How Will CAPEX and OPEX Affect the Cost of Bright Annealing Stainless Steel Lines in 2025?
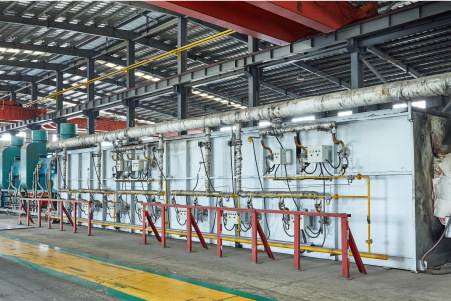
Are you planning to invest in a new bright annealing line but fixated only on the initial purchase price? This narrow focus is a common pitfall, causing companies to overlook the long-term operational costs that can ultimately erode profits and turn a promising asset into a financial burden.
The total cost of a bright annealing stainless steel line is determined by two main factors: Capital Expenditure (CAPEX), the upfront investment in the equipment, and Operational Expenditure (OPEX), the ongoing costs of running it. In 2025, optimizing OPEX through smart CAPEX decisions is critical for profitability.
Making a major investment like this requires looking beyond the sticker price. In my years at AKS Furnace, I’ve seen firsthand how a comprehensive understanding of both initial and recurring costs separates the market leaders from the rest. The most successful operators are those who evaluate a furnace not just on what it costs to buy, but on what it will cost—and save—over its entire lifespan.
A deeper dive into these financial pillars is essential. This isn't just an accounting exercise; it's a strategic necessity. The choices you make at the CAPEX stage will directly influence your energy bills, maintenance schedules, labor needs, and overall efficiency for the next decade or more. By analyzing how trends in technology, energy, and automation are shaping both CAPEX and OPEX in 2025, you can equip your operation for sustainable growth and a powerful competitive edge.
What are the key components of CAPEX in bright annealing stainless steel lines?
Struggling to create a complete budget for your new annealing line? Many companies meticulously account for the furnace itself but are caught off guard by the "hidden" costs. This oversight can lead to project delays, budget overruns, and a compromised start to your operations, impacting your initial return on investment.
The key components of Capital Expenditure (CAPEX) for a bright annealing line include the core furnace and muffle, the heating and cooling systems, automation and control panels, and essential ancillary costs like installation, foundation, commissioning, and operator training. These elements collectively form the total upfront investment.
Understanding these components is the first step toward a well-planned investment. I recently worked with a client in the automotive parts sector who was comparing two furnace quotes. One was significantly cheaper, but a closer look revealed it used a lower-grade alloy for the muffle and offered a very basic control system. I explained that while the initial savings were tempting, the cheaper muffle would likely need replacement years earlier and the lack of precise control would lead to a higher product rejection rate. They realized that the slightly higher initial CAPEX on our AKS furnace was actually an investment in lower future OPEX and higher product quality. This shift in perspective is crucial for any serious manufacturer. The initial quote is merely the beginning of the story, and the true value lies in the engineering, materials, and support that are built into that price. A comprehensive CAPEX plan accounts for everything needed to get the line running efficiently from day one.
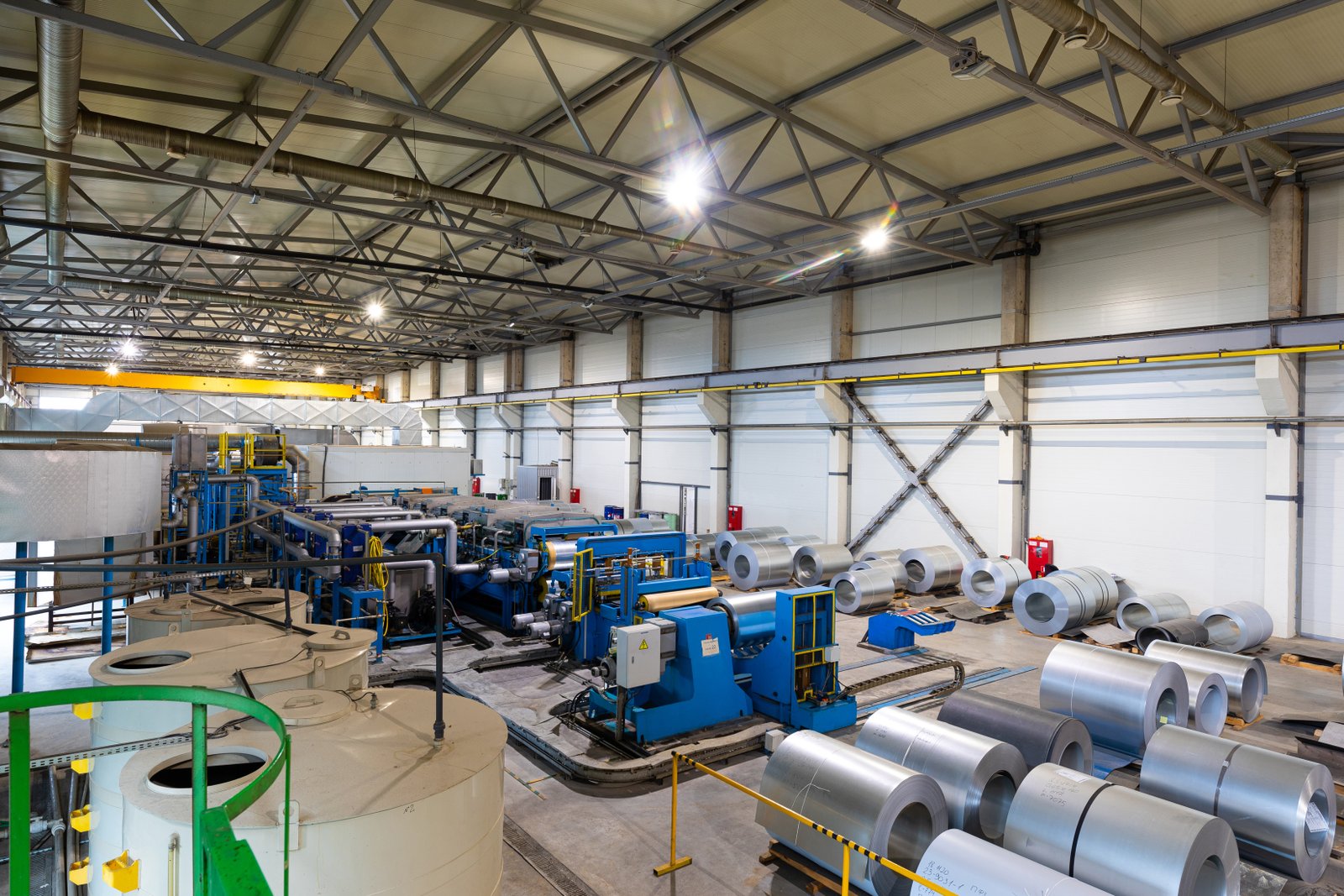
A detailed breakdown of capital expenditures reveals that the furnace is far more than just a heated box. The quality and specification of each component have a direct and lasting impact on your operational efficiency, maintenance costs, and final product quality. When we design a line at AKS, we think in terms of systems, where each part is optimized to work in harmony. This integrated approach ensures that the initial investment delivers value for years to come, rather than creating unforeseen problems. Let’s explore the three core areas of CAPEX that demand careful consideration.
The Furnace Body and Muffle: The Heart of the Investment
The furnace body, its insulation, and the muffle are the foundational elements of your annealing line. Their quality dictates the furnace's thermal efficiency and lifespan. For the main structure, we insist on high-quality steel and superior welding techniques to ensure structural integrity under constant thermal cycling. The insulation is another critical area; using multi-layer, high-density ceramic fiber insulation can significantly reduce heat loss. For instance, a well-insulated furnace can cut ambient temperature rise in the workshop and reduce energy consumption by 10-15% compared to a poorly insulated one. This directly translates to lower electricity or gas bills from the moment you start operating.
The muffle is arguably the most critical component, as it contains the protective atmosphere and is subjected to the highest temperatures. It must be made from a high-temperature resistant alloy, typically 310S or even more advanced materials for demanding applications. I recall a stainless steel strip processor in India who was experiencing frequent production halts. Their existing furnace, from another supplier, had a muffle made from a lower-grade material that warped and cracked within two years. We replaced it with one of our custom-designed 310S muffles, engineered with reinforcement ribs. This single upgrade not only solved their downtime issue but also improved the stability of the atmosphere, leading to a brighter, more consistent finish on their steel strips.
Investing in a robust furnace body and a premium muffle is non-negotiable for long-term reliability. The upfront cost difference between standard materials and high-performance alloys may seem significant, but it pales in comparison to the cost of lost production, frequent repairs, and wasted energy. A superior muffle can last over a decade with proper care, whereas a cheaper one might fail in a fraction of that time, forcing a costly and disruptive replacement. This is a classic example of where a wise CAPEX decision directly prevents future OPEX headaches.
Automation and Control Systems: The Brains of the Operation
In 2025, the control system is no longer just a set of switches; it's the intelligent core of your entire operation. A modern bright annealing line relies on a sophisticated Programmable Logic Controller (PLC) and Human-Machine Interface (HMI) to manage every variable with precision. This includes temperature zones, belt speed, gas flow rates, and cooling parameters. The level of automation you choose is a major CAPEX decision with profound implications for your OPEX. A basic system might be cheaper initially, but an advanced system offers unparalleled advantages.
Consider the precision required in manufacturing electronic components. A client producing high-grade stainless steel connectors needed to maintain a temperature stability of ±3°C to meet their customers' stringent quality standards. Their old system couldn't deliver this consistency, resulting in a rejection rate of nearly 8%. We equipped their new AKS line with a Siemens PLC, precision thyristors for power regulation, and multiple thermocouples per zone. The new system not only maintained the required temperature stability but also allowed them to log process data for every coil, providing full traceability for their clients. Their rejection rate dropped to below 1%, and the savings from reduced scrap paid back the investment in the advanced control system in just 18 months.
Advanced control systems also significantly reduce the reliance on highly skilled operators and minimize the risk of human error. Features like automatic startup and shutdown sequences, alarm diagnostics, and remote monitoring capabilities mean the furnace can run more efficiently with less manual intervention. This lowers labor costs and improves safety. For managers, the ability to access real-time operational data from a desktop or mobile device provides unprecedented control and insight, enabling them to make informed decisions to further optimize production.
Feature Comparison | Basic Control System | Advanced (AKS) Control System |
---|---|---|
Temperature Control | Basic On/Off or PID | Precision Thyristor + Multi-Zone PID |
Data Logging | Manual or None | Automatic, with Export Functionality |
Remote Access | Not Available | Standard Feature |
Alarm System | Simple Light/Buzzer | Diagnostic, with Specific Fault Codes |
Impact on OPEX | Higher Labor Cost, Inconsistent Quality | Lower Labor Cost, Reduced Scrap |
Ancillary and Installation Costs: The Hidden Factors
ly, a comprehensive CAPEX budget must account for the ancillary equipment and one-time costs associated with installation and commissioning. These are often underestimated but are absolutely essential for a successful launch. They include the costs of civil engineering for the foundation, the routing of utilities (electricity, water, and protective gases like hydrogen and nitrogen), and the purchase of required support equipment like gas mixing stations or deionized water systems.
I often advise clients to budget an additional 10-15% of the furnace cost for these items. For instance, a proper foundation is critical for the long-term stability and alignment of a long continuous annealing line. Any settling or shifting can cause issues with the conveyor belt and rollers, leading to premature wear and tear. Similarly, the purity and pressure of your protective gas supply directly affect the surface finish. Investing in a reliable gas mixing and purification system as part of the initial CAPEX is far better than troubleshooting inconsistent brightness and oxidation issues later on.
Furthermore, the costs of on-site installation supervision, commissioning, and operator training are vital investments. At AKS, we don't just ship a furnace; we send our engineers to oversee the installation and ensure everything is calibrated perfectly. We then conduct comprehensive training for the client's production and maintenance teams. A well-trained team can operate the furnace efficiently, perform routine maintenance correctly, and respond to minor issues before they become major problems. A client in Southeast Asia, a newcomer to bright annealing, told me our on-site training program was the most valuable part of their investment, as it gave their team the confidence and skills to take full ownership of the new line.
CAPEX includes installation costsTrue
Ancillary costs like foundation work and commissioning are part of the total CAPEX budget for a bright annealing line.
Basic control systems reduce OPEXFalse
Advanced control systems with automation features actually lower long-term operational costs through reduced labor needs and improved quality control.
How do OPEX factors influence the overall cost of operating bright annealing lines?
Are you feeling the squeeze from rising energy prices and maintenance bills? Focusing solely on the purchase price of your furnace can leave you vulnerable to these volatile operational costs. When OPEX spirals out of control, it directly eats into your profit margins on every meter of stainless steel you produce.
Operational Expenditure (OPEX) significantly influences overall cost by encompassing recurring expenses like energy (electricity and gas), consumables (spare parts, process gases), labor, and maintenance. High OPEX can quickly eclipse initial CAPEX savings, making an seemingly inexpensive furnace a long-term financial liability.
The true cost of a furnace isn't what you pay for it; it's what it costs to run over its entire service life. I often share the story of two clients who bought new lines around the same time. One chose a cheaper, less efficient model from another supplier to save on CAPEX. The other invested in an AKS furnace with our waste heat recovery system1. Within three years, my client's total spending (CAPEX + OPEX) was lower because their monthly energy savings were so substantial. The first company, meanwhile, was struggling with high utility bills and frequent downtime. This real-world example illustrates a fundamental truth: OPEX is not just a line item on a spreadsheet; it's a critical factor that dictates the profitability and sustainability of your heat treatment operations. Understanding and controlling it is paramount.
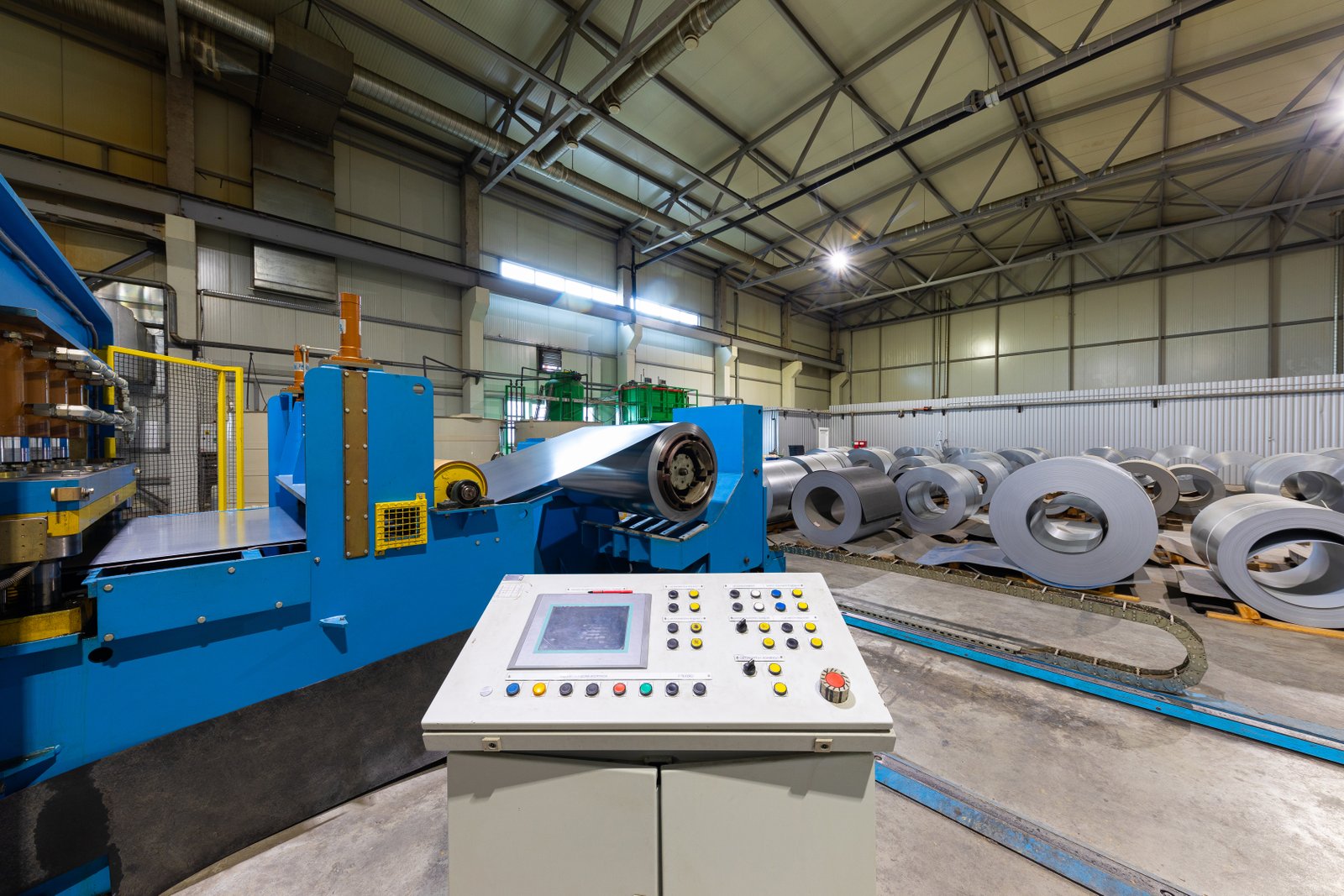
When we dissect the ongoing costs associated with a bright annealing line, it becomes clear that seemingly small inefficiencies can snowball into significant financial burdens over time. The profitability of your entire operation hinges on managing these recurring expenses effectively. From the energy required to reach and maintain annealing temperatures to the human element needed to run the line, every aspect of OPEX demands scrutiny. A furnace that is cheap to buy but expensive to run is a poor investment. At AKS, our design philosophy is centered on building furnaces that minimize these operational costs, delivering a lower Total Cost of Ownership (TCO) and maximizing our clients' profitability.
Energy Consumption: The Dominant Operational Cost
Energy is, without a doubt, the largest single contributor to the OPEX of any bright annealing line. This cost is twofold: the electricity needed to power the heating elements, motors, and control systems, and the consumption of protective atmosphere gases, typically a mix of hydrogen and nitrogen. In a market with volatile energy prices, a furnace's efficiency is directly tied to your bottom line. An inefficient furnace can see its energy costs rival its initial purchase price in just a few years.
This is precisely where modern furnace technology makes the biggest impact. For example, our furnace designs incorporate a dual-layer chamber with a built-in heat exchanger. The hot exhaust gases from the muffle are not simply vented away; they are used to preheat the incoming process gas. This waste heat recovery system can reduce protective gas consumption by 15-20%. For a medium-sized line running 24/7, this translates into tens of thousands of dollars in savings annually. I was reviewing data with a client in Europe who had installed one of our lines. They were facing new carbon taxes, and the documented efficiency of our furnace2 not only saved them money on gas but also helped them meet stricter environmental regulations, turning a compliance issue into a competitive advantage.
Furthermore, precision control of the gas-to-air ratio in gas-fired heating systems ensures complete combustion, maximizing the energy extracted from the fuel. For electrically heated furnaces, the use of high-quality, long-lasting heating elements and efficient power control via thyristors minimizes wasted electricity. The insulation quality, as mentioned under CAPEX, plays a massive role here too. Every kilowatt of heat retained by better insulation is a kilowatt you don't have to pay for again. When you add up these savings over the 15-20 year lifespan of a furnace, the impact on profitability is enormous.
Maintenance and Consumables: The Slow Burn
While not as immediately visible as the energy bill, the costs of maintenance and consumables are a constant drain on resources if not managed properly. These expenses include the replacement of wear-and-tear parts like conveyor belts, rollers, thermocouples, and heating elements, as well as the cost of maintenance labor and production downtime during repairs. The quality of components selected during the CAPEX phase is the single most important factor in controlling these costs.
Consider the rollers that transport the steel strip through the furnace. In a high-temperature environment, rollers made from standard materials can sag or develop surface imperfections, which can scratch the bright finish of the product, leading to costly rejects. Our rollers are made from a centrifugally cast, high-temperature alloy and are dynamically balanced for smooth operation, ensuring a long life and protecting the quality of your product. A stainless steel wire producer in North America reported to us that after switching to an AKS furnace, their annual maintenance budget for the annealing line dropped by 30% primarily due to the longevity of our rollers and heating elements.
The muffle is another major maintenance consideration. A well-designed and properly operated muffle made from 310S alloy can last for many years. However, improper operation—such as rapid heating or cooling, or allowing oxygen to enter the chamber—can drastically shorten its life. This is why our comprehensive training program is so critical. We teach our clients' teams not just how to run the furnace, but how to care for it. Proactive maintenance, such as regular inspections and adherence to recommended operating procedures, is far less expensive than the reactive maintenance required after a component fails unexpectedly, which always includes the high cost of unplanned downtime.
Labor and Training: The Human Element
The final piece of the OPEX puzzle is the human element. This includes the salaries of the operators who run the line and the technicians who maintain it. In the past, running a furnace line required a team of highly skilled, experienced operators. However, the trend in 2025 and beyond is toward increased automation to reduce labor costs and improve process consistency. A modern, automated line from AKS can often be managed by a single operator per shift, whose primary role is to oversee the process via the HMI, load new coils, and perform quality checks.
Investing in a higher level of automation (a CAPEX decision) directly reduces your long-term labor OPEX. An automated system handles the complex sequences of purging, heating, and cooling without the risk of human error. This not only saves on payroll but also drastically reduces the likelihood of costly mistakes, such as damaging the muffle or producing an entire coil of oxidized, scrap material. A kitchenware manufacturer I work with calculated that the reduction in operator error and scrapped material after installing one of our automated lines paid for the automation upgrade within two years.
Moreover, the initial training provided by the furnace manufacturer is an investment that pays dividends throughout the life of the equipment. A well-trained team operates the line more efficiently, leading to lower energy and gas consumption. They can also handle basic troubleshooting and preventive maintenance, reducing the need for expensive service calls. We see our role as a partner, not just a vendor. Ongoing technical support is part of our commitment, ensuring that even if your team changes over the years, the knowledge base required to run your operation profitably is never lost.
OPEX includes energy and maintenance costsTrue
Operational Expenditure (OPEX) indeed covers recurring costs like electricity, gas, spare parts, and labor, which significantly impact long-term furnace expenses.
CAPEX is more important than OPEXFalse
While CAPEX (initial investment) matters, OPEX often exceeds it over time. High operational costs can negate initial savings, making OPEX the decisive factor for profitability.
What trends are impacting CAPEX and OPEX for stainless steel annealing lines in 2025?
Are you preparing your business for the future, or are you reacting to outdated market conditions? The landscape of metal manufacturing is shifting rapidly. Ignoring key global trends when planning your next investment can leave you with an obsolete and uncompetitive operation almost as soon as it's commissioned.
In 2025, the most significant trends impacting CAPEX and OPEX are the global push for sustainability and decarbonization, the integration of Industry 4.0 for smart manufacturing, and persistent volatility in raw material and energy markets. These trends are redefining what constitutes a "smart" investment.
To stay competitive, you can't just think about today's costs; you have to anticipate tomorrow's demands. I was recently in a meeting with a large steel service center planning a major expansion. Their primary concern wasn't just production capacity, but also meeting the ESG (Environmental, Social, and Governance) requirements of their multinational customers. They recognized that an energy-efficient furnace with low emissions wasn't a "nice-to-have" feature anymore—it was a prerequisite for securing high-value contracts. This foresight is changing investment calculus. Higher CAPEX for green and smart technologies is now being seen as a necessary strategy to de-risk future operations and lower long-term OPEX in a world increasingly focused on sustainability and data-driven efficiency.
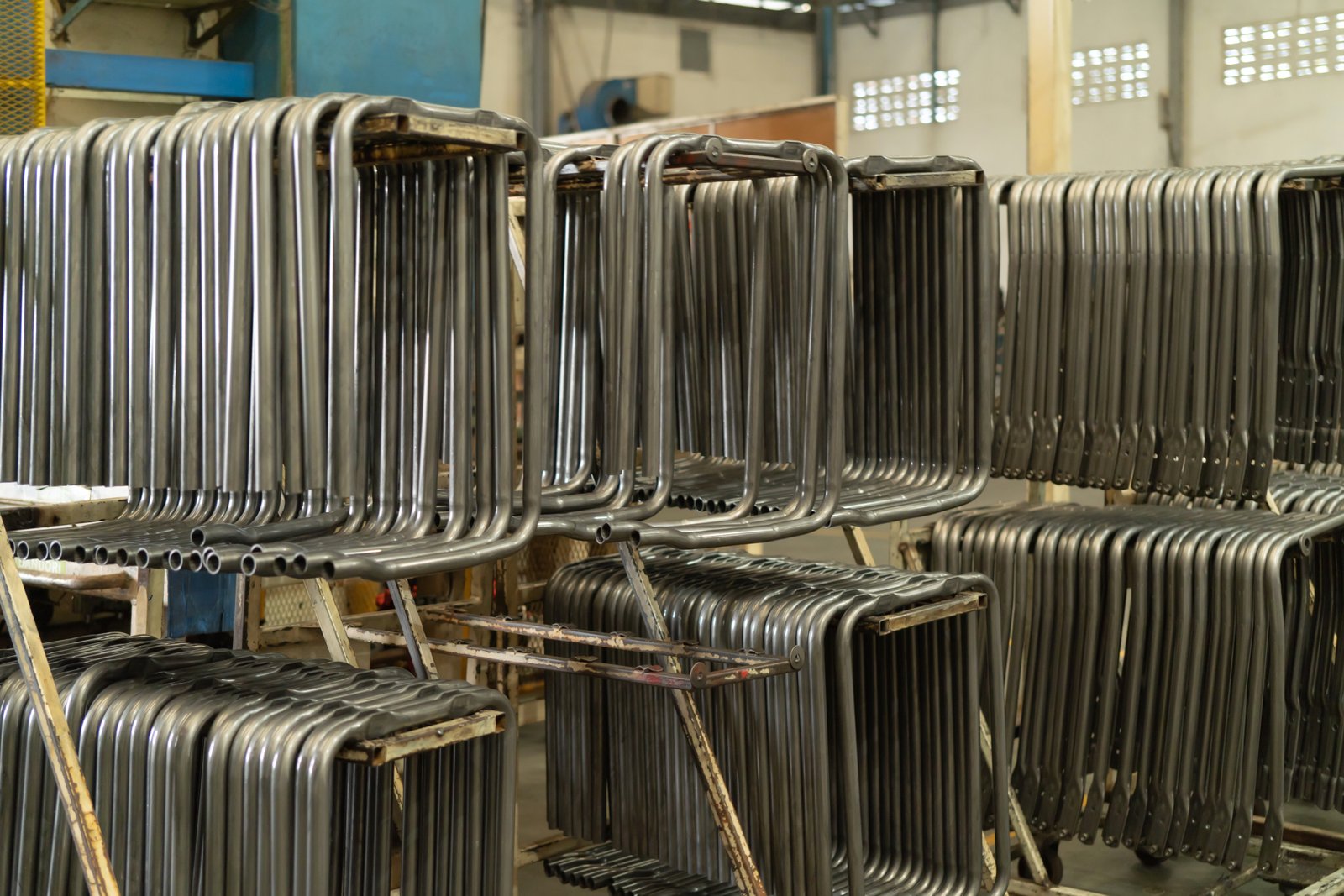
The decision to invest in a new bright annealing line in 2025 cannot be made in a vacuum. It must be informed by the powerful currents of technological innovation, environmental regulation, and economic uncertainty that are reshaping the global manufacturing industry. These macro trends directly influence both the initial cost of the equipment and the long-term expenses of running it. For forward-thinking companies, navigating these trends successfully means turning potential challenges into sources of competitive advantage. At AKS, we are at the forefront of integrating these future-focused solutions into our furnace designs, ensuring our clients are not just prepared for 2025, but for the decade to follow.
The Push for Decarbonization and Energy Efficiency
The global movement toward sustainability is no longer a fringe concept; it is a core business driver. In many regions, carbon taxes, emissions trading schemes, and stringent environmental regulations are a reality. Even in areas without such policies, major consumers of steel products are demanding greater transparency and a lower carbon footprint from their supply chains. This "green pressure" directly impacts both CAPEX and OPEX. The trend is clear: energy-guzzling, high-emission equipment is becoming a significant liability.
This makes investing in energy-efficient technology a strategic imperative. Features that were once considered optional upgrades, such as waste heat recovery systems, enhanced insulation, and precision combustion controls, are now essential. While these technologies may increase the initial CAPEX, the return on investment is compelling. I worked with a client in Europe who was able to secure a "green loan" from their bank at a preferential interest rate specifically because they chose our furnace, which demonstrated best-in-class energy efficiency. Their lower monthly OPEX from energy savings was complemented by a lower cost of capital, a powerful financial combination.
Furthermore, the ability to market your products as being produced through a low-carbon process can open doors to new, high-value markets. Customers in the automotive, electronics, and architectural sectors are increasingly willing to pay a premium for sustainable materials. Your furnace, therefore, becomes part of your company's value proposition. The data logged by a modern control system can be used to generate sustainability reports, providing the verifiable proof that customers and regulators demand. Investing in efficiency is no longer just about saving costs; it's about building a brand that is resilient and respected in a climate-conscious world.
Industry 4.0 and Automation
The fourth industrial revolution, or Industry 4.0, is transforming factories into smart, interconnected ecosystems, and heat treatment is no exception. This trend is all about data, connectivity, and automation3. For bright annealing lines, this means integrating systems that can monitor themselves, predict failures, and optimize their own parameters in real-time. This level of sophistication has a direct and transformative effect on both CAPEX and OPEX. The upfront investment in "smart" features is higher, but the long-term operational benefits are revolutionary.
Predictive maintenance is a prime example. Instead of waiting for a component like a fan motor or a heating element to fail (leading to costly, unplanned downtime), sensors monitor vibrations, power draw, and temperature. The system can then alert operators that a component is degrading and needs to be replaced during the next scheduled maintenance window. A client in the appliance manufacturing industry estimated that this feature alone saved them over 100 hours of lost production in its first year of operation. This shifts maintenance from a reactive, expensive fire-fight to a proactive, controlled, and low-cost activity.
Data logging and process traceability are equally critical. In an Industry 4.0-enabled furnace, every parameter for every coil of steel is recorded and stored. This data is invaluable for quality control, allowing you to prove to a customer that their material was processed exactly to specification. It also allows for continuous improvement. By analyzing historical data, your engineers can identify the perfect combination of belt speed, temperature, and gas flow to achieve the desired metallurgical properties with the minimum possible energy and gas consumption. This data-driven approach to optimization consistently lowers OPEX month after month.
Feature | Traditional Furnace (Industry 2.0/3.0) | Smart Furnace (Industry 4.0) |
---|---|---|
Maintenance | Reactive (Fix when broken) | Predictive (Schedule repairs based on data) |
Process Control | Fixed Setpoints | Self-Optimizing / AI-Assisted |
Quality Assurance | Manual Spot Checks | 100% Traceability via Data Logging |
OPEX Impact | High Downtime, High Scrap | Minimal Downtime, Low Scrap |
Supply Chain Volatility and Material Costs
The past few years have demonstrated the fragility of global supply chains and the volatility of commodity prices. This has a significant impact on furnace manufacturing and, consequently, on CAPEX. The high-temperature stainless steels and alloys (containing nickel, chromium, and molybdenum) used to build durable muffles and furnace components have seen dramatic price fluctuations. This makes budgeting for a new line challenging and underscores the importance of working with a stable, well-managed supplier.
This volatility reinforces the argument for investing in quality and longevity. A furnace built with superior materials that lasts 15-20 years is a much better hedge against future price increases than a cheaper unit that requires a major overhaul or muffle replacement every few years. The cost of that replacement will be subject to the material prices and supply chain conditions of the future, which are likely to be even more challenging than today's. Securing a high-quality asset now is a smart way to lock in value and mitigate future risk.
At AKS, we manage this volatility through strategic sourcing and maintaining a healthy inventory of critical materials. This allows us to provide more stable pricing and reliable delivery timelines for our clients. When a customer commits to a project with us, we can secure the necessary materials, insulating them from subsequent market shocks. This partnership approach is crucial. In an uncertain world, the reliability and financial stability of your equipment supplier become a key part of your own risk management strategy, ensuring that your CAPEX investment is predictable and secure.
Decarbonization impacts CAPEX decisionsTrue
Sustainability requirements are making energy-efficient technologies essential investments, increasing initial CAPEX but lowering long-term OPEX.
Industry 4.0 increases maintenance costsFalse
Smart features like predictive maintenance actually reduce maintenance costs by preventing unplanned downtime and optimizing component replacement.
How can companies optimize CAPEX and OPEX for better financial performance?
Knowing the difference between CAPEX and OPEX is one thing, but are you actively making them work together to boost your bottom line? Many companies treat them as separate budgets, missing the huge opportunity for synergy. This disconnected approach leads to short-sighted decisions that sacrifice long-term profitability for minimal upfront savings.
Companies can optimize CAPEX and OPEX by adopting a Total Cost of Ownership (TCO) mindset, customizing furnace designs to specific production needs, and investing in future-proof technologies like waste heat recovery and modular automation, thereby ensuring the initial investment actively lowers future running costs.
The most financially successful clients I've worked with are those who master this balancing act. They don't ask "What's the cheapest furnace?" They ask "Which furnace will deliver the lowest cost per ton of steel over the next decade?" I guided a stainless steel tube mill through this exact process. We analyzed their production volume and energy costs, and I demonstrated how the slightly higher CAPEX for our high-efficiency model would be paid back in energy savings alone in under 30 months. From that point forward, the furnace would generate positive returns every single day. This strategic approach transforms a capital expenditure from a simple purchase into a powerful tool for enhancing long-term financial performance.
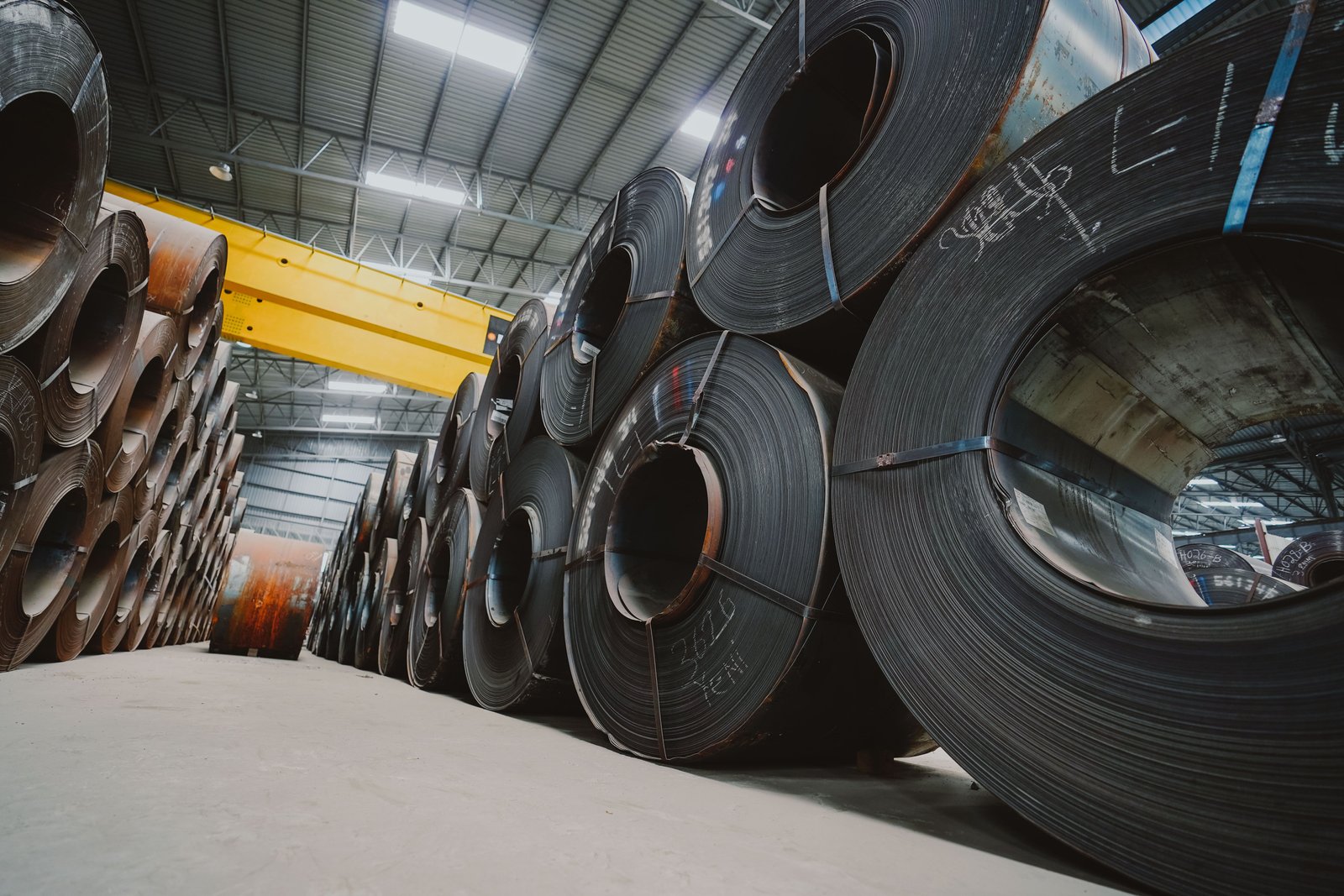
Achieving superior financial performance in the competitive metal processing industry is not about slashing costs indiscriminately. It is about making intelligent, strategic investments where the initial outlay (CAPEX) is deliberately designed to reduce future, recurring costs (OPEX). This holistic approach, often referred to as evaluating the Total Cost of Ownership (TCO), is the cornerstone of modern industrial investment strategy. It requires a shift in perspective—from short-term price tags to long-term value creation. By focusing on customization and investing in technologies that pay for themselves, companies can build a formidable and lasting competitive advantage. At AKS, our entire consultation process is built around helping you find this optimal balance for your specific operational needs.
Adopting a Total Cost of Ownership (TCO) Mindset
The single most effective strategy for optimizing your financial performance is to move beyond purchase price and embrace the concept of Total Cost of Ownership (TCO). The TCO formula is simple in concept but powerful in practice: TCO = Initial CAPEX + Lifetime OPEX. A comprehensive analysis also considers factors like the value of reduced downtime and the cost of rejected materials. When you evaluate investments through the TCO lens, the most financially sound choice becomes clear, and it's often not the one with the lowest initial price tag.
Let's illustrate with a conservative 10-year projection. A standard, low-cost furnace might have a CAPEX of $400,000. Due to its lower efficiency and standard components, its annual OPEX (energy, maintenance, consumables) might be $100,000. In contrast, a high-efficiency AKS furnace with waste heat recovery might have a CAPEX of $500,000, but its advanced design keeps its annual OPEX at just $70,000.
After five years, the cumulative cost of the standard furnace is $400k + (5 $100k) = $900,000. The AKS furnace is $500k + (5 $70k) = $850,000. The "more expensive" furnace is already the cheaper option. Over ten years, the difference is even more stark: $1.4 million for the standard furnace versus $1.2 million for the AKS furnace—a $200,000 saving, not including the value of higher uptime and better quality. This TCO calculation turns an abstract concept into a concrete financial justification for investing in quality.
Leveraging Customization for Efficiency
A one-size-fits-all approach to industrial machinery is inherently inefficient. A furnace designed to handle a wide range of products will be a master of none. True operational efficiency comes from tailoring the equipment to your specific production requirements. This is a key part of our philosophy at AKS. We don't just sell furnaces; we engineer solutions. Customization is a powerful lever for optimizing both CAPEX and OPEX.
For example, a client specializing in very thin-gauge stainless steel foil has different needs than a client annealing heavy-duty automotive components. The foil producer requires extremely precise tension control and a carefully designed cooling zone to prevent distortion. The component manufacturer needs a robust conveyor and specific furnace dimensions to maximize throughput. By designing the furnace chamber width, length, and heating element configuration specifically for the client's product mix, we can optimize energy consumption and maximize output. An oversized furnace wastes enormous amounts of energy and protective gas, while an undersized one creates a production bottleneck.
I recently worked with a manufacturer of stainless steel sinks. Their product has a unique shape. Instead of a standard flat-belt furnace, we designed a custom mesh belt furnace with specific fixtures to hold the sinks as they passed through. This customization increased their throughput by 40% compared to their previous, non-specialized setup. While the CAPEX was tailored to this design, the massive boost in productivity and corresponding drop in energy cost per unit resulted in a much faster ROI and a significant improvement in their overall profitability.
Investing in Future-Proof Technologies
The final piece of the optimization puzzle is to invest with an eye toward the future. Technology and regulations will continue to evolve. A "future-proof" investment is one that either incorporates advanced features from the start or is designed to be easily upgraded later. This approach optimizes the initial CAPEX by preventing the need for a complete replacement of the line in just a few years' time.
The most prominent example of a future-proof technology is a waste heat recovery system. As energy costs and carbon taxes inevitably rise, the value of the energy this system saves will only increase over time. It's an investment that pays you back with ever-increasing dividends. A client who installed our furnace with heat recovery five years ago is now seeing 30% greater annual savings from it than they initially projected, simply because the price of natural gas has risen so sharply.
Another key strategy is modular design. For example, a company might start with a high-quality furnace body and control system but opt for a standard data-logging package. By ensuring the PLC and control panel are designed for modular expansion, they can easily add a more advanced Industry 4.0 data analysis and remote monitoring package later as their needs grow or as capital becomes available. This allows them to manage their initial CAPEX outlay while ensuring their production line can evolve with them, a far smarter strategy than being locked into obsolete technology.
TCO considers both CAPEX and OPEXTrue
Total Cost of Ownership evaluates both initial investment and long-term operating costs.
Customization increases OPEXFalse
Proper customization actually reduces OPEX by improving efficiency and throughput.
What are the best practices for managing costs in bright annealing stainless steel operations?
You've made the investment, and the line is running. But is your team actively managing costs, or are they letting profits slip away through inefficiency? Simply running the equipment isn't enough. Without established best practices for operation and maintenance, even the most advanced furnace will underperform, leading to creeping costs and lost opportunities.
The best practices for managing costs include implementing a proactive maintenance schedule, continuously optimizing the process through[data analysis, and building a strong, collaborative partnership with your equipment supplier for ongoing support and expertise. This approach minimizes downtime and maximizes efficiency.
Cost management is an ongoing discipline, not a one-time setup. It’s about creating a culture of efficiency. I have a client who runs one of the most profitable operations I’ve seen. Their secret? Their team holds a brief weekly meeting to review the furnace's performance data—gas consumption, cycle times, and any minor alerts. This simple habit allows them to catch small deviations before they become costly problems. It empowers their team to take ownership and ensures their state-of-the-art AKS furnace delivers peak performance and profitability year after year. This proactive, data-driven culture is the ultimate best practice.
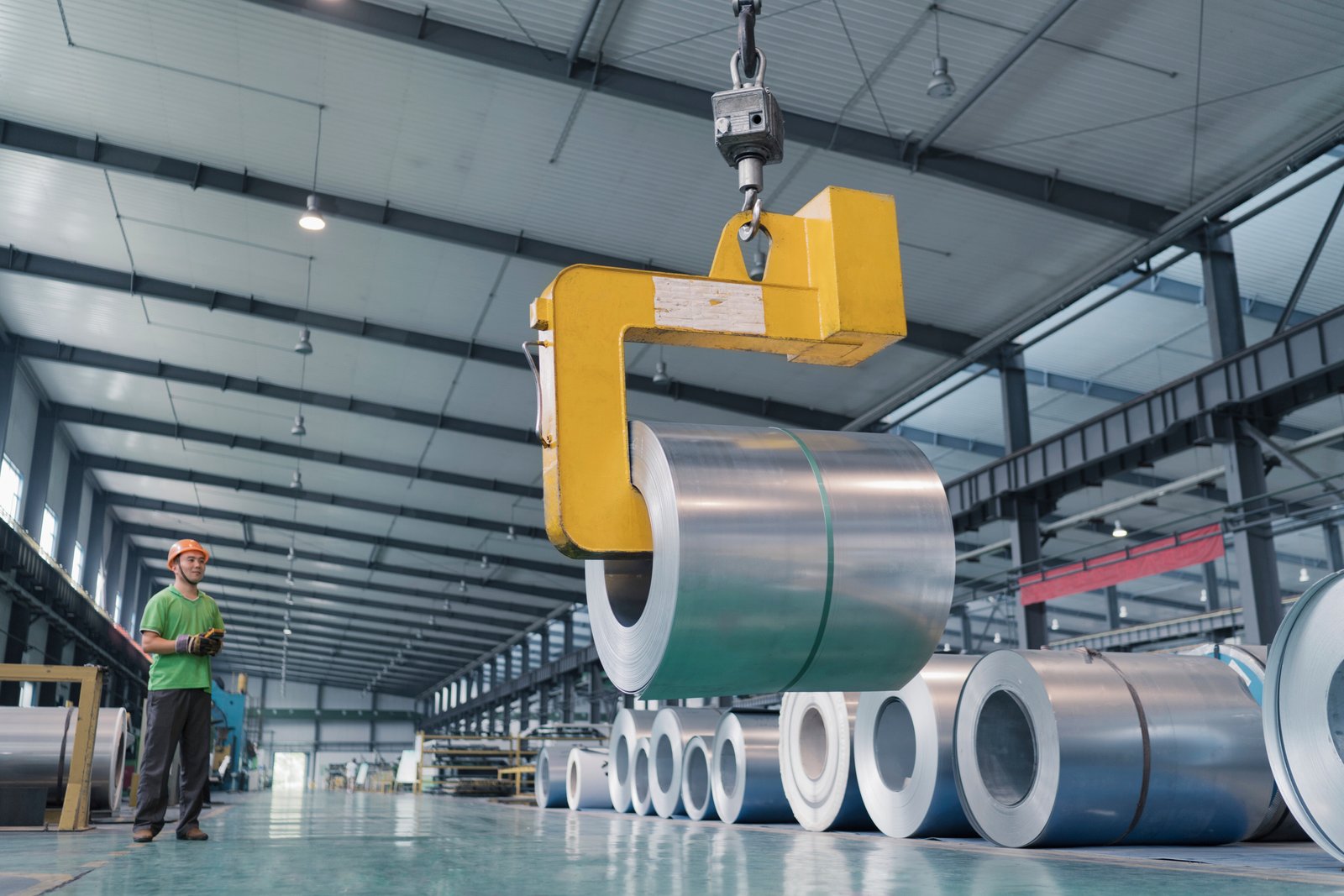
Once your bright annealing line is commissioned, the focus shifts from investment to execution. The long-term profitability of your operation will be determined by the daily, weekly, and monthly practices your team employs. Effective cost management is a dynamic process of continuous improvement, not a static set of rules. It involves a disciplined approach to maintenance to preserve the asset, a rigorous use of data to enhance performance, and a strategic relationship with your technology partner to leverage their expertise. By embedding these best practices into your operational DNA, you can ensure that your initial investment continues to yield maximum returns for its entire lifespan.
Implementing a Proactive Maintenance Schedule
The most significant difference between a low-cost and a high-cost operation is its approach to maintenance. A reactive approach—waiting for something to break before fixing it—is incredibly expensive. It guarantees unplanned downtime, which means lost production, missed deadlines, and potentially damaged customer relationships. Furthermore, emergency repairs are always more costly than planned ones. A proactive maintenance schedule, in contrast, is one of the most effective cost-management tools available.
A proactive schedule is based on regular inspections and preventive replacement of known wear parts. It’s a simple concept that pays huge dividends. For instance, a daily check might involve visually inspecting the drive system and listening for any unusual noises. A weekly check could include verifying thermocouple accuracy and checking gas flowmeter calibrations. Monthly, the team might inspect the condition of the muffle's interior with a boroscope and check the integrity of door seals to prevent gas leaks. We provide all our clients with a detailed checklist and schedule tailored to their specific furnace.
By following this disciplined approach, you can identify potential issues long before they lead to a failure. A slightly worn bearing can be replaced during a scheduled maintenance shift for a few hundred dollars. If that same bearing fails during production, it could seize the main drive roller, tear the conveyor belt, and cause tens of thousands of dollars in damage and days of lost production. Proactive maintenance transforms maintenance from an unpredictable, high-cost risk into a predictable, low-cost operational certainty.
Continuous Process Optimization Through Data Analysis
In the era of Industry 4.0, your furnace should be generating a wealth of valuable data. The best practice is not just to collect this data for quality assurance, but to actively use it to continuously optimize your process for cost efficiency. The data from your PLC and HMI—on temperature curves, gas consumption per cycle, and belt speed—is a roadmap to savings.
For example, your team can experiment with slight adjustments to find the optimal balance point. Can you reduce the percentage of expensive hydrogen in your N2/H2 mix by 2% without affecting the surface brightness? Over a year, a 2% reduction in hydrogen consumption can lead to substantial savings. Can you increase the belt speed by 5% for a certain product gauge while still achieving full annealing? This directly increases your throughput and revenue. This data-driven continuous improvement process, known as Kaizen in lean manufacturing, turns your operation into a learning system that gets more efficient over time.
I worked with an electronics component manufacturer who embraced this philosophy. By analyzing their data, they noticed that their nitrogen consumption spiked during shift changes due to purging procedures. They worked with our engineers to refine their startup/shutdown protocol, creating a "standby mode" that kept the furnace under a positive pressure with minimal gas flow. This simple, data-informed change cut their overall nitrogen consumption by nearly 7%, a significant annual OPEX reduction achieved with zero capital investment.
Building a Strong Partnership with Your Furnace Supplier
Lastly, one of the most overlooked best practices is to view your furnace supplier as a long-term strategic partner, not just a one-time vendor. The relationship should not end when the final payment is made. A true partner, like AKS, has a vested interest in your ongoing success. We have deep expertise not only in building furnaces but in running them efficiently across a wide range of applications. Leveraging this expertise is a powerful cost-management tool.
A strong partnership provides access to ongoing technical support, expert advice on process optimization, and a reliable and efficient supply chain for spare parts. When your team encounters a challenge they can't solve, a quick call to an experienced engineer who knows your exact machine can save hours or days of troubleshooting. When you're looking to expand into a new product line, your furnace partner can advise you on the necessary process adjustments or potential upgrades.
This collaborative approach ensures you are never operating in isolation. We stay in touch with our clients, sharing new findings, maintenance tips, and information on emerging technologies that could benefit their operations. Think of it as having an external team of heat treatment experts on call. This relationship transforms the furnace from a mere piece of equipment into a fully supported production system, minimizing risk and maximizing performance over the long haul.
Approach | Transactional Vendor | Strategic Partner (AKS) |
---|---|---|
Focus | One-Time Sale | Long-Term Client Success |
Support | Reactive, often slow | Proactive, with dedicated support |
Expertise | Sells equipment | Provides holistic solutions |
Spare Parts | Standard supply chain | Optimized inventory, fast delivery |
Cost Impact | Higher risk of long downtime | Minimized risk, continuous improvement |
Proactive maintenance reduces costsTrue
Regular inspections and preventive replacements prevent expensive unplanned downtime and emergency repairs.
Data analysis is optional for cost savingsFalse
Continuous process optimization through data analysis is essential for identifying efficiency improvements and cost savings.
Conclusion
Ultimately, navigating the costs of a bright annealing line in 2025 demands a holistic view. By balancing CAPEX and OPEX, focusing on Total Cost of Ownership, and partnering with a supplier like AKS, you invest not just in a furnace, but in long-term profitability and success.