Что вызывает появление радужных окислов и помутнений в отожженной нержавеющей стали и как их можно устранить?
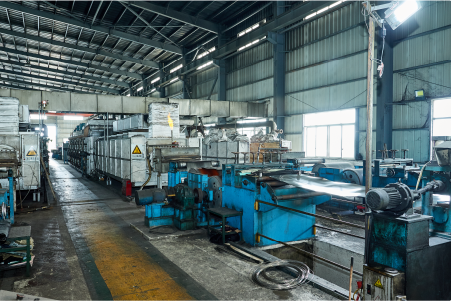
Striving for a perfect, mirror-like finish on stainless steel but ending up with frustrating rainbow tints and cloudy patches? These defects not only ruin the aesthetic but can compromise the material's integrity, leading to costly rejections and rework. You need a reliable solution that ensures consistency.
The primary causes of rainbow oxides and cloudiness in bright annealed stainless steel are improper atmospheric control, temperature inconsistencies, and surface contaminants. Fixing these issues involves maintaining a high-purity, low-dew-point protective atmosphere, ensuring precise temperature regulation, and implementing rigorous pre-cleaning procedures before annealing.
At AKS Furnace, I’ve seen countless manufacturers grapple with these very issues. The frustration is palpable when your final product doesn't meet the high standards your clients expect. But achieving that flawless, bright finish is not a matter of luck; it's a science. This article will guide you through the technical reasons behind these common defects and provide actionable solutions.
Understanding these defects requires a deeper look into the delicate thermodynamics at play during the annealing process. It’s a battle fought on a microscopic level, where even a few parts per million of oxygen or water vapor can sabotage your results. For instance, a study by the Materials Technology Institute1 found that for 304 stainless steel, a dew point above -40°C in a hydrogen atmosphere can lead to the formation of chromium oxides, the very culprit behind the rainbow discoloration. It's not just about having a furnace; it's about mastering the environment within it. We'll explore how to create and maintain this perfect environment.
What are the common defects in bright annealed stainless steel?
Are you investing heavily in bright annealing only to find your stainless steel plagued by defects like orange peel, pitting, or discoloration? These surface flaws can undermine your product's value and reputation, turning a premium material into scrap. You need to identify the root cause.
Common defects in bright annealed stainless steel include rainbow oxides (discoloration from thin oxide layers), cloudiness or haziness (from surface micro-roughness or contamination), orange peel (a rough surface texture), pitting, and black spots. These issues primarily stem from atmospheric impurities, temperature deviations, and inadequate pre-cleaning.
When a client brings me a sample marred by these imperfections, the first thing I do is look beyond the surface. These defects are symptoms of an underlying process issue, a story told by the steel itself. For example, a faint blue or yellow tint—what we call rainbow oxide—points directly to a reaction with oxygen, no matter how minute. Cloudiness might suggest a different problem, perhaps related to lubricants that weren't fully removed before the heat treatment. Understanding this language is the first step toward a cure. It’s a diagnostic process that saves time, money, and materials in the long run. I’ve found that many manufacturers focus solely on the furnace's temperature curve, but the true artistry of bright annealing lies in controlling the unseen elements: the atmosphere, the surface cleanliness, and the material's journey into the heat. In the following sections, we’ll break down each of these common defects, exploring not just what they are, but what they tell you about your process and how to respond effectively to achieve that flawless, brilliant finish your customers demand.
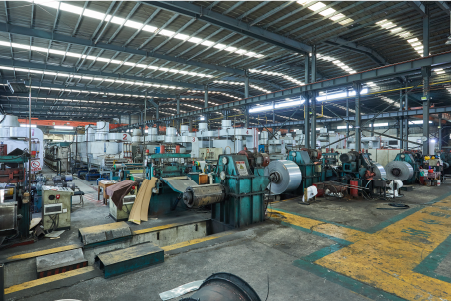
A comprehensive understanding of common defects is foundational to achieving high-quality bright annealing outcomes. These are not merely cosmetic issues; they are indicators of metallurgical and chemical inconsistencies that can affect the performance and lifespan of the final product. Manufacturers must learn to read these signs to diagnose and rectify the underlying process deficiencies, moving from a reactive to a proactive state of quality control. This deep dive will dissect the three most prevalent and costly defects: rainbow oxides, cloudiness, and orange peel texture, providing a framework for their identification and analysis.
The Anatomy of Rainbow Oxides
Rainbow oxides, or heat tint, are thin, transparent oxide layers that form on the surface of stainless steel. The color variation is an optical effect caused by light interference, where the thickness of the oxide layer determines the color we perceive, much like oil on water. This layer is primarily composed of chromium oxide ($Cr_2O_3$). While a very thin, passive layer of chromium oxide is what gives stainless steel its corrosion resistance, uncontrolled oxidation during annealing leads to these visible, non-uniform layers. The thickness can range from 30 to 500 nanometers, creating colors from yellow and gold to purple and blue.
The formation is a direct result of the steel's chromium content reacting with oxidizing agents in the furnace atmosphere. Key culprits include oxygen ($O_2$) and water vapor ($H_2O$). At annealing temperatures (typically above 1000°C), chromium is highly reactive. Even a few parts per million (PPM) of these oxidants can be enough to trigger the reaction. For example, a client in the automotive sector, "PrecisionCo," was producing exhaust components from 304-grade stainless steel2. They experienced persistent blue and purple tinting near the weld seams. Our analysis revealed that their nitrogen-hydrogen atmosphere had a dew point of -35°C, which is insufficient. By implementing a gas purification system to lower the dew point to below -60°C, we eliminated the heat tint, ensuring their parts met the stringent aesthetic and anti-corrosion standards required by their automotive OEM customers.
This defect is more than just a cosmetic flaw. While the passive layer is beneficial, the thicker, colored oxide layer can be detrimental. Research published in the Журнал "Материаловедение и эксплуатация материалов3 has shown that the presence of heat tint can selectively reduce the pitting corrosion resistance of austenitic stainless steels. The area immediately beneath the oxide layer can become depleted of chromium, creating a localized vulnerability. For manufacturers of medical devices or high-purity piping, where corrosion resistance is paramount, rainbow oxides are grounds for immediate rejection. Therefore, controlling the furnace atmosphere isn't just about looks; it's about preserving the fundamental properties that make stainless steel a premium material.
Deconstructing Surface Cloudiness
Cloudiness, often described as a hazy or milky appearance, is another common defect that detracts from the desired mirror-like finish of bright annealed steel. Unlike the distinct colors of rainbow oxides, cloudiness is a more subtle, uniform dullness. This defect can be caused by two primary mechanisms: microscopic surface contamination or the initial stages of oxidation that don't progress to form a colored interference film. It’s a sign that the surface is not perfectly clean or that the protective atmosphere is borderline effective.
One major cause is residual lubricants, rolling oils, or cleaning agents on the steel's surface before it enters the furnace. If the pre-treatment cleaning and degreasing stages are inadequate, these organic compounds can vaporize and pyrolyze in the furnace's hot zone. The carbonaceous residue can then deposit back onto the steel surface, creating a fine, hazy film that scatters light. We worked with a manufacturer of high-end kitchenware who faced persistent cloudiness on their 430-grade ferritic stainless steel sheets. An audit of their process revealed that their aqueous cleaning system wasn't completely removing the rolling oils. By optimizing the detergent concentration and improving their multi-stage rinsing process, the cloudiness was eliminated, resulting in a brilliant, reflective finish that significantly boosted their product's market appeal.
The second cause is related to the furnace atmosphere itself. If the dew point is not low enough, or if there's a minor air leak, a very fine, uniform layer of micro-oxides can form across the entire surface. This layer is too thin to create a colored interference effect but is thick enough to disrupt light reflection, causing the hazy appearance. This is particularly common in furnaces with poor atmospheric integrity or when using a protective gas that is not sufficiently pure. For sensitive materials like 400-series stainless steel, achieving a dew point of -60°C or lower is critical. Preventing cloudiness is therefore a two-front battle: ensuring immaculate surface cleanliness on entry and maintaining an ultra-pure, dry atmosphere during the entire heating and cooling cycle.
Understanding 'Orange Peel' and Surface Texture Defects
'Orange peel' refers to a rough, bumpy surface texture that resembles the skin of an orange. This is not a film or a deposit but a physical defect in the steel's surface topography. It typically becomes apparent after the annealing process, which can accentuate the underlying grain structure of the metal. The primary cause of orange peel is an excessively large grain size in the metal, which can result from over-annealing (holding the material at a high temperature for too long) or from using raw material that already has a coarse grain structure.
During the annealing process, the crystal grains within the metal recrystallize and grow. If this growth is excessive, the boundaries between the large grains become visible on the surface, leading to the characteristic uneven texture. I recall a case with a client producing decorative architectural panels. They were experiencing severe orange peel, making their panels unsuitable for high-gloss applications. We analyzed their process and found they were annealing at a temperature 50°C higher than necessary for the required softness, in an attempt to speed up the cycle. By reducing the annealing temperature and optimizing the belt speed in their continuous mesh belt furnace, we helped them refine the grain structure, eliminating the orange peel and achieving a smooth, reflective surface.
Preventing orange peel involves careful control over both the raw material and the annealing parameters. It starts with sourcing steel with a fine, uniform grain structure. Subsequently, the annealing cycle—specifically the peak temperature and the time spent at that temperature—must be precisely controlled to achieve the desired recrystallization and softening without promoting excessive grain growth. Advanced process control systems, like those in our AKS furnaces, allow for multi-zone temperature regulation to within ±1°C. This level of precision ensures that the material receives the exact amount of thermal energy required, preventing the overheating that leads to coarse grains and the dreaded orange peel effect.
Rainbow oxides indicate oxygen contaminationПравда
The colored tints are caused by chromium reacting with oxygen/water vapor in furnace atmosphere.
Orange peel is purely cosmeticЛожь
Orange peel indicates excessive grain growth which can affect mechanical properties.
Why do rainbow oxides occur during the bright annealing process?
Are you seeing unwanted rainbow colors on your finished stainless steel parts? This heat tint is a clear sign of a process problem, indicating that the chromium in your steel has reacted with oxygen. This compromises the surface quality and can even reduce corrosion resistance.
Rainbow oxides occur during bright annealing when the chromium in the stainless steel reacts with oxidizing agents like oxygen or water vapor present in the furnace atmosphere. At high annealing temperatures, even trace amounts of these contaminants can form a thin oxide layer whose thickness dictates the color.
When I visit a facility struggling with rainbow oxides, the first place I investigate is the furnace atmosphere. The entire principle of "bright" annealing hinges on preventing oxidation, and any discoloration is a direct failure of that principle. It's a sensitive chemical balancing act performed at over 1000°C. Think of the protective atmosphere—typically a blend of hydrogen and nitrogen—as an invisible shield. If that shield has any cracks, such as an air leak or high moisture content (a high dew point), oxygen will rush in and tarnish the steel's surface. A client once told me, "We use 99.99% pure gas, so that can't be the problem." However, their issue wasn't the gas source; it was a small, undetected leak in a fitting after the gas purifier. That tiny leak was enough to elevate the oxygen level by just a few parts per million, causing entire coils to be rejected. This illustrates that achieving a flawless finish requires a holistic view of the system, from the gas source to the furnace's final seal. We will now explore the specific atmospheric conditions, temperature variables, and material factors that contribute to this costly defect.
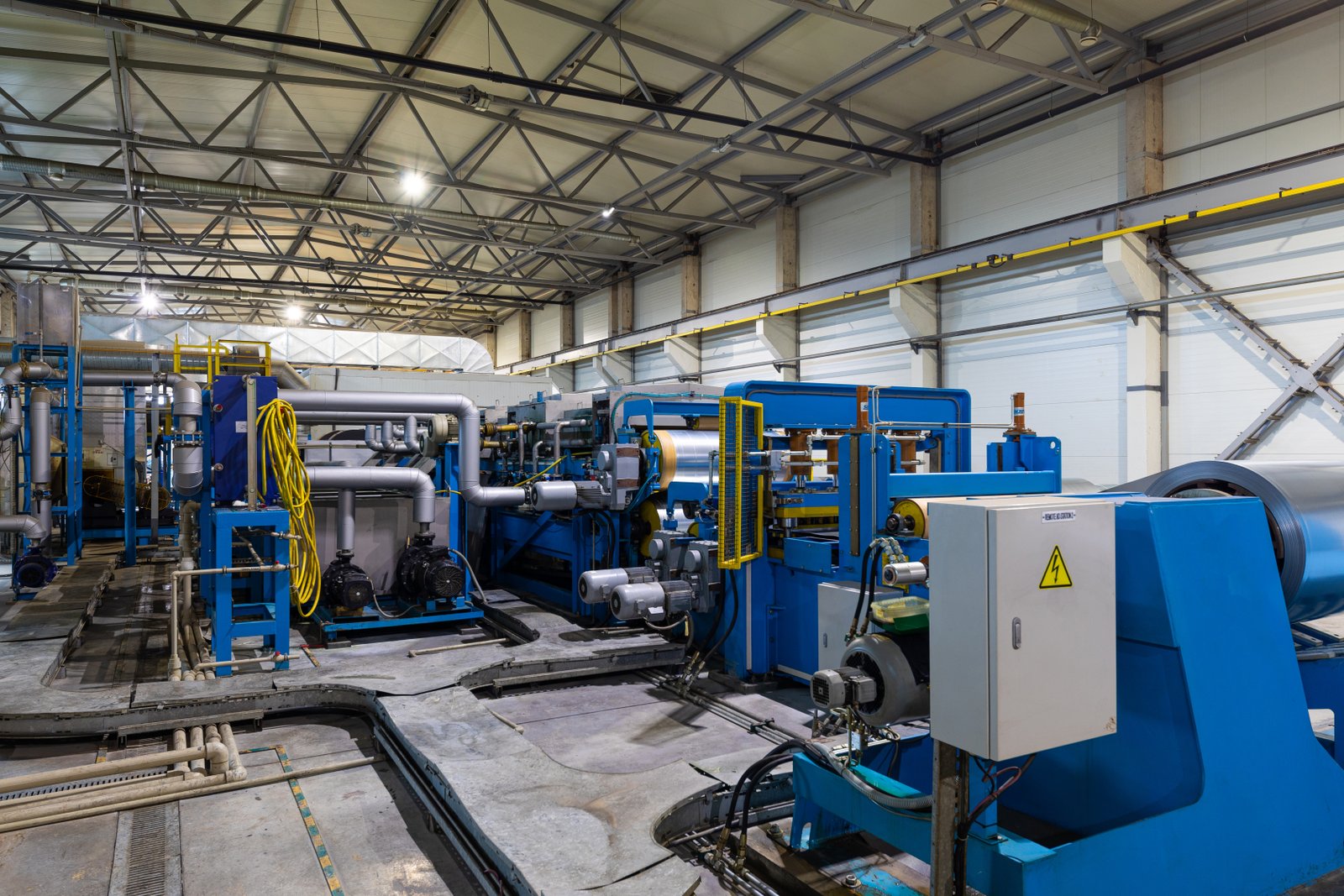
The appearance of rainbow oxides is a direct signal that the thermodynamic conditions within the annealing furnace have favored oxidation over preservation of a clean, metallic surface. While seemingly a simple discoloration, its formation is a complex interplay between atmospheric composition, temperature, and the metallurgy of the stainless steel itself. To truly prevent this defect, one must move beyond a superficial understanding and delve into the precise chemical and physical mechanisms that govern the process. A successful bright annealing operation is a testament to meticulous control over these variables, ensuring the steel emerges as clean and bright as it entered.
Критическая роль чистоты атмосферы и точки росы
The protective atmosphere is the single most critical factor in preventing rainbow oxides. Its purpose is to create an environment with an oxygen potential low enough to prevent the oxidation of the steel's primary alloying elements, especially chromium and iron. The most common protective atmospheres are pure hydrogen, or a mix of nitrogen and hydrogen. Hydrogen acts as a powerful reducing agent4, actively scavenging trace oxygen and reacting with any existing surface oxides to clean the steel. However, the purity of this atmosphere is paramount.
The two main enemies within the furnace atmosphere are oxygen and water vapor. Oxygen can enter through leaks in the furnace seals, muffle, or gas lines5. Water vapor is often introduced with the protective gas itself if it hasn't been properly dried, or through desorption from furnace refractories. The "dew point" is the industry-standard measure of water vapor content in the gas; it is the temperature at which the water vapor would condense into liquid water. A lower dew point signifies a drier, purer gas. For annealing standard austenitic grades like 304, a dew point of -40°C is often considered a minimum requirement. For more sensitive, high-chromium ferritic grades like 430 or 443, a dew point of -60°C or lower is essential.
I remember a project with "PrecisionCo," our automotive client, where they were using a nitrogen-hydrogen mix to anneal 409 stainless steel for exhaust systems. They were battling persistent yellow and brown tinting. Their gas supplier guaranteed a dew point of -50°C at the source, but measurements at the furnace inlet revealed a dew point of only -30°C. We discovered that a long, uninsulated supply line was allowing ambient moisture to permeate through microscopic pores in the hose material. By replacing the line with electropolished stainless steel tubing and installing a point-of-use gas purifier, we brought the dew point at the furnace down to -65°C. This simple change completely eliminated the rainbow oxides and improved their production yield by over 15%, saving them from costly acid pickling to remove the tint.
Temperature Fluctuations and Their Impact on Oxidation Kinetics
While atmosphere is key, temperature dictates the rate at which oxidation reactions occur. The laws of thermodynamics, specifically the Ellingham diagram6, show that as temperature increases, metals become more prone to oxidation. During the annealing cycle, the steel is most vulnerable as it heats up to and soaks at the peak temperature (typically 1040-1150°C). Any momentary lapse in atmospheric purity during this high-temperature phase will result in rapid oxide formation.
Inconsistent temperature control across the furnace can also lead to non-uniform oxidation. If certain parts of the furnace are hotter than others, the steel passing through these "hot spots" will oxidize more readily, leading to patchy or streaky discoloration. This is a common issue in older furnaces with simplistic heating element designs or failing thermocouples. Modern furnaces, like the AKS bright annealing lines, utilize multi-zone PID (Proportional-Integral-Derivative) control systems. These systems use an array of thermocouples along the length of the furnace muffle to monitor temperatures precisely. The controller constantly adjusts power to the heating elements in each zone to maintain a uniform temperature profile, typically within ±1°C of the setpoint.
Furthermore, the cooling rate is just as important. The steel must be cooled back down to a non-reactive temperature (typically below 200°C) while still under the full protection of the high-purity atmosphere. If the steel is exposed to air while it is still too hot, it will instantly form a thick oxide layer, completely undoing the work of the bright annealing process. Our advanced cooling systems use a combination of high-velocity gas jets and a water-jacketed cooling muffle to rapidly and uniformly cool the strip. This not only prevents re-oxidation but also helps in achieving desired mechanical properties and excellent strip flatness.
Contaminants from Pre-Treatment and Material Surface
The final piece of the puzzle is the condition of the stainless steel surface before it even enters the furnace. The principle is simple: what goes in, comes out. Any contaminants on the surface can react with the steel or the furnace atmosphere at high temperatures, causing defects that are often mistaken for atmospheric oxidation. Common contaminants include rolling oils, lubricants, drawing compounds, iron fines from slitting or cutting, and even residue from cleaning solutions.
For example, sulfur- or chlorine-containing lubricants are particularly detrimental. At annealing temperatures, these elements can be released and directly attack the steel surface, causing severe pitting and discoloration that cannot be fixed. A client manufacturing stainless steel wire was experiencing black spots and rainbow streaks. An analysis of their raw wire revealed residual drawing lubricant with a high sulfur content. Their pre-cleaning process was a simple solvent wipe, which was insufficient. We advised them to install a multi-stage ultrasonic cleaning line with an alkaline degreasing solution, followed by a thorough rinse and air-knife drying system immediately before the furnace inlet. This ensured the wire was pristine upon entry, completely resolving the defect.
Even water from a final rinse stage can be a source of contamination if it is not thoroughly dried. The water can carry dissolved minerals that deposit on the surface, and the water itself contributes to a higher effective dew point inside the furnace. This highlights the need for an integrated approach to bright annealing. It is not just a heat treatment process but a complete production line that must include robust, effective cleaning and drying stages. The quality of the final product is a direct reflection of the quality and control exercised at every preceding step.
Chromium reacts with oxygenПравда
Rainbow oxides form when chromium in stainless steel reacts with oxygen during annealing, compromising corrosion resistance.
Pure gas prevents oxidationЛожь
Even 99.99% pure gas won't prevent oxidation if furnace leaks exist - system integrity matters more than gas purity alone.
How does cloudiness affect the quality of stainless steel surfaces?
Is your bright annealed stainless steel coming out with a dull, hazy finish instead of a brilliant shine? This cloudiness might seem like a minor cosmetic issue, but it can signal underlying contamination or process flaws that compromise the material's surface integrity and value.
Cloudiness negatively affects the quality of stainless steel by reducing its reflectivity and aesthetic appeal, which is critical for decorative and consumer-facing products. It can also indicate the presence of microscopic surface residues or a thin, non-uniform oxide layer that may compromise localized corrosion resistance.
I often explain to clients that cloudiness is one of the most deceptive defects. Unlike the obvious alarm bell of a rainbow oxide, a hazy surface can be dismissed as a minor batch variation. However, this is a dangerous assumption. This dullness is evidence that something has interfered with the formation of a clean, smooth surface at a microscopic level. For a manufacturer of high-end appliances, that lack of brilliance is the difference between a premium product and a discounted one. For a producer of medical instruments, it could indicate surface contamination that is simply unacceptable. It’s a subtle but critical indicator of process health. The haze tells a story of inadequate cleaning, a borderline atmosphere, or an incorrect thermal profile. Addressing it isn't just about restoring the shine; it's about tightening process control to guarantee the metallurgical and surface purity that defines high-quality stainless steel. In the following analysis, we'll examine the specific ways this seemingly minor flaw impacts product value, performance, and manufacturability.
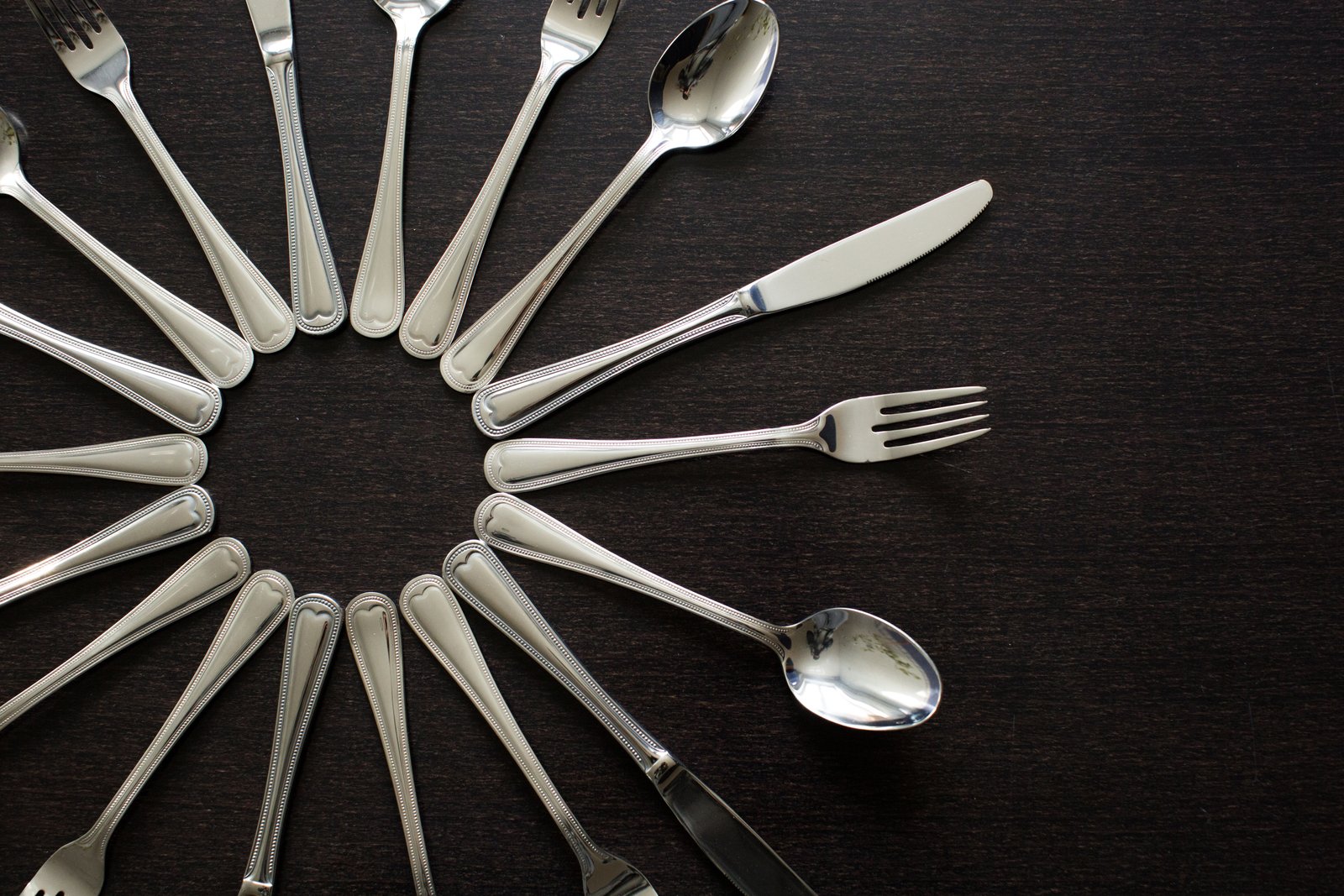
Cloudiness on a bright annealed surface is a critical quality issue that extends far beyond simple aesthetics. It serves as a tangible indicator of microscopic inconsistencies that can have significant repercussions on the material's commercial value, its performance in corrosive environments, and its behavior in subsequent manufacturing processes. While it may lack the alarming appearance of colored oxides, its presence signifies a deviation from an optimal, controlled annealing process7. Understanding its multifaceted impact is essential for any manufacturer aiming to produce truly premium, high-performance stainless steel products.
Impact on Aesthetic Value and Commercial Viability
For a vast range of stainless steel applications, the visual appearance is not just a feature; it is the primary product attribute. In markets such as architectural panels, high-end kitchen appliances, automotive trim, and consumer electronics, a brilliant, defect-free, mirror-like finish is what commands a premium price. Cloudiness directly attacks this value proposition. A hazy surface scatters light instead of reflecting it, resulting in a dull, cheapened appearance. This can lead to immediate rejection by quality-conscious customers.
Consider the case of a company manufacturing stainless steel facades for luxury buildings. Their specification calls for a "No. 8 super mirror finish." If the annealed raw material exhibits even a slight cloudiness, it becomes impossible to achieve this level of reflectivity through subsequent polishing. The defect is inherent in the surface. This forces the manufacturer to either scrap the material or sell it at a steep discount for a less demanding application, directly impacting profitability. A study by a leading European steel distributor found that stainless steel coils with "perfect" surface brightness could command a price 10-15% higher than coils with minor visual defects like cloudiness.
This commercial impact creates a ripple effect. A brand's reputation is built on consistency. If a manufacturer of, for instance, premium range hoods delivers a product with a hazy finish, it undermines consumer confidence in the quality of the entire appliance. In my experience, clients who successfully penetrate high-end markets are those who have mastered the art of eliminating cloudiness. They understand that the perceived value is inextricably linked to this flawless, brilliant shine, and they invest in furnace technology8—like AKS furnaces with advanced atmosphere control and rapid jet cooling—that can deliver this result consistently, coil after coil.
Compromised Corrosion Resistance and Surface Purity
Beyond aesthetics, cloudiness can be a red flag for compromised surface integrity and reduced corrosion resistance. As we've established, one of the primary causes of a hazy finish is the presence of a very thin, non-uniform oxide layer or microscopic residues from incomplete pre-cleaning. While this oxide layer may not be thick enough to create colored interference patterns, its presence disrupts the uniform passive film of chromium oxide that is essential for stainless steel's corrosion protection.
This micro-scale disruption can create sites for localized corrosion to initiate. The American Iron and Steel Institute (AISI) has published guidelines indicating that any surface anomaly, including haziness from processing, can act as a nucleation site for pitting or crevice corrosion, especially in chloride-rich environments. For example, stainless steel used in marine hardware, food processing equipment, or pharmaceutical manufacturing must have a pure, homogenous surface. Cloudiness on a stainless steel mixing tank for saline solutions could lead to premature failure due to pitting corrosion, a catastrophic outcome in a regulated industry.
Furthermore, if the cloudiness is caused by residual carbonaceous films from lubricants, these deposits can create galvanic cells on the surface when an electrolyte is present, accelerating corrosion. They also present a major problem for applications requiring high purity. For semiconductor manufacturing equipment or ultra-high vacuum components, any surface contamination can lead to outgassing, ruining sensitive processes. Therefore, a cloudy surface is not just visually imperfect; it is often metallurgically or chemically impure, rendering it unsuitable for many high-performance applications.
Challenges in Downstream Processing and Fabrication
The negative effects of cloudiness extend to downstream manufacturing operations like welding, coating, and forming. A clean, uniform surface is critical for the success of these processes. Cloudiness, indicating contamination or a micro-oxide layer, can create a host of problems that increase production costs and reduce the quality of the final fabricated product.
During welding, for instance, surface contaminants can vaporize and become incorporated into the weld pool, leading to porosity, reduced weld strength, and poor bead appearance. A thin oxide layer can interfere with arc stability in TIG welding, requiring higher energy input and potentially leading to greater distortion. A fabricator we worked with was experiencing inconsistent weld quality on cloudy 316L stainless steel tubing. The root cause was traced back to a hazy surface from the annealing stage. By resolving the cloudiness, they achieved more consistent, higher-quality welds with a lower rejection rate.
Similarly, for applications requiring painting, powder coating, or the application of protective films, a cloudy surface presents a major adhesion challenge. The microscopic residues or oxides that cause the haze act as a weak boundary layer, preventing the coating from forming a strong, durable bond with the steel substrate. This can lead to premature peeling, blistering, or flaking of the coating. Manufacturers often have to perform an additional, costly surface preparation step, such as mechanical abrasion or chemical etching, to remove the cloudy layer before coating, adding time and expense to their process. A perfectly bright, non-cloudy surface is pristine and ready for subsequent steps, streamlining the entire production workflow.
Cloudiness reduces stainless steel's reflectivityПравда
The article states that cloudiness scatters light instead of reflecting it, resulting in a dull appearance that diminishes aesthetic value.
Cloudiness improves corrosion resistanceЛожь
Cloudiness indicates surface impurities that disrupt the protective chromium oxide layer, potentially creating nucleation sites for localized corrosion.
What solutions are available to prevent or fix rainbow oxides and cloudiness?
Are you tired of battling unpredictable rainbow tints and hazy surfaces on your annealed stainless steel? These defects disrupt production and hurt profits. The good news is that with precise process control and the right equipment, these issues are entirely preventable, ensuring a perfect finish every time.
Solutions to prevent rainbow oxides and cloudiness include maintaining a high-purity protective atmosphere with a dew point below -60°C, implementing rigorous multi-stage pre-cleaning to remove all contaminants, ensuring precise and uniform temperature control during annealing, and utilizing rapid, controlled cooling systems.
In my career, I've helped countless clients transition from fighting defects to preventing them. The solution isn't a single magic bullet but a systematic approach that transforms the entire annealing line into a controlled, predictable environment. Fixing these issues after they occur is expensive and often ineffective; pickling or polishing adds cost, lead time, and can alter the material's dimensions. True success lies in prevention. It starts with an uncompromising attitude toward two things: purity and precision. This means ensuring the steel is immaculately clean before it enters the furnace and that the atmosphere inside is purer and more stable than the process technically requires. This creates a buffer against the minor variations inherent in any industrial operation. I once worked with a large-scale strip processor9 who cut their defect rate by 90% not by overhauling their furnace, but by upgrading their gas management and pre-cleaning systems. This holistic philosophy is the key, and we will now detail the specific, actionable strategies that make it a reality.
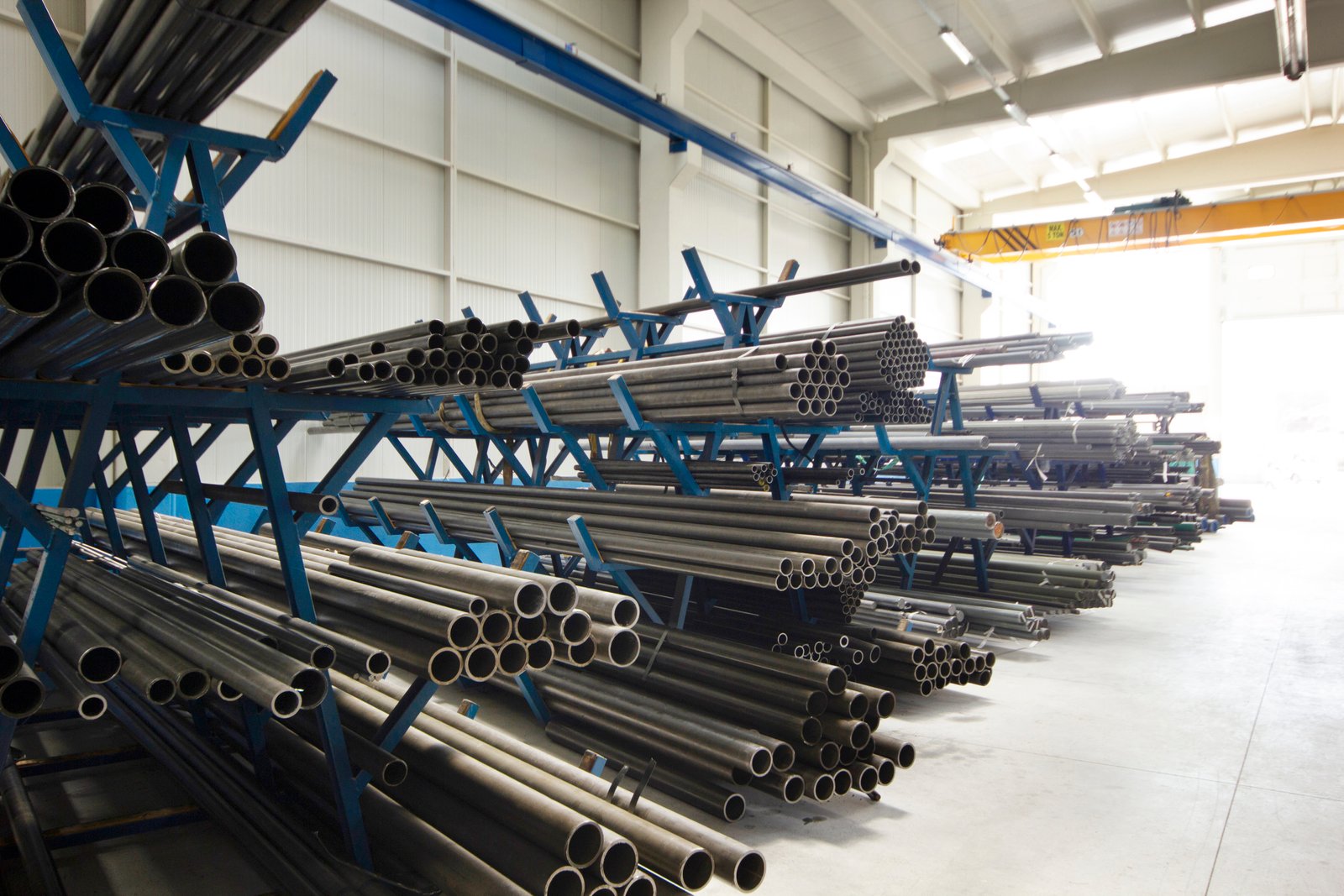
Preventing surface defects in bright annealing is an exercise in meticulous process engineering. It requires a multi-faceted strategy that addresses the three core pillars of the process: the material's initial surface condition, the integrity of the furnace atmosphere, and the precision of the thermal cycle. By implementing robust solutions in each of these areas, manufacturers can move from a reactive, problem-solving mode to a proactive, quality-assurance mindset. The goal is to create a process so stable and controlled that defects like rainbow oxides and cloudiness have no opportunity to form. This deep dive will explore the most effective solutions, supported by best practices and technical data.
Mastering the Protective Atmosphere: Purity, Dew Point, and Flow
The heart of any solution is the furnace atmosphere. The key is to create and maintain an environment10 that is chemically reducing to the steel surface throughout the entire process. This involves three critical components: gas purity, moisture control (dew point), and dynamic flow. First, the source gas—be it hydrogen or a nitrogen-hydrogen blend—must be of high purity, typically 99.99% or better. However, source purity is not enough. The entire gas delivery system, from the tank to the furnace muffle, must be constructed from high-quality, non-permeable materials like stainless steel to prevent contamination.
Second, and most importantly, is controlling the dew point. As discussed, water vapor is a potent oxidizing agent at high temperatures. An in-line gas purifier or dryer is not an optional accessory; it is a mandatory component for high-quality bright annealing. These systems use molecular sieves to strip moisture from the gas, routinely achieving dew points of -60°C to -70°C. This ultra-dry atmosphere dramatically shifts the chemical equilibrium away from oxidation. For example, for 304 stainless steel at 1050°C, the equilibrium dew point for preventing chromium oxidation is approximately -55°C. By operating at -65°C, you create a robust safety margin.
Third, the atmosphere must be dynamic. A continuous, positive flow of the protective gas through the furnace muffle is essential to purge any contaminants that desorb from the steel or the furnace interior and to prevent any air from entering at the inlet and outlet. The flow rate must be optimized—too low, and purging is ineffective; too high, and it becomes a significant operational cost. We engineer our AKS furnaces with sealed muffles and precisely calculated flow dynamics, often using an integrated oxygen and dew point analyzer with a feedback loop to adjust gas flow automatically, ensuring optimal protection with maximum efficiency.
The Non-Negotiable Step: Advanced Pre-Treatment and Cleaning
No furnace, no matter how advanced, can correct for a contaminated surface. The solution to many annealing defects begins long before the steel reaches the hot zone. A robust, multi-stage pre-cleaning and degreasing line is absolutely essential. The goal is to remove all organic compounds (oils, lubricants) and inorganic materials (iron fines, dust) that could cause defects. A typical state-of-the-art cleaning line, which we often integrate for our clients, includes an alkaline spray degreasing station, followed by mechanical brushing, multiple cascading rinse stages, and a final high-velocity air-knife drying system.
The choice of cleaning chemistry is critical and must be matched to the specific lubricants being used. A client producing small electronic components from stainless steel strip was using an oil-based stamping lubricant. Their simple solvent dip was leaving a microscopic film, causing cloudiness. By switching to an ultrasonic cleaning line using a heated alkaline solution specifically designed to saponify that oil, they achieved a perfectly clean surface. The ultrasonic cavitation physically blasts contaminants from the surface, ensuring even microscopic pores are cleaned.
The table below provides a comparative analysis of pre-cleaning methods and their effectiveness against common contaminants, highlighting why a multi-stage approach is superior for preventing annealing defects. This systematic approach ensures the steel entering the furnace is in the most pristine condition possible, eliminating a major variable from the process equation.
Метод очистки | Эффективность на маслах | Effectiveness on Fines/Particulates | Risk of Residue | Recommended For |
---|---|---|---|---|
Solvent Wiping | От низкого до среднего | Низкий | Высокий | Low-volume, non-critical applications only |
Aqueous Spray Wash | Средний | Средний | Средний | General purpose, light contamination |
Ультразвуковая очистка | Высокий | Высокий | Низкий | High-value parts, complex geometries, heavy oils |
Multi-Stage System | Очень высокий | Очень высокий | Очень низкий | All high-quality bright annealing applications |
Precision in Thermal Management: Uniform Heating and Controlled Cooling
ly, the thermal cycle itself must be precisely managed. The solution lies in achieving absolute temperature uniformity and a controlled cooling rate. Non-uniform heating leads to variations in grain structure and oxidation potential across the material. Modern furnaces achieve this through strategic design and advanced control. For instance, our continuous bright annealing furnaces use radiant tubes or strategically placed heating elements in multiple, independently controlled zones. This allows us to create a precise thermal profile—a gradual ramp-up, a stable soak, and a controlled initial cool-down—that is optimized for the specific grade and thickness of the steel being processed.
The cooling phase is equally critical for preventing defects. If the steel is cooled too slowly while still at a moderately high temperature (e.g., 300-600°C), it can still be susceptible to trace oxidation. The solution is rapid, yet controlled, cooling. Our AKS furnaces incorporate a sophisticated jet cooling section. Here, the cooled, purified protective atmosphere is recirculated at high velocity and directed onto the steel strip through an array of nozzles. This process, known as convective cooling, rapidly extracts heat, moving the steel through the vulnerable temperature range as quickly as possible.
This rapid cooling must occur entirely within the sealed, protected atmosphere of the cooling muffle. The steel should not exit into the ambient air until its temperature is well below the point where it can visibly oxidize, typically below 150°C. A client processing thin-gauge 430 stainless for appliance trim found that extending their sealed cooling section by three meters and increasing the jet cooler's gas flow rate completely eliminated a persistent, faint cloudiness that was appearing on the final product. This demonstrates that investing in superior cooling technology is a direct investment in surface quality.
Dew point below -60°C prevents oxidationПравда
Maintaining an ultra-dry atmosphere with dew point below -60°C creates a chemical equilibrium that prevents chromium oxidation during annealing.
Solvent wiping is sufficient for bright annealingЛожь
Solvent wiping alone leaves residues and is ineffective for high-quality bright annealing; multi-stage cleaning systems are required.
How can manufacturers implement best practices in bright annealing stainless steel?
Are you aiming to elevate your bright annealing from a source of problems to a competitive advantage? Simply having the equipment isn't enough. Implementing best practices in process control, maintenance, and training is what separates industry leaders from the rest, ensuring consistent quality and efficiency.
Manufacturers can implement best practices by establishing strict protocols for atmospheric control, including continuous dew point and oxygen monitoring. This involves creating a comprehensive pre-treatment and cleaning regimen, calibrating all furnace instrumentation regularly, and providing ongoing training for operators on quality control checkpoints.
Throughout my years of commissioning furnaces worldwide, I've observed a clear pattern: the most successful manufacturers treat their bright annealing line not as a single machine, but as a complete ecosystem11. They document everything, from the incoming raw material inspection to the gas flow rates for a specific product. They don't wait for defects to appear; they use statistical process control (SPC) to monitor key variables like dew point, temperature uniformity, and strip speed, allowing them to detect and correct drifts before they result in rejected material. This proactive, data-driven culture is the essence of best practice. It’s about building a robust system that is resilient to the small, everyday variations of a busy production floor. Implementing these practices requires commitment, but the payoff—in terms of reduced scrap, higher yields, and enhanced customer trust—is immense. We will now explore the specific pillars of this best-practice framework: robust process control, rigorous maintenance schedules, and empowering your team through knowledge.
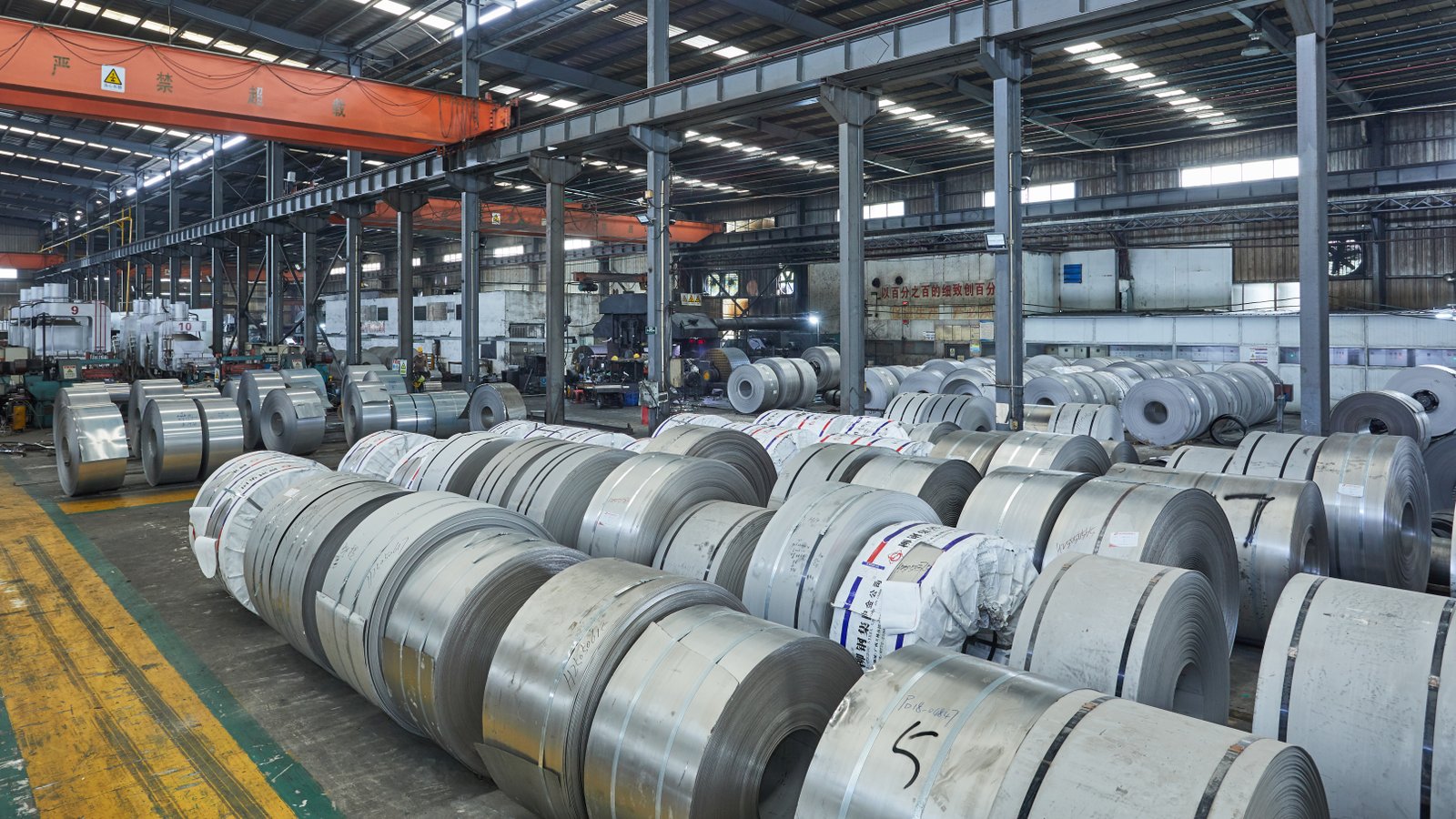
Implementing best practices in bright annealing is a strategic initiative that transforms an industrial process into a repeatable, high-precision manufacturing system. It’s about creating a culture of excellence centered on data, documentation, and continuous improvement. Adopting these practices minimizes variability, reduces waste, and consistently produces a high-quality product that meets the most stringent customer specifications. This transition requires a structured approach focusing on three core areas: developing Standard Operating Procedures (SOPs) and leveraging data, implementing a proactive maintenance and calibration program, and investing in comprehensive operator training and quality awareness.
Developing Data-Driven Standard Operating Procedures (SOPs)
The foundation of any best-practice implementation is the development of detailed and data-driven Standard Operating Procedures (SOPs)12. These are not just generic instruction manuals; they are living documents that specify the exact process parameters for each unique product (grade, thickness, width) that runs through the furnace. A comprehensive SOP for bright annealing should meticulously document every critical variable, leaving no room for guesswork. This includes pre-cleaning solution concentrations and temperatures, furnace temperature setpoints for each zone, strip or belt speed, protective atmosphere composition (e.g., H2/N2 ratio), gas flow rates, and maximum allowable dew point and oxygen levels.
To make these SOPs data-driven, manufacturers must first invest in instrumentation and data logging. This means equipping the furnace line with reliable sensors for continuous monitoring of temperature, gas flow, dew point, and oxygen content. At AKS, we integrate these systems directly into the furnace PLC and HMI. This allows for real-time visualization and, more importantly, historical data logging. By analyzing this data, process engineers can correlate specific parameter sets with optimal surface quality outcomes. For example, by reviewing historical data, a plant manager might discover that a specific grade of 400-series steel achieves the best brightness with a slightly higher hydrogen content and a 5% slower belt speed than initially estimated.
This data-driven approach facilitates continuous improvement. For instance, using Statistical Process Control (SPC), control charts can be created for critical parameters like the dew point. If the chart shows a trend of the dew point slowly increasing over several days, it can signal an impending issue—like the saturation of a gas dryer—long before it crosses the threshold that causes defects. We coached "PrecisionCo," our automotive client, to implement SPC charts for their furnace atmosphere. Within three months, they were able to pre-emptively service their gas purifier based on performance trends, completely avoiding any production downtime or quality issues related to atmospheric moisture. This proactive, evidence-based management is the hallmark of a world-class operation.
Proactive Maintenance and Calibration Routines
A state-of-the-art furnace can only perform as well as it is maintained. A reactive maintenance culture—fixing things only when they break—is a recipe for inconsistent quality and costly downtime. A best-practice approach mandates a rigorous, proactive, and preventive maintenance schedule. This schedule should cover every component of the annealing line, from the pre-cleaning nozzles to the furnace's cooling fans and gas analyzers. Weekly checks might include inspecting furnace door seals for leaks, verifying gas pressures, and cleaning filters. Monthly or quarterly tasks would involve deeper inspections, such as checking heating elements for signs of wear and calibrating thermocouples.
Calibration is a particularly critical aspect of maintenance. If a thermocouple is reading 10°C lower than the actual temperature, the steel is being overheated, potentially leading to grain growth and other defects. Similarly, if a dew point analyzer is out of calibration and reading drier than the actual conditions, operators may be running a process with insufficient atmospheric protection without even knowing it. All critical instrumentation—thermocouples, gas flow meters, oxygen and dew point analyzers—must be calibrated against certified standards on a regular, documented schedule. Traceability of this calibration is essential for quality audits, especially for clients in the automotive, aerospace, or medical industries.
We worked with a strip mill that was struggling with intermittent cloudiness. A maintenance audit revealed that their thermocouples hadn't been calibrated in over a year. After calibration, it was discovered that the temperature in their soak zone was nearly 20°C hotter than the control panel displayed. This excessive temperature was causing micro-oxidation. Implementing a quarterly calibration schedule for all 16 of their thermocouples stabilized their process and eliminated the cloudiness. A proactive maintenance program is not a cost center; it is an investment that protects the much larger investment in equipment, materials, and product quality.
Comprehensive Operator Training and Quality Empowerment
Ultimately, the people running the equipment are the final guardians of quality. Even the most advanced, automated system requires skilled operators who understand the "why" behind the "what." Best-in-class manufacturers invest heavily in training their teams. This training should go beyond basic button-pushing and cover the fundamentals of stainless steel metallurgy13, the principles of protective atmospheres, the chemistry of surface cleaning, and, most importantly, visual defect recognition and root cause analysis.
Operators should be empowered to be the first line of defense for quality control. They should be trained to recognize the subtle differences between cloudiness and minor oxidation, to understand what a rising dew point reading implies, and to know the immediate steps to take when a process parameter drifts outside its control band. We often conduct on-site training workshops for our clients' teams, using real-world examples of good and bad products to build their diagnostic skills. This empowers them to take ownership of the process.
This empowerment is fostered by creating clear communication channels and feedback loops. For example, setting up a quality checkpoint at the furnace exit where operators visually inspect the strip with proper lighting allows for immediate feedback. If an operator spots a developing issue, they should have the authority and a clear protocol to alert a process engineer or pause the line to prevent the production of large amounts of defective material. By investing in their people, manufacturers turn their operators from machine supervisors into true process artisans, creating a resilient and quality-focused culture that drives long-term success.
Контроль точки росы предотвращает окислениеПравда
Continuous dew point monitoring is essential as it helps maintain the protective atmosphere needed to prevent oxidation during bright annealing.
SPC detects defects after they occurЛожь
Statistical Process Control (SPC) is proactive, identifying trends and potential issues before defects appear in the product.
Заключение
Ultimately, preventing rainbow oxides and cloudiness boils down to mastering process control. By maintaining atmospheric purity with a low dew point, ensuring immaculate pre-cleaning, and precisely managing the thermal cycle, you can consistently achieve the flawless, bright finish that high-value markets demand.
-
Confirm the relationship between dew points and chromium oxide formation ↩
-
Learn about the 304-grade stainless steel's benefits and uses ↩
-
Understand how heat tint affects corrosion resistance in stainless steel ↩
-
Learn about hydrogen's role in preventing oxidation in heat treatment ↩
-
Find solutions to prevent furnace atmospheric contamination ↩
-
Understand temperature's effect on oxidation through the Ellingham diagram ↩
-
Learn why a precise annealing process is crucial for surface quality and brightness ↩
-
Understand the benefits of using furnace technology like AKS for superior surface quality ↩
-
Discover the effective strategies used to drastically reduce defect rates ↩
-
Learn how atmosphere quality impacts the prevention of oxidation in stainless steel ↩
-
Learn about the comprehensive approach to manufacturing sustainability and efficiency ↩
-
Understand key elements in creating effective SOPs for industrial processes ↩
-
Gain insights into the properties and processing of stainless steel ↩