How Do Digital Twins in Annealing Process Simulation Accelerate R&D Cycles?

Developing new annealing processes or optimizing existing ones can be a slow, resource-intensive, and risky endeavor, often involving numerous physical trials. This traditional approach leads to extended R&D timelines, increased material waste, and delayed market entry for new, high-quality metal products. By leveraging digital twins for annealing process simulation, we can virtually test and refine parameters, dramatically speeding up innovation and reducing costs.
Digital twins accelerate R&D cycles in annealing by enabling rapid virtual prototyping, parameter optimization, and performance prediction without physical trials. This significantly reduces material waste, shortens development timelines, and allows for quicker iteration of new annealing profiles, ultimately fostering faster innovation in heat treatment.
Imagine slashing your R&D time for new alloy treatments1 from months to weeks, or even days. The power of digital twins in annealing simulation isn't just theoretical; it's a practical revolution in how we approach material science and furnace technology. Stick with me as we explore how this technology is reshaping our industry, offering unprecedented speed and precision. We'll delve into specific applications and uncover the tangible benefits for businesses like yours.
The integration of digital twins into annealing process simulation marks a pivotal shift from traditional, often cumbersome, R&D methodologies. For years, we in the industrial furnace sector, particularly at AKS, have seen clients grapple with the protracted timelines and substantial costs associated with empirical testing. Consider a stainless steel strip producer aiming to develop a new grade with specific mechanical properties and a flawless bright finish from one of our bright annealing furnaces2. Traditionally, this would involve numerous physical runs, meticulously adjusting parameters like temperature, atmosphere composition, and strip speed. Each trial consumes valuable energy, materials, and production time. Digital twins offer a compelling alternative. By creating a high-fidelity virtual replica of the annealing line – from the furnace muffle to the cooling zones – engineers can simulate countless scenarios. For instance, a 2019 study by the Journal of Materials Processing Technology highlighted that simulation could reduce experimental trials by up to 70% in certain heat treatment applications. At AKS, we're exploring how these models, fed with real-time sensor data from our energy-saving systems and advanced cooling mechanisms, can predict outcomes with remarkable accuracy, allowing our clients to innovate faster and more sustainably. This isn't just about speed; it's about de-risking innovation and empowering manufacturers to push the boundaries of material performance.
What role does annealing process simulation play in modern manufacturing?
Modern manufacturing demands high-quality, consistent metal products, but achieving optimal annealing results through trial-and-error is costly and inefficient. Without predictive tools, manufacturers risk material defects, energy wastage, and an inability to quickly adapt to new material specifications or customer demands. Annealing process simulation provides a powerful virtual environment to optimize parameters, predict outcomes, and ensure consistent quality before physical production begins.
Annealing process simulation in modern manufacturing plays a crucial role by enabling virtual testing and optimization of heat treatment parameters. It helps predict material properties, reduce defects, minimize energy consumption, and shorten development cycles for new products, ensuring consistent quality and operational efficiency.
The shift towards "smart manufacturing" and Industry 4.0 principles has placed an unprecedented emphasis on data-driven decision-making. Annealing, a critical step in determining the final properties of many metal products, is no exception. Process simulation has evolved from a niche academic tool to an indispensable asset for manufacturers striving for a competitive edge. It's not just about avoiding a bad batch; it’s about understanding the intricate dance of heat, time, and atmosphere at a granular level. Think about a client of ours, a manufacturer of precision automotive components, who needs to ensure perfect formability for stainless steel exhaust parts produced using one of our bright annealing furnaces. Slight variations in annealing can lead to cracking during stamping. Before simulation, they relied on extensive physical testing for each new batch or design tweak. Now, with simulation, they can pre-validate their bright annealing furnace settings, explore "what-if" scenarios for different steel grades, and drastically reduce their setup time and scrap rates. This proactive approach, understanding the process deeply before committing physical resources, is where the real power lies. It's about transforming raw data into actionable intelligence, enabling manufacturers to be more agile, responsive, and ultimately, more profitable. As we delve deeper, we'll explore the specific mechanisms by which simulation achieves this, and how it integrates with broader manufacturing ecosystems.
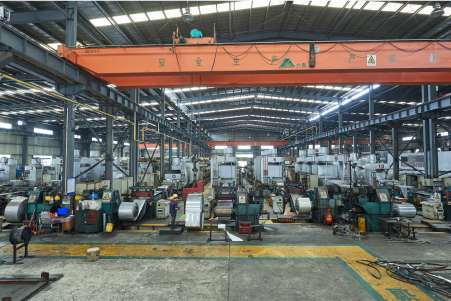
Annealing process simulation is fundamentally reshaping modern manufacturing by injecting a layer of predictive intelligence into what was once a largely empirical practice. Its role extends far beyond simple trial-and-error reduction; it's about holistic process understanding, optimization, and control. This is particularly crucial in industries where material properties are paramount and tolerances are tight, such as in the production of high-strength stainless steel strips or precision electronic components.
The Foundation: Predictive Material Behavior Modeling
At its core, annealing simulation relies on sophisticated material models that predict how a specific alloy will respond to thermal cycling. This involves understanding phase transformations, grain growth kinetics, recrystallization processes, and the development of residual stresses. For instance, when we design a bright annealing furnace for a client producing austenitic stainless steel strips, the simulation must accurately model the dissolution of carbides and the subsequent recrystallization to achieve the desired ductility and bright surface finish. These models are often calibrated using experimental data, but once validated, they allow engineers to explore a vast parameter space virtually. A 2021 study published in Materials & Design demonstrated that multiphysics simulations, coupling thermal, mechanical, and metallurgical models, could predict final grain size and tensile strength with over 95% accuracy for certain steel grades.
This predictive capability is invaluable. Consider a scenario where a copper strip mill, one of our target clients at AKS, wants to introduce a new, thinner gauge product using their existing mesh belt furnace. Traditional R&D would involve numerous runs, adjusting temperature profiles and belt speeds, risking material damage or inconsistent properties. With simulation, they can model the heat transfer dynamics specific to the thinner strip, predict the temperature uniformity across its width, and determine the optimal annealing cycle to achieve the required softness without excessive grain growth. This not only saves material and energy but also accelerates time-to-market for the new product. I recall a project where we assisted a client in exactly this scenario; the simulation results allowed them to bypass nearly a dozen planned physical trials, saving them weeks of development time and significant material costs.
Furthermore, these simulations can account for variations in incoming material properties. No two coils of steel or copper are perfectly identical. Simulation tools can be used to assess the sensitivity of the annealing process to these minor variations, helping manufacturers establish robust processing windows that ensure consistent product quality despite input fluctuations. This is a critical aspect of achieving high-quality output, especially for export-oriented manufacturers who serve demanding international markets. We’ve seen this benefit clients producing components for the electronics industry, where even slight material inconsistencies can lead to downstream production issues.
Process Optimization and Energy Efficiency Gains
Beyond predicting material behavior, annealing simulation is a powerful tool for process optimization, with a significant focus on energy efficiency – a key feature of AKS furnaces like our bright annealing lines equipped with waste heat recovery. The simulation can model heat transfer within the furnace, including radiation, convection, and conduction, as well as the flow of protective atmospheres. This allows for the optimization of burner firing strategies, recuperator designs (like those in our waste heat recovery systems), and insulation configurations to minimize heat loss and maximize thermal efficiency. For example, when developing our waste heat recovery systems, simulation helps us quantify the energy savings by modeling flue gas temperatures and heat exchanger performance under various operating conditions, ultimately demonstrating tangible ROI to our clients.
A practical application involves optimizing the heating and cooling rates. For many alloys, rapid heating can be detrimental, while excessively slow cooling can lead to undesirable microstructures. Simulation allows engineers to design temperature profiles that achieve the desired metallurgical outcomes in the shortest possible time, thereby increasing throughput and reducing energy consumption per ton of material processed. A report by the U.S. Department of Energy (DOE) on industrial heat treatment indicated that optimized process controls, often guided by simulation, can lead to energy savings of 10-20%. For a large-scale stainless steel processor using a continuous bright annealing line, such as those we supply to clients in Southeast Asia, even a 5% reduction in energy consumption translates to substantial annual cost savings. I remember a client in India who, after implementing simulation-guided adjustments to their annealing line, reported a consistent 7% reduction in natural gas consumption.
Let's consider a bogie hearth annealing furnace used for large castings, a common requirement for industrial component manufacturers. Simulating the heat distribution within the furnace and the part itself can identify potential hot or cold spots, ensuring uniform temperature and preventing distortion or incomplete annealing. This is critical for meeting stringent quality standards in aerospace or heavy machinery components. AKS might use such simulations to demonstrate the effectiveness of our precision gas-to-air ratio control in achieving uniform heating, directly impacting the client's operational costs and product quality. The ability to virtually "see" inside the furnace and the part is a game-changer.
Parameter | Traditional Approach | Simulation-Assisted Approach | Benefit Examples (AKS Client Focus) |
---|---|---|---|
Cycle Development | Multiple physical trials | Few virtual iterations | Reduced R&D time for new stainless steel grades in bright annealing. |
Energy Usage | General guidelines, empirical | Optimized firing, insulation | Lower gas/electricity bills for mesh belt or bogie hearth furnaces. |
Defect Analysis | Post-production inspection | Predictive, preventative | Reduced surface oxidation in bell-type furnace; improved strip flatness. |
New Alloy Intro | Lengthy, high-risk R&D | Faster, de-risked evaluation | Quicker launch of products with custom aluminum alloy annealing. |
Process Robustness | Reactive adjustments | Proactive design for variation | Consistent quality for export-oriented copper strip products. |
This table illustrates how simulation transforms the approach for various annealing parameters, directly benefiting the types of clients we serve at AKS.
Integration with Digital Manufacturing Ecosystems
The role of annealing simulation is further amplified when integrated into broader digital manufacturing ecosystems, often linked with the concept of digital twins, which we will discuss later. Data from sensors within the annealing furnace (temperature, atmosphere, strip speed) can be fed back into the simulation model in real-time or near real-time to refine its accuracy and adapt to changing conditions. This creates a dynamic loop where the physical process informs the virtual model, and the virtual model, in turn, provides insights for optimizing the physical process.
For instance, a client using an AKS bell-type annealing furnace for steel coils could integrate simulation with their Manufacturing Execution System (MES). When a new coil with slightly different chemistry arrives, the MES could trigger a simulation run with the updated material data to recommend optimized annealing parameters. This level of integration supports agile manufacturing and mass customization, critical for clients serving diverse markets. Furthermore, simulation results can be used for operator training, creating virtual environments where personnel can learn to manage different annealing scenarios without risking actual production. I’ve seen how this can significantly shorten the learning curve for operators working with new, advanced furnace control systems.
Looking ahead, the combination of AI and machine learning with annealing simulation promises even greater advancements. AI algorithms can analyze vast datasets from simulations and real-world operations to identify complex patterns and correlations that human engineers might miss. This can lead to self-optimizing annealing processes that continuously learn and adapt to achieve peak performance. A 2022 research paper in Computers in Industry explored how machine learning models trained on simulation data could predict annealing outcomes with even higher speed and accuracy, paving the way for truly autonomous heat treatment control. This proactive, intelligent approach enabled by simulation is what defines its critical role in modern, competitive manufacturing, helping our clients stay ahead.
Digital twins reduce physical trials by 70%True
Studies show digital twins can reduce experimental trials by up to 70% in heat treatment applications.
Annealing simulation is only about trial reductionFalse
Simulation enables holistic process understanding, optimization, and control beyond just reducing trials.
How are digital twins currently utilized in the annealing process industry?
Optimizing complex annealing processes for various metals and alloys in real-time remains a significant challenge, often leading to inconsistencies. Without a dynamic virtual counterpart, manufacturers struggle with predictive maintenance, rapid troubleshooting, and adapting processes to new material grades efficiently. Digital twins3 are increasingly used to create live, virtual replicas of annealing lines, enabling real-time monitoring, predictive analytics, and process optimization.
Digital twins in the annealing industry are currently utilized to mirror physical furnace operations, enabling real-time performance monitoring, predictive maintenance, and process simulation. This facilitates optimized energy consumption, improved product quality, reduced downtime, and faster adaptation to changing production requirements.
The concept of a "digital twin" – a dynamic virtual representation of a physical asset or process – has moved from futuristic vision to practical application in many manufacturing sectors, and the annealing industry is no exception. While full-scale, perfectly synchronized digital twins are still evolving, their foundational elements are already delivering significant value. It's about creating a living model that not only simulates but also interacts with the real-world annealing furnace and its environment. Imagine having a complete virtual replica of your AKS bright annealing line, fed with live sensor data – temperatures, gas flows, strip tension, and speed. This isn't just a static simulation; it's a dynamic tool that reflects the current state of your operations. This allows us at AKS, and our clients, to move beyond periodic checks and reactive adjustments. We can start asking "what if" questions based on the actual current conditions, not just theoretical ones. For example, if a sensor indicates a slight deviation in the protective atmosphere composition within a bell-type furnace, the digital twin could instantly simulate the potential impact on the coil being annealed and suggest corrective actions before any quality issues arise. I recall a client in the automotive sector who leveraged a rudimentary digital twin to troubleshoot an intermittent issue in their heat treatment line, pinpointing the root cause in days rather than the weeks it might have taken previously. This level of proactive control and insight is where digital twins are making their mark, transforming how we manage and optimize these critical thermal processes. We are seeing these applications emerge in various forms, from sophisticated process control systems to advanced diagnostic tools, all aimed at enhancing efficiency and product consistency.
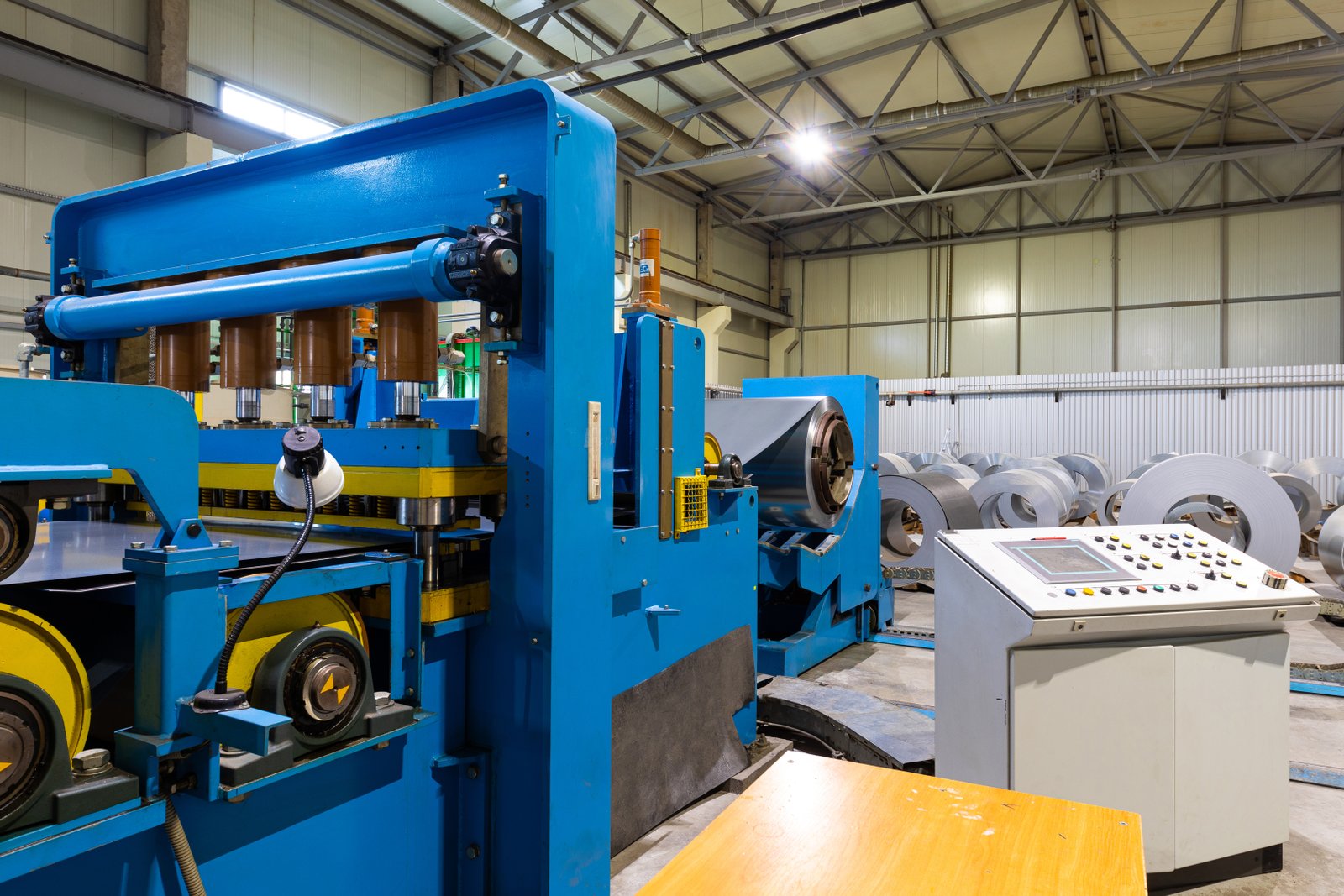
The utilization of digital twins in the annealing process industry, while still in its growth phase, is already demonstrating transformative potential across various aspects of furnace operation, maintenance, and product development. At AKS, we see this technology as pivotal for delivering the next generation of energy-efficient and high-performance heat treatment solutions, such as our bright annealing furnaces or vacuum annealing furnaces4. Current applications range from enhancing operational efficiency to accelerating the development of new annealing cycles for advanced materials.
Real-Time Process Monitoring and Optimization
One of the primary applications of digital twins in annealing is for real-time process monitoring and optimization. By continuously feeding sensor data from the physical annealing furnace (e.g., temperatures from multiple zones in a bright annealing line, gas flow rates in a bell-type furnace, conveyor speeds in a mesh belt furnace, vacuum levels in a vacuum furnace) into its virtual counterpart, operators gain an unprecedentedly clear and dynamic view of the process. For instance, in one of our AKS bright annealing furnaces for stainless steel strips, numerous thermocouples monitor the temperature profile along the muffle. The digital twin can visualize this profile in 3D, compare it against the ideal setpoints, and even predict the temperature distribution within the strip itself. If deviations occur, the twin can simulate the impact on the final material properties (like ductility or surface brightness) and suggest adjustments to heating elements or gas flows to bring the process back into optimal parameters. A 2020 case study from a European steel processor, reported in Iron & Steel Technology, showed that implementing a digital twin for their continuous annealing line led to a 15% reduction in temperature variations and a 5% improvement in yield due to more consistent product quality.
This real-time linkage allows for more than just reactive control; it enables proactive optimization. The digital twin can run "what-if" scenarios in parallel with the live operation. For example, if an incoming material coil for an AKS mesh belt furnace has slightly different thickness or chemical composition (data perhaps supplied by an upstream MES), the digital twin can quickly simulate the optimal adjustments to the annealing cycle to ensure consistent results, rather than relying on operator experience or standardized recipes that may not be perfectly suited. This is particularly valuable for our clients in the automotive or electronics sectors, where material consistency for components like sensor sleeves or connectors is non-negotiable. Our precision control systems for gas-to-air ratio, a key feature of AKS furnaces, can feed data into the twin, which can then fine-tune combustion for maximum energy efficiency based on real-time heat demand and flue gas analysis, directly impacting our clients' bottom line.
The ability to accurately model and predict the conditions inside a furnace, such as a vacuum annealing furnace where direct measurement of all parameters can be challenging due to the extreme environment, is another significant benefit. The digital twin, built on fundamental physics and validated with available sensor data (like vacuum level and zonal temperatures), can infer conditions in inaccessible areas, providing a more complete understanding of the heat treatment of specialty metals. I’ve seen this help a client optimize cycles for complex alloy parts, reducing the risk of overheating or incomplete annealing in critical sections.
Predictive Maintenance and Anomaly Detection
Digital twins are proving invaluable for predictive maintenance (PdM) in annealing operations. Annealing furnaces, whether they are bogie hearth, bell-type, or continuous lines, are complex systems with numerous components – heating elements, fans, seals, sensors, refractory linings – that are subject to wear and tear. A digital twin can incorporate models of these components' degradation over time and under operational stress. By analyzing real-time sensor data (e.g., vibration signatures from fans in advanced cooling systems, power consumption of heating elements in a bright annealing furnace, heat-up rates of a bogie hearth furnace), the twin can detect subtle anomalies that might indicate impending failure. For instance, if a heating element in a bogie hearth furnace starts drawing more current than predicted by the twin for a given temperature, it could signify degradation. The twin could then alert maintenance teams and even estimate the remaining useful life (RUL) of the component. A survey by McKinsey in 2021 indicated that AI-driven predictive maintenance, often leveraging digital twin concepts, can reduce downtime by up to 50% and maintenance costs by up to 40% in industrial settings.
Consider the advanced cooling systems in our AKS bright annealing furnaces, critical for achieving optimal sheet flatness and superior quality. These systems rely on precise airflow and temperature control. A digital twin could monitor fan motor currents, bearing temperatures, and heat exchanger efficiency (if part of a waste heat recovery system). If the cooling rate starts to deviate from the twin's prediction, it could point to a clogged filter or a failing fan, allowing for scheduled maintenance before it impacts product quality or causes an unexpected shutdown. This proactive approach minimizes costly unplanned downtime, a major concern for our clients in high-volume sectors like stainless steel strip processing or automotive parts manufacturing. I recall a client in Southeast Asia who managed to avert a major breakdown in their cooling section by heeding an early warning from their monitoring system, which was based on digital twin principles.
Furthermore, digital twins can simulate the long-term effects of different operational strategies on equipment health. For example, before implementing a new, more aggressive heating cycle to increase throughput in a mesh belt furnace for small metal parts, the digital twin could assess the potential impact on the lifespan of the heating elements and conveyor belt. This allows for a balanced decision between productivity and maintenance costs, ensuring the long-term reliability that AKS furnaces are known for. This is particularly relevant for export-oriented manufacturers who need to maximize uptime to meet demanding delivery schedules.
Virtual Commissioning and Operator Training
Another powerful application of digital twins is in virtual commissioning and operator training. Before a new annealing line, say a complex bright annealing furnace from AKS, is physically installed at a client's site in Europe or North America, its digital twin can be used to test and validate the control logic, PLC programming, and system integration. This "virtual run-in" allows engineers to identify and resolve potential issues in the software and control strategies without risking damage to expensive equipment or delaying the actual commissioning process. A 2019 report by ARC Advisory Group highlighted that virtual commissioning can reduce startup times by 25-50%. At AKS, as we expand into new export markets, being able to virtually commission aspects of our furnaces can significantly streamline the on-site installation and ramp-up for our clients, ensuring they get to full production faster.
For operator training, the digital twin provides a safe and realistic environment to learn how to operate the annealing furnace, manage different process recipes (e.g., for various steel grades in a bell-type furnace), and respond to abnormal situations or emergencies. Trainees can interact with a virtual control panel that mirrors the real one, and the digital twin will simulate the furnace's response to their actions. They can experience alarms, troubleshoot simulated faults (e.g., a loss of protective atmosphere in a bell-type furnace, or a temperature overshoot in a vacuum furnace), and practice emergency shutdown procedures without any risk to personnel or equipment. This enhances operator competency and confidence, leading to smoother operations and fewer human errors. This is particularly beneficial for clients adopting more advanced automation and control systems, as it helps bridge any skills gaps. As part of our comprehensive technical service at AKS, incorporating digital twin-based training could be a significant future value-add, ensuring our clients maximize the potential of their investment.
Digital twins enable real-time furnace monitoringTrue
Digital twins continuously receive sensor data from physical furnaces, allowing operators to track and optimize processes in real-time.
Digital twins eliminate all furnace maintenanceFalse
While digital twins enable predictive maintenance, they don't eliminate the need for physical maintenance - they help schedule it more effectively.
What challenges do manufacturers face in traditional R&D cycles for annealing?
Traditional R&D for annealing processes is often a lengthy, expensive, and resource-intensive endeavor, fraught with uncertainty and reliance on empirical trial-and-error. This leads to slow innovation, high material waste, significant energy consumption during testing, and delayed market entry for new or improved metal products. Understanding these inherent challenges highlights the urgent need for more efficient, predictive, and cost-effective R&D methodologies like simulation and digital twins.
Manufacturers in traditional annealing R&D face challenges like lengthy development times, high costs from physical trials, material waste, energy inefficiency, and difficulty scaling lab results to production. These hurdles impede rapid innovation and responsiveness to market demands for new materials.
For decades, the path to developing or refining an annealing process has been well-trodden, yet notoriously challenging. As someone who has been deeply involved in the design and commissioning of industrial furnaces at AKS for many years, I've witnessed firsthand the frustrations our clients encounter. It often involves a painstaking series of physical experiments, meticulously adjusting one variable at a time – temperature, soak time, atmosphere – and then conducting extensive material testing to evaluate the results. Imagine a stainless steel strip producer, a core client for our bright annealing furnaces, aiming to optimize their process for a new, thinner gauge of a high-strength alloy. Each trial on their production line means downtime for regular manufacturing, consumption of expensive alloy material, significant energy usage (counter to our energy-saving system goals), and the labor of skilled technicians and metallurgists. If a trial doesn't yield the desired results, it's back to the drawing board, often with limited insight into why it failed. I remember a client in the white goods sector struggling to achieve a consistent bright finish; their trial-and-error approach took months. This empirical approach, while it has served the industry for years5, is increasingly at odds with the modern demand for rapid innovation, cost efficiency, and sustainability. The pressure to quickly develop new products or adapt to fluctuating raw material quality highlights the limitations of these conventional methods.
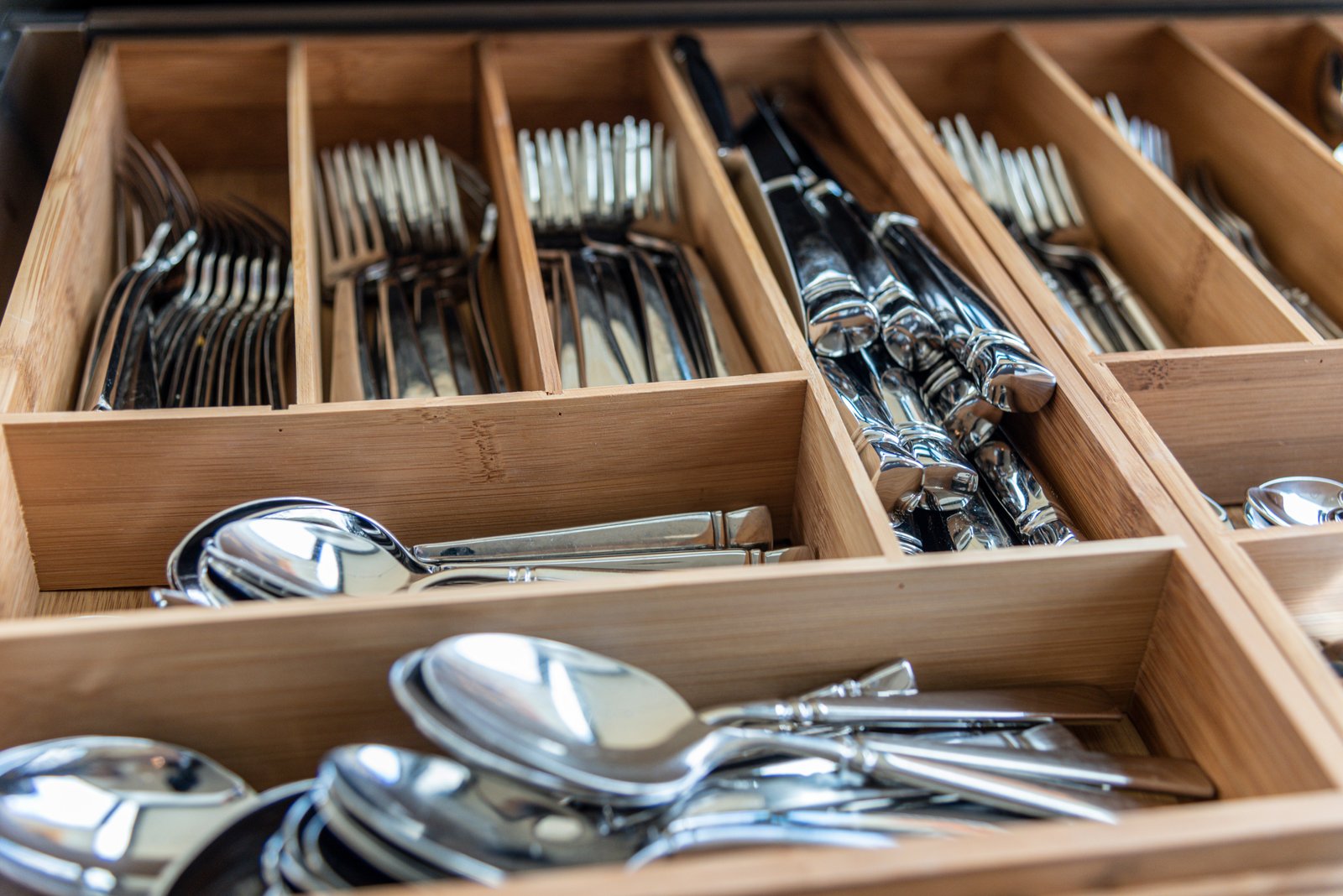
The traditional R&D cycle for annealing processes, while foundational to metallurgical advancements for centuries, is riddled with inherent challenges that increasingly hinder manufacturers in today's fast-paced, competitive, and resource-conscious environment. These challenges span from economic and temporal constraints to technical and scalability issues, impacting everyone from small specialty alloy producers using vacuum annealing furnaces to large-scale steel mills operating extensive bright annealing lines. At AKS, we frequently engage with clients, such as carbon steel strip heat treatment plants or copper and brass strip mills, grappling with these very problems as they seek more efficient heat treatment solutions.
Prohibitive Costs and Extended Timelines
One of the most significant hurdles in traditional annealing R&D is the substantial cost and time investment required. Each physical trial involves direct expenses such as raw materials (which can be very costly for specialty alloys like those processed in our vacuum annealing furnaces, or even large volumes of stainless steel for bright annealing lines), energy to heat the furnace (often for extended periods), labor for setup and operation, and subsequent material testing (e.g., tensile tests, hardness measurements, metallographic analysis). For instance, a company developing a new annealing cycle for a proprietary nickel-based superalloy destined for a vacuum annealing furnace might conduct dozens of trials. Each trial could consume kilograms of expensive material and require days of furnace time and analysis. A 2018 survey by a leading materials science journal6 suggested that developing a new heat treatment process for an advanced alloy can take anywhere from 6 months to 2 years using purely traditional methods. I've personally seen R&D projects for relatively common stainless steel grades take up to a year to perfect when relying solely on physical trials in a production bright annealing furnace.
These extended timelines directly impact a manufacturer's ability to respond to market opportunities or evolving customer requirements. If a competitor, perhaps one with more agile R&D, introduces a product with superior properties, the lengthy R&D cycle can mean a significant loss of market share before a comparable or better product can be developed. I recall a client, a producer of high-quality copper strips for electronics using a mesh belt furnace, who struggled for nearly a year to optimize their bright annealing process for a new, ultra-thin gauge. The numerous trials not only incurred substantial costs but also delayed their entry into a lucrative new market segment in Southeast Asia. This highlights how R&D speed is not just an internal metric but a critical competitive factor, especially for export-oriented manufacturers.
Furthermore, the "opportunity cost" of tying up production-scale equipment for R&D trials can be immense. For manufacturers running near full capacity, dedicating a production bright annealing furnace or a mesh belt furnace for experimental runs means lost output of commercial products, directly impacting revenue. This often relegates R&D to off-peak hours or necessitates investment in dedicated pilot-scale equipment, which itself adds to the cost burden. Many of our medium to large-scale clients simply cannot afford to take a primary production furnace offline for extensive R&D.
Material Waste and Energy Inefficiency
Traditional R&D is often characterized by significant material waste and high energy consumption. Since the process relies on physical experimentation, many trials will inevitably result in suboptimal or unacceptable material properties, rendering the processed material as scrap or requiring costly re-processing. For high-value materials like aerospace-grade titanium (often processed in vacuum annealing furnaces) or specialized stainless steels for automotive parts, this material waste represents a substantial financial loss. A study by the Fraunhofer Institute7 indicated that in some complex manufacturing processes, R&D-related scrap can account for up to 5-10% of total material usage during the development phase. I've seen coils of expensive stainless steel strip rendered unusable after experimental runs in a bright annealing line went awry.
The energy consumed during these iterative trials is another major concern, especially with growing emphasis on sustainability and rising energy costs – issues we actively address with AKS furnace features like energy-saving systems and waste heat recovery. Heating an industrial furnace, whether it's a large bogie hearth furnace for castings or a continuous bright annealing line for steel strips, to high temperatures for multiple experimental runs consumes vast amounts of energy. Each unsuccessful trial represents not just wasted material but also wasted kilowatt-hours or cubic meters of gas. This is directly contrary to the energy-saving ethos we champion at AKS. Traditional R&D, by its trial-and-error nature, inherently struggles with energy optimization during the development phase itself, as the focus is primarily on achieving the target properties, often with less initial regard for energy efficiency of the R&D process. I have seen clients run a furnace for an entire shift just for one or two R&D trials, a huge drain on resources.
The environmental impact of this waste (both material and energy) is also increasingly under scrutiny. Manufacturers, including many of our clients aiming for "green" credentials, are under pressure to reduce their carbon footprint and improve resource efficiency, making the inherently wasteful aspects of traditional R&D less tenable in the long run.
Difficulties in Scaling and Process Understanding
A persistent challenge in traditional annealing R&D is the difficulty in scaling results from laboratory or pilot-scale experiments to full-scale production, and the often limited fundamental understanding gained from purely empirical approaches. Conditions in a small lab furnace can be very different from those in a large industrial unit like an AKS bogie hearth annealing furnace or a wide continuous bright annealing line. Heat transfer characteristics, temperature uniformity (critical for sheet flatness from our advanced cooling systems), and atmosphere control can vary significantly with scale. An annealing cycle developed in a small muffle furnace might not produce the same results when applied to a multi-ton coil in a bell-type annealing furnace or a wide strip in a continuous line. This "scale-up" problem can necessitate further rounds of costly trials on production equipment. I’ve often heard from clients, "It worked in the lab, but we can't replicate it on the production line."
Moreover, traditional trial-and-error, while it might eventually lead to a working process, often provides limited insight into the fundamental metallurgical phenomena at play. Without a deep understanding of why certain parameters work and others don't, it becomes difficult to troubleshoot issues, adapt the process to new material variations (e.g., a new batch of carbon steel strip with slightly different chemistry), or make informed improvements. The R&D process can feel like navigating in the dark, with each adjustment based more on educated guesses than on a robust, physics-based understanding. This lack of deep process insight makes it harder to innovate systematically and can lead to processes that are sensitive to small, uncontrolled variations. For instance, a client might find a "sweet spot" for their annealing process but struggle to maintain consistency if the ambient temperature changes seasonally, affecting cooling rates, because the underlying heat transfer dynamics were never fully modeled or understood during the R&D phase. This is a common pain point we hear from manufacturers before they explore more advanced process control and simulation tools that can complement our precision-controlled AKS furnaces.
Traditional R&D is expensiveTrue
Physical trials consume costly materials, energy, and labor, with each failed attempt adding to the financial burden.
Lab results scale perfectlyFalse
Heat transfer and atmosphere control differ significantly between small lab furnaces and full-scale production equipment, often requiring additional costly trials.
How can digital twins address these challenges and improve efficiency?
Traditional R&D for annealing is plagued by high costs, long lead times, material waste, and difficulties in scaling, hindering innovation. These inefficiencies mean manufacturers struggle to keep pace with market demands, optimize resource use, and gain deep process understanding. Digital twins offer a transformative approach by enabling virtual experimentation, predictive insights, and continuous optimization, directly tackling these longstanding R&D bottlenecks.
Digital twins address R&D challenges in annealing by enabling rapid virtual prototyping, reducing physical trials, material waste, and energy consumption. They improve process understanding, facilitate faster scaling, and allow for continuous optimization, significantly enhancing R&D efficiency and innovation speed.
Having explored the often-painful realities of traditional R&D cycles in annealing, the promise of digital twin technology comes as a breath of fresh air. It’s not just an incremental improvement; it’s a paradigm shift in how we approach the development and optimization of heat treatment processes. At AKS, we're excited by how digital twins can directly counteract the challenges of high costs, protracted timelines, and resource inefficiency that our clients, from stainless steel strip processors using our bright annealing furnaces8 to automotive component manufacturers relying on specialized heat treatments, have historically faced. Imagine being able to run hundreds, even thousands, of virtual annealing trials in the time it would take to conduct a single physical one. Picture understanding the intricate interplay of temperature, atmosphere, and material microstructure with a clarity never before possible, all without consuming a single piece of metal or kilowatt of unnecessary energy. I've spoken with R&D managers who dream of this capability. This is the power digital twins bring to the table – transforming R&D from a resource-draining marathon into a swift, insightful, and data-driven endeavor. They allow us to move from educated guesses to precise predictions, fundamentally changing the economics and speed of innovation in the annealing industry.
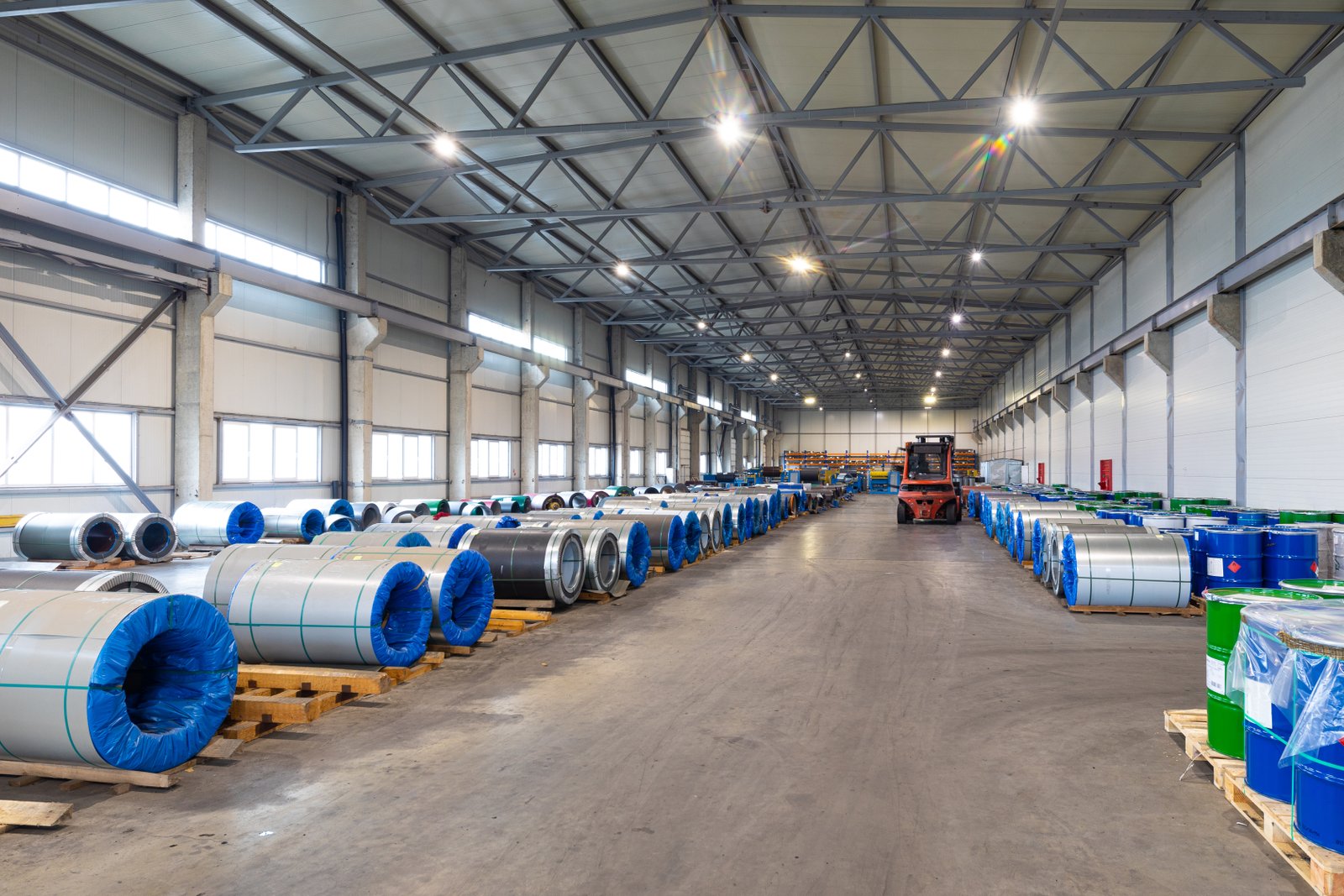
Digital twins offer a potent solution to the multifaceted challenges inherent in traditional R&D cycles for annealing processes. By creating a dynamic, high-fidelity virtual replica of the physical annealing system – be it an AKS bright annealing furnace, a bogie hearth furnace, or a vacuum annealing furnace – and the material behavior within it, manufacturers can significantly enhance R&D efficiency, reduce costs, and accelerate innovation. This technology directly targets the bottlenecks of time, cost, material waste, and limited process understanding that have long constrained progress for many of our clients, including metal processing factories and industrial component manufacturers9.
Accelerated Experimentation and Reduced Prototyping Costs
The most immediate impact of digital twins on annealing R&D is the drastic reduction in reliance on physical trials. Instead of conducting numerous costly and time-consuming experiments on actual furnaces, engineers and metallurgists can perform a vast majority of their iterative testing within the virtual environment of the digital twin. For example, when developing an annealing cycle for a new alloy grade intended for our AKS bright annealing furnaces, the digital twin can simulate the effects of varying peak temperatures, soak times, heating/cooling rates (perhaps modeling our advanced cooling system performance), and protective atmosphere compositions on the material's microstructure (e.g., grain size, phase distribution) and mechanical properties (e.g., hardness, ductility). A 2021 study in the Journal of Manufacturing Processes demonstrated that simulation-driven R&D, a core component of digital twin functionality, could reduce the number of physical experiments by over 60-80% in heat treatment process development. I’ve seen early adopters achieve similar reductions when modeling cycles for stainless steel wire or carbon steel strips.
This virtual experimentation translates directly into substantial cost savings. The expense of physical materials, particularly for specialized alloys processed in vacuum annealing furnaces or even large coils for bell-type furnaces, is largely eliminated during the virtual R&D phase. Energy consumption, a significant operational cost in heat treatment (which our energy-saving systems aim to reduce), is minimized as simulations run on computational resources rather than energy-intensive furnaces. Labor costs associated with setting up, running, and monitoring physical trials are also significantly reduced. As an example, a client of AKS, an export-oriented manufacturer of stainless steel kitchenware using a mesh belt furnace, could use a digital twin to test dozens of annealing parameters for achieving a specific bright finish on a new austenitic grade. This virtual exploration would cost a fraction of physical trials, both in terms of direct expenses and lost production time. The ability to rapidly iterate through designs and parameters in silico means that only the most promising candidates proceed to limited physical validation, dramatically shortening the overall R&D timeline from months or years to potentially weeks.
Enhanced Process Understanding and De-risked Innovation
Digital twins provide a much deeper and more nuanced understanding of the annealing process than is typically achievable through traditional empirical methods. The underlying physics-based models within the digital twin allow researchers to visualize and analyze phenomena that are difficult or impossible to measure directly in a physical furnace, such as internal temperature gradients within a thick component in a bogie hearth furnace, or the precise evolution of microstructural features during the annealing cycle in an aluminum strip. This detailed insight helps in identifying critical process parameters and their sensitivities, leading to more robust and optimized annealing recipes. For instance, by simulating stress evolution during cooling in our advanced cooling systems, manufacturers can better predict and mitigate issues like strip distortion or cracking, ensuring the high-quality, flat product our clients demand. A client producing precision electronic hardware once told me that understanding these subtle internal dynamics through simulation was like "turning the lights on" in their process development.
This enhanced understanding de-risks the innovation process. Manufacturers can explore more radical or unconventional annealing strategies in the virtual environment without the fear of costly failures or equipment damage. They can push the boundaries of material performance with greater confidence, knowing that the digital twin has already vetted the feasibility and potential outcomes of new approaches. A research team at a university collaborating with an industrial partner, as reported in Metallurgical and Materials Transactions A (2022), used a digital twin to investigate novel rapid annealing cycles. The simulations allowed them to identify promising pathways that would have been considered too risky or expensive to explore through purely physical trials initially. This ability to "fail fast and cheap" in the virtual world is a cornerstone of accelerated innovation, enabling our clients to potentially develop new heat-treated products for export markets more quickly.
R&D Challenge | Traditional Approach | Digital Twin Solution (AKS Context) | Improvement Metric (Illustrative for AKS Clients) |
---|---|---|---|
Development Time | Months to years (many trials on furnace) | Weeks to months (virtual trials of bright/vacuum annealing) | 50-75% time reduction for new alloy cycles |
Cost of Trials | High (materials, energy, labor) | Low (computation, few validation trials on AKS furnace) | 60-80% cost reduction for R&D projects |
Material Waste | Significant (failed coils/parts) | Minimal (only from limited validation in mesh belt/bell furnace) | >90% scrap reduction during R&D phase |
Energy Consumption (R&D) | High (multiple furnace runs) | Low (computational, few runs of energy-saving AKS furnace) | >90% R&D energy use reduction |
Process Insight | Limited, empirical | Deep, physics-based; e.g., effect of atmosphere on bright finish | Leap in understanding material-process interaction |
Scaling Risk | High (lab-to-production issues) | Reduced (models incorporate AKS production furnace parameters) | Faster, reliable scale-up for carbon/stainless steel |
Innovation Speed | Slow, incremental | Rapid, e.g., for new high-strength automotive parts | 2-5x faster innovation cycles |
This table illustrates the transformative potential of digital twins, contextualized for the types of annealing challenges and furnace solutions relevant to AKS and our target clients.
Optimized Resource Utilization and Faster Scale-Up
Digital twins enable the optimization of resource utilization not only during R&D but also in subsequent production. By identifying the most energy-efficient annealing cycles that still meet all quality requirements, digital twins contribute directly to AKS's commitment to energy-saving systems and waste heat recovery. For example, a simulation might reveal that a slightly longer soak time at a marginally lower temperature in a bogie hearth furnace can achieve the same metallurgical results for large components as a shorter, hotter cycle, but with 10% less energy consumption. Such insights, easily generated by the digital twin, are hard-won in traditional R&D but are invaluable for our clients focused on energy savings.
Furthermore, digital twins facilitate a smoother and faster transition from R&D to full-scale production. The models developed can be adapted to represent the specific characteristics of production-scale equipment, such as an AKS bright annealing line for stainless steel strip or a bell-type furnace for copper coils. This allows for virtual testing and optimization of the process on the production line's digital counterpart before actual production begins, minimizing the risks and time associated with scale-up. If the digital twin is already integrated with the physical furnace for real-time monitoring, the validated R&D parameters can be seamlessly transferred to the production control system. This ensures that the innovations developed in R&D are quickly and effectively implemented on the factory floor, leading to faster realization of benefits such as improved product quality (e.g., consistent bright surface finish), reduced costs, and increased throughput. For our clients in demanding export markets like India or Southeast Asia, who often need to ramp up production of new products quickly, this streamlined scale-up capability is a significant competitive advantage.
Digital twins reduce physical trialsTrue
Digital twins enable virtual experimentation, cutting physical trials by 60-80% according to studies.
Digital twins increase material wasteFalse
They actually reduce material waste by over 90% during R&D by minimizing failed physical trials.
What strategies can be adopted to implement digital twin technologies effectively in R&D?
Despite the clear benefits, implementing digital twin technology for annealing R&D10 can seem complex and resource-intensive for many manufacturers. Without a clear strategy, companies risk fragmented efforts, underutilized capabilities, and a failure to achieve the desired acceleration in their R&D cycles. Adopting a structured, phased approach focusing on specific goals, data integration, and skill development is key to successfully leveraging digital twins.
Effective implementation of digital twins in R&D involves starting with clear objectives, focusing on high-impact annealing processes, ensuring robust data infrastructure, fostering collaboration between domain experts and data scientists, and adopting an iterative, scalable approach to development and deployment.
Recognizing the transformative power of digital twins11 is one thing; successfully integrating this technology into your R&D framework for annealing processes is another. It's not a plug-and-play solution but a strategic initiative that requires careful planning, investment, and a shift in mindset. As a company like AKS, which prides itself on innovation and providing comprehensive technical service for our industrial furnaces, we understand that our clients, from large stainless steel coil processors in export markets to specialized automotive part producers, need practical pathways to adoption. The journey towards a fully functional digital twin can seem daunting, potentially involving new software, sensor integrations on existing bright annealing or mesh belt furnaces, data management protocols, and upskilling of personnel. However, by breaking down the implementation into manageable stages and focusing on clear, achievable goals, the path becomes much clearer. The key is to avoid trying to boil the ocean and instead build capabilities incrementally, demonstrating value at each step. I often advise starting with a single furnace type or a specific material challenge. This ensures buy-in, continuous learning, and ultimately, a successful and sustainable integration of digital twin technology that genuinely accelerates R&D.
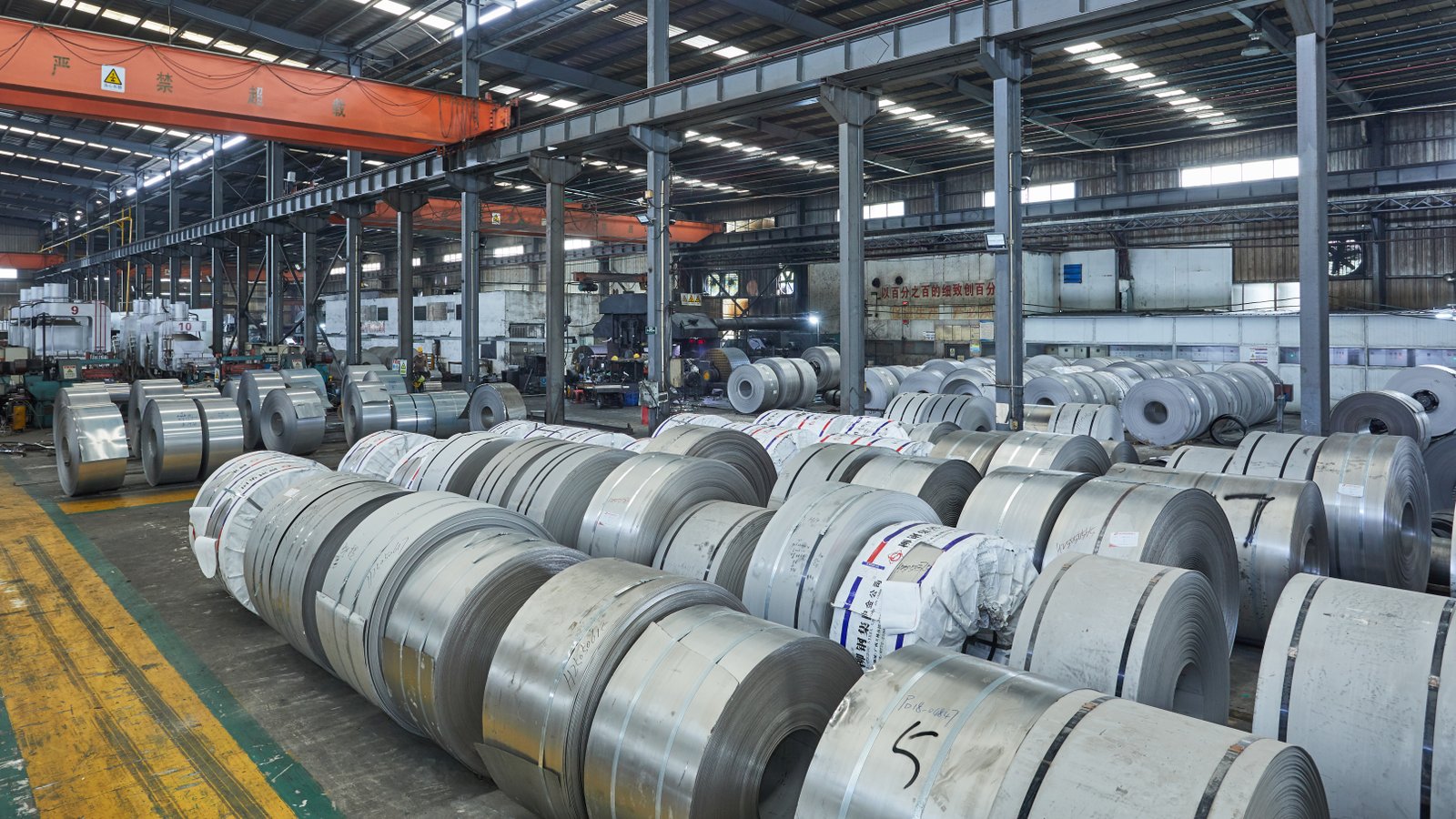
Adopting digital twin technologies effectively in annealing R&D requires a well-thought-out strategy that aligns with the manufacturer's specific goals, resources, and existing infrastructure, especially when dealing with diverse equipment like AKS's range from bright annealing furnaces to vacuum furnaces. It’s a journey that blends technological adoption with organizational change. A haphazard approach can lead to wasted investment and disillusionment, while a strategic one can unlock significant competitive advantages for our clients, whether they are medium-to-large scale producers or focused on high-end domestic sectors. At AKS, we advise clients considering such advancements to focus on a pragmatic, value-driven implementation.
Phased Implementation and Clear Objective Setting
A crucial first step is to avoid an "all-or-nothing" approach. Instead, adopt a phased implementation strategy, starting with a pilot project that targets a specific, high-impact area. This could be optimizing the annealing cycle for a particularly problematic alloy in a vacuum annealing furnace, reducing energy consumption in a high-throughput bright annealing furnace (leveraging its energy-saving system), or improving the yield of a high-value product processed in a bell-type furnace. For example, a stainless steel strip producer might initially focus on creating a digital twin for just the heating zone of their continuous annealing line to optimize temperature uniformity and reduce defects related to uneven heating, aiming for enhanced metallurgical consistency. The objectives for this pilot project should be clearly defined and measurable, such as "reduce R&D trials for new Grade X stainless steel by 30%" or "identify parameters to cut energy use in our AKS Bogie Hearth Furnace by 5% during the annealing of large components." Such clear targets help in demonstrating early wins and securing buy-in for broader adoption. According to a 2022 Deloitte report on digital twins, companies that start with well-defined use cases and scale incrementally are significantly more successful. I’ve seen this firsthand; a client who started with a small project on one furnace quickly gained momentum for wider deployment.
This phased approach allows the organization to learn and adapt. The initial digital twin might be relatively simple, perhaps focusing on thermal modeling for an existing AKS furnace. As expertise grows and value is demonstrated, more complexity can be added, such as incorporating microstructural evolution models, integrating more sensor data from the furnace's precision control systems, or linking with MES/ERP systems. For instance, after successfully modeling the thermal aspects of a bell-type annealing furnace, the next phase could involve modeling the protective atmosphere dynamics and their interaction with the coil surface to ensure a perfect bright surface finish. This iterative development ensures that the digital twin evolves in line with the organization's needs and capabilities, potentially even informing future custom furnace designs from AKS.
A key part of this phase is also selecting the right tools and platforms. This involves evaluating various simulation software, IoT platforms for data acquisition from furnace sensors, and data analytics tools. The choice should be guided by the specific requirements of the annealing processes (e.g., the complexity of physics to be modeled for a vacuum annealing furnace vs. a simpler mesh belt furnace for fasteners), existing IT infrastructure, and the skills available within the team. Partnering with furnace manufacturers like AKS, who understand the equipment intricacies, can also be beneficial in this selection process.
Data Infrastructure, Integration, and Model Validation
A digital twin is only as good as the data it's built on and fed with. Therefore, establishing a robust data infrastructure is paramount for any annealing operation, from carbon steel strip plants to aluminum foil manufacturers. This involves identifying all relevant data sources: historical process data from past annealing cycles, material properties databases for various alloys, real-time sensor data from the annealing furnaces (temperatures from multiple zones, pressures, gas flows from energy-saving systems, speeds from mesh belt drives), and results from physical experiments. Strategies for data acquisition, storage, cleaning, and management need to be developed. For our clients using advanced AKS furnaces with precision control systems, much of this data might already be available but may need to be consolidated and made accessible to the digital twin platform. For older equipment, retrofitting with necessary sensors might be required. For instance, to accurately model an older bogie hearth furnace, additional thermocouples or atmosphere sensors might need to be installed to capture data comparable to that from a newer, more instrumented furnace.
Data integration is key. The digital twin needs to seamlessly integrate data from various sources. This might involve connecting to PLCs controlling the furnace, SCADA systems for overall line monitoring, LIMS (Laboratory Information Management Systems) for material test results, and ERP systems for production planning. This holistic data view enables a more accurate and comprehensive virtual representation. Model validation is an ongoing critical process. The predictions made by the digital twin must be regularly compared against real-world experimental results or production data from the client’s specific annealing line (e.g., an AKS bright annealing furnace processing stainless steel strip). Any discrepancies must be investigated, and the models refined accordingly. This iterative validation loop, using data from limited, targeted physical trials, builds confidence in the digital twin's accuracy and reliability. For example, if a digital twin predicts a certain grain size and surface brightness for a given annealing cycle in a bright annealing furnace, this prediction should be verified by metallographic analysis and surface inspection of a sample processed under those conditions.
A challenge here can be data quality and quantity, especially for manufacturers with older records or less automated processes. Historical data might be incomplete or inconsistent. Ensuring high-quality data input is crucial. This might involve implementing new data governance policies or investing in data cleansing tools. As a furnace provider, we at AKS emphasize the importance of good data logging from the outset with our equipment.
Cross-Functional Collaboration and Skill Development
Implementing digital twin technology effectively is not solely an IT or engineering project; it requires strong cross-functional collaboration. Metallurgists, process engineers, R&D scientists, data scientists, IT specialists, and even furnace operators need to work together. Metallurgists and process engineers provide the domain expertise essential for building accurate physical models of the annealing process for specific materials like copper, aluminum, or various steel grades. Data scientists contribute skills in data analysis, machine learning, and model building. IT specialists ensure the necessary infrastructure and data flows are in place. Operators can provide valuable insights into the practical aspects of furnace operation, for example, how an AKS mesh belt furnace behaves with different loading patterns. At AKS, when we develop new furnace technologies like our energy-saving systems or advanced cooling systems, collaboration between our R&D, design, manufacturing, and technical service teams is vital. This same collaborative spirit is essential for clients implementing digital twins.
Investing in skill development is also critical. The team needs to be proficient in using simulation software, interpreting data, and understanding the principles behind the digital twin. This might involve specialized training programs, hiring new talent with specific skill sets (e.g., computational materials science), or partnering with external experts or academic institutions. Many universities now offer courses and research programs focused on digital manufacturing and materials modeling, providing a potential source of talent and collaboration. Creating a "center of excellence" or a dedicated digital twin team within the organization can help consolidate expertise and drive the initiative forward. This team would be responsible for developing, maintaining, and evolving the digital twin capabilities, ensuring that the technology remains a strategic asset for accelerating R&D and improving overall operational performance. For our clients, particularly those in export-oriented sectors who need to stay competitive, building this internal capability is a long-term investment in their success.
Phased implementation reduces riskTrue
Starting with a pilot project allows for learning and demonstrating value before full-scale adoption.
Digital twins require perfect dataFalse
While quality data is important, digital twins can start with available data and improve over time through validation.
Conclusion
Digital twins revolutionize annealing R&D by enabling rapid virtual experimentation, drastically cutting costs and timelines. This accelerates innovation, enhances process understanding, and boosts efficiency, empowering manufacturers to deliver superior metal products faster and more sustainably in a competitive global market.
-
Learn about the efficiency and speed-up in researching alloy treatments with digital twins. ↩
-
Understand applications and benefits of bright annealing furnaces in metal treatment. ↩
-
Gain an understanding of digital twins and their application in modern industries ↩
-
Learn about AKS furnace technologies and their advantages in heat treatment processes ↩
-
Gain historical context on the reliance on trial-and-error in annealing R&D. ↩
-
Understand the traditional timeframes in alloy heat treatment R&D. ↩
-
Learn about material waste during R&D phases and its economic impact. ↩
-
Learn about the benefits of bright annealing furnaces in reducing oxidation and enhancing product quality ↩
-
Discover how digital twins enhance process efficiency and drive innovation in manufacturing ↩
-
Discover how digital twins improve efficiency and innovation in annealing R&D ↩
-
Learn about key applications of digital twins across various R&D sectors ↩