равномерная температура по всей полосе стали обеспечивает стабильные металлургические свойства и предотвращает появление таких дефектов, как твердые/мягкие пятна.
Все сорта требуют одинаковой температурыЛожь
Различные марки нержавеющей стали (например, аустенитная и ферритная) требуют значительно отличающихся температур отжига (1050°C против 850°C).
Почему атмосфера имеет решающее значение в процессе яркого отжига?
У вас чистая поверхность и идеальный температурный контроль, но сталь все равно получается тусклой и покрытой окалиной. Что же пошло не так? Если подвергнуть горячую нержавеющую сталь воздействию даже незначительного количества кислорода, поверхность мгновенно потускнеет, что полностью перечеркнет цель процесса.
Атмосфера печи имеет решающее значение, поскольку она действует как защитный экран, не позволяя горячей поверхности нержавеющей стали вступать в реакцию с кислородом. Чистая, сухая и восстановительная атмосфера, обычно состоящая из водорода или смеси азота и водорода, гарантирует отсутствие образования оксидного слоя, сохраняя присущую материалу блестящую поверхность.
Мне нравится описывать защитную атмосферу как "невидимого героя" яркого отжига. Вы ее не видите, но ее роль абсолютно неоспорима. Достижение желанного зеркального блеска полностью зависит от поддержания внутри печи не только бескислородной, но и активно восстанавливающей среды. Восстановительная атмосфера не только предотвращает образование новых окислов, но и очищает все слабые, остаточные поверхностные окислы, которые могли присутствовать на стали в момент ее поступления. Именно поэтому выбор газа, его чистота и содержание влаги (точка росы7) являются такими критическими параметрами процесса. Кроме того, механическая целостность самой печи - ее способность быть газонепроницаемой - имеет первостепенное значение. Любая утечка, какой бы маленькой она ни была, может позволить воздуху проникнуть внутрь, загрязнить атмосферу и испортить продукт. Именно поэтому в компании AKS мы прилагаем огромные инженерные усилия к разработке муфелей и систем уплотнения наших печей, обеспечивая создание идеально контролируемой среды, в которой нержавеющая сталь может преобразовываться в идеальных условиях, защищенных от разрушительного воздействия кислорода.
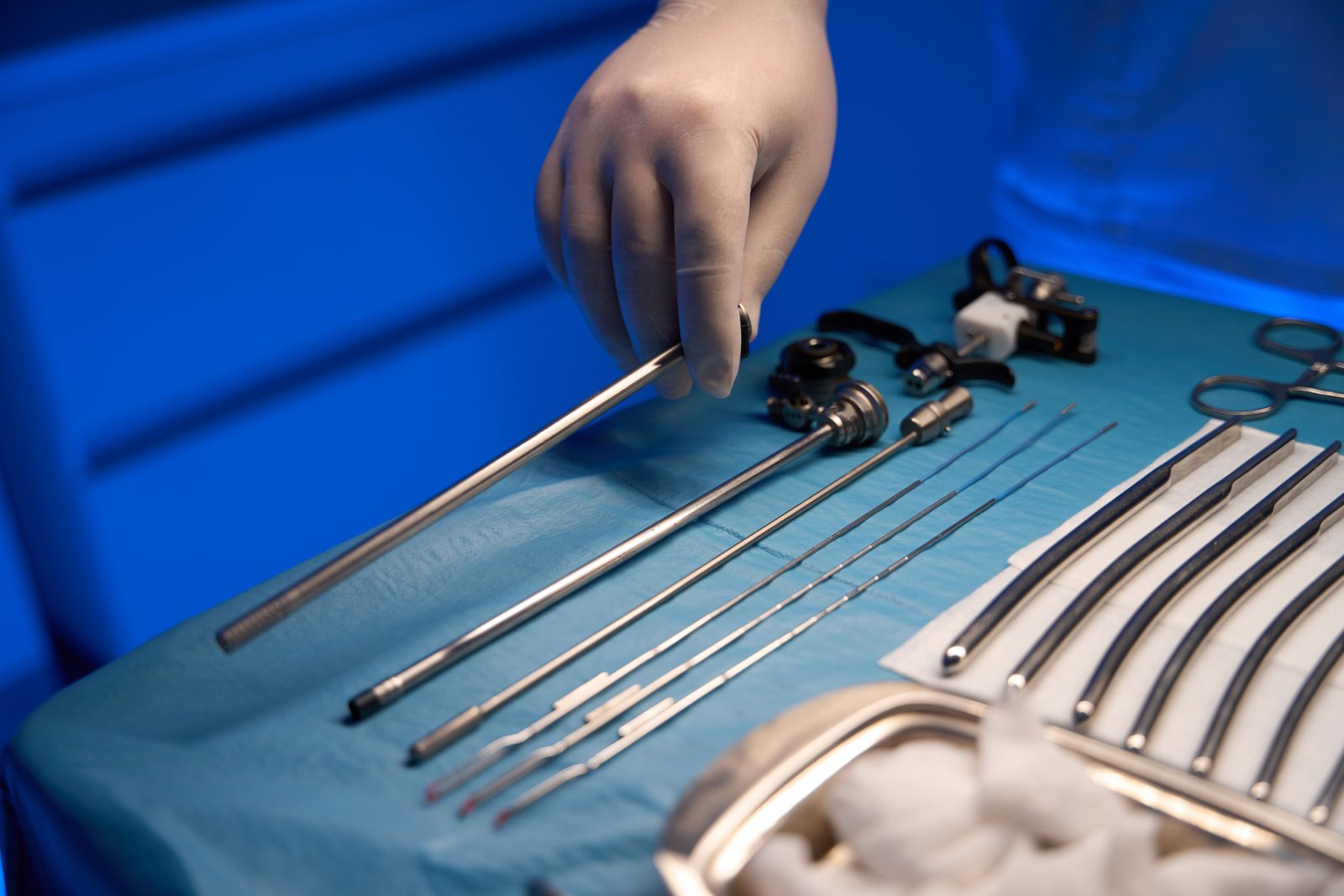
Контролируемая атмосфера является определяющей характеристикой яркого отжига. Ее состав, чистота и управление лежат в основе технологии. В то время как температура изменяет внутреннюю структуру стали, атмосфера диктует качество ее поверхности. Неспособность контролировать этот невидимый элемент приведет к неудачной партии, напрасной трате энергии и несоответствию продукта техническим требованиям. Глубокое погружение в выбор защитных газов, критическую метрику точки росы и инженерные решения, необходимые для обеспечения целостности атмосферы, раскрывают сложную науку, лежащую в основе поддержания простого и блестящего блеска. Именно здесь сходятся тщательная инженерная и производственная дисциплина, чтобы создать продукт действительно премиум-класса.
Выбор правильного защитного газа
Выбор защитной атмосферы - это баланс между производительностью, стоимостью и безопасностью. Чаще всего используются два газа: чистый водород (H2) и смесь азота и водорода (N2-H2). Чистый сухой водород - самый эффективный и мощный восстановитель. Он активно отбирает атомы кислорода, вступая с ними в реакцию с образованием водяного пара (H2O), который затем удаляется из печи. Это делает его идеальным для самых требовательных областей применения и для отжига нержавеющих сталей с высоким содержанием хрома, которые более склонны к окислению. Однако водород очень огнеопасен и требует наличия строгих систем безопасности, включая датчики утечки, циклы продувки и аварийные вентиляционные отверстия, что увеличивает капитальные и эксплуатационные сложности.
Более распространенной и экономичной альтернативой является азотно-водородная смесь, часто называемая "формовочным газом". Такие смеси обычно содержат от 5% до 25% водорода, а остальную часть составляет азот. В то время как азот инертен и не вступает в реакцию со сталью, водородный компонент обеспечивает необходимую восстановительную способность. Для большинства марок нержавеющей стали смеси 10-25% H2 достаточно для предотвращения окисления и получения превосходной блестящей поверхности. Эти смеси часто дешевле чистого водорода и могут поставляться в составе, который не воспламеняется, что упрощает требования безопасности.
Другим источником для атмосферы является диссоциированный аммиак. Диссоциатор аммиака (NH3) - это оборудование, которое расщепляет аммиак на составляющие: 75% водорода и 25% азота. Это может быть очень экономичным способом создания подходящей атмосферы N2-H2 на месте, особенно в местах, где доставка промышленного газа стоит дорого. Выбор полностью зависит от конкретных сортов отжига, местных цен на газ, а также от безопасности и эксплуатационных предпочтений заказчика.
Критическая роль точки росы
Хотя мы часто обращаем внимание на состав газа, содержание влаги в атмосфере, измеряемое как точка росы, является, пожалуй, более важным параметром для достижения успеха. Точка росы - это температура, при которой водяной пар в газе конденсируется в жидкую воду. Более низкая точка росы означает, что газ более сухой. Даже в атмосфере чистого водорода присутствие водяного пара (H2O) при высоких температурах создает окислительный потенциал. Атом кислорода в молекуле воды может вступить в реакцию с хромом и железом в стали, образуя тонкий, тускнеющий оксидный слой.
Для получения действительно яркого покрытия, особенно на высокохромистых сталях, атмосфера печи должна быть невероятно сухой. Целевым показателем обычно является точка росы -40°C или ниже, а для высокотехнологичных применений в электронике и медицинских приборах требуется точка росы -60°C или ниже. Поэтому просто закачать газ в печь недостаточно. Поступающий газ должен быть высокой чистоты, а печная система в идеале должна включать газоочиститель или осушитель, чтобы обеспечить чистоту атмосферы.
Мы устанавливаем датчики точки росы в критических местах наших печных систем. Эти датчики в режиме реального времени передают данные о содержании влаги в атмосфере на ПЛК. Если точка росы поднимается выше заданного уровня тревоги, это предупреждает оператора о потенциальной проблеме, такой как утечка в печи или снижение качества подаваемого газа. Такой непрерывный мониторинг является ключевой мерой контроля качества, которая позволяет предотвратить разрушение целых змеевиков из-за невидимого загрязнения.
Целостность печи и управление атмосферой
Поддержание атмосферы высокой чистоты и низкой точки росы невозможно без механически исправной и идеально герметичной печи. Сердцем печи непрерывного отжига является "муфель" - длинная газонепроницаемая металлическая камера, обычно изготовленная из высокотемпературного нержавеющего сплава, такого как 310S или Inconel, в которой находится полоса и защитная атмосфера. Муфель должен быть изготовлен с использованием высококачественных непрерывных сварных швов, чтобы предотвратить любые утечки.
Герметизация мест входа и выхода стальной ленты представляет собой серьезную инженерную задачу. Мы добиваемся этого с помощью комбинации волоконных завес и системы контроля положительного давления. В печи поддерживается небольшое положительное давление по отношению к наружному воздуху, поэтому при наличии любого крошечного отверстия защитный газ будет выходить наружу, а не воздух поступать внутрь. На входе и выходе мы используем специально разработанные уплотнительные коробки с регулируемыми волокнистыми завесами, которые минимизируют отверстие вокруг полосы, и в эти коробки подается постоянный поток газа для создания буфера.
Для североамериканского клиента, занимающегося производством прецизионных электронных компонентов, требование сверхчистой атмосферы с низкой точкой росы было первостепенным. Мы разработали специальную печь с полностью сварным муфелем из инконеля и интегрированной замкнутой системой рециркуляции и очистки газа. Эта система непрерывно забирает атмосферу из печи, охлаждает ее для конденсации влаги, пропускает через каталитический очиститель для удаления следов кислорода, а затем снова подает в печь. Это позволило не только поддерживать чрезвычайно низкую точку росы -65°C, но и сократить общее потребление водорода более чем на 30%, обеспечив быструю окупаемость инвестиций.
Водород предотвращает образование оксидаПравда
Чистый водород действует как восстановитель, вступая в реакцию с кислородом для предотвращения образования оксидных слоев на нержавеющей стали при отжиге в светлых тонах.
Для яркого отжига достаточно только азотаЛожь
Хотя азот инертен, он не обладает восстановительными свойствами; для активного предотвращения окисления и получения яркого покрытия необходимо присутствие водорода.
Каковы этапы отделки после отжига нержавеющей стали?
Ваша нержавеющая сталь выходит из печи идеально блестящей и отожженной. Но работа еще не закончена. Неправильное обращение или охлаждение на этом заключительном этапе может привести к искривлению и деформации или поцарапать первозданную поверхность, сведя на нет все труды, затраченные ранее.
Основные этапы отделки включают контролируемое охлаждение стали до температуры ниже температуры окисления перед выходом из защитной атмосферы. Затем следует аккуратная намотка или резка по длине с точным контролем натяжения, а также окончательный контроль качества на предмет яркости поверхности и механических свойств.
На заключительных этапах линии яркого отжига сохраняется и подтверждается качество, достигнутое в печи. Секция охлаждения, в частности, является чудом теплотехники, столь же важным, как и секция нагрева. Как я уже объяснял ранее, для многих марок нержавеющей стали скорость охлаждения жизненно важна по металлургическим причинам, но она также должна быть невероятно равномерной, чтобы материал оставался идеально ровным. В полосе, которая охлаждается быстрее по краям, чем в центре, возникнут внутренние напряжения, что приведет к нарушению формы и плоскостности, а это неприемлемо для прецизионных применений. Именно поэтому в наших передовых системах охлаждения используются высокоскоростные струи рециркулирующего, охлажденного защитного газа для равномерного и быстрого отвода тепла. После этого системы перемещения материалов, такие как откатчик8Теперь с размягченной сталью нужно обращаться бережно, с точным натяжением, чтобы создать идеальную катушку без повреждений. Окончательный проверка9 это последний привратник качества, дающий окончательное подтверждение того, что все предыдущие этапы были выполнены правильно. Это приятная заключительная глава в истории превращения сырья в ценный продукт.
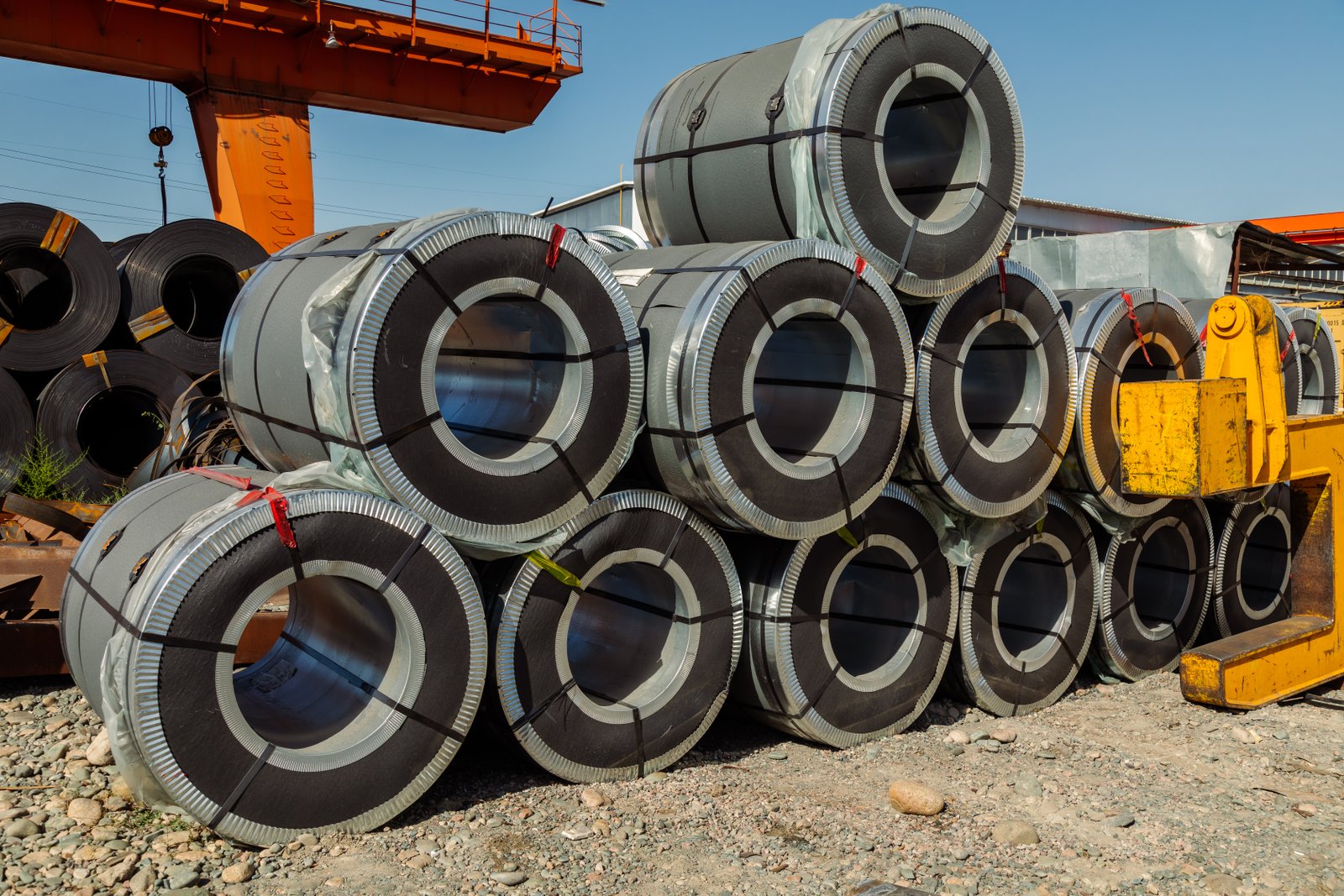
Финишная секция линии отжига - это не просто выходная рампа; это интегрированная система, предназначенная для фиксации свойств материала и качества поверхности, созданных в печи. Этот этап требует глубокого понимания теплопередачи, механической обработки хрупких материалов и надежных методик контроля качества. Инженерные решения, которые используются для равномерного охлаждения, точность, необходимая для обработки после отжига, и строгий контроль качества - вот что отличает производственную линию мирового класса от обычной. Каждый из этих элементов способствует получению не только яркого, но и ровного, точного по размерам и металлургически чистого продукта, готового к использованию в конечной области применения.
Инженерия контролируемого охлаждения
Охлаждающая секция печи непрерывного отжига представляет собой закрытый муфель, такой же, как и нагревательная секция, и остается заполненной защитной атмосферой. Это очень важно, поскольку сталь должна быть охлаждена до достаточно низкой температуры (обычно ниже 200°C), чтобы она не окислялась при контакте с окружающим воздухом. Задача состоит в том, чтобы быстро и равномерно отвести огромное количество тепловой энергии от движущейся полосы стали.
Для этого мы используем передовую технологию струйного охлаждения. Для этого над и под полосой располагаются пленумы, содержащие сотни небольших сопел. Большие объемы охлажденного защитного газа нагнетаются через эти сопла с высокой скоростью, воздействуя непосредственно на стальную поверхность. Этот высокоскоростной поток разрушает изолирующий пограничный слой газа, который естественным образом прилипает к полосе, что приводит к очень высокому коэффициенту теплопередачи и чрезвычайно быстрому охлаждению. Затем газ отводится, проходит через теплообменник с водяным охлаждением и возвращается в струи по замкнутому контуру.
Конструкция этих струйных охладителей имеет решающее значение для обеспечения плоскостности полосы. Форма и давление сопел тщательно разрабатываются, чтобы обеспечить одинаковую скорость охлаждения в центре и по краям полосы. Для оптимизации этих систем на этапе проектирования используется сложное моделирование вычислительной гидродинамики (CFD). Такое равномерное охлаждение предотвращает возникновение термических напряжений, которые являются основной причиной дефектов формы после отжига, таких как "краевая волна" или "центральный изгиб".
Обработка материалов после отжига
Когда сталь достаточно остынет, она выходит из защитной атмосферы и попадает на участок окончательной обработки на линии. Теперь материал находится в самом мягком и пластичном состоянии, что делает его восприимчивым к царапинам и деформации. Все ролики и направляющие на этом участке должны быть идеально гладкими, часто хромированными или покрытыми немарким полимером, и точно выровненными.
Разматыватель - это последняя часть основного оборудования. Его задача - смотать непрерывную полосу в плотный рулон с прямыми сторонами для удобства транспортировки и обработки. Для этого требуется очень точная система контроля натяжения. Слишком слабое натяжение - и рулон будет рыхлым и нестабильным, склонным к повреждениям. Слишком сильное натяжение может привести к растяжению мягкой отожженной полосы, уменьшению ее толщины и изменению механических свойств - явление, известное как "омертвение". В современных линиях используется танцующий вал или система на основе тензодатчика, обеспечивающая обратную связь с приводным двигателем отдатчика, поддерживая постоянное натяжение на протяжении всего процесса наращивания рулона, от пустой оправки до полного диаметра рулона.
Для линий, производящих не рулоны, а разрезанные листы, используются летучие ножницы. Это устройство должно разрезать полосу на требуемую длину на лету, не останавливая линию, и делать это без образования заусенцев или деформации краев листа. Точность этого оборудования для послеотжиговой обработки имеет решающее значение для получения продукта, который соответствует размерам и физическим характеристикам заказчика.
Обеспечение качества и контроль
Последний шаг перед тем, как продукт будет одобрен к отправке, - тщательная проверка качества. Именно здесь подтверждается успешность всего процесса. Эта проверка обычно включает в себя несколько основных этапов. Во-первых, это визуальный осмотр при контролируемом освещении для выявления любых дефектов поверхности, таких как пятна, царапины или неравномерность яркости.
Во-вторых, часто проводятся количественные измерения. Для измерения отражательной способности поверхности можно использовать блескомер, который дает числовое значение "яркости", которое можно отслеживать при статистическом контроле процесса (SPC). Это обеспечивает постоянство от рулона к рулону. Также часто отбираются образцы для механических испытаний. Испытание на растяжение проводится для измерения предельной прочности материала на разрыв и удлинения, что подтверждает, что в процессе отжига была достигнута желаемая мягкость и пластичность. Также могут проводиться испытания на твердость.
На многих современных предприятиях некоторые из этих проверок интегрированы непосредственно в линию. Например, автоматизированная система контроля поверхности может использовать высокоскоростные камеры и алгоритмы машинного обучения для сканирования 100% поверхности полосы в режиме реального времени, отмечая любые потенциальные дефекты для проверки. Это обеспечивает немедленную обратную связь с операторами, позволяя им быстро вносить коррективы в процесс при обнаружении каких-либо отклонений. Эта заключительная, комплексная проверка качества является для клиента окончательной гарантией того, что он получает продукт, соответствующий всем его требованиям.
Охлаждение должно быть равномернымПравда
Неравномерное охлаждение вызывает внутренние напряжения и дефекты формы, такие как краевая волна или центральный изгиб.
Сталь выходит из строя при 200°CЛожь
Для предотвращения окисления сталь перед выходом из печи должна быть охлаждена ниже 200°C, а не при 200°C.
Заключение
В конечном итоге достижение безупречной яркости отжига - это систематический процесс. Он основывается на четырех принципах: безупречной предварительной очистке, точном многозонном температурном контроле, поддержании сверхчистой защитной атмосферы и контролируемом равномерном охлаждении. Овладение этими этапами превращает нержавеющую сталь в высококачественный высокопроизводительный материал.
-
Понять процесс отжига и его преимущества при обработке нержавеющей стали ↩
-
Узнайте, почему хром вступает в реакцию с кислородом и как он влияет на стальные поверхности. ↩
-
Откройте для себя решение для устранения поверхностных дефектов при отжиге нержавеющей стали ↩
-
Узнайте о процессе очистки для удаления загрязнений перед отжигом ↩
-
Поймите важность быстрого охлаждения для сохранения коррозионной стойкости нержавеющей стали. ↩
-
Узнайте, как различается обработка аустенитных и ферритных нержавеющих сталей. ↩
-
Понять, как содержание влаги влияет на качество отделки отожженной стали ↩
-
Узнайте, как натяжение разматывателя предотвращает дефекты и поддерживает качество рулонов ↩
-
Понимание этапов контроля, обеспечивающих соответствие отожженной стали стандартам качества ↩