Как управление печью с помощью искусственного интеллекта позволяет достичь нулевого окисления при отжиге нержавеющей стали 4.0?
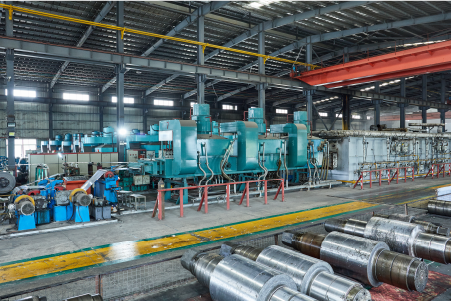
Striving for a flawless, zero-oxidation finish on stainless steel can feel like a constant battle against invisible enemies. The slightest deviation in furnace atmosphere or temperature can lead to microscopic oxidation, resulting in costly rejections, wasted energy, and a loss of your customer's trust and confidence. This challenge is a daily reality in metal processing. But what if your furnace could think for itself? This is the promise of Stainless Steel 4.01, where AI-powered control turns the art of annealing into a precise science, delivering a perfect, mirror-bright finish on every coil, every single time.
Bright Annealing Stainless Steel 4.0 represents the complete integration of intelligent technologies, like Artificial Intelligence and the Internet of Things (IoT), into the heat treatment process. Its significance is rooted in achieving unprecedented levels of precision, consistency, and energy efficiency, enabling manufacturers to produce defect-free, high-value materials.
The idea of an "intelligent furnace" might have sounded like science fiction a decade ago, but at AKS Furnace, we are deploying this technology today. For years, the industry has relied on the invaluable experience of operators and the rigidity of static PLC setpoints. But what happens when the operator changes, or the atmospheric conditions shift? We believe the future lies in furnaces that can think, predict, and adapt in real time. This is the core promise of AI in bright annealing, transitioning us from making reactive adjustments to implementing proactive, predictive control.
This evolution from traditional automation to true Industry 4.02 is not just about adding a new feature; it’s about fundamentally creating a cyber-physical system where the furnace becomes a living, learning entity. A standard PLC is excellent at executing pre-programmed commands, but it doesn’t learn from previous cycles. AI, in contrast, continuously analyzes immense datasets—gas flow rates, dew point measurements, temperature curves, strip speed—to identify subtle patterns and correlations that are completely invisible to the human eye. Research from leading institutes has demonstrated that AI-driven process control can slash energy consumption by over 15% while simultaneously boosting product quality. This isn't just about preventing a bit of surface oxidation; it’s about meticulously optimizing the entire value chain, challenging us to move beyond fixed recipes toward dynamic, self-optimizing systems that guarantee quality.
AI prevents surface oxidationПравда
AI-powered control systems can predict and prevent microscopic oxidation by dynamically adjusting furnace conditions in real-time.
PLC systems learn from experienceЛожь
Traditional PLCs follow fixed recipes and cannot learn or adapt like AI systems, which continuously improve through machine learning.
How is AI revolutionizing furnace control in the bright annealing process?
Problem: Even the most skilled and experienced furnace operator cannot possibly monitor and react to dozens of interacting variables every single second, 24/7. This fundamental human limitation leaves the door wide open for subtle process deviations that can compromise the perfect, bright finish. Agitate: Think of the immense frustration of chasing the "perfect" settings, only to have them rendered ineffective by a change in the weather, a new batch of protective gas, or slight variations in the steel coil itself. Solution: AI steps in to perform this monumental task, providing vigilant, intelligent oversight around the clock. It acts as the ultimate super-operator, making microscopic adjustments with a speed and precision that is simply beyond human capability.
AI is fundamentally revolutionizing furnace control by transforming the operational philosophy from a reactive to a predictive model. It leverages machine learning algorithms to analyze a continuous stream of real-time sensor data, allowing it to dynamically and proactively adjust critical parameters like temperature and gas atmosphere.
The shift towards AI control isn't about replacing our valued, skilled operators; it's about empowering them with a tool of unprecedented capability. At AKS Furnace, we view AI as a collaborative partner on the factory floor. An experienced operator can set the strategic goals for a production run—defining the desired metallurgical properties and surface finish—while the AI handles the complex, second-by-second tactical execution required to flawlessly achieve that goal. This synergy is where the real power lies. A compelling example comes from a large-scale stainless steel strip processor we work with in India. They were facing a persistent challenge with maintaining consistent quality across different shifts. The "feel" for the furnace varied from one operator to another, leading to unacceptable variations in the final product. By integrating our AI control module into their existing line, we helped them standardize the entire process. The AI learned by modeling the actions of their most skilled operator, effectively capturing that "golden touch" and making it the unvarying standard for every single run. This eliminated human variability and ensured uniform, high-quality output, day and night.
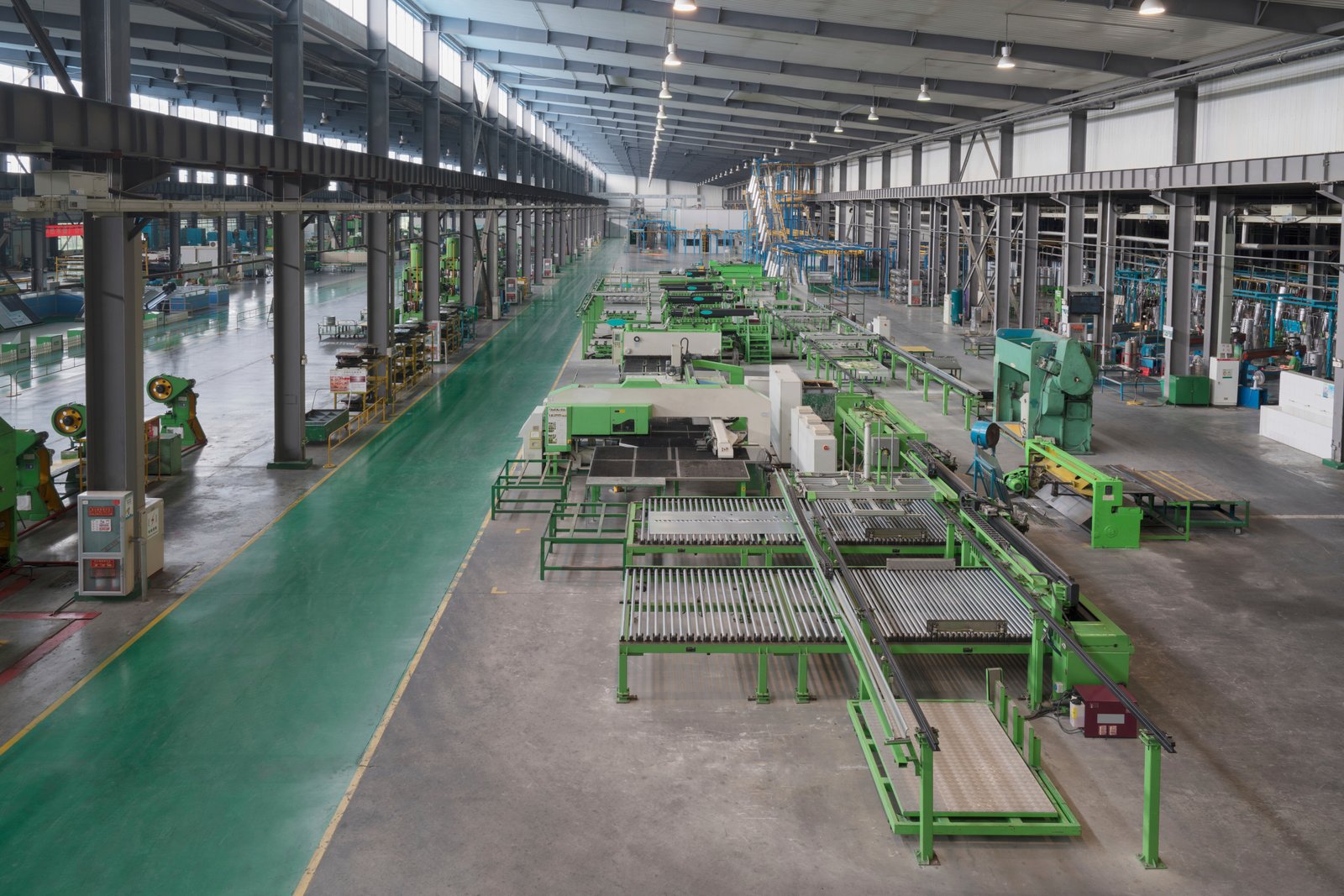
The practical magic of AI is its ability to democratize expertise and elevate the quality baseline for the entire operation. It turns the art of annealing into a data-driven science, accessible to all. The implications of this are vast, touching every aspect of production. For instance, AI can analyze historical data to identify that a specific grade of steel from a particular supplier requires a slightly different thermal profile to achieve optimal brightness, an insight that might take an operator months to discover through trial and error. This level of granular optimization was previously unattainable. It allows for a more agile and responsive manufacturing process, one that can adapt to changing inputs without sacrificing quality. This revolution is not in the distant future; it's happening now, and it's redefining the standards of excellence in bright annealing.
Predictive Atmosphere Management: The End of Guesswork
The single most critical factor in achieving a zero-oxidation finish is the furnace atmosphere. It must be highly reducing, meaning it is devoid of oxygen and other oxidizing agents like water vapor (H₂O). The key parameters are the hydrogen-to-nitrogen ratio (H₂/N₂) and, most importantly, the dew point, which is a direct measure of moisture content. Traditionally, operators would set a fixed flow rate for the protective gases and perform periodic manual checks of the dew point. This method is fraught with risk. An air leak, a dip in gas purity, or moisture carried in by the steel strip can quickly elevate the dew point, leading to oxidation.
AI transforms atmosphere management from guesswork into a precise, predictive science. It uses a network of high-sensitivity sensors, including zirconia oxygen probes and in-line dew point meters, to create a dynamic, real-time model of the furnace atmosphere from the entry seal to the exit. The AI doesn't just react to a high dew point reading; it predicts it. It understands that an increase in line speed means the strip will carry more ambient air into the furnace, and it will proactively increase the nitrogen purge at the entry vestibule moments до the speed change occurs. This anticipatory action ensures the internal atmosphere remains perfectly stable and protective at all times.
A clear example of this is a customer of ours who manufactures high-precision electronic connectors. The subsequent plating process required an absolutely pristine, oxide-free stainless steel surface. They were experiencing sporadic plating failures that were eventually traced back to micro-oxidation, invisible to the naked eye. After we integrated our AI control system, the AI model quickly learned the direct correlation between the ambient humidity in their factory (which fluctuated throughout the day) and the precise amount of protective gas needed to maintain the target dew point of -60°C inside the furnace. The system now adjusts the gas flow automatically and continuously, completely eliminating the micro-oxidation problem and reducing their downstream reject rate by over 90%.
Dynamic Thermal Profiling for Metallurgical Perfection
A thermal profile is the precise temperature curve that a steel strip experiences as it travels through the heating and cooling sections of the furnace. A "one-size-fits-all" approach, where the same heating setpoints are used for different products, is fundamentally suboptimal. Different steel grades (e.g., 304 vs. 430), and variations in strip thickness and width, all require unique thermal profiles to achieve the desired metallurgical properties without risking overheating or under-annealing. This complexity often forces operators to use "safe," conservative settings that consume more energy and may not produce the best possible quality.
AI enables the creation of fully dynamic thermal profiles in real-time. Before a coil even enters the furnace, the AI can receive its specifications (grade, dimensions) from the plant's ERP or scheduling system. It then calculates the theoretically perfect heating and cooling curve for that specific product. As the strip travels through the furnace, the AI continuously monitors its actual temperature using an array of non-contact pyrometers. It then dynamically adjusts the power to individual heating zones and modulates the speed of cooling fans to ensure every segment of the steel strip precisely follows the ideal curve. If there's a momentary slowdown in the line, the AI will instantly reduce power to prevent overheating.
This level of control delivers benefits that go far beyond just a bright surface. It ensures unparalleled consistency in the steel's final metallurgical state—its grain structure, tensile strength, and ductility. We have an automotive parts client who was experiencing intermittent issues with tearing during their deep-drawing stamping process. The root cause was inconsistent mechanical properties from their old annealing line. After switching to an AKS furnace with our AI thermal profiling, the problem vanished. The superior metallurgical consistency of the annealed steel resulted in a more stable and predictable forming process, directly increasing their press shop's uptime and yield.
Параметр управления | Traditional PLC Control | AI-Driven Control |
---|---|---|
Heating Zone Temp. | Fixed setpoints based on a static recipe | Dynamically adjusted based on strip mass, grade, and speed |
Скорость охлаждения | Pre-set fan speeds or damper positions | Modulated in real-time to achieve target exit temperature |
Atmosphere Flow | Constant flow rate for the entire recipe | Adjusted based on real-time dew point and O₂ analysis |
Response to Disturbance | Reactive, based on triggered alarms or operator notice | Proactive, predicts and mitigates disturbances before they occur |
Energy Usage | Sub-optimal, often based on worst-case scenarios | Highly optimized, matches energy input to real-time process need |
The Power of Predictive Maintenance and Self-Diagnostics
In a high-throughput manufacturing environment, unplanned downtime is the ultimate enemy. A furnace failure can bring an entire production facility to a grinding halt, causing massive financial losses and disrupting delivery schedules. The traditional approach to maintenance is either reactive (fixing something after it breaks) or based on a fixed schedule (replacing parts whether they need it or not), both of which are highly inefficient.
AI introduces a paradigm shift to predictive maintenance (PdM). The same sensors that monitor the annealing process also monitor the health of the furnace itself. The AI analyzes vibration signatures from cooling fans, monitors the electrical current draw of each individual heating element, and tracks pressure drops across filters in the gas lines. It learns the normal operating signature of every component. When it detects a subtle deviation—for example, a fan's vibration pattern changing slightly, indicating a bearing is beginning to wear—it flags it for maintenance long before it becomes a critical failure.
This capability transforms the entire maintenance workflow. Instead of a catastrophic failure causing an emergency shutdown, our AKS 4.0 system can automatically generate a detailed work order in the plant's maintenance software weeks in advance. The alert will specify the exact component that needs attention, diagnose the likely issue, and even suggest the required spare parts. This allows maintenance to be scheduled during planned downtime, maximizing uptime and reducing costs. A major European client using our AI-powered bogie hearth furnace reported a 30% reduction in their annual maintenance budget and, more importantly, a near-total elimination of unplanned downtime in their first year of operation, validating the immense ROI of this intelligent feature.
AI enables predictive furnace controlПравда
AI analyzes real-time data to proactively adjust parameters like temperature and gas atmosphere before deviations occur.
AI replaces human operators entirelyЛожь
AI collaborates with operators by handling tactical execution while humans set strategic goals.
What challenges are faced in achieving zero oxidation in stainless steel?
Problem: Achieving a truly perfect, zero-oxidation surface on stainless steel is incredibly difficult because the process is highly sensitive to a multitude of interacting variables. Agitate: Tiny, unseen issues like a microscopic air leak, a slight impurity in the protective gas, or residual moisture on the strip can create costly surface defects, turning a high-value coil into scrap. Solution: The key is to gain precise, real-time control over the furnace's internal environment, especially the protective atmosphere, to proactively counteract these threats before they can cause damage.
The primary challenges in achieving zero oxidation are maintaining an extremely low dew point (moisture content) and eliminating any trace oxygen within the furnace atmosphere. These conditions are constantly threatened by external factors like air leaks, gas impurities, and strip surface contaminants, requiring vigilant, real-time control.
Over my years at AKS Furnace, I've seen clients struggle with the same elusive enemies of a perfect bright finish. The challenge is that you are fighting an invisible chemical reaction. The chromium in stainless steel has a very high affinity for oxygen, especially at annealing temperatures. Even a few parts-per-million of oxygen or a dew point that creeps up from -60°C to -40°C is enough to form a thin, dulling oxide layer. The sources of these contaminants are numerous. It could be a worn-out door seal, a batch of nitrogen gas with impurities[^3], or even lubricants from a previous rolling stage that haven't been fully cleaned off the strip. A traditional furnace, relying on static settings, is blind to these sudden changes. An operator might only notice the problem after an entire coil has been processed with a sub-par finish. This reactive loop of producing, inspecting, and then adjusting is inherently wasteful and is precisely the problem that modern furnace technology must solve to meet today's quality demands.
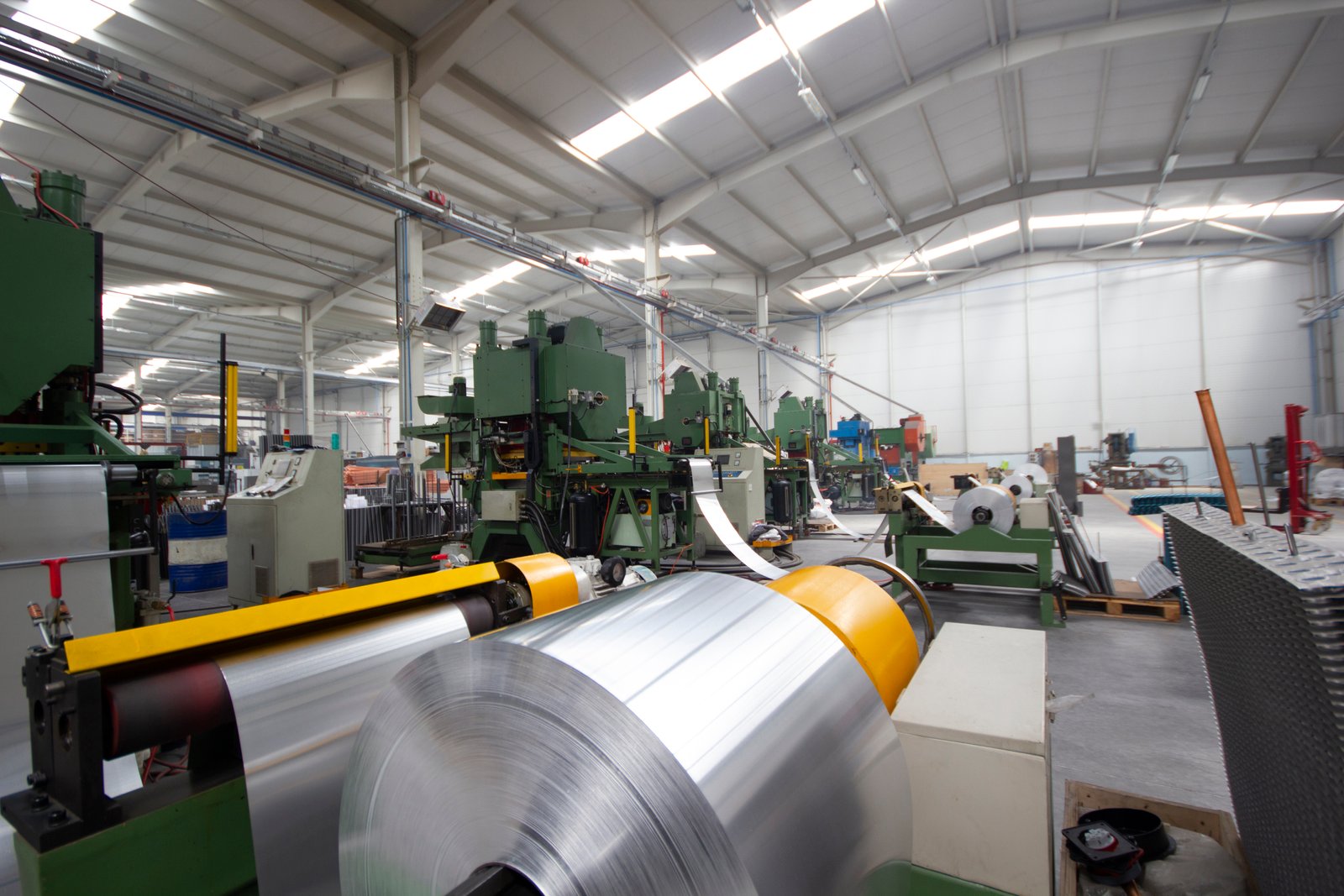
The complexity deepens when you consider the dynamic nature of a continuous annealing line. The very act of introducing the steel strip into the furnace is a source of contamination, as it drags in ambient air. The faster the line speed, the greater this challenge becomes. Furthermore, the outgassing of volatile compounds from the steel surface itself as it heats up can alter the delicate chemical balance of the protective atmosphere. To combat this, furnaces are designed with multiple zones, seals, and purging systems, but orchestrating all these elements perfectly has traditionally been more of an art form. The fundamental difficulty lies in managing a dynamic process with static tools. It’s like trying to navigate a winding road with your steering wheel locked in a fixed position. To truly achieve zero oxidation consistently, you need a system that can see the curves ahead and make constant, subtle adjustments.
The Intricacies of Atmospheric Integrity
The core of the challenge lies in maintaining the integrity of the protective atmosphere, which is typically a blend of nitrogen (N₂) and hydrogen (H₂). Nitrogen is inert, serving primarily to displace air, while hydrogen is the active reducing agent. Hydrogen actively seeks out and combines with any free oxygen (O₂) atoms to form water vapor (H₂O), which is then purged from the furnace. For this reaction to be effective, the atmosphere must be pristine. The target is often a dew point of -60°C or lower, which corresponds to a moisture content of only a few parts per million.
Achieving this level of purity is a constant battle. The most common point of failure is atmospheric leakage. In a large industrial furnace, which can be over 50 meters long, there are numerous potential leak points: entry and exit seals, sensor ports, and flanges. Even a tiny, pinhole-sized leak can allow enough oxygen to enter to compromise the entire atmosphere, creating a dull or discolored strip. Identifying the source of such a small leak in a conventional furnace can be a time-consuming and frustrating process of trial and error, often involving costly downtime.
Furthermore, the materials themselves introduce contaminants. The steel strip, arriving from the rolling mill, can have a thin layer of residual rolling oils or cleaning agents on its surface. As the strip heats up in the furnace, these compounds vaporize, a process known as outgassing. These vaporized hydrocarbons can break down and react with the protective atmosphere, consuming hydrogen and potentially creating carbon soot on the strip surface if not managed correctly. This means the demand for protective gas is not constant; it changes based on the cleanliness of the strip being processed. A fixed-flow gas system cannot adapt to this variability.
Thermal Management and Its Impact on Oxidation
While atmosphere is key, temperature control is inextricably linked to the oxidation challenge. The rate of oxidation is highly dependent on temperature. For stainless steel, there is a critical temperature window where it is most susceptible to oxidation. If the strip is heated too slowly or held in this critical window for too long, oxidation can occur even in a relatively good atmosphere. Conversely, overheating can not only damage the metallurgical structure but also accelerate any potential reactions with trace contaminants in the furnace.
The challenge is to heat the strip as rapidly as possible to the target annealing temperature, hold it there for the precise duration needed for recrystallization, and then cool it quickly and in a controlled manner. In a continuous furnace, this is complicated by variations in the product. A thicker, wider strip requires significantly more energy to heat up than a thinner one. If the furnace's heating system is not responsive enough, the thicker strip will move through the heating zone before it has reached the proper temperature, resulting in incomplete annealing. Operators might compensate by running the line slower, which hurts productivity, or by increasing setpoint temperatures, which wastes energy and increases the risk of overheating thinner-gauge products.
Moreover, the cooling process is just as critical. The strip must be cooled below its oxidation temperature before it exits the furnace and comes into contact with ambient air. Inefficient or non-uniform cooling, often caused by poor airflow dynamics in the cooling section, can lead to "hot spots" on the strip. These hot spots will instantly oxidize the moment they are exposed to air, creating unacceptable surface defects. Achieving a perfectly uniform thermal profile—both in heating and cooling—across the entire width and length of the strip is a major engineering challenge that requires sophisticated control.
Challenge Category | Specific Problem | Impact on Bright Finish |
---|---|---|
Atmospheric Control | Air leaks at seals/flanges | Introduces O₂, causing direct oxidation and surface dullness. |
High dew point (moisture) | Acts as an oxidizing agent, creating a chromium oxide layer. | |
Impurities in protective gas | Unwanted reactions can consume H₂ and reduce protective capacity. | |
Material Contamination | Residual rolling oils on strip | Outgassing consumes H₂ and can cause soot deposits. |
Surface moisture on strip | Directly increases the dew point inside the furnace. | |
Thermal Management | Non-uniform heating | Inconsistent annealing and potential for localized oxidation. |
Improper cooling rate | If strip exits too hot, it will immediately oxidize in air. | |
Incorrect thermal profile | Can leave steel in a vulnerable temperature range for too long. |
The Human Factor and Process Variability
Ultimately, in a traditional furnace operation, the system's final line of defense is the human operator. While experienced operators are incredibly valuable, this reliance introduces inherent variability. Different operators may have different philosophies on how to run the furnace. One might prefer a higher gas flow rate "just to be safe," which wastes expensive hydrogen, while another might run closer to the edge to save costs, increasing risk. This inconsistency can lead to puzzling variations in quality from shift to shift.
This "human factor" becomes a significant challenge when manufacturers are trying to meet the exacting standards of SPC (Statistical Process Control) demanded by top-tier customers like automotive giants. These customers require predictable, repeatable processes with quantifiable results. An operation that relies heavily on the subjective "art" and "feel" of an operator struggles to provide this level of data-backed quality assurance.
Furthermore, training new operators to handle the complexities of a bright annealing line is a long and expensive process. There is a constant risk that valuable process knowledge is lost when an experienced operator retires or leaves the company. The challenge, therefore, is not to eliminate the human operator, but to codify the best practices and institutionalize process knowledge into a system that is not dependent on any single individual. The goal is to create a process that is robust, repeatable, and consistently excellent, regardless of who is supervising the line.
Hydrogen reduces oxygen in furnaceПравда
Hydrogen actively combines with free oxygen to form water vapor, which is then purged from the furnace atmosphere.
Static settings prevent oxidationЛожь
Fixed furnace settings cannot adapt to dynamic contamination sources, making real-time atmosphere control essential for zero oxidation.
How can AI-driven solutions overcome these oxidation challenges?
Problem: The complex, interacting variables that lead to oxidation—like micro-leaks, gas impurities, and thermal fluctuations—are impossible for a human operator to manage perfectly in real time. Agitate: This leaves production vulnerable to random defects and inconsistent quality, forcing companies to rely on wasteful, high-consumption "safe" settings or risk producing scrap. Solution: AI-driven solutions provide a powerful answer by using predictive analytics and real-time sensor feedback to anticipate and neutralize threats to the furnace atmosphere and thermal profile before they can cause oxidation.
AI-driven solutions overcome oxidation challenges by transforming furnace control from a reactive to a predictive system. By continuously analyzing real-time data from sensors for dew point, oxygen, and temperature, AI can make proactive micro-adjustments to gas flow and heating elements to maintain a perfect anti-oxidation environment.
At AKS Furnace, we have seen firsthand how implementing an AI layer on top of a well-engineered furnace completely changes the game. It directly tackles the core challenges of atmospheric integrity[^4] and thermal management with a level of precision that was previously unattainable. Instead of discovering a quality issue after the fact, the AI prevents it from ever happening. For example, if a tiny air leak develops at an entry seal, the AI will immediately detect the resulting subtle change in the oxygen and dew point readings downstream. It won't just sound an alarm; it will instantly and automatically increase the protective gas flow just enough to compensate and maintain the required reducing atmosphere, while simultaneously notifying maintenance of the exact location of the issue. This ability to see, understand, and act in milliseconds is what enables a near-perfect success rate in preventing oxidation. It’s about creating a furnace with a built-in immune system.
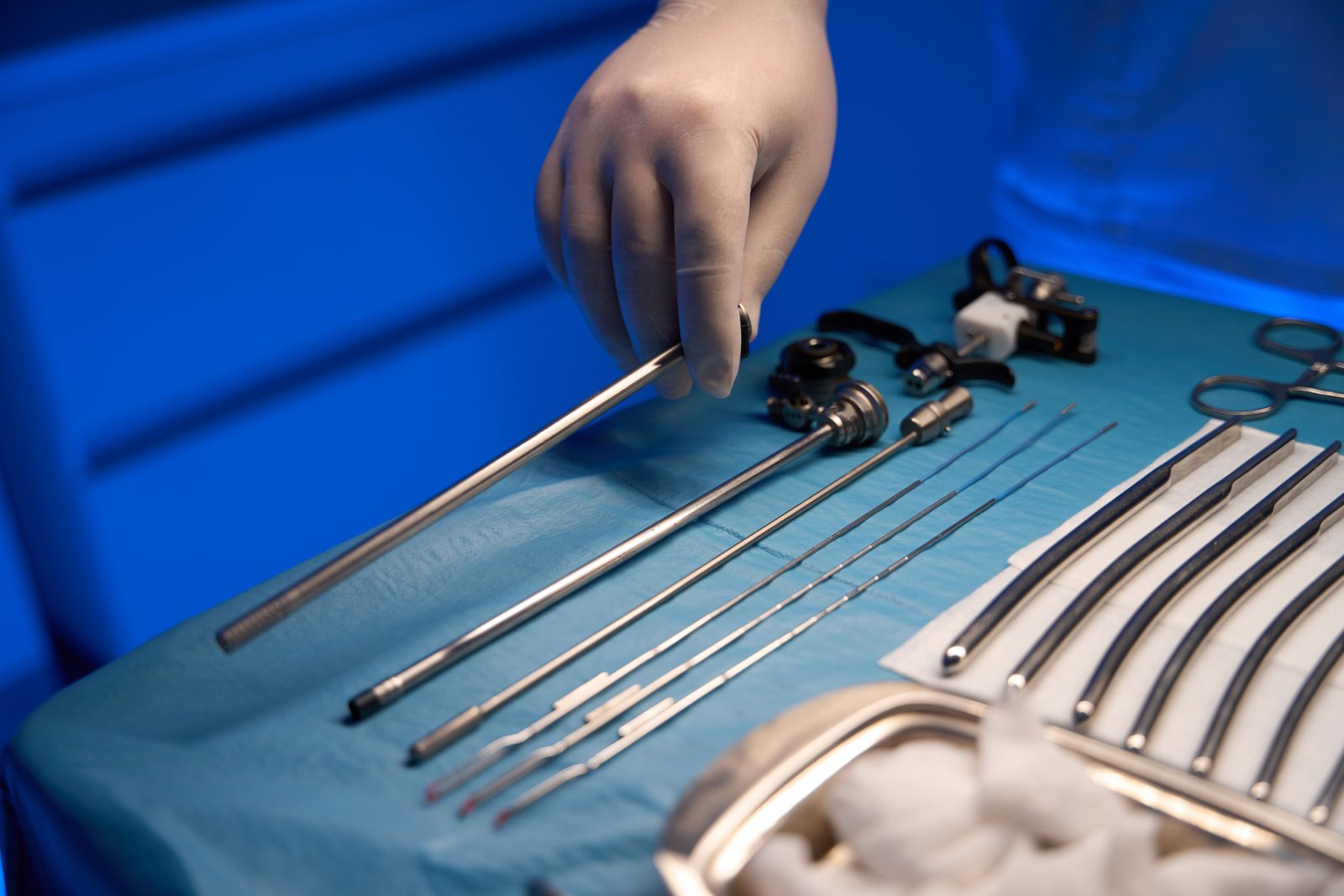
This intelligent, self-correcting capability extends to every aspect of the process. We had a client who processes various grades and gauges of stainless steel for architectural panels, where surface consistency is critical. Their old system[^5] required extensive manual adjustments and recipe changes between product runs, leading to significant downtime and material waste during transition periods. Our AI-driven solution automated this entirely. The AI uses a "digital twin"—a virtual model of the furnace—to simulate the upcoming run based on the new material's properties. It then automatically executes a new control strategy, perfectly synchronizing changes in line speed, temperature, and atmosphere. The result was a dramatic reduction in transition scrap and a significant boost in overall equipment effectiveness (OEE). This is the power of AI: it turns complex challenges into solved problems, delivering consistent, high-quality results run after run.
Creating a Self-Healing Atmosphere
The most significant way AI overcomes oxidation challenges is by creating what we call a "self-healing" atmosphere. A traditional furnace is brittle; a disturbance like an air leak can "break" the process. An AI-controlled furnace is resilient; it can absorb disturbances and maintain stability. This is achieved through a high-speed, closed-loop control system that is constantly working to maintain equilibrium. The AI's algorithm has a single primary objective: keep the dew point and oxygen levels below the critical threshold for oxidation at all times.
To do this, it continuously monitors a network of sensors. If the dew point at the exit of the cooling section begins to rise even slightly, the AI instantly assesses the situation. It cross-references data from sensors at the furnace entry, in the heating zones, and from the gas supply line. Is the incoming gas purity stable? Did the line speed just increase? Is the strip surface moisture higher than usual? Based on its analysis of these inputs and its historical data model, it determines the most effective countermeasure. It might increase the hydrogen content to boost the reducing potential, or it might increase the overall nitrogen flow to more effectively purge the contaminants.
This isn't a simple "if-then" logic; it's a sophisticated, multi-variable control strategy. For example, a client in the Middle East faced challenges with large fluctuations in ambient humidity between day and night. Their previous PLC-based system couldn't adapt, leading to inconsistent finishes. Our AI solution now monitors external weather data and proactively adjusts the furnace's atmospheric controls. It anticipates that at 8 PM, as humidity rises, the load on the entry vestibule's purge system will increase, and it adjusts accordingly до the dew point inside the furnace is affected. This proactive stance is the key to its success.
Precision Thermal Control for Defect Prevention
AI provides a similar level of sophisticated control over the furnace's thermal profile. As discussed, improper heating or cooling is a major contributor to oxidation defects. AI-driven systems replace static temperature setpoints with a dynamic, model-based control strategy. The AI understands the thermal physics of the furnace and the specific heat capacity of the steel being processed. Its goal is to ensure every square centimeter of the strip follows the ideal time-temperature path.
Imagine a scenario where the thickness of the steel strip varies slightly along its length—a common issue from the rolling process. A traditional furnace, with its fixed heating power, would under-anneal the thicker sections and potentially overheat the thinner sections. Our AI system, using real-time data from thickness gauges and pyrometers, anticipates these changes. As a thicker section enters a heating zone, the AI will momentarily boost the power to that specific zone to ensure it gets up to temperature correctly. As the section passes, it reduces the power back to the baseline. This happens automatically and continuously, ensuring perfect metallurgical consistency.
This same precision applies to the cooling section. A common defect, "strip-edge oxidation," occurs when the edges of the strip cool slower than the center and are still hot when they exit the furnace. The AI mitigates this by controlling an array of cooling jets or dampers across the strip width. If it detects that the edges are hotter than the center, it will increase the cooling flow specifically to the edges, ensuring the entire strip is at a uniform, safe temperature before it sees oxygen. This level of granular control virtually eliminates a whole class of common thermal defects.
Problem Source | Traditional Furnace Response | AI-Driven Solution |
---|---|---|
Small Air Leak | Alarm sounds after O₂ level is critical; manual search for leak. | Instantly detects O₂/dew point change, compensates with gas flow, logs alert. |
Inconsistent Strip Cleanliness | Operator may not notice; risk of soot or oxidation from outgassing. | Senses higher gas consumption, adjusts flow to handle contaminants. |
Varying Strip Thickness | Inconsistent annealing; operator may slow line speed reactively. | Proactively adjusts heating zone power based on thickness gauge data. |
Ambient Humidity Change | Dew point drifts; operator must manually adjust gas settings. | Predicts impact from weather data, pre-emptively adjusts purge rates. |
Product Changeover | Significant downtime for manual recipe change and stabilization. | Automatically loads optimized recipe, minimizing transition time and scrap. |
From Operator Dependence to Data-Driven Assurance
Perhaps the most profound way AI solves the oxidation challenge is by shifting the basis of quality from operator dependence to data-driven assurance. It captures the knowledge of the best operators and the fundamental physics of the process into a repeatable, verifiable system. This provides manufacturers with an unprecedented level of process transparency and proof of quality. For every coil of steel produced, our system can generate a "birth certificate" of data, showing the exact thermal profile and atmospheric conditions it experienced from start to finish.
This is a powerful tool for quality assurance and customer trust. If a customer ever has a question about a specific coil, the manufacturer can provide a complete data log showing that it was processed within exact specifications. A client of ours, an OEM/ODM factory exporting to Europe, uses this feature as a key selling point. They can prove to their demanding customers that their heat treatment processes are under precise, intelligent control, giving them a significant edge over competitors who cannot offer the same level of assurance.
This data-driven approach also creates a continuous improvement loop. The AI is always learning. It analyzes the data from every single production run to refine its own models. If it finds a new combination of settings that results in even better surface brightness or lower energy consumption, that becomes the new "best practice." The furnace literally gets smarter and more efficient over time. This turns the challenge of achieving zero oxidation from a daily battle into a solved problem, allowing our clients to focus on what they do best: producing world-class stainless steel products.
AI prevents oxidation proactivelyПравда
AI uses real-time sensor data to make micro-adjustments before oxidation can occur, unlike reactive human operators.
AI follows fixed temperature setpointsЛожь
AI dynamically adjusts heating based on real-time thickness variations, replacing static temperature controls.
What future advancements can we expect in AI-powered furnace technology?
Problem: While current AI systems are revolutionary, technology never stands still. Manufacturers are always looking for the next leap in efficiency, quality, and automation to maintain a competitive edge. Agitate: Simply keeping up is not enough; anticipating the future of manufacturing technology is critical for long-term success and investment planning. What will the "smart furnace" of tomorrow look like? Solution: The future points towards even deeper integration, with AI driving not just individual furnaces but the entire manufacturing value chain, using concepts like generative AI[^6] and fully autonomous digital twins.
Future advancements in AI-powered furnace technology will likely focus on three key areas: fully autonomous "digital twin" operations, generative AI for process and alloy design, and seamless integration with the entire supply chain for end-to-end optimization, further enhancing both efficiency and material quality.
Looking ahead, we at AKS Furnace are not just focused on what AI can do today, but what it will enable tomorrow. The trajectory is clear: a move towards even greater autonomy and intelligence. We envision a future where a furnace doesn't just self-correct; it self-optimizes on a strategic level. Imagine a system that not only prevents oxidation but also experiments with new heating and cooling profiles in a virtual environment to discover a way to achieve the same quality with 10% less energy or 5% less hydrogen consumption. This leap from responsive control to generative innovation[^7] is the next frontier. It’s about creating a furnace that is not just a tool, but a true partner in research and development, constantly pushing the boundaries of what is possible in materials science and heat treatment.
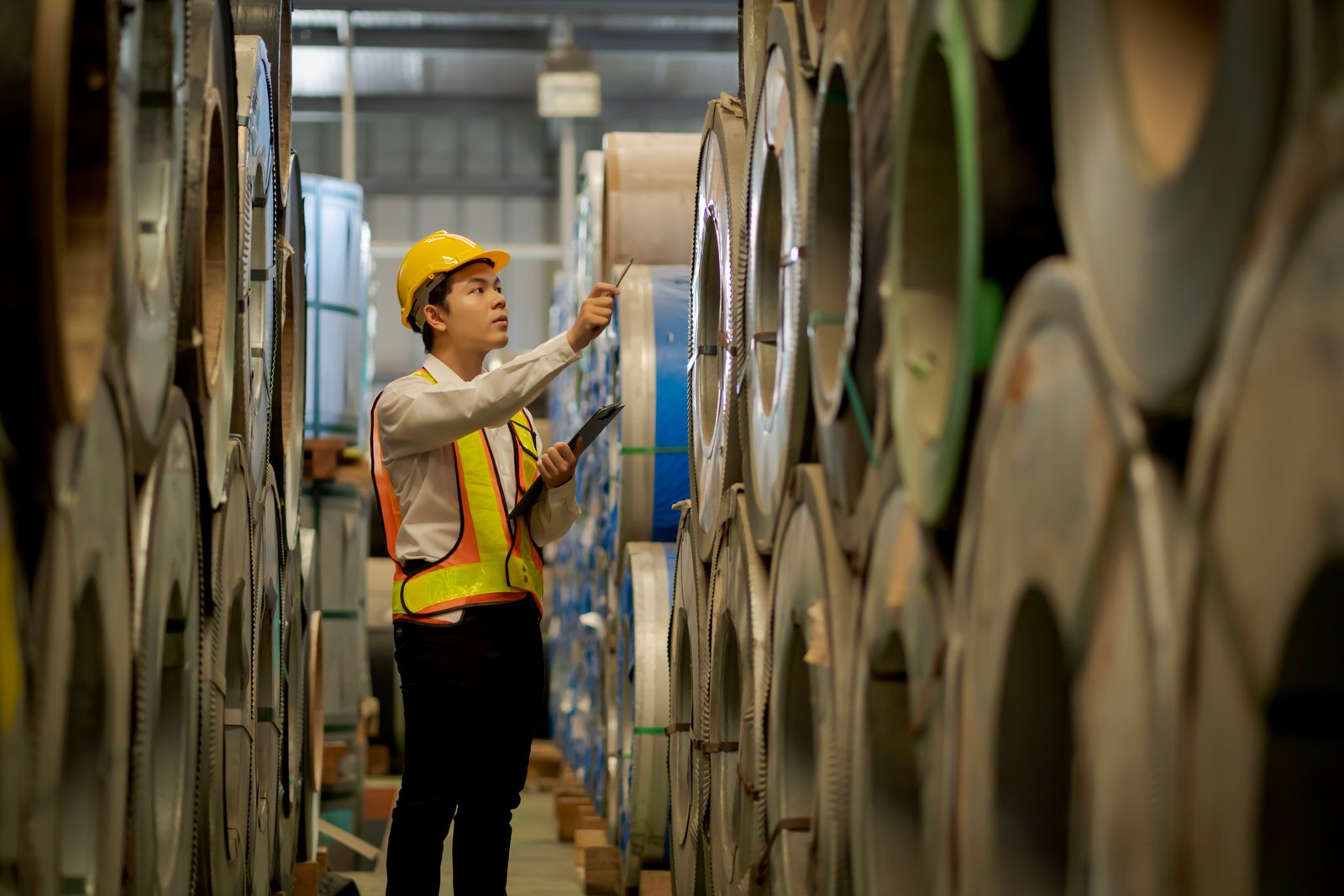
The concept of the "digital twin" will become central to this evolution. A digital twin is a highly complex, real-time virtual simulation of the physical furnace. It’s more than just a model; it’s a living replica that is constantly updated with data from the real furnace. This allows us to test new ideas risk-free. Before processing a new, experimental alloy, we can run it through the digital twin hundreds of times, allowing the AI to learn its unique properties and develop a perfect, first-time-right annealing recipe without ever wasting a single inch of physical material. This will dramatically accelerate innovation cycles and reduce the cost of developing new products. For our clients, this means they can respond to new market demands faster and with greater confidence, knowing their thermal processes have already been perfected in the virtual world before they begin in the real one.
The Rise of the Autonomous Digital Twin
The "digital twin" concept is the cornerstone of the next generation of smart furnaces. Currently, we use AI to model and control the physical furnace. In the future, the digital twin will take on a more autonomous role. It will serve as a perfect virtual sandbox where the AI can run millions of simulations to optimize the process in ways that would be too time-consuming, expensive, or risky to test on the physical line. For example, the AI could simulate the long-term effects of using a slightly different nitrogen/hydrogen gas blend to find a new optimum that balances cost and performance.
This autonomous digital twin will also revolutionize troubleshooting and diagnostics. If a physical furnace encounters an unknown issue, the digital twin can be used to replicate the fault conditions and test potential solutions in a virtual space. An engineer could test a hypothesis on the digital twin without taking the physical furnace offline. The AI could even run its own diagnostics, simulating thousands of potential fault scenarios to identify the most probable cause of a problem, reducing diagnostic time from hours or days to mere minutes.
Furthermore, the digital twin will become the primary training tool for operators and maintenance staff. A new operator can learn to run the furnace on a hyper-realistic simulation, experiencing a wide range of production scenarios and even simulated emergency situations in a completely safe environment. This will ensure that when they do step onto the factory floor, they are fully prepared and highly skilled, reducing the learning curve and improving operational safety and efficiency from day one.
Generative AI in Process and Material Design
While current AI excels at optimizing existing processes (predictive AI), the next wave will be dominated by generative AI. Generative AI doesn't just analyze data; it creates new things based on the patterns it has learned. In the context of furnace technology, this has staggering implications. Instead of simply perfecting the annealing recipe for a known steel grade, a manufacturer could define a set of desired final properties: "I need a material with X tensile strength, Y ductility, and a mirror-bright, Z-level finish."
The generative AI would then work backward, designing the ideal process to achieve that outcome. It might determine that a novel, non-linear cooling curve, combined with a pulsating atmospheric gas flow, could produce the desired grain structure. It could effectively invent new heat treatment recipes that a human engineer might never conceive of. This moves the furnace from a piece of production equipment to an active participant in materials research and development.
This capability could even extend to alloy design itself. By integrating the furnace's AI with metallurgical databases, a system could suggest modifications to the steel's chemical composition. For instance, it might propose that a small addition of niobium, combined with a specific, AI-generated annealing cycle, could achieve the target properties at a lower overall cost. This synergy between AI-driven process control and AI-driven material design will create a powerful feedback loop, accelerating the development of next-generation materials for aerospace, energy, and beyond.
Advancement Area | Current State (Industry 4.0) | Future State (Industry 5.0+) |
---|---|---|
Digital Twin | Used for modeling and real-time monitoring. | Autonomous; used for predictive simulation and "what-if" analysis. |
Artificial Intelligence | Predictive AI optimizes existing, known processes. | Generative AI designs novel processes and material recipes. |
System Integration | Integrated with plant-level MES/ERP systems. | Fully integrated with the entire external supply chain. |
Human Role | Operator supervises AI and manages strategy. | Human-AI collaboration on R&D and strategic goals. |
Optimization Goal | Maximize quality and efficiency of a specific process. | Optimize the entire value chain from raw materials to end-customer. |
Seamless Supply Chain and Ecosystem Integration
Looking beyond the four walls of the factory, the future of AI-powered furnaces involves seamless integration into the broader supply chain ecosystem. The furnace's AI won't just talk to the factory's ERP system; it will communicate directly with suppliers and customers[^8]. For example, the furnace's AI could receive real-time data on the chemical composition of a steel coil directly from the steel mill's own systems as it's being produced. This would allow the annealing furnace to pre-calculate the perfect recipe before the coil even arrives at the factory.
On the other end, the data from the annealing process—the "birth certificate" for each coil—could be automatically shared with the end customer's systems. An automotive manufacturer, for instance, could feed this data into their own stamping press simulators to predict how a specific coil will behave, allowing them to adjust their own processes for optimal performance. This creates a "digital thread" that follows the material from its creation to its final use, ensuring quality and traceability at every step.
This level of integration will enable a truly responsive and agile manufacturing ecosystem. If a customer places an urgent order for a product with specific properties, the system can instantly check the availability of raw materials with suppliers, schedule the production run, and provide an accurate delivery date, all automatically. This will reduce lead times, minimize inventory, and create a highly efficient, demand-driven value chain, with the intelligent, AI-powered furnace operating as a critical, data-rich node in this interconnected network.
Digital twins enable risk-free experimentationПравда
Digital twins allow manufacturers to test new processes and materials virtually before physical implementation, reducing waste and accelerating innovation.
Current AI can design new alloys autonomouslyЛожь
While current AI optimizes existing processes, generative AI for alloy design is still emerging and requires human-AI collaboration.
Заключение
AI-powered furnace control is no longer a future concept but a present-day reality for achieving zero-oxidation in bright annealing. By leveraging predictive analytics and real-time, data-driven adjustments, Stainless Steel 4.0 delivers unparalleled quality, efficiency, and reliability, defining the new standard for the global metals industry.