Как предотвратить поверхностные трещины и коррозию при отжиге проволоки из нержавеющей стали?
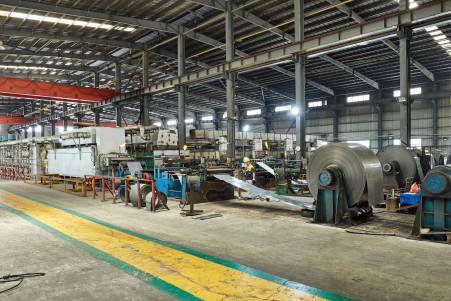
Страдаете от микротрещин и неожиданной коррозии на проволоке из нержавеющей стали после отжига? Эти дефекты могут нарушить целостность вашего продукта, привести к дорогостоящему браку и испортить репутацию вашего бренда. Ключ к решению этой проблемы лежит в освоении яркий отжиг1 для достижения безупречного и долговечного покрытия.
Яркий отжиг - это критический процесс термообработки, требующий точного контроля температуры и атмосферы. Поверхностные трещины в основном вызваны термическим напряжением из-за неправильной скорости нагрева/охлаждения, а коррозия возникает из-за атмосферных примесей или недостаточного ухода после отжига - оба эти фактора разрушают защитный пассивный слой материала.
За годы работы дизайнером промышленные печи2Я видел, как эти, казалось бы, незначительные проблемы могут стать серьезными препятствиями для производителей. Речь идет не только о проволоке, но и об эксплуатационных характеристиках конечного продукта, будь то критически важный медицинский имплантат или высокопрочная пружина. Эта статья поможет вам разобраться в сложностях этого процесса и перейти от устранения дефектов к активному обеспечению качества.
Мы всесторонне рассмотрим основные причины этих распространенных, но сложных проблем. Это путешествие выходит за рамки простых температурных настроек. Мы изучим науку о напряжении материалов, химию защитной атмосферы и практические шаги, которые вы можете предпринять для совершенствования своих операций. Опираясь на реальные примеры из практики и отраслевые данные, я хочу предоставить вам действенные идеи, которые вы сможете применить непосредственно на своем предприятии для производства неизменно превосходной проволоки из нержавеющей стали.
Что вызывает поверхностные трещины при отжиге проволоки из нержавеющей стали?
Вы заметили тонкие линии или трещины на проволоке после выхода ее из печи? Эта проблема, известная как поверхностное растрескивание, часто указывает на внутренние напряжения, которые становятся слишком большими для материала во время цикла отжига, что в конечном итоге приводит к дорогостоящим производственным потерям.
Поверхностные трещины в проволоке из нержавеющей стали, подвергнутой отжигу, в основном возникают из-за быстрого или неравномерного нагрева и охлаждения, что создает термическое напряжение. Другими факторами, способствующими появлению трещин, являются существующие дефекты материала, чрезмерное натяжение проволоки и нечистая атмосфера печи, вызывающая охрупчивание поверхности.
Понимание этих причин - первый важный шаг к их устранению. Это не одна проблема, а комбинация термических, механических и химических факторов, которые действуют против целостности вашего продукта. По моему опыту, многие производители концентрируются исключительно на пиковой температуре, упуская из виду критическую роль нагрева и охлаждения. тарифы. Путешествие проволоки через печь - это тонкий танец расширения и сжатия. Если этот процесс происходит поспешно или неравномерно, напряжение концентрируется на поверхности, особенно вокруг микроскопических дефектов или границ зерен. В конечном итоге это напряжение находит выход в виде трещины. Кроме того, сама атмосфера, призванная защищать проволоку, может обернуться против нее, если ее не контролировать. Такие загрязнители, как кислород или влага, даже в незначительных количествах могут привести к выборочному окислению по границам зерен, создавая слабые места, в которых могут зарождаться трещины. Нам необходимо глубже изучить эти элементы, чтобы создать надежную стратегию предотвращения, перейдя от реактивного к проактивному состоянию контроля качества. Речь идет о создании процесса, который будет не только эффективным, но и устойчивым.
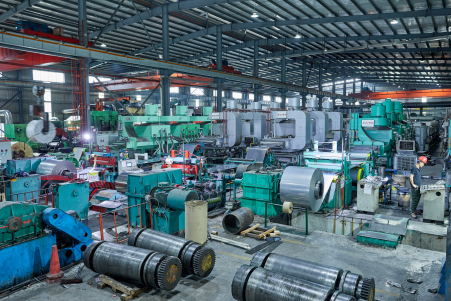
Когда мы анализируем основные причины растрескивания поверхности, необходимо выйти за рамки поверхностного списка и углубиться во взаимосвязанные физические и химические процессы. Весь процесс яркого отжига должен рассматриваться как целостная система, в которой терморегулирование, целостность атмосферы и обработка материалов неразрывно связаны между собой. Сбой в одной из областей может легко перерасти в дефект поверхности, который сделает конечный продукт непригодным для использования, особенно в таких ответственных областях, как медицинские приборы или автомобильные компоненты. Я работал с клиентом, производящим тонкую проволоку из нержавеющей стали марки 304 для хирургических инструментов, у которого внезапно увеличился процент брака из-за микротрещин. Первоначальное расследование было направлено на сырье, но в конечном итоге проблема оказалась связана с тонкими изменениями в процессе отжига.
Критическое воздействие теплового удара и стресса
Терморегулирование, пожалуй, является наиболее влиятельным фактором в предотвращении поверхностных трещин. Нержавеющая сталь, как и все металлы, расширяется при нагревании и сжимается при охлаждении. Если этот процесс происходит неравномерно по всему сечению проволоки, возникают внутренние напряжения. Поверхность нагревается или охлаждается быстрее, чем сердцевина, создавая температурный градиент, который оказывает сильное давление на зернистую структуру материала. Это и есть тепловой удар. Например, если проволока слишком быстро попадает в зону перегрева, поверхность быстро расширяется, в то время как сердцевина отстает, вызывая растягивающее напряжение в сердцевине и сжимающее напряжение на поверхности.
Эта проблема усугубляется на этапе охлаждения. Быстрое охлаждение, часто предназначенное для повышения производительности, может оказаться губительным. Поверхность быстро сжимается над все еще расширенной сердцевиной, создавая огромное растягивающее напряжение в поверхностном слое. Если это напряжение превышает предел прочности материала на растяжение при данной температуре, образуются трещины. Данные металлургических исследований показывают, что для нержавеющих сталей серии AISI 300 скорость охлаждения, превышающая 100°C в секунду, может привести к образованию микротрещин, особенно в проволоках большого диаметра. Наши печи для отжига блестящей стали AKS имеют многозонный нагрев и точно контролируемый муфель для охлаждения. Это позволяет получить запрограммированный, постепенный температурный профиль, который минимизирует тепловые градиенты, снижая внутреннее напряжение до 70% по сравнению с более старыми конструкциями печей с одной зоной нагрева.
В качестве примера можно привести производителя пружин из нержавеющей стали, который боролся с растрескиванием намотанной проволоки. В их печи была нарушена равномерность температуры, а горячие точки превышали заданное значение более чем на 30 °C. Внедрив печь с улучшенным зональным контролем и более медленной, плавной кривой охлаждения, они смогли полностью устранить трещины, связанные с тепловым ударом. Это подчеркивает, что тариф Изменение температуры так же важно, как и сама пиковая температура.
Чистота атмосферы и ее влияние на охрупчивание материалов
Яркий" отжиг обусловлен использованием защитной атмосферы, обычно диссоциированного аммиака (75% водорода, 25% азота) или чистого водорода, для предотвращения окисления. Однако чистота этой атмосферы имеет первостепенное значение. Такие загрязнители, как кислород и водяной пар (определяемый по точке росы), могут быть невероятно вредными. При высоких температурах отжига эти загрязнители избирательно окисляют хром на границах зерен нержавеющей стали. Такое обеднение хромом ослабляет границы, делая материал хрупким и подверженным растрескиванию под нагрузкой.
Я вспоминаю клиента из электронной промышленности, производящего тонкую проволоку для разъемов. Они испытывали периодические проблемы с растрескиванием, которые не могли объяснить. Мы проанализировали атмосферу их печи и обнаружили, что точка росы колеблется, иногда поднимаясь до -30°C. На этом уровне присутствовало достаточно водяного пара, чтобы вызвать микроокисление. Идеальная точка росы для яркого отжига должна составлять -60°C или ниже. Даже небольшая утечка в уплотнении печи или подача загрязненного газа может поднять точку росы до опасного уровня. Такое окисление не только создает начальную точку для образования трещин, но и снижает коррозионную стойкость нержавеющей стали.
Именно поэтому в современных печах, подобных тем, которые мы строим в AKS, особое внимание уделяется газонепроницаемой конструкции и передовым системам контроля атмосферы. Мы используем изоляцию из высокочистого керамического волокна и многоточечные уплотнения для предотвращения проникновения воздуха. Встроенный датчик точки росы, обеспечивающий обратную связь в режиме реального времени, позволяет операторам немедленно принять меры по исправлению ситуации, если чистота атмосферы нарушена. Для заказчика электроники переход на печь с повышенной герметичностью и системой мониторинга решил проблему растрескивания и улучшил паяемость проволоки, обеспечив неожиданную вторичную выгоду.
Роль предсуществующих условий и механического напряжения
Процесс отжига часто может выявить или усугубить проблемы, которые уже присутствовали в проволоке. Дефекты поверхности, образовавшиеся в процессе волочения, такие как царапины, швы или вкрапления смазки, могут служить концентраторами напряжений. При нагреве проволоки эти мелкие дефекты становятся местами зарождения трещин. Микроскопическая царапина от изношенной волочильной матрицы создает слабую точку, в которой концентрируются термические напряжения, что значительно повышает вероятность ее выхода из строя.
Поэтому тщательная очистка перед отжигом не является необязательной, она необходима. Смазочные материалы для волочения, особенно содержащие хлор или серу, должны быть полностью удалены. Если они останутся на поверхности, то при высоких температурах могут запечься в стали, вызывая науглероживание или сульфидирование, что приводит к локальному охрупчиванию и дефектам поверхности. Один из наших клиентов, производитель архитектурной проволочной сетки, смог отследить проблему растрескивания, связанную с изменением смазки для волочения. Новая, более дешевая смазка труднее очищалась и оставляла остатки, которые вызывали точечную коррозию поверхности в печи.
Кроме того, фактором является механическое обращение с проволокой в самой печи. Чрезмерное натяжение, создаваемое системами подачи и отбора, может вызвать значительное механическое напряжение в дополнение к тепловому напряжению, которое уже испытывает проволока. Это особенно верно для тонкой проволоки. Правильно спроектированная печная линия включает в себя сложные системы контроля натяжения, которые поддерживают постоянный, минимальный уровень нагрузки на проволоку на всем ее пути. Это гарантирует, что проволока не растягивается в то время, когда она находится в самом слабом состоянии, т. е. при пиковой температуре отжига.
Фактор | Плохая практика и результат | Передовой опыт и результаты | Влияние на растрескивание |
---|---|---|---|
Скорость охлаждения | >100°C/с (ударное охлаждение) | <50°C/с (контролируемое охлаждение) | Высокий |
Точка росы в атмосфере | -30°C (загрязнено) | <-60°C (высокая чистота) | Высокий |
Подготовка поверхности | Остаточная смазка для вытяжки | Тщательно обезжиренная поверхность | Средний |
Натяжение проволоки | >5% от предела текучести | <1% от предела текучести | Средний |
Тепловой удар вызывает поверхностные трещиныПравда
Быстрое или неравномерное нагревание/охлаждение создает тепловое напряжение, превышающее прочность материала, что приводит к образованию поверхностных трещин в проволоке из нержавеющей стали.
Чистота атмосферы не влияет на растрескиваниеЛожь
Такие загрязнители, как кислород или влага, содержащиеся в атмосфере печи, вызывают истощение хрома на границах зерен, делая материал хрупким и склонным к растрескиванию.
Почему коррозия является распространенной проблемой при использовании проволоки из нержавеющей стали?
Вы выбрали нержавеющую сталь за ее легендарную коррозионную стойкость, но обнаружили ржавчину или точечный налет на готовой проволоке. Это досадное противоречие часто возникает, когда нарушается защитный пассивный слой - проблема, которая может начаться задолго до установки проволоки.
Коррозия возникает в проволоке из нержавеющей стали при повреждении или неправильном формировании пассивного слоя оксида хрома. Обычные причины включают загрязнение поверхности частицами железа, воздействие агрессивных хлоридов (например, соли), коррозию, вызванную хлоридами, и сенсибилизацию, вызванную неправильной термообработкой, которая истощает хром по границам зерен.
Репутация нержавеющей стали зависит от микроскопической, невидимой защиты: пассивного слоя оксида хрома. Этот слой образуется естественным образом, когда хром в стали вступает в реакцию с кислородом. Однако он не является неуязвимым. Считайте его тонким слоем брони. Несмотря на свою прочность, он может быть пробит. Сайт яркий отжиг3 предназначен для идеального формирования этого слоя в контролируемой среде, но любая ошибка может оставить его слабым или неполным. Например, если атмосфера печи недостаточно чиста или если процесс охлаждения несовершенен, защитный слой не сформируется правильно. Кроме того, жизнь проволоки после печи сопряжена с опасностями. Загрязнение от оснастки из углеродистой стали, воздействие прибрежного соляного тумана или контакт с промышленными химикатами - все это может вызвать коррозионную атаку. Проще говоря, хотя нержавеющая сталь по своей природе устойчива к коррозии, она не является неуязвимой, и для поддержания ее целостности требуется глубокое понимание как металлургии, так и окружающей среды. Это битва, ведущаяся в микроскопических масштабах, и победа в ней требует усердия на каждом этапе производства и эксплуатации.
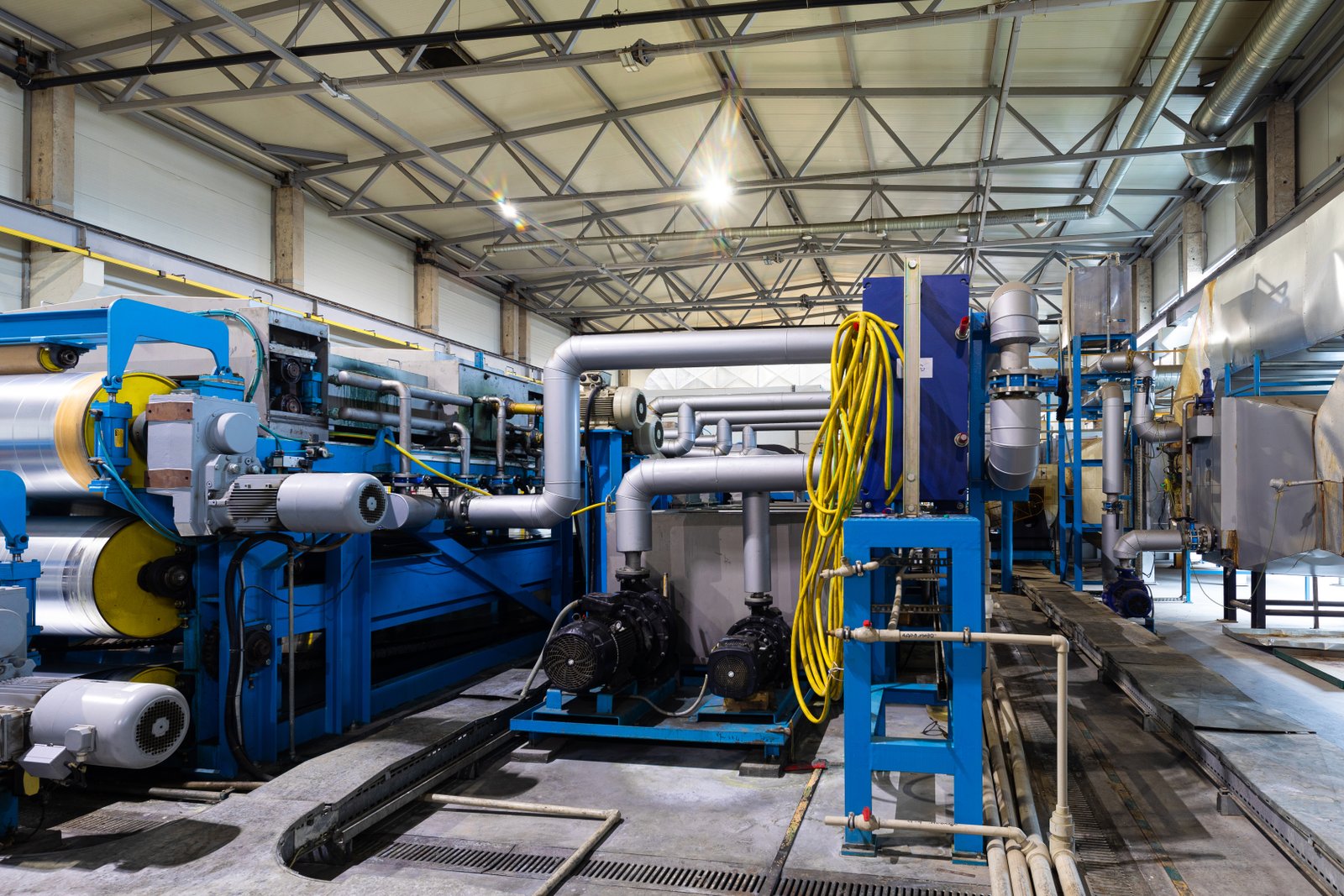
Чтобы по-настоящему понять и предотвратить коррозию, мы должны оценить тонкую природу пассивного слоя. Это динамическая пленка толщиной всего в несколько нанометров, которая защищает железо в сплаве от реакции с окружающей средой. Любой процесс, нарушающий формирование этого слоя оксида хрома (Cr₂O₃) или локально разрушающий его, открывает двери для коррозии. Многие пользователи удивляются, когда их "нержавеющая" сталь покрывается пятнами, но причины почти всегда можно найти в конкретном нарушении этого защитного механизма. В компании AKS мы не просто строим печи, мы предлагаем решения, что означает помощь нашим клиентам в понимании полного жизненного цикла их продукции и экологических проблем, с которыми они столкнутся. Такой целостный подход имеет решающее значение для предотвращения отказов, связанных с коррозией.
Сенсибилизация: Скрытый враг внутри
Одной из самых коварных причин коррозии является "сенсибилизация" - явление, возникающее при неправильной термической обработке. Это особенно актуально для аустенитных нержавеющих сталей, таких как 304 и 316. Если сталь слишком долго выдерживать в определенном температурном диапазоне (примерно от 450°C до 850°C), углерод в сплаве мигрирует к границам зерен и соединяется с хромом, образуя карбид хрома (Cr₂₃C₆). Этот процесс блокирует хром, истощая области, прилегающие к границам зерен, именно тем элементом, который необходим для формирования защитного пассивного слоя.
В результате микроструктура становится очень уязвимой для межкристаллитной коррозии. Основная часть зерна остается защищенной, но истощенные границы зерен выступают в роли анодных дорожек, и коррозия агрессивно атакует эти сети, опустошая материал изнутри. Это может привести к катастрофе, поскольку поверхность может выглядеть хорошо, но внутренняя структура сильно ослаблена. Я работал с производителем проволоки из нержавеющей стали для морского применения, который столкнулся с отказами в работе, несмотря на то, что после отжига проволока выглядела идеально. A металлургический анализ нержавеющей стали4 выявили классическую сенсибилизацию. В их старой печи была очень медленная, неконтролируемая зона охлаждения, из-за чего проволока слишком долго находилась в критическом диапазоне температур.
Для предотвращения сенсибилизации требуется быстрое охлаждение в диапазоне 450-850°C. В наших печах для отжига блестящей стали AKS используется усовершенствованная система охлаждения с высокоскоростной газовой струей, которая позволяет охлаждать проволоку в этой критической зоне за секунды, а не за минуты. Такое быстрое охлаждение не дает атомам углерода времени на миграцию и образование карбидов, сохраняя хром там, где он больше всего нужен - в твердом растворе, готовом к образованию пассивного слоя. Использование низкоуглеродистых нержавеющих сталей (марки L), таких как 304L или 316L, с максимальным содержанием углерода 0,03%, также значительно снижает риск, поскольку ограничивает количество углерода, доступного для образования карбидов.
Влияние загрязнения поверхности и загрязняющих веществ
Коррозия - это часто внешняя работа, инициированная чем-то, что не должно находиться на поверхности проволоки. Одним из наиболее распространенных виновников является загрязнение "свободным железом". Это происходит, когда проволока из нержавеющей стали вступает в контакт с инструментами из углеродистой стали, стойками, проволочными щетками или даже воздушной пылью от близлежащих шлифовальных операций. Эти крошечные частицы железа оседают на поверхности и в присутствии влаги ржавеют. Затем эта ржавчина может разрушить пассивный слой под ней и вызвать точечную коррозию в самой нержавеющей стали.
Еще одна серьезная угроза - хлориды. Хлорид-ионы, содержащиеся в соли, антиобледенительных растворах и многих промышленных химикатах, особенно агрессивны по отношению к пассивному слою. Они могут вызвать локальное разрушение пленки, что приводит к точечной коррозии - мелким, глубоким ямам, которые быстро проникают в материал. Однажды я консультировал компанию, производящую проволочные корзины из нержавеющей стали для пищевого предприятия, где использовались дезинфицирующие средства на основе хлоридов. Они заметили точечные повреждения уже через несколько недель после установки. Решение было двояким: переход на более устойчивую к хлоридам марку нержавеющей стали (например, 316, содержащую молибден) и внедрение строгого протокола промывки пресной водой после очистки.
Сам процесс яркого отжига может стать источником загрязнения, если им неправильно управлять. Как уже говорилось ранее, нечистая атмосфера печи может привести к образованию некачественного, незащищенного оксидного слоя. Чистая поверхность и чистая атмосфера во время процесса являются обязательными условиями для достижения максимальной коррозионной стойкости. Именно поэтому в наших конструкциях печей большое внимание уделяется изоляции технологической камеры от любых потенциальных загрязнителей, гарантируя, что то, что выходит на выходе, будет таким же чистым, как и то, что вошло внутрь.
Понимание различных видов коррозии
Не всякая коррозия одинакова, и определение ее типа - ключ к поиску причины. Если общая коррозия (равномерное истончение поверхности) встречается в нержавеющей стали редко, то локальная коррозия - настоящий враг. Мы уже обсуждали межкристаллитную коррозию (в результате сенсибилизации) и питтинговую коррозию (в результате воздействия хлоридов). Еще один важный вид - щелевая коррозия, которая возникает в узких местах, где кислород ограничен, например, под шайбами или в несваренных накладках. В этих щелях кислород обеднен, что препятствует реформированию пассивного слоя в случае его повреждения. Область внутри щели становится анодной, а область снаружи с большим количеством кислорода - катодной, создавая коррозионную ячейку, которая может быстро разъедать материал.
Коррозионное растрескивание под напряжением (КРН) - это, пожалуй, самая опасная форма. Для ее возникновения требуется особое сочетание трех факторов: восприимчивый материал, коррозионная среда (часто хлориды) и растягивающее напряжение (либо при изготовлении, либо при применении). Результатом может стать внезапное, хрупкое разрушение детали, которая на первый взгляд кажется совершенно нормальной. Процесс отжига играет здесь важную роль, снимая остаточные напряжения, возникающие при волочении проволоки, что значительно снижает восприимчивость материала к SCC.
Необходим комплексный подход. Он начинается с выбора сплава, подходящего для предполагаемой среды, затем следует тщательно контролируемый процесс отжига для снятия напряжения и формирования идеального пассивного слоя, и, наконец, надлежащие протоколы обращения и обслуживания, позволяющие избежать загрязнения и воздействия агрессивных химических веществ.
Тип коррозии | Основная причина | Внешний вид | Стратегия профилактики |
---|---|---|---|
Межкристаллитная | Сенсибилизация (неправильное охлаждение) | Микроскопический удар по границам зерен | Быстрое охлаждение, использование сортов "L" |
Питтинг | Воздействие хлоридов | Небольшие, глубокие отверстия на поверхности | Молибденсодержащие марки (например, 316), избегайте хлоридов |
Щель | Кислородно-дефицитные щели/зазоры | Локализованная атака в ограниченном пространстве | Разработайте щели, обеспечьте надлежащий дренаж |
Коррозионное растрескивание под напряжением | Растягивающее напряжение + коррозионная среда. | Тонкие трещины, часто ветвящиеся | Отжиг для снятия напряжения, выбор материала, условия контроля |
Нержавеющая сталь может корродироватьПравда
Несмотря на свою прочность, пассивный слой нержавеющей стали может быть нарушен загрязнением, хлоридами или неправильной термообработкой.
Вся коррозия выглядит одинаковоЛожь
Нержавеющая сталь подвержена различным видам коррозии (питтинговая, межкристаллитная, щелевая, SCC), которые имеют разные причины и проявления.
Как поверхностные трещины и коррозия влияют на характеристики проволоки из нержавеющей стали?
Думаете, что крошечные поверхностные трещины или небольшие пятна ржавчины - это просто косметические проблемы? Подумайте еще раз. Эти дефекты - тихие убийцы производительности, резко снижающие прочность и надежность проволоки, что может привести к катастрофическим отказам в критически важных областях применения - от медицинских приборов до конструкционных кабелей.
Поверхностные трещины действуют как источники напряжения, значительно снижая усталостную прочность и прочность на разрыв, что приводит к преждевременному механическому разрушению проволоки. Коррозионная точечная коррозия разрушает материал, вызывая потерю площади поперечного сечения и образуя ямы, которые также могут привести к образованию трещин и нарушить целостность и внешний вид изделия.
Влияние этих дефектов выходит далеко за рамки эстетики; они коренным образом изменяют механические и химические свойства проволоки. Проволоку из нержавеющей стали часто выбирают за точное сочетание прочности, пластичности и коррозионной стойкости. Когда появляется трещина, она создает точку слабости, где напряжение концентрируется чрезвычайно сильно. Представьте, что сила, проходящая через проволоку, вынуждена огибать кончик микроскопической трещины - локализованное напряжение в этой точке может быть в сотни раз выше, чем общее напряжение в проволоке. Вот почему проволока, которая должна выдерживать тысячи циклов, может выйти из строя всего через несколько сотен. Аналогичным образом, коррозия - это не просто пятно на поверхности; это химическая атака, которая активно удаляет материал, истончая проволоку и создавая грубые ямы, служащие новыми источниками напряжения. В своей роли в AKS я подчеркиваю, что производство "хорошей" проволоки - это не просто соблюдение допусков на размеры; это обеспечение базовых эксплуатационных характеристик, от которых зависит конечный пользователь. Целостность поверхности напрямую связана с целостностью конечного продукта.
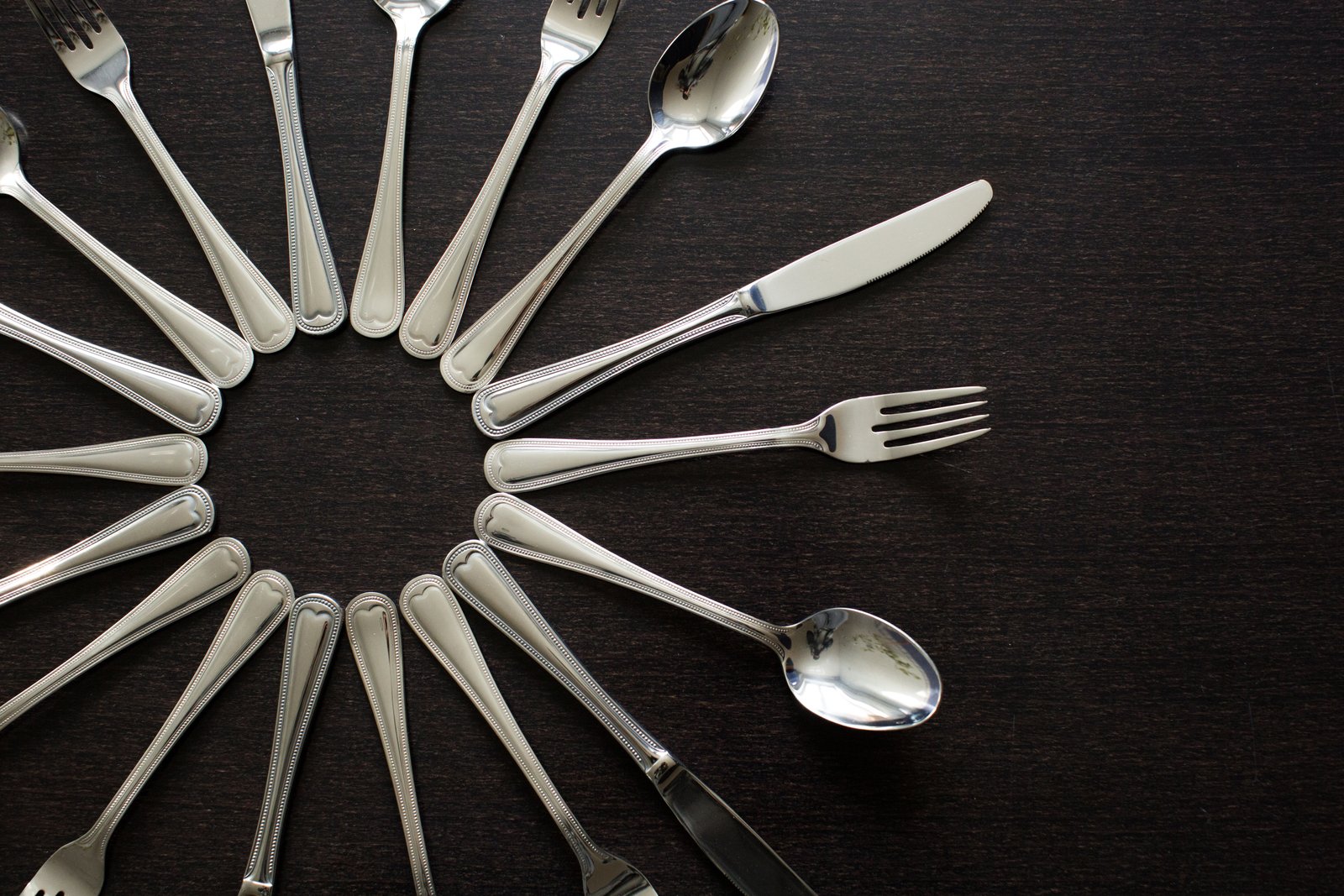
Когда заказчик указывает определенную марку и температуру проволоки из нержавеющей стали, он приобретает набор обещаний, касающихся эксплуатационных характеристик. Эти обещания - будь то усталостная прочность пружины, электропроводность соединителя или биосовместимость хирургического инструмента - немедленно нарушаются наличием поверхностных трещин и коррозии. Финансовые и репутационные издержки таких отказов могут быть огромными. Давайте разберемся, как именно эти дефекты снижают эффективность, опираясь на инженерные принципы и реальные примеры, с которыми я сталкивался, помогая клиентам оптимизировать процессы термообработки.
Снижение механической прочности и усталостной долговечности
Самым непосредственным следствием поверхностной трещины является резкое снижение механической целостности проволоки. С инженерной точки зрения, трещина - это "концентратор напряжения" или "источник напряжения". Как описано в Теория хрупкого разрушения Гриффита5Напряжение на кончике острой трещины может быть усилено на несколько порядков. Это означает, что проволока при нормальном, безопасном уровне натяжения может испытывать напряжение на кончике трещины, превышающее ее предел прочности на растяжение, что приведет к быстрому распространению трещины и ее разрушению. Провод выходит из строя при нагрузке, намного меньшей его расчетной мощности.
Это особенно важно при динамических или циклических нагрузках, таких как пружины, канаты и вибрационные компоненты. Усталостное разрушение - это процесс, при котором материал разрушается после многократного воздействия циклов нагрузки. Гладкая, без дефектов поверхность может выдержать очень большое количество циклов. Однако поверхностная трещина служит местом зарождения усталостной трещины, которая будет расти с каждым циклом. Исследования нержавеющей стали 304 показали, что наличие поверхностной трещины глубиной 0,1 мм может снизить усталостный ресурс более чем на 50%. Один из клиентов, производящий пружины для автомобильных клапанов, на собственном опыте убедился в этом, когда столкнулся с проблемой отзыва. Проблема была связана с микротрещинами на линии отжига, которые выступали в качестве инициаторов усталости.
Коррозия также играет здесь непосредственную роль. Точечная коррозия создает небольшие полости, которые, с точки зрения механики, идентичны небольшим трещинам. Дно коррозионной ямы представляет собой острую выемку, концентрирующую напряжение, что делает ее идеальной отправной точкой для усталостного разрушения. Такое взаимодействие коррозии и напряжения известно как коррозионная усталость, и оно может привести к тому, что компоненты выйдут из строя даже быстрее, чем это сделал бы один из механизмов.
Снижение коррозионной стойкости и загрязнения продуктов
Само наличие коррозии указывает на то, что основной защитный механизм проволоки - пассивный слой - вышел из строя. Как только коррозия начинается, она часто ускоряется. Например, ржавчина от загрязнения свободным железом может удерживать влагу и хлориды на поверхности, создавая еще более агрессивную среду и заставляя нержавеющую сталь корродировать быстрее. Это приводит к потере материала, уменьшению диаметра проволоки и, следовательно, ее несущей способности.
Во многих отраслях отсутствие коррозии является не только показателем эффективности, но и нормативным требованием. В пищевой, фармацевтической и медицинской промышленности корродированная поверхность неприемлема. На ней могут размножаться бактерии, что делает невозможной надлежащую санитарную обработку. Кроме того, продукты коррозии (например, оксиды железа и хрома) могут просачиваться в обрабатываемый продукт, приводя к его загрязнению, изменению цвета или появлению неприятного привкуса.
Я консультировал производителя проволочных лотков для фармацевтических чистых помещений. На их лотках появились следы точечной коррозии. Это не только вызывало опасения по поводу их структурной целостности, но и означало, что они больше не соответствовали стандартам GMP (надлежащей производственной практики), поскольку стерильность изъязвленных поверхностей не могла быть гарантирована. Причина была найдена в процессе отжига, который оставил поверхность слегка сенсибилизированной, в сочетании с воздействием чистящих средств. Переход на печь с быстрым охлаждением и внедрение более строгих протоколов обращения с продуктом были необходимы для восстановления его характеристик и соответствия требованиям.
Деградация эстетических и функциональных свойств поверхности
Для многих изделий яркая и чистая отделка из нержавеющей стали является ключевым преимуществом. Архитектурные сетки, кухонные приборы и бытовая электроника - все они полагаются на эту эстетическую привлекательность. Коррозия и трещины разрушают эту визуальную ценность. Ржавая проволока на дорогом приборе или обесцвеченная сетка на фасаде здания - это немедленный признак низкого качества, что приводит к жалобам клиентов и гарантийным обязательствам.
Помимо эстетики, качество поверхности часто имеет функциональное значение. Для электрополированных проволок, используемых в медицинских стентах или направляющих проволоках, поверхность должна быть безупречно гладкой, чтобы обеспечить биосовместимость и низкое трение. Трещина или ямка делают это невозможным. В тех случаях, когда проволока сваривается, загрязненная или корродированная поверхность может привести к плохому качеству сварки, пористости и слабым соединениям.
Процесс блестящего отжига назван так из-за получаемой в результате обработки поверхности. Цель - зеркальная, гладкая и чистая поверхность. В компании AKS мы разрабатываем наши линии для отжига с учетом этой конечной цели. Муфель, изготовленный из высокотемпературных сплавов, таких как 310S или инконель, предназначен для предотвращения любого контакта, который может поцарапать проволоку. Атмосферный контроль достаточно точен, чтобы предотвратить даже малейшее окисление, сохраняя блестящую поверхность, полученную в процессе волочения. Достижение идеальной поверхности - это не только внешний вид; это прямой показатель здоровой, ослабленной напряжением микроструктуры и прочного пассивного слоя, гарантирующего, что проволока будет работать как надо во всех аспектах.
Дефект | Влияние на механические свойства | Влияние на химические свойства | Влияние на функциональные/эстетические свойства |
---|---|---|---|
Поверхностные трещины | Сильное снижение усталостной прочности и прочности на разрыв. | Действует как место начала кревизионной/напряженной коррозии. | Видимый дефект; предотвращает гладкую отделку поверхности. |
Коррозия (питтинг) | Уменьшает поперечное сечение, создавая очаги напряжения. | Указывает на сбой пассивного слоя; может ускориться. | Неприемлемы для использования в санитарных целях; плохой эстетический вид. |
Сенсибилизация | Внутреннее ослабление, риск внезапной поломки. | Высокая восприимчивость к межкристаллитной коррозии. | Скрытый дефект, но приводящий к видимой коррозии в процессе эксплуатации. |
Поверхностные трещины снижают усталостную прочностьПравда
Даже микроскопические трещины действуют как концентраторы напряжения, резко снижая количество циклов нагрузки, которые может выдержать проволока до разрушения.
Коррозия влияет только на внешний видЛожь
Коррозия активно ухудшает свойства материала, уменьшая площадь поперечного сечения и создавая напряжения, что существенно снижает механические характеристики.
Какие существуют решения для предотвращения поверхностных трещин при отжиге проволоки из нержавеющей стали?
Вы постоянно боретесь с поверхностными трещинами на проволоке из нержавеющей стали, что нарушает ваш производственный график? Решение заключается не в одной волшебной пуле, а в систематическом подходе к контролю термического напряжения и обеспечению чистоты материала на протяжении всего процесса яркого отжига, превращающего непредсказуемость в точность.
Для предотвращения поверхностных трещин осуществляйте точный тепловой контроль с постепенным, запрограммированным нагревом и быстрым, но контролируемым охлаждением, чтобы минимизировать тепловой удар. Обеспечьте высокую чистоту атмосферы печи (точка росы <-60°C) и тщательную очистку перед отжигом для удаления поверхностных загрязнений и смазочных материалов, которые могут вызвать охрупчивание.
Переход от борьбы с трещинами к их профилактике требует изменения мышления. Вы должны рассматривать свою линию отжига как прецизионный инструмент, а не просто нагреватель. Каждая зона, каждый ролик и каждая молекула газа играют свою роль в конечном качестве проволоки. За свою карьеру я видел, как компании повышали производительность, сосредоточившись на трех основных направлениях: управлении тепловым профилем, контроле атмосферы и подготовке материалов. Речь идет о том, чтобы взять под контроль переменные факторы до того, как они приведут к дефектам. Например, простое построение графика температурного профиля печи может выявить неравномерности, о которых вы даже не подозревали. Аналогично, установка анализатора точки росы в режиме реального времени может обеспечить раннее предупреждение, необходимое для предотвращения выпуска плохой партии. Речь идет не об усложнении, а об усилении контроля. Систематически решая эти задачи, вы создаете надежный по своей сути процесс, способный производить проволоку без трещин, катушка за катушкой, день за днем. Такая последовательность является основой высококачественного и прибыльного производства.
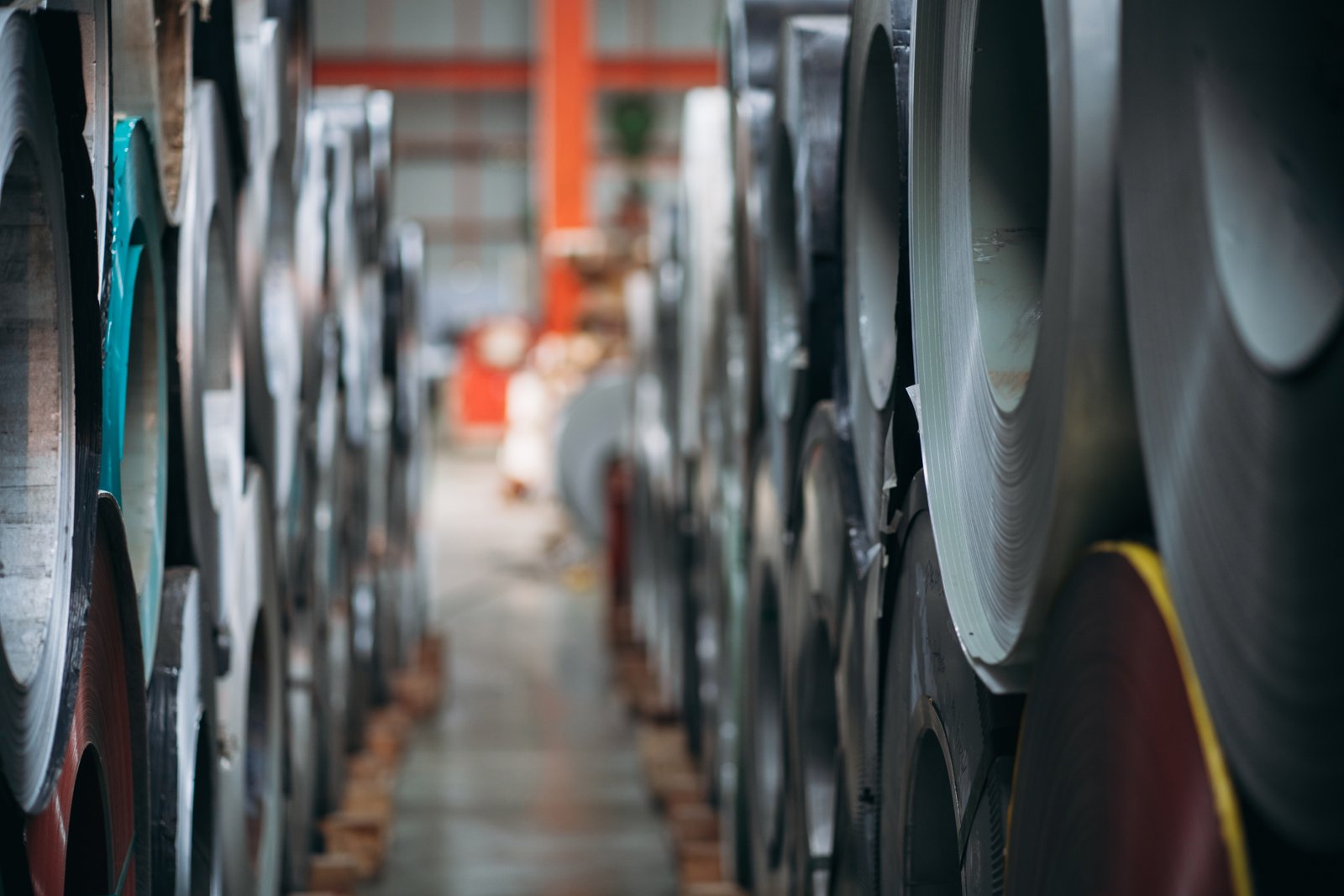
Комплексное решение проблемы поверхностного растрескивания основывается на тщательном контроле всей экосистемы отжига. Это многогранная стратегия, которая начинается еще до того, как проволока попадает в печь, и продолжается до конечной намотки. В компании AKS, когда мы проектируем печную линию, мы не просто продаем оборудование; мы разрабатываем технологическое решение с учетом конкретных требований клиента к материалу и качеству. Давайте рассмотрим три критические области, в которых необходимо установить контроль, чтобы гарантировать отсутствие трещин на поверхности блестящей отожженной проволоки из нержавеющей стали. Клиент, производящий проволоку с высоким удлинением для глубокой вытяжки, обнаружил, что только освоив все три области, он смог устранить тонкие поверхностные трещины, которые вызывали разрывы в штампах его клиентов.
Оптимизация тепловых профилей: Искусство управления стрессом
Прохождение проволоки через печь должно быть плавным тепловым переходом, а не серией толчков. Цель - минимизировать градиент температуры (ΔT) между поверхностью проволоки и ее сердцевиной в любой момент времени. Для этого требуется печь со сложным многозональное отопление и контролируемое охлаждение6 возможности. Вместо одной нагревательной камеры, работающей по принципу "грубой силы", современная печь имеет несколько независимо управляемых зон нагрева. Это позволяет запрограммировать темп нагрева, при котором проволока постепенно доводится до температуры отжига. Например, типичный профиль для нержавеющей стали 304 может включать повышение температуры отжига до 1050°C в течение 1-2 минут, выдержку в течение 30-60 секунд для обеспечения равномерной температуры по всему сечению, а затем начало процесса охлаждения.
Стадия охлаждения не менее, если не более, важна. Как уже говорилось, неконтролируемое быстрое охлаждение создает огромное поверхностное натяжение. Решением является сочетание радиационного и конвективного охлаждения в длинном закрытом муфеле. Начальная секция охлаждения позволяет проволоке контролируемо излучать тепло, прежде чем она попадет в конечную зону конвективного охлаждения с высокой скоростью. Наша усовершенствованная система охлаждения AKS использует направленные струи охлажденного, рециркулирующего защитного газа для быстрого и равномерного отвода тепла, обеспечивая быстрое прохождение проволоки через диапазон сенсибилизации (850-450°C) без создания теплового удара, вызывающего трещины.
Мы можем количественно оценить улучшение. В традиционной, плохо контролируемой печи равномерность температуры в зоне может составлять ±20°C. Этой разницы достаточно, чтобы создать различные скорости теплового расширения в пучке проволоки, вызывая напряжение. Наши прецизионные системы управления, использующие передовые алгоритмы ПИД-регулирования и высококачественные термопары, поддерживают равномерность температуры на уровне ±5°C и выше. Такой уровень контроля напрямую приводит к снижению внутреннего напряжения и значительному уменьшению частоты термического растрескивания.
Освоение атмосферы печи: Мандат чистоты
Защитная атмосфера не просто предотвращает окисление; ее чистота является прямым фактором, препятствующим охрупчиванию, которое приводит к растрескиванию. Два ключевых параметра - содержание кислорода и точка росы (содержание влаги). Кислород, даже в количестве частей на миллион (PPM), может вызвать селективное окисление хрома на границах зерен. Водяной пар еще более коварен, поскольку при высоких температурах он создает окислительный потенциал. Стандартом для высококачественного яркого отжига является точка росы -60°C или ниже, что соответствует всего 10 PPM водяного пара.
Для достижения такого уровня чистоты требуется два подхода: источник газа высокой чистоты и герметичная газонепроницаемая печь. Источник газа, будь то бутилированный чистый водород или диссоциатор аммиака на месте, должен хорошо обслуживаться. Но чаще всего проблема кроется в самой печи. Утечки воздуха через изношенные уплотнения, вводы термопар или на входе и выходе могут нарушить чистоту атмосферы. Именно поэтому мы изготавливаем муфели наших печей из высокопрочных сплавов, таких как 310S, и используем комбинацию графитовых канатных уплотнений и положительного контроля давления, чтобы обеспечить практически полное отсутствие утечек воздуха.
Я помню случай с компанией "WireTech Solutions", производителем медицинской проволоки. Они использовали печь, которой было более десяти лет, и испытывали проблемы с непостоянным качеством. Мы установили новую линию AKS с анализатором кислорода и точки росы в реальном времени, интегрированным в контур управления. Они обнаружили, что их атмосфера часто ухудшалась до точки росы -35°C из-за небольших утечек на выходном уплотнении. Благодаря новой системе, обеспечивающей постоянный мониторинг, и превосходной конструкции уплотнения, точка росы теперь стабильно поддерживается на уровне ниже -65°C. Коэффициент брака по трещинам снизился в среднем с 3% до менее чем 0,1%, что позволило окупить модернизацию печи менее чем за 18 месяцев только за счет снижения количества брака.
Целостность материалов до и после обработки
Печь не может устранить проблему, которая уже заложена в проволоке. Процесс предотвращения трещин начинается с того, что проволока, поступающая в печь, должна быть максимально чистой и без дефектов. Волочение - это агрессивный процесс, в результате которого проволока может иметь напряженную поверхность и покрываться смазкой. Многоступенчатая ультразвуковая система очистки и обезжиривания перед входом в печь имеет решающее значение. Она должна полностью удалить все составы для волочения, масла и мелкие частицы. Как уже упоминалось, остатки смазочных материалов могут разлагаться при высоких температурах и вступать в реакцию со стальной поверхностью, образуя хрупкие участки, которые становятся местами образования трещин.
Механическая обработка - еще один важнейший элемент. Система контроля натяжения проволоки должна быть точной. Чрезмерное натяжение приводит к растяжению проволоки, особенно когда она горячая и ее прочность на разрыв низкая. Этого механического напряжения, добавленного к неизбежному тепловому напряжению, может быть достаточно, чтобы перевести материал через точку разрыва. В современных линиях используются танцевальные рычаги или тензодатчики с обратной связью с приводными двигателями, поддерживающие натяжение проволоки на постоянном, низком уровне (например, менее 1-2% от предела текучести проволоки).
ли, также важна обработка после отжига. Проволока, выходящая из печи, идеально чистая и имеет высокоактивную поверхность. Она должна быть намотана на чистые шпули в чистой среде, чтобы избежать немедленного загрязнения свободным железом или другими источниками, которые впоследствии могут привести к коррозионному растрескиванию. Это цепочка качества, которая должна оставаться непрерывной от начала до конца.
Область решения | Ключевая технология/практика | Параметр управления | Целевое значение для предотвращения трещин |
---|---|---|---|
Тепловой контроль | Многозональное отопление с ПИД-регулятором, управляемое струйное охлаждение | Равномерность температуры / скорость охлаждения | ±5°C / Быстрое прохождение зоны 850-450°C |
Контроль атмосферы | Газонепроницаемая муфта, анализ газа в режиме реального времени | Точка росы / содержание O₂ | < -60°C / < 5 PPM |
Обработка материалов | Ультразвуковая очистка перед отжигом, регулировка натяжения барабана | Чистота поверхности / натяжение проволоки | Без органических остатков / <2% от предела текучести |
Постепенный нагрев предотвращает появление трещинПравда
Запрограммированные темпы нагрева минимизируют тепловой удар за счет снижения градиента температур между поверхностью и сердцевиной.
Более быстрое охлаждение всегда лучшеЛожь
Неконтролируемое быстрое охлаждение создает поверхностное натяжение - для оптимального охлаждения требуются ступенчатые радиационные/конвективные зоны.
Как лучше всего ухаживать за проволокой из нержавеющей стали, чтобы избежать коррозии?
Вы только что изготовили идеальную, яркую отожженную проволоку из нержавеющей стали. Как сделать так, чтобы она оставалась такой же? Правильный уход - это не просто забота, а важнейший заключительный шаг для сохранения коррозионной стойкости, которую вы так старательно создавали во время отжига.
Чтобы сохранить проволоку из нержавеющей стали и предотвратить коррозию, храните ее в чистом, сухом, мало влажном помещении, вдали от углеродистой стали. Для работы с проволокой используйте чистые неметаллические инструменты или инструменты только из нержавеющей стали. Для очистки используйте моющие средства, не содержащие хлоридов, и тщательно промывайте чистой водой, обеспечивая полное высыхание.
Как только проволока покидает контролируемую среду печи для отжига, она попадает в мир, полный коррозионных угроз. Пассивный слой, хотя и прочный, не является непроницаемым, и его защита требует сознательных усилий. Подумайте об этом, как об уходе за высокопроизводительным автомобилем: вы не оставите его без защиты. Тот же принцип применим и к высококачественной нержавеющей стали. Каждое взаимодействие с ней - от катушки, на которую она намотана, до инструментов, которые к ней прикасаются, и воздуха, в котором она хранится, - имеет значение. Я видел слишком много случаев, когда идеально изготовленная проволока была испорчена неправильной практикой после производства, например, хранением ее рядом со станцией для шлифовки углеродистой стали или упаковкой в загрязненную бумагу. Принятие передовых методов обработки, хранения и очистки необходимо для доставки проволоки заказчику в том же первозданном состоянии, в котором она была при выходе из вашей печи. Такая тщательность позволяет сохранить целостность материала и поддержать вашу репутацию производителя.
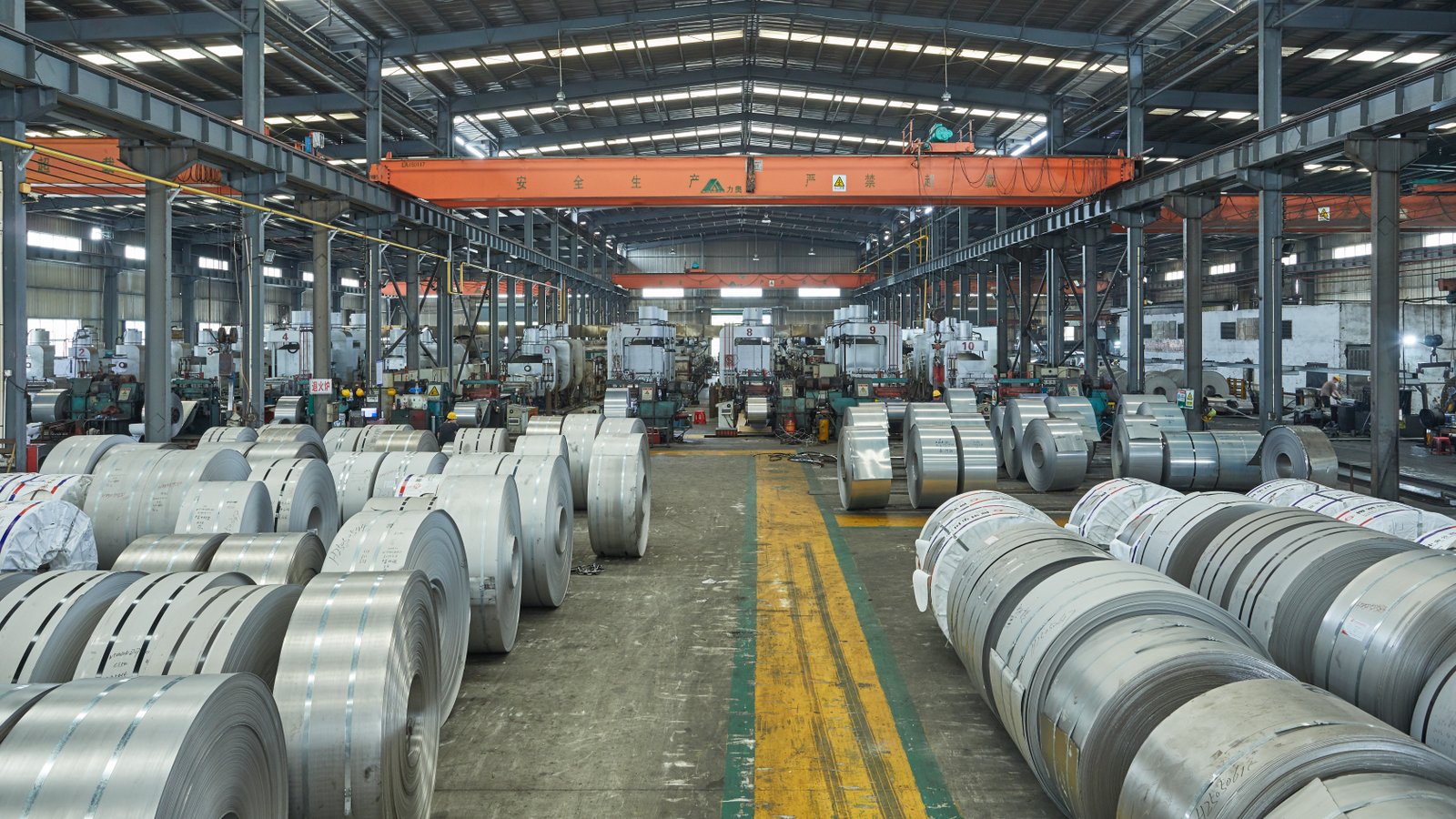
Поддержание антикоррозийного состояния блестящей отожженной проволоки из нержавеющей стали - это дисциплина предотвращения загрязнения и контроля окружающей среды. Пассивный слой оксида хрома - герой нашей истории, и все эти передовые методы направлены на его защиту. Неудача на этом заключительном этапе может свести на нет всю точную работу по выбору материала и термообработке. В компании AKS мы часто консультируем наших клиентов по поводу этих процедур после печи, поскольку знаем, что восприятие клиентом качества нашей печи напрямую связано с конечным состоянием получаемой им проволоки. Давайте рассмотрим три основных элемента обслуживания после отжига: правильное хранение и обращение, соответствующие протоколы очистки и обоснованный выбор материала в соответствии с условиями применения.
Золотые правила хранения и обработки
Самой распространенной причиной коррозии после производства является загрязнение "свободным железом". Именно поэтому правило номер один гласит: изолировать нержавеющую сталь от вся углеродистая сталь7. Это означает наличие специальных мест хранения, специального оборудования для обработки и даже специальных рабочих зон. Проволока из нержавеющей стали никогда не должна храниться в зоне, где ведется резка, шлифовка или сварка углеродистой стали, так как частицы воздуха оседают на поверхности и вызывают ржавчину. Инструменты, используемые для работы с нержавеющей сталью, такие как направляющие, ролики и режущие ножницы, должны быть либо сами изготовлены из нержавеющей стали, либо быть неметаллическими (например, нейлоновыми или из твердых пород дерева). Использование стальной проволочной щетки, которая ранее применялась для углеродистой стали, - гарантированный способ загрязнить поверхность.
Очень важна сама среда хранения. Она должна быть чистой, сухой и, в идеале, климатически контролируемой. Высокая влажность может ускорить коррозию, особенно если в атмосфере присутствуют следы загрязняющих веществ или хлоридов. Проволока должна храниться не на полу, на чистых поддонах. Однажды я посетил клиента, у которого на намотанной проволоке появились пятна ржавчины. Мы обнаружили, что на их складе протекает крыша, и за ночь конденсат капал на катушки, обеспечивая электролит, необходимый для начала коррозии на микроскопических частицах пыли.
Упаковка также играет важную роль. Проволока должна быть завернута в чистую, не содержащую хлоридов бумагу или пластик. Некоторые виды бумаги содержат кислотные или хлоридные остатки, которые со временем могут разрушить поверхность. Использование бумаги с паровым ингибитором коррозии (VCI) может обеспечить дополнительный уровень защиты, особенно при длительном хранении или транспортировке через морскую среду. Это небольшое вложение, которое может сэкономить много денег и головной боли.
Правильные процедуры очистки и пассивации
Даже при самом лучшем обращении с проволокой в какой-то момент может потребоваться ее очистка. Главное правило - быть осторожным и избегать хлоридов. Для общей очистки от пыли или отпечатков пальцев достаточно мягкой ткани с мягким моющим средством, не содержащим хлоридов, и теплой воды. После мытья обязательно тщательно промойте проволоку чистой водой (идеально подходит деионизированная вода), чтобы удалить все следы чистящего средства. ли, проволоке необходимо дать полностью высохнуть. Застоявшаяся вода является питательной средой для щелевой коррозии.
Для более стойких загрязнений или в качестве завершающего этапа, гарантирующего максимальную коррозионную стойкость, используется процесс, называемый пассивация8 может быть выполнена. Важно отличать пассивацию от травления. При травлении используются сильные кислоты, такие как фтористоводородная или азотная, для удаления накипи, в то время как при пассивации используется более мягкая кислотная ванна, обычно азотная или лимонная кислота. Цель пассивации - не травление поверхности, а химическое удаление свободного железа и других загрязнений, а также укрепление и утолщение естественного пассивного слоя оксида хрома. Стандарт ASTM A967 регламентирует этот процесс.
Однако пассивация должна быть выполнена правильно. Концентрация кислоты, температура и время погружения должны тщательно контролироваться в зависимости от марки нержавеющей стали. Неправильная пассивация может повредить поверхность. Я всегда рекомендую, чтобы при необходимости пассивации ее выполнял квалифицированный специалист или после тщательного изучения соответствующих стандартов. Для большинства применений проволока, которая была правильно отожжена и содержалась в чистоте, не требует последующего пассивирования.
Обучение конечного пользователя и выбор материала
ли, важнейшей передовой практикой является общение. Производителю проволоки крайне важно понимать назначение конечного пользователя и обучать его правильному обслуживанию. Если проволока предназначена для морской среды, архитектурных сооружений вблизи побережья или предприятий пищевой промышленности, использующих хлоридные дезинфектанты, стандартной марки 304 может оказаться недостаточно. В таких случаях рекомендуется рекомендовать более прочный сплав, например 316 (с молибденом для устойчивости к точечной коррозии) или дуплексную нержавеющую сталь.
Предоставление клиентам простого руководства по обращению и чистке может предотвратить множество проблем. Оно может включать в себя такую информацию, как:
- "Не используйте стальную вату или щетки из углеродистой стали для этой проволоки".
- "Очистите мягким мылом и водой, тщательно промойте и высушите".
- "Избегайте контакта с хлорсодержащими чистящими средствами, солями и кислотами".
Такое проактивное общение демонстрирует вашу компетентность и приверженность качеству не только на этапе продажи. Это помогает гарантировать, что конечный продукт будет работать так, как ожидалось, что хорошо отразится как на изготовителе, так и на вас, производителе проволоки. У хорошо информированного клиента меньше шансов столкнуться с неудачей и ошибочно обвинить качество материала. Этот заключительный этап замыкает цикл, гарантируя, что целостность, так тщательно культивируемая в печи отжига, сохранится на протяжении всего жизненного цикла продукта.
Практика | Цель | Ключевые действия | Распространенные ошибки, которых следует избегать |
---|---|---|---|
Хранение и обработка | Предотвращение загрязнения свободным железом | Используйте нержавеющие/неметаллические инструменты, храните в сухом/чистом месте | Использование инструментов из углеродистой стали, хранение вблизи шлифовальных работ |
Очистка | Удаление загрязнений без повреждения пассивного слоя | Используйте моющие средства, не содержащие хлоридов, тщательно промойте, полностью высушите. | Использование стальной ваты, хлорного отбеливателя или чистящих средств на основе кислот |
Пассивация | Укрепление пассивного слоя и удаление загрязнений | Следуйте стандарту ASTM A967, используйте ванны с азотной или лимонной кислотой. | Использование неправильной концентрации кислоты или времени, путаница с маринованием |
Обучение клиентов | Обеспечьте правильное применение и обслуживание | Предоставьте руководства по обращению, порекомендуйте подходящий сплав | Предполагается, что конечный пользователь знает, как обращаться с нержавеющей сталью |
Нержавеющая сталь нуждается в изоляции от углеродистой сталиПравда
Загрязнение свободным железом из углеродистой стали является наиболее распространенной причиной послепроизводственной коррозии проволоки из нержавеющей стали.
Пассивация удаляет поверхностную окалинуЛожь
Пассивация укрепляет слой оксида хрома и удаляет загрязнения, а травление (не пассивация) удаляет накипь с помощью более сильных кислот.
Заключение
В конечном итоге предотвращение трещин и коррозии в проволоке из нержавеющей стали зависит от точности управления. Оптимизируя термические профили, обеспечивая атмосферную чистоту в печи для отжига и соблюдая строгие протоколы обработки, вы обеспечиваете целостность поверхности проволоки и ее микроструктуры, что позволяет добиться максимальных эксплуатационных характеристик.
-
Изучите преимущества отжига для повышения коррозионной стойкости и улучшения качества поверхности ↩
-
Понять технологию промышленных печей для оптимизации процесса отжига ↩
-
Поймите, как яркий отжиг помогает реформировать пассивный слой. ↩
-
Узнайте, как определяется сенсибилизация и как она влияет на целостность металла. ↩
-
Понять принципы концентрации напряжений вокруг трещин. ↩
-
Понять роль многозонального отопления в контроле теплового стресса ↩
-
Узнайте, почему изоляция нержавеющей стали от углеродистой предотвращает появление ржавчины и ухудшение качества ↩
-
Понять процесс пассивации и его роль в предотвращении коррозии нержавеющей стали ↩