What are the Safe Windows for Annealing Copper, Cu-Ni, and Cu-Zn Alloys?
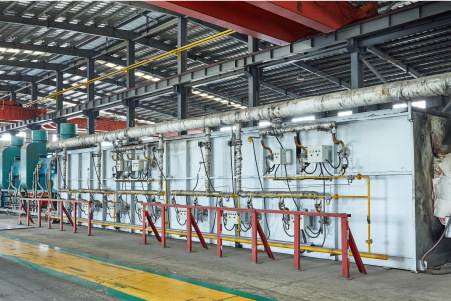
Are you struggling with inconsistent results when annealing copper alloys, leading to wasted material or subpar product quality? The challenge of hitting that perfect annealing window can be frustrating and costly. As your partner in heat treatment, I'm here to guide you through achieving optimal results.
Safe annealing windows for copper, Cu-Ni, and Cu-Zn alloys depend critically on the specific alloy composition, the degree of prior cold work, desired final mechanical properties, and precise control over annealing temperature, time, and furnace atmosphere to ensure metallurgical integrity and prevent defects.
Understanding the nuances of annealing these versatile alloys is more than just academic; it's fundamental to your production quality and efficiency. If you've ever faced issues like insufficient softening, excessive grain growth, surface oxidation, or even catastrophic failures like cracking, you know the stakes are high. This article will delve into the precise parameters needed.
The world of copper alloy annealing1 is intricate, with each alloy family presenting unique challenges and requiring tailored approaches. Simply applying a one-size-fits-all method can lead to detrimental outcomes, impacting everything from the material's formability and strength to its corrosion resistance and surface finish. At AKS Furnace, we've seen firsthand how nuanced control, backed by robust furnace technology featuring energy-saving systems and precision gas-to-air ratio control, can transform an unpredictable process into a reliable one. For instance, a client processing high-conductivity copper components was experiencing variations in electrical performance due to inconsistent annealing. By refining their process with a furnace offering tighter temperature uniformity (often ±3-5°C in our designs) and controlled atmospheres, they achieved the consistent metallurgical structure necessary for their demanding application. This highlights that success isn't just about knowing the temperatures; it's about understanding the interplay of all variables and having the right equipment to manage them.
What are the key factors to consider when annealing copper alloys?
Finding your copper alloys are either too hard after annealing, or perhaps too soft and grainy, leading to production headaches? This often stems from overlooking critical process variables. At AKS, we believe understanding these factors is the first step to consistent, high-quality annealing.
Key factors for annealing copper alloys include the specific alloy composition (e.g., pure copper, brass, cupronickel), the amount of prior cold deformation, the target grain size and mechanical properties, the annealing temperature, soak time, heating/cooling rates, and the furnace atmosphere's composition.
Successfully annealing copper alloys is a balancing act. It's not just about heating the metal; it's about precisely controlling a transformation that dictates the final product's performance. The alloy's composition is paramount – pure copper behaves differently than a complex brass or a robust cupronickel. Each alloying element, be it zinc in brasses or nickel in cupronickels, alters the material's recrystallization behavior, influencing the required temperature and time. For example, the zinc content in brass significantly affects its annealing range and susceptibility to dezincification if the atmosphere isn't carefully controlled. Similarly, nickel in cupronickel alloys raises the annealing temperature and demands specific atmospheric conditions to prevent nickel oxide formation, which is harder to reduce than copper oxide.
The amount of prior cold work the material has undergone is another crucial determinant. A heavily cold-worked piece will recrystallize at a lower temperature or in a shorter time than a lightly worked one. This is because the stored energy from deformation acts as a driving force for recrystallization. Overlooking this can lead to either incomplete annealing, leaving the material harder than desired, or excessive grain growth if the temperature/time is too high for the given cold work, resulting in reduced strength and poor surface finish (orange peel effect) after forming. At AKS Furnace, our clients, particularly those in metal strip processing or wire drawing, rely on our Bright Annealing Furnaces with precise tension and speed control to handle materials with varying degrees of cold work, ensuring uniform properties. Our furnaces, equipped with advanced cooling systems, also play a vital role in controlling the cooling rate, which can be critical for preventing thermal shock and maintaining dimensional stability, especially for intricate parts. The desired final grain size and mechanical properties (like tensile strength, yield strength, and elongation) dictate the annealing regime. A fine grain size generally offers a good combination of strength and ductility, while a coarser grain size might be preferred for deep drawing operations but can compromise strength. Achieving this target requires meticulous control over both temperature and soak time.
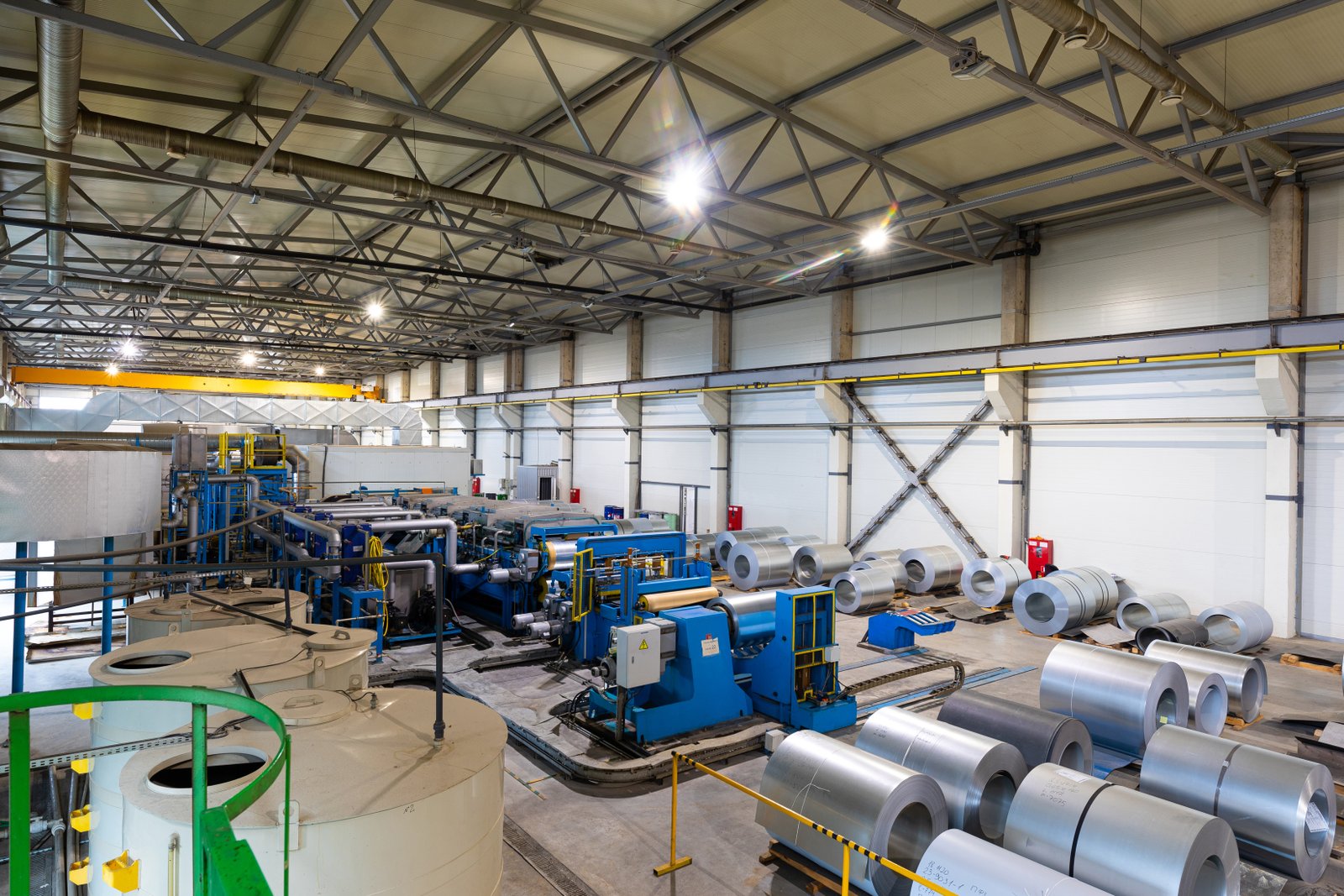
The furnace atmosphere is the unsung hero of bright annealing. For copper and its alloys, preventing oxidation is key to achieving a bright, clean surface, minimizing post-annealing cleaning processes, and preserving the material's intrinsic properties. This is where our expertise in designing furnaces with excellent sealing and precise atmosphere control systems—managing everything from nitrogen and hydrogen to dissociated ammonia—comes into play. Our systems, featuring precision control of gas-to-air ratio, ensure complete combustion in gas-fired models or clean environments in electrically heated ones, maximizing energy efficiency while protecting the product. For instance, a client manufacturing high-quality copper tubes for HVAC systems significantly reduced their rejection rates due to surface defects after upgrading to an AKS furnace with an optimized inert gas system. The waste heat recovery systems integrated into many of our furnace designs further enhance operational efficiency, reducing energy consumption and contributing to a more sustainable manufacturing process. This holistic approach, considering every factor from material science to furnace engineering, is what enables us to help our customers achieve consistent, high-quality annealing results.
The Profound Impact of Alloy Composition on Annealing Parameters
The specific chemical makeup of a copper alloy is arguably the most fundamental factor influencing its annealing behavior. Pure copper, for instance, has a relatively straightforward annealing response, primarily governed by its purity level. However, the introduction of alloying elements like zinc (in brasses), nickel (in cupronickels), tin (in bronzes), or aluminum (in aluminum bronzes) significantly alters the material's recrystallization temperature, the rate of grain growth, and its interaction with the furnace atmosphere. Each element brings its own set of characteristics that must be carefully managed.
Consider brasses (Cu-Zn alloys): as zinc content increases, the annealing temperature generally decreases, but the susceptibility to dezincification (preferential loss of zinc from the surface) in certain atmospheres or at higher temperatures becomes a major concern. For example, a 70/30 brass (C26000) will have different optimal annealing parameters and atmospheric requirements than a 90/10 brass (C22000). A client of ours producing intricate brass connectors for the electronics industry initially faced issues with inconsistent hardness and occasional surface dullness. After a detailed process audit, we identified that their existing furnace lacked the precise atmospheric control needed for the specific brass alloy they were using. Switching to an AKS Bell-Type Annealing Furnace, known for its gas-tight operation and ability to maintain a highly controlled protective atmosphere, allowed them to consistently achieve the desired bright finish and mechanical properties, significantly reducing their reject rate. This furnace also incorporated our energy-saving system, which provided them with a noticeable reduction in operational costs.
Cupronickel alloys (Cu-Ni) present another distinct set of challenges. Nickel significantly raises the annealing temperature compared to pure copper or brasses. A 90/10 cupronickel (C70600) might anneal in the range of 650-800°C, while a 70/30 cupronickel (C71500) typically requires 750-900°C. The presence of nickel also makes these alloys more prone to forming tenacious nickel oxides if the atmosphere is not sufficiently reducing. We worked with a manufacturer of marine components who needed to anneal large cupronickel plates. Their primary challenge was achieving uniform heating and preventing oxidation across these large surfaces. We supplied a custom-designed Bogie Hearth Annealing Furnace with multiple control zones for precise temperature uniformity and a robust hydrogen-based atmosphere system, which successfully addressed their quality requirements. The furnace's design also incorporated our waste heat recovery technology, making their high-temperature process more energy-efficient.
Balancing Time and Temperature for Optimal Mechanical Properties
The interplay between annealing temperature and soak time is a delicate dance crucial for achieving the desired mechanical properties and microstructure. For any given copper alloy and level of prior cold work, there isn't a single "correct" temperature; rather, there's a range, and within that range, temperature and time are inversely related. A higher temperature will achieve recrystallization and grain growth faster than a lower temperature. The goal is to ensure complete recrystallization, which restores ductility, without allowing excessive grain growth, which can reduce strength and lead to issues like "orange peel" during subsequent forming operations.
For instance, looking at C11000 ETP (Electrolytic Tough Pitch) copper, if it's been heavily cold-worked (e.g., 60% reduction in area), it might fully recrystallize within an hour at around 350-400°C, yielding a fine grain structure. However, if the same material is annealed at 600°C, the soak time might be reduced to mere minutes, but there's a higher risk of rapid grain coarsening if the time isn't precisely controlled. One of our customers, a producer of copper strips for electrical connectors, needed to achieve a specific balance of conductivity, strength, and formability. They were using an older continuous furnace with limited zone control. We helped them upgrade to one of our multi-zone Bright Annealing Furnaces. This furnace, featuring our precision control systems, allowed them to implement a carefully profiled heating and soaking curve. Data from their trials showed that by maintaining a temperature of 480°C ±5°C for a specific line speed (translating to an effective soak time of 15 minutes), they consistently achieved an ASTM grain size of 6-7, meeting their tight specifications. Conversely, accidental overheating to 550°C in their old furnace had previously resulted in grain sizes of ASTM 4-5, leading to cracking during stamping.
The choice also depends on the desired end properties. If maximum softness and ductility are required, a higher temperature or longer time (leading to a slightly coarser grain size) might be acceptable. If a balance of strength and ductility is needed, or if fine grain size is critical for fatigue resistance or surface finish, then lower temperatures and carefully controlled shorter times are preferred. Our advanced cooling systems also play a part here, ensuring that the cooling rate after soaking doesn't introduce new stresses or unwanted phase transformations, particularly in more complex alloys. For batch operations, like those handled by our Bell-Type or Bogie Hearth Annealing Furnaces, ensuring uniform temperature throughout the entire load during the soak period is critical, often requiring sophisticated air circulation systems within the furnace chamber.
The Critical Role of Furnace Atmosphere and Prior Cold Work
The furnace atmosphere during annealing is not just a passive environment; it actively interacts with the metal surface and can significantly influence the final product quality. For copper and its alloys, the primary goal is often to achieve a "bright anneal," meaning the surface remains clean, shiny, and free of oxides. This requires a protective atmosphere that prevents oxygen from reacting with the copper or other alloying elements. Common protective atmospheres include dissociated ammonia (a mix of hydrogen and nitrogen), pure nitrogen, pure hydrogen (for specific applications), or exothermic/endothermic gases with controlled reducing potential. The choice depends on the alloy, cost, safety considerations, and desired surface finish. For example, while pure copper can be bright annealed in relatively lean reducing atmospheres, brasses require careful control to prevent zinc volatilization, and cupronickels need strongly reducing conditions to avoid nickel oxide formation. One client producing high-quality copper foils for electronics using our Vacuum Annealing Furnace achieved an exceptionally clean and bright surface, critical for their application, by annealing under a high vacuum which eliminates virtually all reactive gases.
The degree of prior cold work is intimately linked to the annealing process. Cold working introduces dislocations and strain energy into the metal's crystal lattice. This stored energy is the driving force for recrystallization. The higher the amount of cold work, the lower the temperature or shorter the time required to initiate and complete recrystallization. For example, a copper strip with 10% cold reduction might require an annealing temperature of 500°C to fully soften, while the same material with 60% cold reduction might achieve the same result at 350°C. This relationship is critical for process optimization. If the level of cold work varies within a batch or between batches, but the annealing parameters remain constant, the final properties will be inconsistent. This is why manufacturers often aim for consistent cold reduction levels before the final anneal. Our Mesh Belt Furnaces are popular for continuous annealing of small parts or strips where consistent input material condition is vital for uniform output. These furnaces ensure that each part experiences the same thermal cycle.
Furthermore, the initial grain size before cold working and the amount of cold work itself influence the final annealed grain size. Generally, a higher degree of cold work and a lower annealing temperature (or shorter time) will result in a finer recrystallized grain size. This is often desirable for improved strength and formability. Conversely, light cold work followed by high-temperature annealing can lead to very coarse grains. Understanding this interplay allows manufacturers to tailor their entire process chain – from casting through rolling/drawing to final annealing – to achieve specific microstructural and mechanical property targets. The table below illustrates how prior cold work can affect the recrystallization temperature for a common brass alloy, C26000 (Cartridge Brass, 70% Cu, 30% Zn). Note that these are typical ranges and can be influenced by other factors like initial grain size and impurities.
% Cold Work (Reduction in Area) | Typical Recrystallization Start Temp. (°C) for C26000 Brass | Typical Full Anneal Temp. Range (°C) for C26000 Brass (1 hour soak) |
---|---|---|
10% | ~375-425 | 550-650 |
30% | ~325-375 | 475-575 |
60% | ~275-325 | 425-525 |
80% | ~250-300 | 400-500 |
This data underscores the necessity of knowing your material's history and precisely controlling the annealing conditions. Our furnace designs, with their emphasis on uniform heat distribution and precise temperature and atmosphere control, empower our clients to navigate these complexities effectively.
Alloy composition affects annealing temperatureTrue
Different copper alloys (like brass vs cupronickel) require different annealing temperatures due to their unique chemical compositions.
All copper alloys anneal at same temperatureFalse
Brass (Cu-Zn) typically requires lower annealing temperatures than cupronickel (Cu-Ni) due to their different alloying elements.
How do you determine suitable temperatures for annealing pure copper?
Are you unsure about the right annealing temperature for your pure copper, risking either incomplete softening or detrimental grain growth? It's a common concern, but with the right approach, you can pinpoint the optimal range. At AKS, we guide clients to achieve consistent results.
Suitable annealing temperatures for pure copper (e.g., C10100, C11000 typically range from 300°C to 650°C (572°F to 1202°F), depending on the desired degree of softness, final grain size, extent of prior cold work, and soak time.
Determining the ideal annealing temperature for pure copper isn't a one-size-fits-all answer; it's a careful calibration of several interconnected factors. Pure copper, known for its excellent electrical and thermal conductivity and ductility, undergoes recrystallization to relieve internal stresses and restore formability after being cold worked. The primary goal is to achieve this recrystallization without inducing excessive grain growth, which can negatively impact mechanical properties and surface finish. The specific grade of pure copper also matters; for instance, Oxygen-Free High Conductivity (OFHC) copper2 (like C10100 or C10200) might have slightly different considerations, especially regarding atmosphere, compared to Electrolytic Tough Pitch (ETP) copper (like C11000) due to its susceptibility to hydrogen embrittlement if not handled correctly.
The extent of prior cold work is a major determinant: heavily cold-worked copper will recrystallize at lower temperatures or in shorter times compared to lightly worked material. For instance, copper that has undergone a 60% reduction in area might fully anneal at 350°C, while copper with only 20% cold work might require temperatures closer to 450-500°C for a similar degree of softening within a practical timeframe. Moreover, the desired final properties play a crucial role. If maximum softness for extreme forming operations is needed, a higher annealing temperature (e.g., 500-650°C) might be used, leading to a larger grain size. Conversely, if a finer grain size is required for better strength or surface finish after forming, lower temperatures (e.g., 300-450°C) and carefully controlled soak times are preferred. We've assisted clients in the electronics sector who require fine copper wires with specific temper and grain structure; for them, precise control within a narrow temperature window using our Bright Annealing Furnaces is paramount to ensure consistent electrical and mechanical performance. The furnace's ability to maintain uniform temperature and a protective atmosphere is key to achieving these exacting standards.
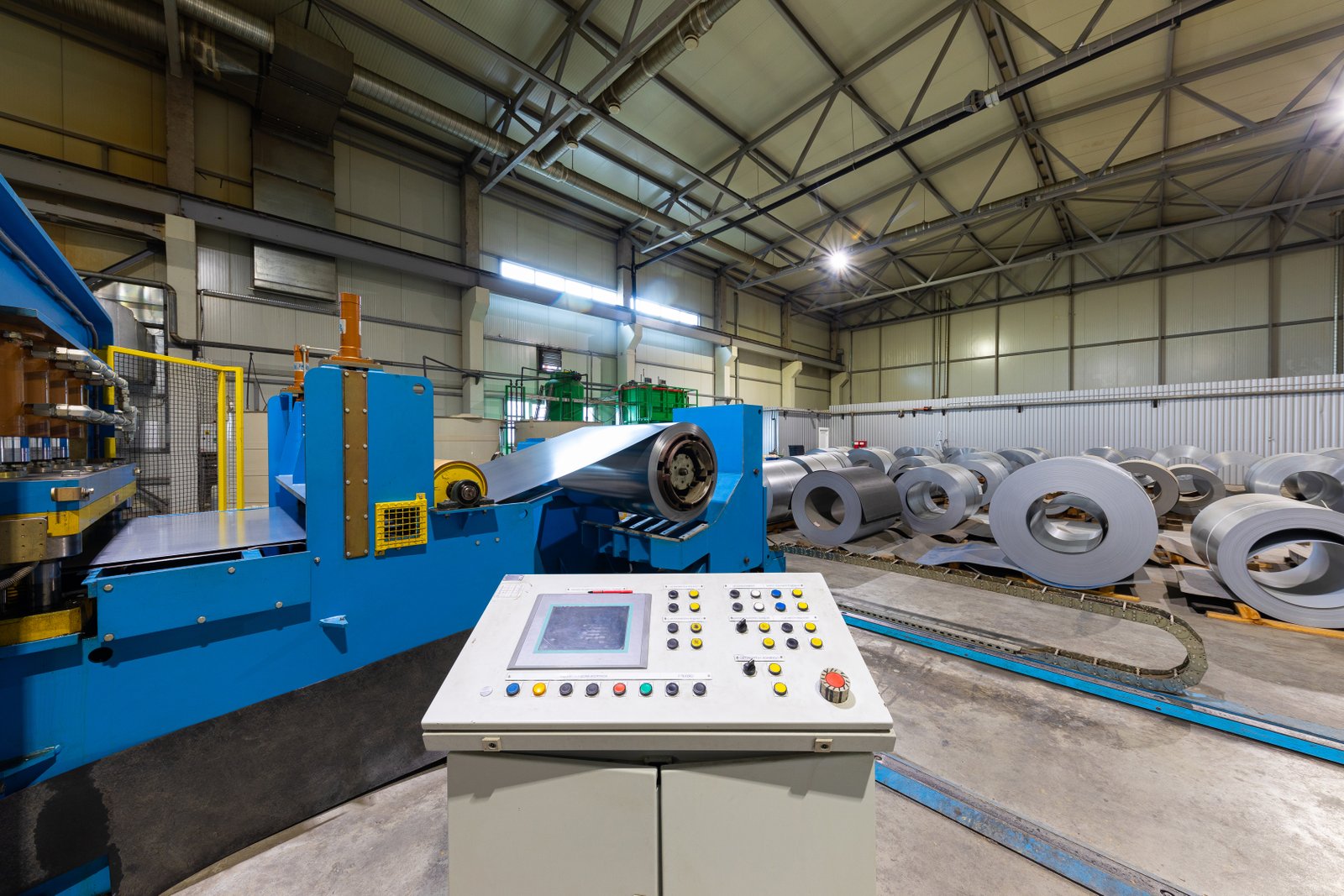
The soak time at the chosen temperature is another critical variable. Generally, higher temperatures require shorter soak times, while lower temperatures necessitate longer soaks to achieve complete recrystallization. It's a trade-off that also considers production throughput. For continuous annealing processes, such as those in our Mesh Belt Furnaces used for small copper components or strips, the line speed directly translates to soak time within different heating zones. These furnaces are designed with multiple, independently controlled heating zones to create precise temperature profiles—heating, soaking, and cooling—optimizing the process for both quality and efficiency. Our advanced cooling systems ensure that the copper is cooled at a controlled rate, preventing re-oxidation and maintaining the bright surface achieved in the protective atmosphere. For batch processes, like annealing copper coils in one of our Bell-Type Annealing Furnaces, ensuring the entire load reaches and maintains the target temperature uniformly is critical. This is achieved through robust furnace design, including efficient air circulation systems and precise temperature sensors. The energy-saving systems in our furnaces also contribute to cost-effective operation, particularly for the longer cycles sometimes associated with lower temperature annealing or large batch sizes. Ultimately, determining the suitable temperature involves a combination of understanding these metallurgical principles, empirical testing (often starting with established guidelines and refining based on results), and utilizing equipment that offers the necessary precision and control.
Understanding Recrystallization in Pure Copper (e.g., C11000 ETP Copper)
Recrystallization is the core metallurgical phenomenon we harness during annealing. For pure copper like C11000 (Electrolytic Tough Pitch copper), which is widely used for its excellent electrical conductivity and formability, cold working (such as rolling, drawing, or stamping) introduces a high density of dislocations and internal stresses. This makes the copper harder, stronger, but less ductile. Recrystallization is a process where, upon heating to a sufficient temperature, these strained, deformed grains are replaced by new, stress-free grains. This restores ductility and softness, making the copper suitable for further processing or its final application.
The temperature at which recrystallization begins and the rate at which it proceeds are highly dependent on the amount of prior cold work and the purity of the copper. For heavily cold-worked C11000 copper (e.g., >50% reduction), recrystallization can technically start at temperatures as low as 200°C (392°F). However, for practical annealing purposes, where a complete transformation is desired within a reasonable timeframe, temperatures typically range from 320°C to 650°C (608°F to 1202°F). Lower temperatures within this range (e.g., 320-450°C) will result in a finer recrystallized grain size, while higher temperatures (e.g., 500-650°C) will lead to coarser grains and more rapid softening. It's crucial to understand that time at temperature is as important as the temperature itself. A short soak at a high temperature can achieve the same degree of recrystallization as a longer soak at a lower temperature. We often advise clients, such as a manufacturer of copper gaskets, that for applications requiring good formability and a fine grain structure to prevent surface roughness (orange peel effect), annealing in the lower end of the range with precise time control is preferable. Our Bright Annealing Furnaces, with their ability to maintain temperature uniformity often better than ±5°C and provide controlled atmospheres, are ideal for such precise operations.
Even small amounts of impurities in pure copper can significantly affect its recrystallization temperature and grain growth characteristics. Elements like silver, phosphorus, or arsenic, even in trace amounts, can raise the recrystallization temperature or inhibit grain growth. This is why the specific grade of copper (e.g., C10100 OFHC3 vs. C11000 ETP vs. C12200 DHP) must be considered. For example, phosphorus-deoxidized copper (DHP copper like C12200) generally has a higher recrystallization temperature than ETP copper. A client producing copper tubing for plumbing applications (often DHP copper) found that parameters that worked well for their ETP copper products resulted in incomplete annealing for DHP. By adjusting their process based on metallurgical data and utilizing the precise control of their AKS furnace, they were able to establish a new, effective annealing window for the DHP grade, ensuring consistent product quality. The advanced control systems in our furnaces allow for programmable recipes, making it easy to switch between parameters for different copper grades.
Selecting Annealing Temperatures for Specific Applications
The choice of annealing temperature for pure copper is not arbitrary; it's directly linked to the desired end-use characteristics of the material. Different applications demand different combinations of softness (ductility), strength, and grain structure, all of which are influenced by the annealing regimen. For instance, if the copper is intended for severe deep drawing or complex forming operations where maximum ductility is paramount, a "full anneal" or "soft anneal" is typically performed. This often involves temperatures in the higher range, say 500°C to 650°C (932°F to 1202°F), which ensures complete recrystallization and promotes some grain growth, leading to very low hardness and high elongation. A kitchenware manufacturer using our Bell-Type Annealing Furnaces for copper blanks destined for deep-drawn pots and pans targets this type of anneal to minimize cracking and ensure smooth forming.
Conversely, for applications where a certain level of residual strength is desirable, or where a very fine grain size is needed for improved fatigue resistance or a superior surface finish after light forming, a "partial anneal" or "light anneal" might be employed. This involves using temperatures at the lower end of the annealing range, perhaps 300°C to 450°C (572°F to 842°F), or very short soak times. This approach can achieve sufficient stress relief and recrystallization to restore some ductility without causing significant grain growth. For example, copper strips used in electrical springs or connectors might undergo such an anneal to retain some of the strength imparted by cold working while still allowing for some formability. We worked with an automotive supplier producing small copper terminals who needed this balance. Using our continuous Mesh Belt Furnace, they were able to precisely control the time-temperature profile to achieve a consistent "spring temper" in their copper parts, ensuring both reliable electrical contact and mechanical stability. The furnace's advanced cooling system was also critical in this application to set the desired properties quickly after annealing.
Grain size control is a significant aspect of selecting the annealing temperature. As a general rule, lower annealing temperatures and shorter times result in finer grain sizes, while higher temperatures and longer times lead to coarser grains. A fine grain structure (e.g., ASTM grain size 7-8) generally provides better tensile strength, fatigue strength, and a smoother surface after forming. Coarser grains (e.g., ASTM 3-5) offer better creep resistance at elevated temperatures and can sometimes be preferred for their extreme softness in certain forming operations, though they can lead to an "orange peel" surface defect if forming is severe. For most general-purpose applications requiring good formability and a decent surface finish, a medium grain size (ASTM 5-7) is often targeted, typically achieved by annealing ETP copper in the 400-550°C range. Our furnaces, with their emphasis on precision temperature control and uniformity, allow manufacturers to consistently hit these target grain sizes, which is often a key quality parameter specified by their customers.
Practical Considerations: Time, Atmosphere, and Cooling for Pure Copper
Beyond selecting the correct temperature, several practical considerations are vital for successful pure copper annealing, namely soak time, furnace atmosphere, and the cooling process. Soak time, the duration the copper is held at the peak annealing temperature, must be sufficient to ensure that the entire cross-section of the material reaches temperature and that recrystallization is complete. For thin sections or continuous strip annealing, soak times can be relatively short, often measured in minutes. For instance, in our continuous Bright Annealing Furnaces for copper strip, the line speed is precisely calibrated with the heated length of the furnace to achieve the optimal soak time, which might only be 2-5 minutes at 550-650°C. However, for heavy sections or large, densely packed batch loads, such as coils annealed in a Bell-Type Annealing Furnace, soak times can extend to several hours to ensure thermal equilibrium and complete microstructural transformation throughout the entire load. Under-soaking can lead to incomplete annealing, resulting in non-uniform properties, while excessive soaking, especially at higher temperatures, can cause undesirable grain coarsening.
The furnace atmosphere is critical for preventing oxidation and ensuring a bright, clean surface finish on the annealed copper. Pure copper is susceptible to oxidation at elevated temperatures, forming copper oxides (CuO and Cu₂O) that can discolor the surface and may need to be removed by pickling, adding cost and an extra processing step. To prevent this, annealing is typically carried out in a protective atmosphere. For ETP copper (C11000), common atmospheres include dissociated ammonia (a mixture of ~75% hydrogen and ~25% nitrogen), nitrogen-hydrogen mixtures (typically 2-10% H₂ in N₂), or sometimes steam for specific applications. It is crucial that these atmospheres have a low dew point (i.e., are very dry) to be effective. A client producing high-purity copper components for vacuum systems uses one of our Vacuum Annealing Furnaces, which provides the ultimate protective environment by removing virtually all gases, ensuring an exceptionally clean, oxide-free surface. For OFHC (Oxygen-Free High Conductivity) copper (C10100/C10200), it's especially important to avoid atmospheres containing hydrogen if the copper has not been properly deoxidized, as this can lead to hydrogen embrittlement. However, commercially available OFHC copper is typically deoxidized, making hydrogen-bearing atmospheres generally safe and effective. Our furnace systems include precise gas flow control and monitoring to maintain the integrity of the protective atmosphere.
Controlled cooling after the soak period is the final crucial step. The cooling rate can influence the final properties and surface quality. Rapid cooling, facilitated by our Advanced Cooling Systems integrated into continuous lines or fan-assisted cooling in batch furnaces, can help to set the fine grain structure achieved during annealing and improve productivity. However, for some applications or very large sections, a slower, controlled cool-down might be necessary to prevent thermal shock or distortion. The cooling must also occur under the protective atmosphere until the copper is below a temperature where it will readily oxidize if exposed to air (typically below 150-200°C). Our Bright Annealing Furnaces are designed with extended cooling chambers where the protective atmosphere is maintained, ensuring that the copper emerges bright and clean. This attention to detail in the cooling phase is just as important as the heating and soaking stages for achieving high-quality annealed copper products.
Heavily cold-worked copper anneals at lower temperaturesTrue
Copper with greater prior cold work (e.g., 60% reduction) requires lower annealing temperatures (around 350°C) compared to lightly worked material, due to higher stored energy from deformation.
All copper grades anneal at identical temperaturesFalse
Different copper grades (e.g., OFHC vs ETP vs DHP) have varying recrystallization temperatures due to compositional differences - phosphorus-deoxidized copper (DHP) typically requires higher annealing temperatures than ETP copper.
What temperature ranges are optimal for Cu-Ni alloy annealing?
Are you facing challenges in annealing Cu-Ni alloys, perhaps struggling to achieve the right balance of strength and ductility, or dealing with unwanted surface oxidation? These robust alloys require specific attention. As your heat treatment specialist, I can help clarify their optimal annealing ranges.
Optimal annealing temperatures for Cu-Ni alloys (cupronickels), such as C70600 (90/10) and C71500 (70/30), generally fall between 650°C and 900°C (1200°F to 1650°F), varying significantly with nickel content and desired final properties.
Cupronickel alloys, renowned for their excellent corrosion resistance, particularly in marine environments, and good strength, require higher annealing temperatures compared to pure copper or brasses. The presence of nickel significantly elevates the recrystallization temperature and influences the alloy's behavior during heat treatment. The two most common grades, C70600 (90% copper, 10% nickel) and C71500 (70% copper, 30% nickel), have distinct annealing windows. Generally, C70600 is annealed in the range of 650°C to 800°C (1200°F to 1470°F), while C71500, with its higher nickel content, requires even higher temperatures, typically between 750°C and 900°C (1380°F to 1650°F). Selecting a temperature within these ranges depends on factors similar to other copper alloys: the amount of prior cold work, the desired final grain size, and the required mechanical properties (e.g., tensile strength, yield strength, elongation).
Achieving full recrystallization is crucial for cupronickels to optimize their corrosion resistance and ductility. Incomplete annealing can leave residual stresses and a non-uniform microstructure, which can be detrimental to performance, especially in demanding applications like heat exchanger tubing, shipbuilding, or desalination plant components. At AKS Furnace, we've worked with manufacturers of such critical components. For instance, a client producing C71500 tubing for naval applications needed to ensure complete softening and a specific fine-to-medium grain structure for optimal performance. Using one of our precision-controlled Bright Annealing Furnaces, capable of maintaining tight temperature uniformity even at these higher temperatures and equipped with a strongly reducing atmosphere (often a hydrogen-rich mixture), they were able to consistently meet these stringent specifications. The furnace's energy-saving design, incorporating waste heat recovery, was also a key benefit for them, given the higher energy demands of annealing cupronickels. The robust construction of our furnaces ensures longevity and reliability even under these more demanding high-temperature conditions.
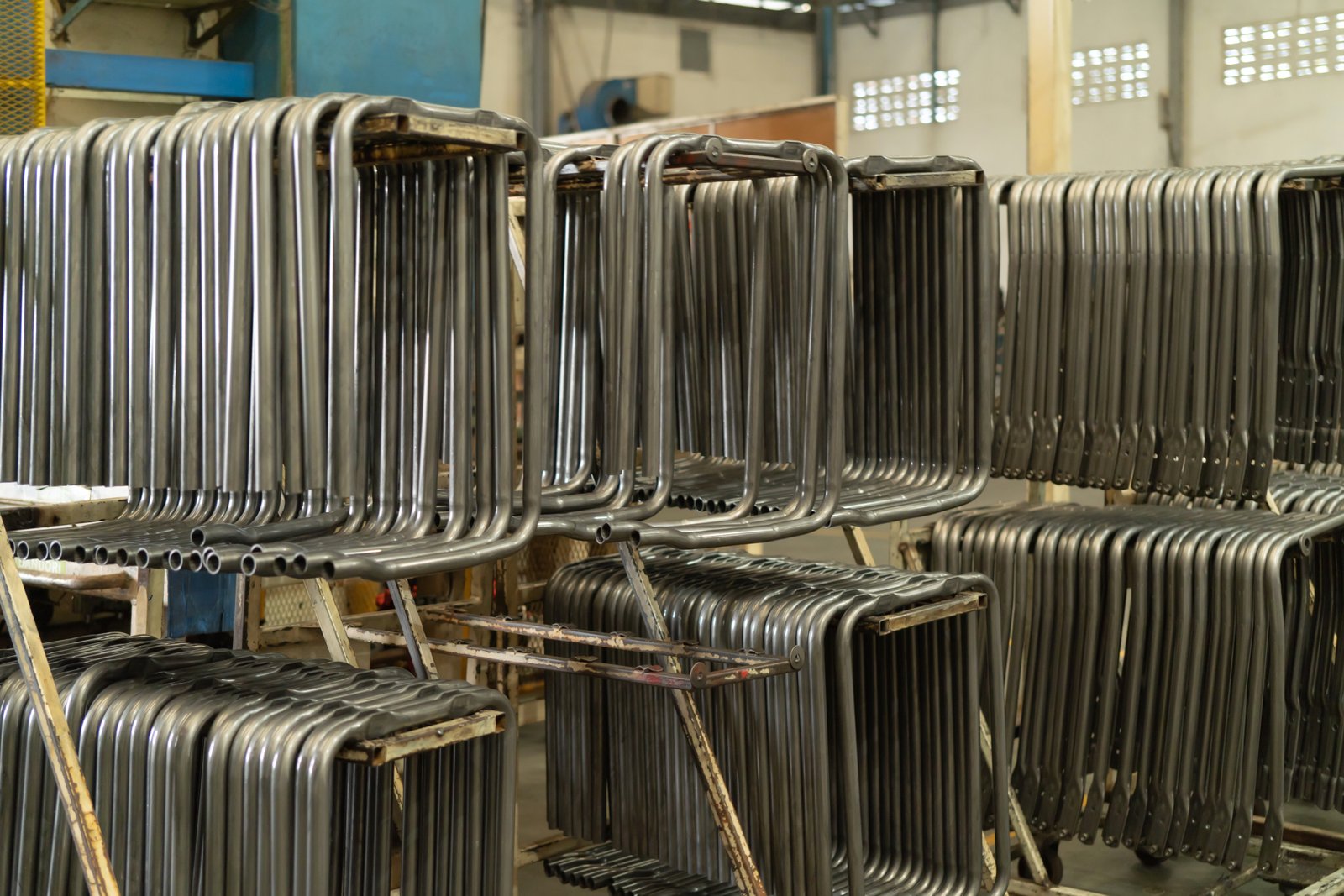
The choice of temperature within the optimal range also influences grain size. As with other alloys, higher temperatures or longer soak times will lead to coarser grains. While this maximizes softness, an excessively coarse grain structure can sometimes reduce fatigue strength or lead to a less desirable surface finish after forming. Therefore, a balance must be struck. For many cupronickel applications, a fully recrystallized structure with a controlled, relatively fine grain size is preferred. This requires precise control over both the annealing temperature and the soak time. Our continuous annealing lines, such as Mesh Belt Furnaces or roller hearth furnaces, are designed with multiple heating and soaking zones, allowing for very precise thermal profiles. This ensures that the material is brought to temperature efficiently, soaked uniformly, and then cooled under a protective atmosphere using our advanced cooling systems to preserve the bright, clean surface. The protective atmosphere is particularly important for cupronickels because nickel readily oxidizes at elevated temperatures, and nickel oxide is more difficult to remove than copper oxide. A dry, reducing atmosphere, such as cracked ammonia or a nitrogen-hydrogen blend with a sufficiently high hydrogen content, is essential to prevent oxidation and ensure a bright finish, minimizing or eliminating the need for post-annealing pickling.
Influence of Nickel Content on Annealing Temperatures
The nickel content in cupronickel alloys is the primary determinant of their annealing temperature range. Nickel, when alloyed with copper, forms a solid solution that significantly increases the material's strength and elevates its recrystallization temperature. This effect is quite pronounced: the more nickel present, the higher the temperature required to achieve full softening and recrystallization after cold working. This is a fundamental principle that guides the selection of annealing parameters for different cupronickel grades.
For example, C70600 alloy, commonly known as 90/10 cupronickel, contains approximately 10% nickel. It typically undergoes full annealing in a temperature range of 650°C to 800°C (approximately 1200°F to 1470°F). In contrast, C71500 alloy, or 70/30 cupronickel, with its 30% nickel content, requires a considerably higher annealing temperature range, generally between 750°C and 900°C (approximately 1380°F to 1650°F). This difference of over 100°C in the typical annealing ranges for these two common alloys highlights the potent effect of nickel. Data from metallurgical handbooks confirms this trend; for a similar amount of prior cold work (e.g., 50% reduction), the temperature to achieve complete recrystallization in one hour for C71500 can be 100-150°C higher than for C70600. A client of ours specializing in manufacturing components for marine cooling systems works with both 90/10 and 70/30 cupronickel tubes. They utilize one of our versatile Bogie Hearth Annealing Furnaces, which is capable of precise temperature control across a wide range. This flexibility allows them to switch between annealing cycles optimized for each alloy, ensuring consistent quality. The furnace's robust insulation and energy-efficient design are particularly beneficial when operating at the higher temperatures required for 70/30 cupronickel.
The reason for this increase in annealing temperature with higher nickel content lies in atomic-level interactions. Nickel atoms, being slightly different in size from copper atoms, create lattice distortions and have different diffusion characteristics within the copper matrix. This makes dislocation movement (the basis of plastic deformation) more difficult, hence increasing strength, and also requires more thermal energy (higher temperature) to enable the atomic rearrangement necessary for recrystallization and grain growth. Furthermore, nickel's higher melting point compared to copper also contributes to the increased thermal stability of cupronickel alloys, necessitating higher annealing temperatures. Understanding this direct correlation between nickel content and annealing temperature is the first step in successfully processing these valuable alloys. Our furnace designs at AKS always consider the specific temperature ranges required by our clients' materials, ensuring that the heating elements, insulation, and control systems are appropriately specified for optimal performance and longevity, especially for high-temperature applications like cupronickel annealing.
Achieving Desired Mechanical Properties and Corrosion Resistance
For cupronickel alloys, annealing is not just about restoring ductility; it's critically important for optimizing their renowned corrosion resistance, especially in aggressive environments like seawater. A proper anneal ensures a homogenous, stress-free microstructure, which is less susceptible to localized corrosion mechanisms such as stress corrosion cracking or preferential attack. Therefore, achieving full recrystallization is paramount. Incompletely annealed cupronickel, which may retain some internal stresses or a partially deformed grain structure, can exhibit significantly reduced corrosion performance. This is particularly true for applications like ship hulls, heat exchanger tubes in desalination plants, or offshore platform piping, where material integrity is non-negotiable.
The balance between strength and ductility is carefully managed through the annealing temperature and time. While higher temperatures within the annealing range will ensure complete recrystallization and maximize softness, they can also lead to coarser grain sizes. A coarser grain structure might be acceptable for some applications, but for others requiring better fatigue resistance or improved toughness, a finer, more uniform grain size is preferred. This is typically achieved by annealing at the lower end of the appropriate temperature range for the specific alloy, or by using shorter soak times at slightly higher temperatures, always ensuring full recrystallization. We worked with a manufacturer of high-pressure cupronickel fittings who needed to achieve a specific yield strength and elongation to meet stringent industry standards. Through controlled trials using one of our Bright Annealing Furnaces with precise multi-zone temperature control and atmosphere management, they were able to fine-tune their annealing process for C71500 alloy to consistently achieve a grain size of ASTM 4-6, which provided the optimal balance of mechanical properties and corrosion resistance for their product. Our furnace's advanced cooling system also played a role in rapidly cooling the parts under a protective atmosphere, preventing undesirable precipitation and maintaining surface quality.
The homogeneity of the microstructure achieved through annealing is also vital. Cupronickel alloys are single-phase solid solutions, and a uniform distribution of nickel within the copper matrix is essential for consistent properties. Proper annealing helps to ensure this homogeneity. Any significant segregation or the presence of secondary phases (which are generally not an issue in standard Cu-Ni alloys if processed correctly) could compromise both mechanical integrity and corrosion performance. Data from various studies shows a direct link between a fully recrystallized, homogenous microstructure and the superior pitting and crevice corrosion resistance of cupronickel alloys in chloride-containing environments. This underscores the importance of not just reaching the target temperature, but ensuring uniform heating and adequate soaking time throughout the entire material load, a key design feature of AKS industrial furnaces, from continuous strip lines to large batch furnaces.
Atmosphere and Cooling Considerations for Cu-Ni Alloys
The furnace atmosphere during the annealing of cupronickel alloys is a critical process parameter that directly impacts the surface quality and, potentially, the subsurface integrity of the material. Both copper and nickel can oxidize at elevated annealing temperatures, but nickel oxide (NiO) is more stable and tenacious than copper oxides. If a sufficiently protective atmosphere is not maintained, a dark, adherent scale can form, which is difficult to remove and can detract from the alloy's appearance and performance. Therefore, annealing cupronickels almost invariably requires a reducing atmosphere to prevent oxidation and, ideally, to slightly reduce any existing surface oxides, resulting in a bright, clean finish.
The most common protective atmospheres for annealing cupronickels are those rich in hydrogen, such as dissociated ammonia (DA), which provides a mix of approximately 75% H₂ and 25% N₂, or a blend of pure hydrogen and nitrogen. The hydrogen content needs to be sufficient to create a reducing potential that overcomes the tendency for nickel and copper to oxidize at the annealing temperature. It's also crucial that the atmosphere is dry (low dew point), as moisture can be oxidizing at high temperatures. One of our clients, a producer of cupronickel strip for coinage, utilizes an AKS Bright Annealing Furnace equipped with a high-purity nitrogen-hydrogen atmosphere system. This system includes precise gas mixing capabilities and continuous monitoring of dew point and oxygen levels, ensuring an optimal bright annealing environment. For particularly sensitive applications or very high-purity requirements, Vacuum Annealing Furnaces can also be an excellent choice for cupronickels, as they provide an environment virtually free of any reactive gases.
Another important consideration, especially when using atmospheres containing hydrogen, is the potential for intergranular attack if sulfur is present, either from contaminants on the material surface (e.g., residual drawing lubricants) or from impurities in the furnace atmosphere or refractories. Sulfur can react with nickel at high temperatures, leading to the formation of low-melting-point nickel sulfide (Ni₃S₂) at grain boundaries, which can cause embrittlement or "hot shortness." Therefore, meticulous cleaning of parts before annealing and ensuring a high-purity atmosphere are essential. Our furnace designs often incorporate features like metallic muffles or specific refractory material selections to minimize any potential contamination from the furnace itself. Controlled cooling after the soak period is also important. Rapid cooling is generally preferred to minimize the time spent in temperature ranges where undesirable precipitation or oxidation could occur if the protective atmosphere integrity is compromised during cooling. Our furnaces, whether batch or continuous, are designed with efficient cooling zones or systems that maintain the protective atmosphere until the material is below critical temperatures, ensuring the annealed cupronickel parts emerge bright, clean, and with the desired properties.
Higher nickel requires higher annealing temperaturesTrue
The article clearly states that C71500 (70/30) requires higher annealing temperatures (750-900°C) than C70600 (90/10) (650-800°C) due to its higher nickel content.
Cupronickels anneal at same temperatures as pure copperFalse
The text explicitly mentions that cupronickels require higher annealing temperatures compared to pure copper or brasses due to nickel's effect on recrystallization temperature.
Which specific parameters ensure safe annealing of Cu-Zn alloys?
Worried about issues like dezincification or the dreaded season cracking when annealing your brass (Cu-Zn) components? These are valid concerns with brasses, but understanding and controlling specific parameters can ensure a safe and successful anneal. Let me share some insights from our experience at AKS.
Safe annealing of Cu-Zn alloys (brasses) hinges on precise temperature control (typically 425°C to 700°C), a carefully managed furnace atmosphere to prevent dezincification (zinc loss), and controlled heating/cooling rates to avoid stress-induced cracking, especially in high-zinc brasses.
Annealing brass alloys, which are essentially alloys of copper and zinc, presents unique challenges primarily due to the relatively high vapor pressure of zinc. If the temperature is too high or the atmosphere is not controlled, zinc can preferentially evaporate from the surface, a phenomenon known as dezincification. This not only changes the alloy composition at the surface, potentially affecting its color, corrosion resistance, and mechanical properties, but can also lead to a porous, weakened surface layer. Therefore, temperature control is paramount. The optimal annealing temperature range for brasses varies significantly with zinc content. For instance, low-zinc brasses like red brass (C23000, ~15% Zn) might be annealed between 550-700°C, while common yellow brass or cartridge brass (C26000, ~30% Zn) is typically annealed between 425-675°C. Alpha-beta brasses, like Muntz metal (C28000, ~40% Zn), have more complex annealing behavior due to phase transformations and are often annealed in the 425-600°C range to primarily affect the alpha phase.
Beyond temperature, the furnace atmosphere4 plays a crucial role in preventing dezincification and ensuring a good surface finish. While strongly reducing atmospheres might seem ideal, they can sometimes exacerbate zinc loss if not carefully managed. Often, a slightly reducing or neutral atmosphere, such as that produced by combusted fuel gas with controlled oxygen content, nitrogen, or even steam for certain applications, is preferred for brasses. The goal is to minimize both oxidation and zinc volatilization. We've assisted clients, like a manufacturer of brass ammunition casings, in optimizing their continuous annealing process in one of our Mesh Belt Furnaces. By carefully controlling the gas composition and dew point in the furnace atmosphere, along with precise temperature zoning, they were able to achieve consistent mechanical properties and a clean surface finish, minimizing downstream cleaning operations. The energy-saving features of our furnaces also helped them manage the operational costs associated with maintaining these specific atmospheric conditions.
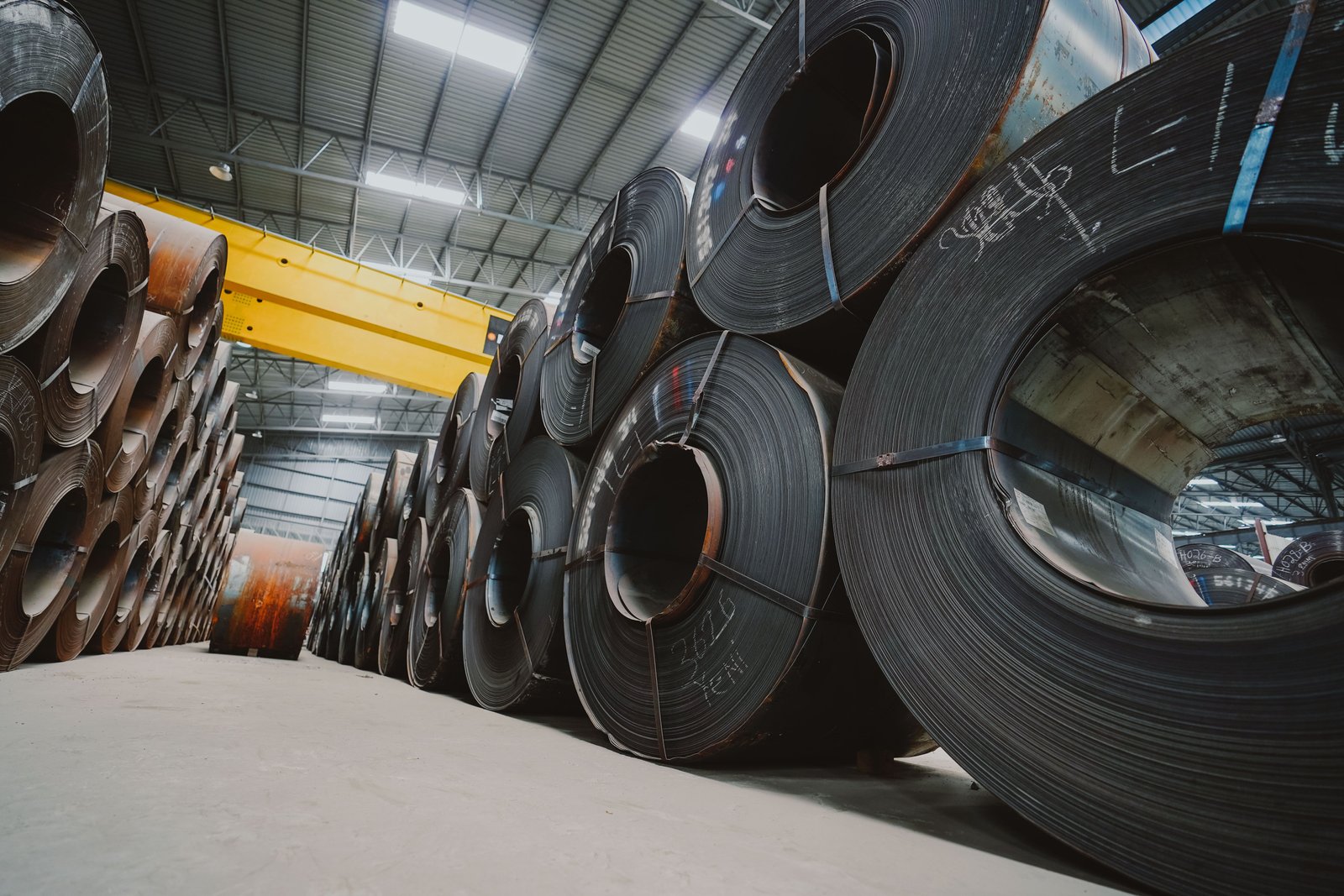
Another critical aspect of safely annealing brasses, particularly those with higher zinc content or those that have been heavily cold-worked, is managing internal stresses to prevent "season cracking" or stress corrosion cracking. These phenomena occur when susceptible alloys with high residual tensile stresses are exposed to certain corrosive environments (even mild ones like atmospheric ammonia). A proper annealing cycle effectively relieves these internal stresses. This often involves not just reaching the target annealing temperature but also employing controlled heating and cooling rates. Slow, uniform heating can be beneficial for heavily stressed parts to allow stresses to dissipate gradually. Similarly, controlled cooling, especially through critical temperature ranges, can prevent the reintroduction of thermal stresses. Our furnace designs, including Bogie Hearth Annealing Furnaces for large brass components or Bell-Type Annealing Furnaces for coils of brass strip, incorporate features for uniform heat distribution and programmable heating/cooling cycles. This precision control, a hallmark of AKS furnaces, is key to mitigating risks like season cracking and ensuring the long-term integrity of annealed brass products. Furthermore, our advanced cooling systems are designed to bring the material temperature down efficiently while still protecting it from oxidation or thermal shock.
Temperature Control to Prevent Dezincification and Excessive Grain Growth
Precise temperature control is arguably the most critical parameter in annealing copper-zinc alloys to prevent two major issues: dezincification and excessive grain growth. Dezincification, the selective loss of zinc from the surface of the brass, becomes a significant risk as annealing temperatures rise, particularly in brasses with higher zinc content (typically >20% Zn) and in atmospheres that are either oxidizing or too aggressively reducing without proper humidity control. This zinc loss not only alters the surface composition, leading to a copper-rich layer that can affect color and properties, but can also result in a porous, weakened surface. Therefore, it's crucial to operate within a temperature window that allows for full recrystallization without promoting significant zinc volatilization. For example, C26000 (70/30 Cartridge Brass) is commonly annealed between 425°C and 675°C (797°F to 1247°F). Operating towards the lower end of this range, perhaps 450-550°C, minimizes zinc loss but may require longer soak times. Data shows that annealing C26000 at 600°C for one hour typically yields a grain size of 0.035-0.050 mm, a common target for good formability. Pushing the temperature to 700°C, even for a shorter time, can significantly coarsen the grain and increase the risk of dezincification.
Simultaneously, the temperature must be high enough and held for a sufficient duration to achieve the desired degree of recrystallization and grain size. If the temperature is too low or the soak time too short, the brass may be incompletely annealed, retaining some of the hardness and internal stresses from prior cold working. This can lead to problems in subsequent forming operations or inadequate performance in service. Excessive grain growth, on the other hand, occurs if the temperature is too high or the soak time too long. Coarse grains in brass can lead to reduced tensile strength, poor fatigue properties, and an undesirable "orange peel" effect on the surface after forming. We once worked with a client producing decorative brass hardware who experienced surface roughness issues. An investigation revealed that their batch annealing furnace had poor temperature uniformity, leading to some parts being overheated and developing coarse grains. By upgrading to an AKS furnace with multi-zone control and enhanced air circulation, ensuring a temperature uniformity of ±5°C, they were able to achieve a consistent, fine grain structure (around 0.025 mm), which eliminated the orange peel problem and improved the aesthetic quality of their products.
The key is to find the sweet spot for the specific brass alloy and its intended application. This often involves careful process development, starting with recommended parameters from metallurgical handbooks and then refining them through empirical trials. For example, for C27000 (Yellow Brass, ~35% Zn), the annealing range is similar to C26000, but the propensity for dezincification might be slightly higher. Therefore, even more care is needed with temperature and atmosphere. Our precision control systems, often PLC-based with multiple thermocouple inputs, allow for very accurate temperature management and the programming of specific heating, soaking, and cooling profiles tailored to different brass alloys and product requirements. This level of control is fundamental to consistently achieving the desired microstructure while mitigating the risks associated with brass annealing.
Managing Stress Cracking (Season Cracking) and Achieving Homogeneity
Brasses, particularly those with higher zinc content (typically >15% Zn) and those subjected to significant cold work, are susceptible to a form of stress-corrosion cracking known as "season cracking." This phenomenon occurs when parts containing high residual tensile stresses are exposed to specific corrosive environments, even seemingly mild ones like atmospheres containing traces of ammonia (common in industrial or urban environments). The cracks are often intergranular and can lead to premature failure of components. One of the primary purposes of annealing brass, beyond softening it for further forming, is to relieve these internal stresses, thereby rendering the material immune or highly resistant to season cracking.
A full anneal, which involves heating to the recrystallization temperature range (e.g., 425-675°C for C26000 brass), is very effective at eliminating these stresses. However, for applications where maintaining a higher strength is desirable, a lower temperature stress relief anneal, typically in the range of 200-300°C (392-572°F), can be employed. This temperature is below that required for significant recrystallization but is sufficient to reduce residual stresses to a safe level without markedly decreasing the hardness and strength imparted by prior cold work. The choice between a full anneal and a stress relief anneal depends on the application's mechanical property requirements and the severity of the expected corrosive environment. We had a client manufacturing brass fasteners who faced occasional field failures due to season cracking. While their parts were being annealed, the process wasn't optimized for complete stress relief. We helped them implement a validated full annealing cycle in their AKS Mesh Belt Furnace, ensuring that every fastener experienced a uniform thermal treatment. This, coupled with careful control of heating and cooling rates to prevent the introduction of new thermal stresses, effectively eliminated the season cracking problem.
Achieving microstructural and thermal homogeneity throughout the annealed part or batch is also crucial. Non-uniform heating or cooling can lead to variations in grain size, hardness, and residual stress levels within a single component or across a batch of components. This can result in inconsistent performance during subsequent manufacturing steps or in the final application. For instance, if a large coil of brass strip is annealed in a Bell-Type furnace, it's essential that the inner and outer wraps of the coil reach the same temperature and are held for the same effective soak time. This is achieved in AKS Bell-Type furnaces through powerful atmosphere circulation fans and strategically placed heating elements, ensuring excellent temperature uniformity. Similarly, for continuous annealing of brass strip or wire, our Bright Annealing lines are designed with multiple, independently controlled heating zones to create a precise and repeatable thermal profile, ensuring that every section of the material receives the identical heat treatment. This focus on homogeneity is fundamental to producing high-quality, reliable annealed brass products.
Atmosphere Requirements and Post-Annealing Handling for Brasses
The furnace atmosphere during the annealing of brass alloys is a delicate balance. It must be controlled to minimize both the oxidation of copper and, more critically, the volatilization or preferential loss of zinc (dezincification). While a strongly reducing atmosphere (e.g., high hydrogen content) is excellent for preventing copper oxidation, it can sometimes accelerate zinc loss at higher annealing temperatures if not carefully managed, especially if the atmosphere is very dry. Therefore, for many brass annealing applications, a mildly reducing or neutral atmosphere is often preferred. Common choices include combusted fuel gas (exothermic or rich exothermic gas) where the air-to-fuel ratio is controlled to produce low levels of oxygen and controlled amounts of CO and H₂, or nitrogen-based atmospheres, sometimes with small additions of hydrogen (e.g., 1-5% H₂). Steam atmospheres have also been used historically for annealing brass, as the water vapor can help to suppress zinc volatilization to some extent by creating a specific surface partial pressure.
A common issue if the atmosphere is not correctly controlled is the formation of "red stains" on the surface of the brass. These stains are typically areas that have become enriched in copper due to localized dezincification. Maintaining a consistent atmosphere composition, dew point (moisture content), and furnace pressure is key to avoiding such defects and achieving a uniform surface appearance. At AKS Furnace, our equipment is designed with robust sealing and precise gas control systems. For example, our continuous Bright Annealing Furnaces for strip can incorporate atmosphere monitoring systems (e.g., oxygen analyzers, dew point sensors) that provide real-time feedback, allowing for automatic adjustments to maintain the optimal atmospheric conditions. This helps our clients, such as manufacturers of brass decorative items or musical instruments, achieve the consistent bright finish they require.
Depending on the specific brass alloy, the annealing parameters, and the quality of the atmosphere control, some light surface oxidation or tarnish may still occur. In such cases, a post-annealing pickling or bright dipping operation (typically using acid solutions) may be necessary to restore the desired surface luster. However, the goal of modern annealing practices, supported by advanced furnace technology like ours, is to minimize or eliminate the need for such post-processing. By achieving a "bright anneal" directly from the furnace, manufacturers can save on chemical costs, reduce processing time, and minimize environmental impact associated with pickling operations. Careful handling after annealing is also important to prevent surface damage or contamination, especially if the brass is intended for applications where appearance is critical or where it will undergo further surface treatments like plating. The table below provides typical annealing temperature ranges and resulting properties for C26000 (70/30 Cartridge Brass), illustrating the relationship between temperature, mechanical properties, and grain size. It's important to note that soak times are also critical and are usually determined based on material thickness and furnace type.
Annealing Temp (°C) for C26000 Brass | Typical Soak Time (for ~1mm thickness) | Approx. Tensile Strength (MPa) | Approx. Elongation (%) | Typical Grain Size (mm) | Common Applications/Notes |
---|---|---|---|---|---|
425-475 | 30-60 minutes | 340-380 | 45-55 | 0.015-0.025 | Fine grain, good strength, moderate formability |
500-575 | 30-60 minutes | 300-340 | 55-65 | 0.030-0.050 | Medium grain, good balance of properties |
600-675 | 15-45 minutes | 280-310 | 60-70 | 0.060-0.090 | Coarser grain, excellent formability, max. |
~250-300 | 60-120 minutes | (Varies with prior cold work) | (Slight increase) | (No significant change) | Stress relief anneal, reduces risk of season cracking |
This table emphasizes that the selection of annealing parameters for brass is a multi-faceted decision, aiming to optimize for the desired end properties while managing the inherent challenges of these versatile alloys.
Temperature controls dezincificationTrue
Precise temperature control between 425°C-700°C is essential to prevent zinc loss from brass surfaces during annealing.
Hydrogen prevents all dezincificationFalse
While hydrogen creates a reducing atmosphere, excessive hydrogen can actually accelerate zinc loss at high temperatures.
What are the steps to ensure uniformity and safety in the annealing process?
Are you concerned about achieving consistent results across your entire batch of annealed parts, or perhaps worried about the safety aspects of your heat treatment operations? These are crucial considerations for any manufacturer. At AKS, we prioritize both uniformity and safety in all our furnace designs and operational guidance.
Ensuring uniformity involves precise furnace temperature control, uniform heat distribution (e.g., via circulation fans, element placement), and consistent atmosphere management. Safety steps include rigorous furnace maintenance, comprehensive operator training, adherence to established safety protocols, and proper handling of protective atmospheres.
Achieving uniformity in the annealing process is fundamental to producing high-quality, reliable metal components. Variations in temperature, soak time, or atmosphere exposure across a load can lead to inconsistent microstructures, hardness levels, and mechanical properties. This, in turn, can result in unpredictable performance during subsequent manufacturing stages or in the final product. Imagine a batch of copper strips where some parts are perfectly soft while others remain partially hardened – this lack of uniformity can wreak havoc on stamping dies or lead to forming defects. To combat this, modern annealing furnaces, like those we design at AKS, incorporate several features. These include multiple, independently controlled heating zones, strategically placed heating elements or burners to ensure even heat input, and high-velocity atmosphere circulation fans5 (especially in batch furnaces like Bell-Type or Bogie Hearth models) to promote temperature homogeneity throughout the load. Our advanced PLC-based control systems continuously monitor and adjust temperatures based on feedback from numerous thermocouples placed strategically within the furnace chamber, often achieving temperature uniformity better than ±5°C, or even ±3°C for critical applications.
Safety in annealing operations cannot be overstated. We are often dealing with high temperatures, flammable or asphyxiant protective atmospheres, and heavy machinery. A comprehensive safety program begins with the furnace design itself. AKS furnaces are built with safety interlocks, emergency stop systems, over-temperature protection, and, where applicable, systems for the safe handling and purging of combustible atmospheres (like hydrogen or dissociated ammonia). For instance, our furnaces using flammable gases incorporate automated purge cycles with inert gas (like nitrogen) before the introduction of the flammable atmosphere and before opening the furnace after the cycle, to prevent explosive mixtures with air. Operator training is another cornerstone of a safe annealing process. Operators must be thoroughly trained on standard operating procedures (SOPs), emergency protocols, the correct use of personal protective equipment (PPE), and the specific hazards associated with the materials and atmospheres being used. We provide comprehensive training as part of our technical service when commissioning new furnace installations.
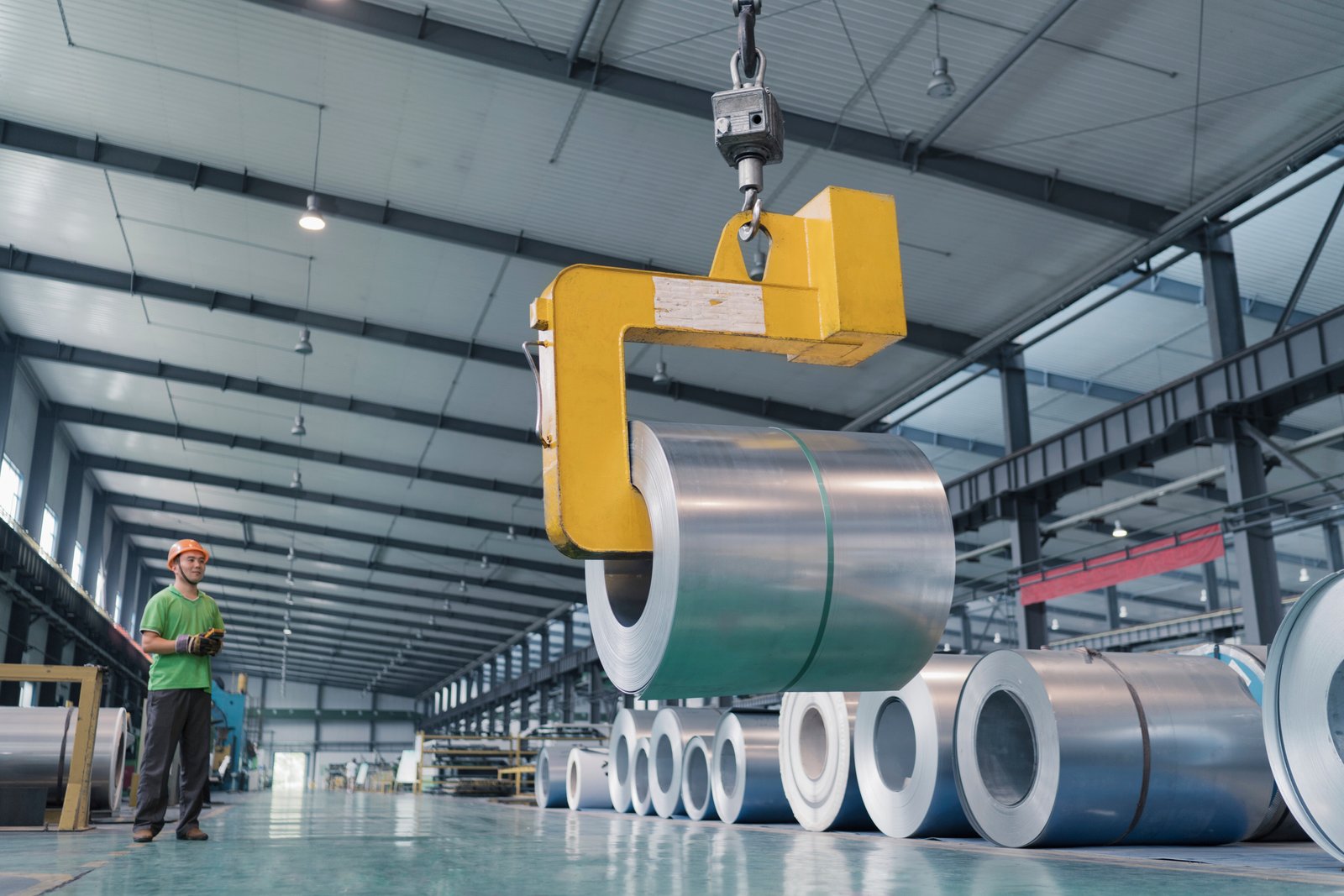
Regular and meticulous maintenance is also key to both uniformity and safety. A well-maintained furnace is more likely to perform consistently and less likely to pose a safety hazard. This includes routine checks of heating elements or burners, refractory linings, door seals, atmosphere control systems (gas analyzers, flow meters, safety valves), temperature sensors (thermocouples), and all safety interlocks. We provide detailed maintenance schedules and support for all our furnace types, from continuous Mesh Belt Furnaces to large-scale Bogie Hearth Annealing Furnaces. For example, ensuring that door seals are intact is critical for maintaining atmosphere integrity (which affects uniformity) and preventing leakage of potentially harmful gases (a safety concern). Similarly, calibrated thermocouples are essential for accurate temperature control, which directly impacts product quality. By implementing a robust preventive maintenance program, manufacturers can significantly reduce the risk of unexpected breakdowns, ensure consistent product quality, and maintain a safe working environment. This proactive approach, combining advanced furnace technology with rigorous operational and safety practices, is what allows our clients to anneal their copper, Cu-Ni, and Cu-Zn alloys uniformly and safely, day in and day out.
Achieving Temperature Uniformity and Precise Control
Achieving precise temperature uniformity throughout the entire workload is a cornerstone of successful annealing. If different parts of a load experience varying temperatures, the resulting metallurgical properties – such as grain size, hardness, and ductility – will be inconsistent. This can lead to significant problems in downstream processes or in the final product's performance. For instance, in a batch of copper wire coils annealed in a Bell-Type furnace, if the outer coils get hotter than the inner ones, you'll end up with wire of varying tempers. At AKS, our furnace designs prioritize temperature uniformity. This is achieved through a combination of strategic heating element placement (in electrically heated furnaces) or advanced burner design and positioning (in gas-fired furnaces), the use of high-quality insulation materials to minimize heat loss and cold spots, and often, the incorporation of powerful, heat-resistant circulation fans. These fans force the furnace atmosphere to move vigorously around and through the load, promoting convective heat transfer and equalizing temperatures. For many of our furnaces, especially those for critical applications like aerospace or electronics, we can guarantee temperature uniformity of ±5°C or even better (e.g., ±3°C) within the working zone.
The sophistication of the control system is equally important. Modern annealing furnaces, including ours, utilize Programmable Logic Controllers (PLCs) or dedicated microprocessor-based temperature controllers. These systems receive input from multiple thermocouples strategically placed within the furnace chamber and, in some cases, within the load itself (load thermocouples). Proportional-Integral-Derivative (PID) control algorithms then precisely modulate the power to the heating elements or the fuel flow to burners in different zones to maintain the setpoint temperature and ensure uniformity. A client of ours processing large aluminum forged components (though the principle applies to copper alloys too) in a custom AKS Bogie Hearth Annealing Furnace, reported a significant improvement in the consistency of hardness values across their large parts after upgrading to our multi-zone PID control system. This system allowed them to program complex heat treatment cycles with precise ramp rates, soak times, and controlled cooling, all while logging critical process data for quality assurance and traceability, which is increasingly demanded by high-end domestic sectors and export markets.
Load configuration also plays an undeniable role in achieving temperature uniformity. Even the best-designed furnace can struggle if the load is packed too densely, restricting atmosphere circulation and heat transfer. Operators must be trained on proper loading techniques to ensure adequate spacing between parts or layers of material. For continuous furnaces, like our Mesh Belt Furnaces used for annealing small metal parts, the belt loading density and distribution must be consistent to ensure each part receives the same thermal exposure. We often work with clients to optimize their loading patterns as part of our technical service, sometimes using thermal modeling to predict heat distribution within complex loads. This collaborative approach ensures that the furnace's inherent capabilities for temperature uniformity are fully realized in practice, leading to consistent, high-quality annealed products.
Maintaining a Consistent and Safe Furnace Atmosphere
The furnace atmosphere is a critical component of the annealing process, especially when aiming for a bright, oxide-free surface on copper and its alloys. Maintaining a consistent and appropriate atmosphere composition throughout the heating, soaking, and cooling cycles is essential. This requires robust systems for atmosphere generation (if generated on-site, like exothermic gas or dissociated ammonia), precise mixing (for blends like nitrogen-hydrogen), and reliable delivery into the furnace. Equally important are systems for monitoring and controlling the atmosphere within the furnace. This can include oxygen sensors, dew point analyzers (to measure moisture content), and gas chromatographs for more detailed analysis. For example, in our Bright Annealing lines for stainless steel strip, which can also be adapted for high-quality copper alloy annealing, we employ highly sensitive oxygen probes and dew point meters that provide continuous feedback to the control system. This allows for automatic adjustments to gas flow rates to maintain, for instance, extremely low oxygen levels (often in the ppm range) and dew points (e.g., below -40°C), critical for achieving a mirror-bright finish.
The integrity of the furnace sealing is paramount for maintaining the desired atmosphere. Any leaks in door seals, sight ports, thermocouple entries, or conveyor openings (in continuous furnaces) can allow air (oxygen and moisture) to ingress or the protective atmosphere to escape. This can lead to oxidation of the product, inconsistent results, and increased consumption of protective gases. Regular inspection and maintenance of all furnace seals are crucial. AKS furnaces are designed with high-quality, durable sealing systems, and we provide guidance on their upkeep. For instance, our Bell-Type Annealing Furnaces feature robust sand seals or liquid seals, along with clamped covers, to ensure a gas-tight environment, vital for long annealing cycles of copper or brass coils under protective atmospheres like nitrogen or HNX gas.
Safety in handling furnace atmospheres, particularly those containing flammable (e.g., hydrogen, dissociated ammonia, carbon monoxide) or asphyxiant (e.g., nitrogen, argon) components, is a top priority. Furnaces using flammable atmospheres must be equipped with appropriate safety interlocks, purge systems, and often, flame supervision systems or gas detection alarms. Standard procedure6 involves purging the furnace chamber with an inert gas (like nitrogen) before introducing the flammable atmosphere at the start of a cycle, and again purging with inert gas to remove the flammable atmosphere before opening the furnace at the end of the cycle. This prevents the formation of explosive mixtures with air. We provide extensive training to our clients' operators on these safe operating procedures. One of our customers in Southeast Asia, using a hydrogen atmosphere for annealing specialized copper alloy components, implemented a comprehensive safety protocol we helped them develop, including automated purge sequencing and emergency ventilation, significantly enhancing their operational safety.
Implementing Comprehensive Safety Protocols and Maintenance Routines
Beyond the specific safety measures related to furnace atmospheres, a broader framework of safety protocols and diligent maintenance is essential for any heat treatment facility. This begins with thorough operator training, which should cover not only the standard operating procedures (SOPs) for the annealing furnaces but also hazard identification, risk assessment, emergency shutdown procedures, lockout/tagout (LOTO) procedures for maintenance, and the correct use of Personal Protective Equipment (PPE). PPE for annealing operations might include heat-resistant gloves, face shields, safety glasses, and, depending on the atmosphere, respiratory protection or portable gas detectors. We always emphasize to our clients, from China to our export markets in India or Europe, that well-trained operators are the first line of defense against accidents.
A robust preventive maintenance program is critical for both safety and operational reliability. This program should be based on the furnace manufacturer's recommendations (like those we provide for AKS furnaces) and tailored to the specific operating conditions. Regular checks should include:
- Heating Systems: Inspection of electric heating elements for wear or damage; for gas-fired furnaces, checking burners, ignitors, and flame safety systems.
- Refractory and Insulation: Looking for cracks, spalling, or degradation that could lead to heat loss or structural issues.
- Safety Interlocks and Controls: Verifying the functionality of door switches, over-temperature cutouts, atmosphere safety systems, and emergency stops.
- Mechanical Components: Checking fans, conveyors, door mechanisms, and other moving parts for wear and proper lubrication.
- Instrumentation: Calibration checks for thermocouples, pressure sensors, and atmosphere analyzers. A client in the Middle East, operating one of our Mesh Belt Furnaces for continuous annealing of small brass parts, reported a significant reduction in unplanned downtime and an improvement in process consistency after implementing a structured preventive maintenance schedule we helped them establish. Their data showed a 20% decrease in maintenance-related interruptions over a six-month period.
Finally, adherence to relevant industry safety standards (e.g., NFPA standards for ovens and furnaces if applicable in the region) and local health and safety regulations is mandatory. This includes conducting regular safety audits, maintaining proper documentation of training and maintenance activities, and fostering a strong safety culture within the organization. Risk assessments should be periodically reviewed and updated, especially if new materials, processes, or equipment are introduced. For instance, when we install a new furnace, like a Vacuum Annealing Furnace for specialty metals, we work with the client to integrate it into their existing safety management system, ensuring all specific risks associated with high vacuum and high temperatures are addressed. By taking a proactive and systematic approach to safety and maintenance, manufacturers can protect their personnel, preserve their assets, and ensure the long-term, reliable operation of their annealing processes.
Temperature uniformity ensures consistent annealingTrue
Maintaining ±5°C uniformity prevents variations in microstructure and mechanical properties across the load.
Furnace seals don't affect safetyFalse
Compromised seals can leak flammable/oxygen-depleting atmospheres, creating explosion or asphyxiation hazards.
Conclusion
Successful annealing of copper, Cu-Ni, and Cu-Zn alloys demands precise control over temperature, time, and atmosphere, tailored to each alloy's unique needs. Prioritizing process uniformity and robust safety protocols, supported by advanced furnace technology like ours at AKS, ensures optimal results and operational excellence.
-
Discover diverse annealing requirements for copper alloys for optimal production outcomes ↩
-
Understand OFHC copper's advantages and potential pitfalls in industrial applications ↩
-
Explore why C10100 copper's purity makes it favorable for certain uses ↩
-
Understand the impact of different atmospheres on zinc volatilization ↩
-
Understand the role of fans in temperature uniformity during annealing ↩
-
Explore procedures that prevent explosive mixtures in furnaces ↩