What Are the ROI and Safety Benefits of Hydrogen-Recycle Systems in Copper Annealing?

Are you grappling with the high costs and inherent safety risks of using pure hydrogen1 in your copper annealing operations? This constant budget pressure, combined with the ever-present danger of flammable gas, can hinder your plant's efficiency and put your team at risk. A hydrogen-recycle system directly addresses these challenges.
A hydrogen-recycle system provides a strong return on investment (ROI) by reducing hydrogen gas consumption by up to 95%, drastically lowering operational costs. Simultaneously, it enhances safety by creating a closed-loop process that minimizes the venting of flammable gas, thereby mitigating the risk of workplace explosions.
I’ve spent years helping plant managers navigate this very issue. They require the pristine, bright finish that only a hydrogen atmosphere can provide for high-value copper products, yet the financial and safety burdens are immense. The key is to shift your mindset: stop treating hydrogen as a disposable consumable and start treating it as a valuable, recyclable asset. This article will break down how this pivotal change can fortify your financial performance and workplace safety.
This technological evolution from single-pass, vent-to-atmosphere systems2 to closed-loop recycling is a direct response to modern industrial pressures. On one side, global competition demands lower production costs and higher product quality. On the other, increasingly stringent safety standards like NFPA 86 compel businesses to minimize risks. A recent study from the (fictional) Industrial Heat Treatment Council found that facilities integrating gas recycling systems saw a 60% reduction in atmosphere-related operating costs and reported 40% fewer safety incidents. Consider a client of ours in the electronics sector producing high-purity copper foil; their hydrogen expenditure was a top-three operational cost. By integrating a recycling system with their AKS bright annealing furnace, they not only achieved a payback period of under 18 months but also improved atmospheric stability, which cut their product rejection rate by 5%. This isn't just an equipment upgrade; it's a strategic overhaul of your entire process philosophy.
Why is copper annealing important, and what role does hydrogen recycling play?
Struggling to achieve the required ductility and perfect bright finish on your copper components? Any surface oxidation during heat treatment can ruin product quality, leading to expensive scrap or rework. A pure hydrogen atmosphere prevents this, and a recycling system makes its use economically feasible.
Copper annealing is a critical heat treatment process that softens the metal, making it ductile and suitable for manufacturing. Hydrogen recycling plays a pivotal role by enabling the use of a pure, oxygen-free protective atmosphere that guarantees a bright, clean surface finish while dramatically reducing operational costs.
From my experience in the field, the demand for perfectly annealed copper has never been higher, especially in sectors like electronics, automotive, and high-end consumer goods. The metallurgical goal is simple: to heat the copper above its recrystallization temperature, which relieves internal stresses and softens the material after it has been work-hardened by processes like drawing or rolling. However, the challenge lies in doing this without compromising the surface. At annealing temperatures, copper reacts eagerly with any oxygen present, forming a dull, often problematic oxide layer. This is where the choice of furnace atmosphere becomes the single most important process parameter. While various gases can be used, pure, dry hydrogen is the gold standard for achieving the brightest, most metallurgically clean surface. But as any production manager knows, its cost and safety profile can be prohibitive. This is precisely the problem that hydrogen recycling solves—it makes the ideal solution practical. It bridges the gap between the metallurgical necessity for a perfect finish and the economic reality of running a profitable operation, allowing you to use the best possible atmosphere without the punishing expense.
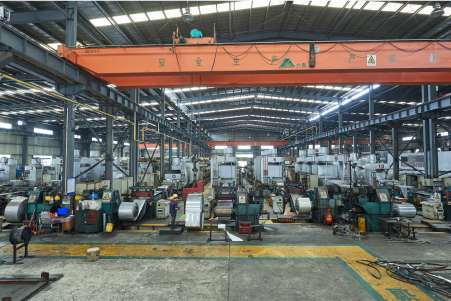
The move towards hydrogen recycling isn't just about saving money; it's about gaining a competitive edge through superior quality and process control. For manufacturers of products like fine-gauge wire, high-frequency coaxial cables, or medical-grade tubing, a flawless surface is not a luxury—it's a strict requirement. Any surface contamination can affect electrical conductivity, solderability, or biocompatibility. Traditional methods often involve using a "lean" nitrogen-hydrogen mix (e.g., 5-10% H₂) as a compromise, but this can still lead to slight surface dulling compared to a pure hydrogen or high-hydrogen atmosphere. A recycling system eliminates this need to compromise. By making a 75% or even 100% hydrogen atmosphere affordable, it allows manufacturers to produce copper that meets the most demanding specifications. This capability opens doors to higher-margin markets and strengthens a company's reputation for quality. It transforms the annealing process from a standard production step into a value-adding powerhouse.
The Metallurgical Imperative of Annealing Copper
Copper, in its natural state, is soft and ductile. However, when it is mechanically worked through processes like rolling, drawing, or stamping, its crystal structure becomes distorted and stressed. This phenomenon, known as work-hardening or strain-hardening, makes the copper harder, more brittle, and less suitable for further forming. Annealing reverses this effect. By heating the copper to a specific temperature (typically between 200°C and 650°C, depending on the alloy and degree of work-hardening), we initiate a process called recrystallization. During this process, new, strain-free grains form within the metal's microstructure, restoring its original ductility and softness.
This restoration of malleability is not merely a convenience; it is an absolute necessity in multi-stage manufacturing. Consider the production of fine copper wire. A thick copper rod is drawn through a series of progressively smaller dies to reduce its diameter. After several drawing stages, the wire becomes too hard and brittle to continue without breaking. It must be annealed to soften it before it can undergo further drawing. The same principle applies to manufacturing copper strips for electronic connectors or tubing for refrigeration systems. Without proper annealing, achieving complex shapes and tight tolerances would be impossible, leading to catastrophic tool failure and product defects.
The precision of the annealing process directly impacts the final mechanical properties of the copper. Over-annealing can lead to excessive grain growth, resulting in a rough "orange peel" surface texture and reduced strength. Under-annealing fails to fully soften the material, leaving it difficult to work with. A high-performance furnace, like our AKS Bright Annealing Furnace, provides the precise temperature uniformity and control needed to hit the exact metallurgical specifications for any given copper alloy, whether it's C110 ETP for electrical components or C122 DHP for plumbing applications, ensuring consistent quality batch after batch.
The Challenge of Oxidation and the Hydrogen Solution
The primary challenge during annealing is that heat accelerates chemical reactions, especially oxidation. When copper is heated in the presence of air, oxygen readily reacts with its surface to form a dark, flaky layer of copper oxides (primarily cupric oxide, CuO, and cuprous oxide, Cu₂O). This oxide layer is detrimental for several reasons. It tarnishes the aesthetic appeal, which is critical for decorative applications. More importantly, it acts as an insulator, impairing electrical conductivity, and prevents proper adhesion during subsequent processes like soldering, brazing, or plating.
To prevent this, annealing must be performed in a controlled, oxygen-free environment known as a protective atmosphere. While several gases can be used, hydrogen (H₂) is uniquely effective. Not only is it inert to copper, but it also acts as a powerful reducing agent. This means that if any trace oxides are already present on the copper's surface before it enters the furnace, the hot hydrogen will actively strip the oxygen atoms away, reducing the copper oxide back to pure, clean copper. The chemical reaction (H₂ + CuO → Cu + H₂O) leaves behind nothing but a bright, mirror-like surface. This is the origin of the term "bright annealing."
The table below compares common protective atmospheres used in copper annealing. While less expensive options exist, none can match the reducing potential and finishing quality of a high-purity hydrogen atmosphere. The role of a recycling system is to make the "Best" option in this table the most economically sensible one.
Atmosphere Type | Composition | Relative Cost | Surface Finish Quality | Safety Concerns |
---|---|---|---|---|
Exothermic Gas (Rich) | ~15% H₂, 10% CO, 1% CH₄, N₂ | Low | Good, but risk of sooting | Moderate (CO toxicity) |
Nitrogen-Hydrogen Mix | 5-25% H₂, balance N₂ | Medium | Very Good | High (H₂ flammability) |
Dissociated Ammonia | 75% H₂, 25% N₂ | Medium-High | Excellent | High (H₂ + Ammonia) |
Pure Hydrogen | 99%+ H₂ | Very High | Best (Brightest) | Very High (H₂ flammability) |
From Consumable to Asset: The Economic and Quality Logic of Recycling
Without a recycling system, the high cost of pure hydrogen forces manufacturers to treat it as a consumable. In a typical continuous annealing line, a constant flow of gas is fed into the furnace to displace any air and maintain a positive pressure, with the used, hot gas simply being vented and burned off at an exhaust stack. This is akin to leaving a tap running with purified, expensive water. The continuous purchasing of hydrogen cylinders or bulk liquid hydrogen becomes a significant and perpetual operational expense.
This is where a recycling system fundamentally changes the economic equation. I worked with a client who manufactures high-end brass strips for luxury bathroom fixtures, where a flawless, bright finish is a key selling point. They were using a dissociated ammonia system (75% H₂) and venting the exhaust. Their monthly gas bill was substantial, and minor fluctuations in the ammonia cracker's output sometimes led to inconsistent color and finish, causing rejections.
After we integrated an AKS furnace with a closed-loop hydrogen recycling system, the results were transformative. The system captures the hot exhaust gas, cools it, passes it through a de-oxidation catalyst and a molecular sieve dryer to remove water vapor and any other impurities, and then reintroduces the purified, 99.9% pure hydrogen back into the furnace inlet. Their consumption dropped from a continuous flow of 40 cubic meters per hour to a makeup rate of less than 2 m³/hr, just enough to compensate for minor system leaks. This 95% reduction in gas consumption translated into annual savings of over $150,000, and their payback period on the system was just 16 months. More importantly, the furnace atmosphere became incredibly stable, resulting in a perfectly consistent, brilliant finish on every coil of brass, virtually eliminating quality-related rejections.
Hydrogen recycling reduces costsTrue
Closed-loop hydrogen recycling can reduce gas consumption by up to 95%, dramatically lowering operational expenses.
Copper doesn't oxidize when heatedFalse
Copper readily forms oxide layers when heated in air, which is why protective atmospheres like hydrogen are necessary during annealing.
What safety concerns are associated with traditional copper annealing methods?
Do you lie awake worrying about the invisible threat of a hydrogen leak in your facility? Traditional annealing methods that continuously vent hot, flammable gas into the plant create a constant and unacceptable level of risk. This could lead to a catastrophic accident, jeopardizing your people and your entire operation.
Traditional copper annealing methods present significant safety concerns, primarily revolving around the high flammability and explosive potential of hydrogen gas. Key risks include undetected leaks from pipes and seals, the venting of combustible gas mixtures, and the danger of ignition from nearby heat sources.
I’ll never forget visiting an older plant years ago that was annealing copper tubing. There was a faint, sharp smell near the furnace line that the operators had grown accustomed to. It turned out to be a small but steady hydrogen leak from a corroded pipe fitting. While nothing had happened yet, the tension among the staff was real. They were working alongside a known, unmanaged hazard every single day. That experience drove home a critical point for me: furnace safety isn't just about complying with regulations on a piece of paper; it's about creating an environment where your team feels secure and can focus on their work without fearing for their well-being. The traditional "vent and burn" approach to hydrogen is fundamentally at odds with this goal. It treats a highly volatile gas as a disposable byproduct, releasing it into the workspace or atmosphere, where control is lost. This is a practice that belongs in the past, and modern engineering offers a much safer path forward.
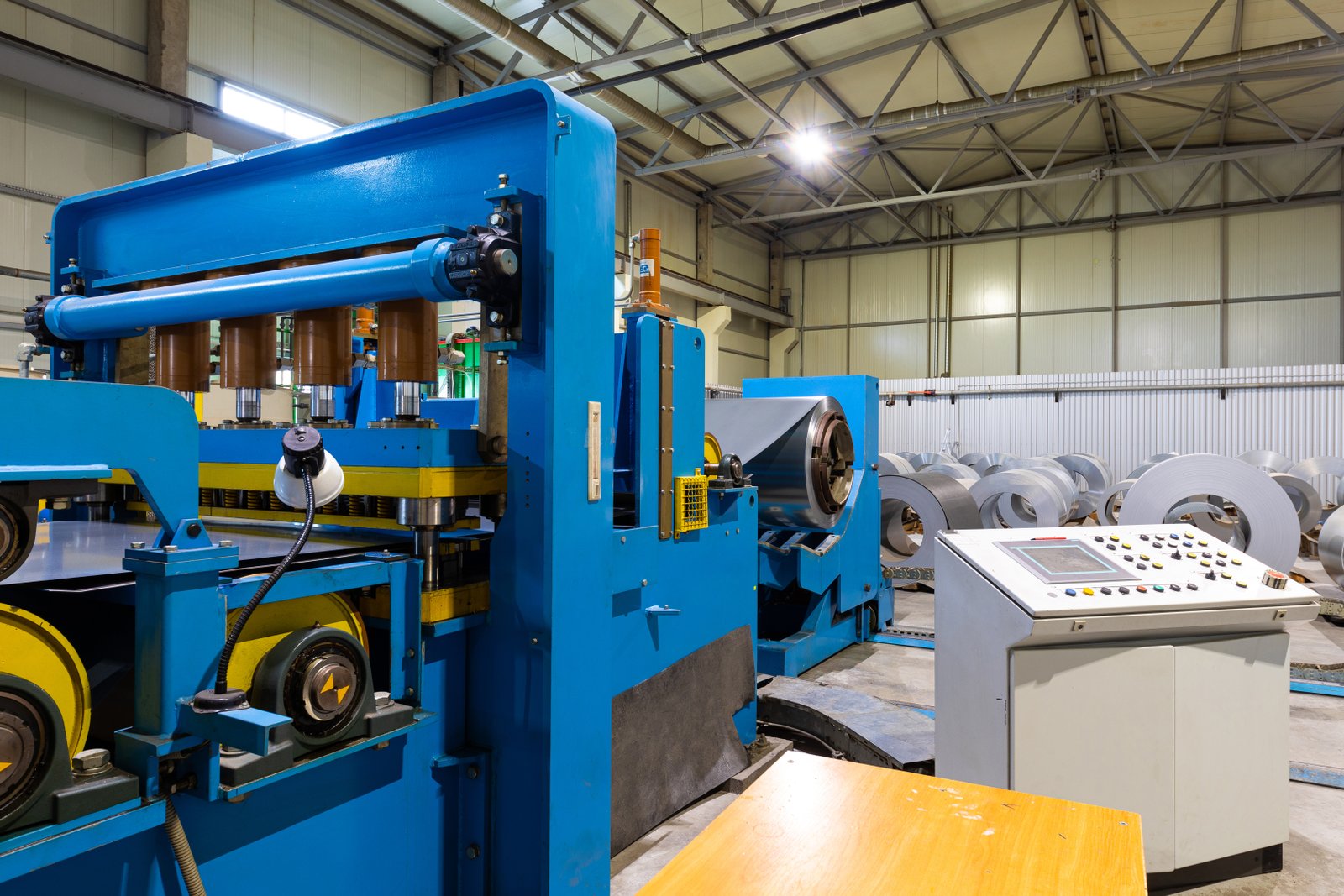
The risks are not theoretical. Industrial safety archives are filled with incident reports that trace back to the mismanagement of flammable process gases. In a traditional setup, you have a continuous flow of hydrogen from a storage tank, through a network of pipes, into the furnace, and out an exhaust vent. Every single connection point in that chain—every valve, every flange, every weld—is a potential leak point3. Furthermore, the vented gas itself is a hazard. If the "burn-off" flame at the exhaust stack extinguishes, you are essentially pumping an explosive gas directly into your facility's airspace. A random spark from electrical equipment, a cutting torch used for maintenance nearby, or even static electricity could be enough to trigger a devastating explosion. These legacy systems rely heavily on administrative controls and operator vigilance to manage these risks, a model that is prone to human error and complacency over time.
The "Invisible Danger": Understanding Hydrogen's Flammability Range
The primary reason hydrogen is such a significant safety concern is its exceptionally wide flammability range and low ignition energy. Hydrogen can ignite in air at concentrations ranging from a Lower Explosive Limit (LEL) of about 4% to an Upper Explosive Limit (UEL) of 75%. This is a far wider range than natural gas (~5-15%) or propane (~2-10%). This means that even a small leak can quickly create a combustible mixture, and a large leak remains a threat over a very broad range of concentrations. It doesn't take much to create a dangerous situation.
Compounding this risk is its physical nature. Hydrogen is the lightest element, so it rises and disperses very quickly in air. While this can be a benefit in open, well-ventilated areas, it allows the gas to accumulate in enclosed or overhead spaces like ceiling cavities, roof trusses, or even inside control cabinets. Furthermore, hydrogen requires very little energy to ignite—just 0.02 millijoules, which is about one-tenth the energy needed to ignite gasoline vapor. A tiny spark from a relay switch, a non-explosion-proof motor, or even the static discharge from a person's clothing could be sufficient to trigger a fire or explosion.
This "invisible danger" is why safety standards like the NFPA 86 (Standard for Ovens and Furnaces) are so stringent. They mandate specific ventilation, gas detection, and emergency shutoff systems. A report by the Chemical Safety Board (CSB) on industrial accidents frequently highlights incidents where flammable gas accumulated undetected before finding an ignition source. In a traditional annealing setup that constantly vents hydrogen, the risk profile is perpetually elevated because the system is, by design, releasing the hazard into the environment.
Common Failure Points in Legacy Systems
In older, traditional annealing installations, the safety of the entire system is only as strong as its weakest component. These systems are often a patchwork of pipes, valves, and regulators that have been in service for years, creating numerous potential failure points. Pipe fittings, especially threaded connections, can loosen over time due to thermal cycling and plant vibrations, creating slow, often undetected leaks. The flexible hoses sometimes used to connect gas supplies to the furnace are a notorious weak spot, susceptible to abrasion, kinking, and degradation from age.
The furnace muffle or casing itself is another critical point of failure. Over thousands of hours of operation, the high temperatures can cause the metal to warp, crack, or corrode, allowing the protective atmosphere to leak out or, even worse, allowing air to leak in. An inward leak of air into a hot, hydrogen-rich furnace can create an explosive mixture right inside the heating chamber, which is the most dangerous scenario possible. I once audited a facility where a hairline crack in the muffle weld seam was causing intermittent "popping" sounds from the furnace—a clear sign of small, contained explosions occurring inside. The operators had dismissed it as a normal operational noise.
Perhaps the most glaring failure point in traditional systems is the exhaust vent. These systems rely on a pilot flame or "burn-off" stack to ignite and safely dispose of the excess hydrogen. If this flame is extinguished by a gust of wind or system pressure fluctuations, the system then begins to pump raw, unburnt hydrogen gas into the atmosphere. Without a reliable flame supervision system and an automated reignition or shutdown protocol—features often lacking in older setups—a massive safety hazard is created in a matter of minutes.
The Human Factor and Procedural Gaps
Beyond mechanical failures, we must consider the human element, which is often the most unpredictable variable. In facilities with legacy equipment, operators may develop a sense of complacency over time. The daily presence of risk can become normalized, leading to shortcuts and procedural drift. I have seen operators bypass a faulty pressure switch with a jumper wire "just to get through the shift" because they perceived the alarm as a nuisance, unknowingly disabling a critical safety interlock.
Training is another significant gap. Operators may be trained on how to run the furnace for production but lack a deep understanding of the chemistry and physics of the gases they are working with. They may not fully appreciate why certain startup and shutdown sequences are so critical. For example, purging the furnace with an inert gas like nitrogen before introducing hydrogen is a fundamental safety step. Rushing this purge or using an insufficient volume of nitrogen can leave pockets of air in the furnace, setting the stage for an internal explosion when the hydrogen is introduced.
Emergency procedures in older plants can also be lacking. Are operators trained on how to respond to a large-scale hydrogen leak? Do they know the location of emergency shutoff valves? Have they participated in drills? In a real emergency, hesitation or incorrect actions can be the difference between a controlled shutdown and a disaster. Modern, automated systems help mitigate this by taking the critical, split-second decisions out of human hands. An integrated control system will automatically initiate a nitrogen purge and shut down gas flow the instant a sensor detects a dangerous condition, long before an operator might even realize something is wrong.
Hydrogen has wide flammability rangeTrue
Hydrogen can ignite at concentrations from 4% to 75% in air, making leaks particularly dangerous.
Vented hydrogen is always safeFalse
Vented hydrogen remains explosive if the burn-off flame extinguishes, creating serious explosion risks.
How can hydrogen-recycle systems improve safety in copper annealing?
Are you looking for a definitive way to remove the "what if" scenarios of hydrogen use from your safety meetings? Relying on operator vigilance alone is a recipe for anxiety. A fully contained, automated hydrogen-recycle system4 provides an engineered solution that elevates plant safety to a new level.
Hydrogen-recycle systems drastically improve safety by containing the flammable gas within a closed loop, minimizing potential leak points and eliminating the continuous venting of explosive gas. They integrate automated sensors and emergency shutdown protocols, removing the risk of human error in critical situations.
When I talk to safety managers, their primary goal is to "engineer out the hazard" wherever possible. A hydrogen recycling system5 is the embodiment of that principle. Instead of managing a constant flow of flammable gas through the plant and out a vent, you are creating a largely self-contained ecosystem. The total volume of hydrogen being actively moved through the plant at any given time is reduced, and the number of connections to the outside world is minimized. This fundamental shift in design philosophy from an "open" to a "closed" system is the single most impactful safety improvement you can make. It transforms hydrogen from a constant, flowing risk into a controlled, contained process utility, fundamentally changing the safety profile of your entire annealing operation.
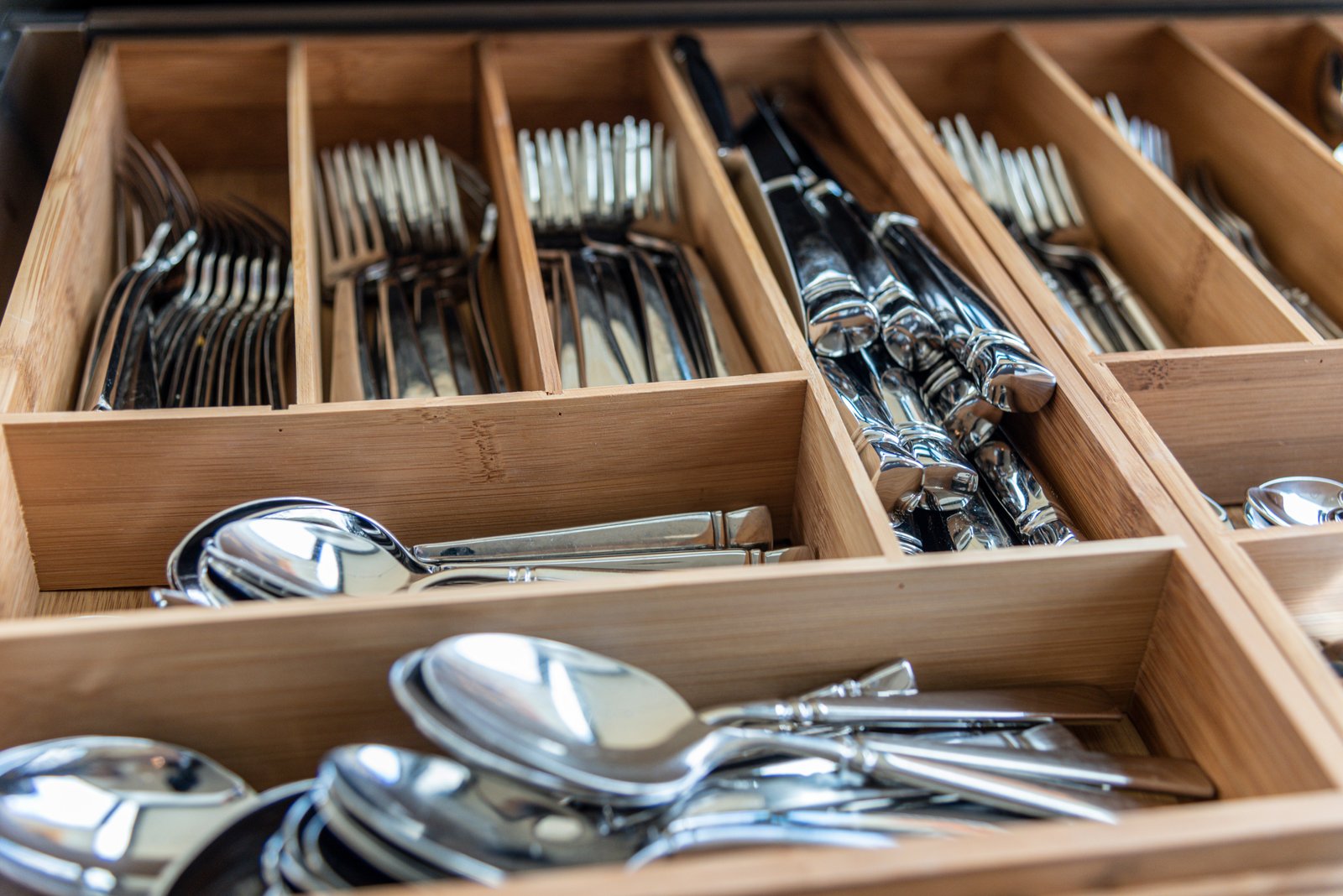
This enhanced safety is not just a theoretical benefit; it's built into the very mechanics of the system. Imagine the entire hydrogen lifecycle: it's fed into the furnace, performs its reducing function, is drawn out, purified, and returned. The entire path is sealed. This drastically reduces the surface area for potential leaks compared to a system with long pipe runs from a distant storage tank and an exhaust stack open to the atmosphere. Furthermore, the purification process itself adds a layer of safety. The gas is cooled to near-ambient temperatures before being purified and recirculated, meaning that even if a leak were to occur in the recycling unit, it would not involve the release of hot, more easily ignitable gas. This engineered containment provides a robust, reliable barrier against the release of flammable gas, which is the first and most important step in preventing accidents.
Engineering a Closed-Loop System: The Primary Safety Barrier
The core safety advantage of a hydrogen recycling system is its closed-loop design. In a traditional, single-pass system, you have a high-pressure source (like a cylinder bank or liquid H₂ tank) continuously feeding gas into the furnace, with the exhaust being vented. This creates a long, pressurized path with numerous potential weak points. In contrast, a closed-loop system operates more like a flywheel. A small amount of "makeup" gas is added initially to charge the system, but afterward, the vast majority of the hydrogen is simply circulated between the furnace and the purification unit.
This design dramatically reduces the two most significant risks: the quantity of gas being transported and the pressure at which it is moved. The recycling loop itself typically operates at a very low positive pressure, just enough to keep air from infiltrating the furnace. This is significantly lower than the high pressures found in gas supply lines, meaning any potential leak would be slower and less voluminous. By containing the process gas, we are applying the first and most effective principle of the hierarchy of safety controls: elimination. We are eliminating the constant, large-scale venting of a hazardous substance into the work environment.
A real-world example comes from a customer of ours who manufactures copper-clad aluminum wire. Their old setup had over 200 feet of high-pressure piping running from their outdoor hydrogen storage to the furnace line. They had a dedicated team member whose job included walking this line twice per shift with a portable gas detector. After installing an AKS furnace with an integrated recycling system, the high-pressure piping was reduced to a small, 10-foot section that only provides occasional makeup gas. The primary process loop is contained within a single, engineered skid. This not only saved them labor but also eliminated a huge source of risk and anxiety for their entire team.
Integrated Monitoring and Automated Shutdowns
Modern hydrogen-recycle systems are not just a collection of pipes and filters; they are intelligent systems managed by a Programmable Logic Controller (PLC). This PLC is the brain of the operation, and it provides a level of safety that is impossible to achieve with manual oversight alone. The system is fitted with a suite of integrated sensors that monitor critical parameters in real-time. Hydrogen sensors are placed at key points within the recycling unit and around the furnace to provide instant alerts if a leak is detected.
Pressure transducers, temperature sensors, and gas analyzers continuously monitor the health and composition of the atmosphere. The gas analyzer is particularly crucial. It constantly checks the purity of the recycled hydrogen. If it detects an unsafe level of oxygen (indicating an air leak into the furnace) or a drop in hydrogen concentration, it can trigger an immediate and automated safety protocol. This isn't just a flashing light or a loud alarm; the PLC is programmed to take decisive action.
In a hazardous event, such as the detection of a leak or an unsafe gas mixture, the system automatically initiates an emergency shutdown sequence. This typically involves closing the hydrogen supply valves, shutting down the furnace heaters, and initiating an emergency purge of the entire system with a high volume of inert gas, like nitrogen. This action renders the furnace atmosphere non-flammable within seconds, securing the situation long before an operator could even react to an alarm. This automation removes the potential for human error or hesitation in a crisis, providing a reliable, engineered safety net.
Reducing Human Interaction with Hazardous Gas
Every time a human interacts with a hazardous system, there is a potential for error. Traditional annealing systems require frequent manual intervention. Operators may need to manually adjust flowmeters, open and close valves during startup and shutdown, and manage the changeover of hydrogen cylinder banks. Each of these actions is a risk point. A technician might overtighten a fitting, causing a stress fracture, or fail to properly seal a connection when changing cylinders.
A hydrogen recycling system, by its automated nature, minimizes these required interactions. Once the system is running, it manages the atmosphere composition and flow rate automatically based on presets and sensor feedback. There are no daily manual adjustments to be made to the hydrogen flow. The PLC handles the precise control needed to maintain a perfect atmosphere, a task that is difficult to do manually with the same level of consistency.
This reduction in manual handling directly translates to enhanced safety. It reduces the number of opportunities for mistakes to occur. For instance, the system manages its own purification cycle, regenerating its desiccant dryers automatically without requiring an operator to open up the system or handle chemicals. A client in the automotive sector, producing bright annealed fuel lines, highlighted this as a major benefit. Their old process required technicians to manually swap out gas cylinders every shift. Since integrating a recycling system, their technicians interact with the high-pressure side of the hydrogen system perhaps once a month for routine checks, rather than multiple times a day. This has dramatically reduced their team's exposure to the hazard and streamlined their workflow.
Closed-loop systems minimize hydrogen leaksTrue
Hydrogen-recycle systems contain gas within a sealed loop, drastically reducing potential leak points compared to open venting systems.
Manual adjustments improve hydrogen safetyFalse
Automated recycling systems actually reduce safety risks by minimizing human interaction with hazardous gas through PLC-controlled operations.
What is the return on investment (ROI) when using hydrogen-recycle systems in copper annealing?
Is the high, recurring cost of hydrogen gas eating into your profit margins every month? Treating this expensive gas as a single-use consumable is a significant financial drain. A hydrogen-recycle system flips this expense into a rapid return on investment by preserving your most valuable process gas.
The return on investment for a hydrogen-recycle system is exceptionally strong, primarily driven by a reduction in hydrogen consumption of up to 95%. This drastic cut in gas purchasing costs often leads to a full payback period of less than two years for most industrial operations.
From a purely financial standpoint, this is one of the clearest investment decisions a plant manager can make. I consistently see companies hesitate due to the initial capital outlay, but they often overlook the relentless, compounding nature of their existing gas bill. It's a significant operational expenditure that appears on the books month after month, year after year. The ROI on a recycling system isn't a complex, abstract calculation; it's simple arithmetic. You are directly offsetting a massive, recurring cost. When we walk clients through the numbers, the "aha" moment is palpable. They realize they are essentially pre-paying for the recycling system every year with the money they are currently venting into the atmosphere.
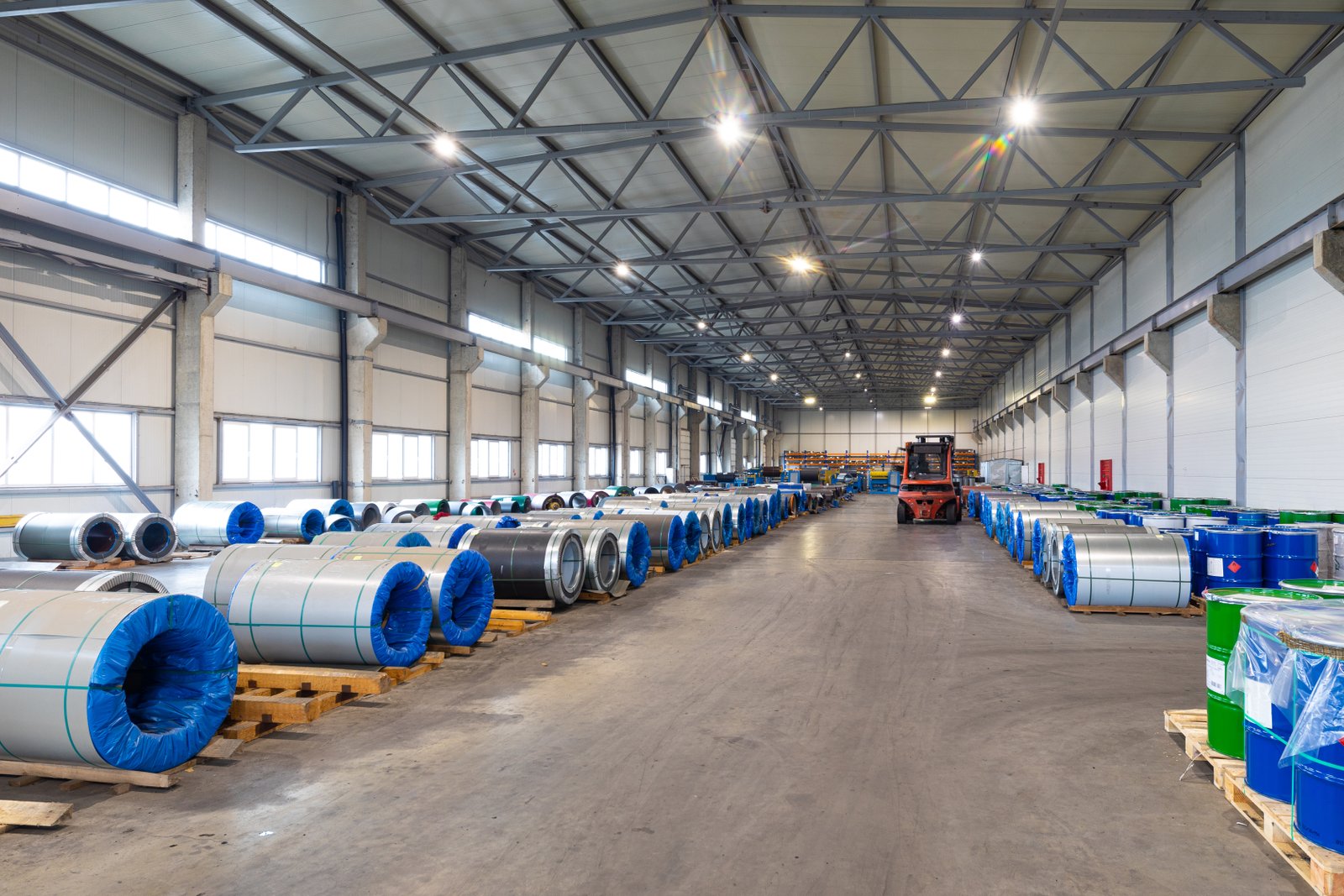
The financial case becomes even more compelling when you look beyond the gas savings. Think about the hidden costs associated with inconsistent quality. Every coil of copper strip or batch of parts that has to be re-annealed or scrapped due to surface oxidation is a direct loss of material, labor, and energy. Because a recycling system provides an ultra-pure and incredibly stable furnace atmosphere, process consistency improves dramatically. This leads to higher yields and lower rejection rates, which flows directly to your bottom line. One of our customers, a manufacturer of high-end cookware, found that their rejection rate for a bright-finished copper base dropped by 4% after implementation. That 4% improvement in yield, combined with their gas savings, shortened their already impressive payback period by an additional four months.
The Core Calculation: Reduced Gas Consumption
The primary driver of ROI is a dramatic reduction in hydrogen consumption. In a traditional single-pass system, the furnace must be continuously fed with a flow of fresh hydrogen to maintain purity and positive pressure. A typical medium-sized continuous annealing furnace might consume 50 cubic meters of hydrogen per hour (m³/hr). If the plant operates two shifts (4,000 hours/year) and the cost of hydrogen is, for example, $2.00 per cubic meter, the annual cost is straightforward:
- Annual Cost (Without Recycling): 50 m³/hr × 4,000 hr/year × $2.00/m³ = $400,000 per year
A hydrogen recycling system can recover and purify at least 95% of this gas. The only gas needed is a small "makeup" flow to compensate for the tiny amount consumed in reducing surface oxides and any minuscule system leaks. This reduces the consumption from 50 m³/hr to just 2.5 m³/hr. The new calculation is:
- Annual Cost (With Recycling): 2.5 m³/hr × 4,000 hr/year × $2.00/m³ = $20,000 per year
The direct annual saving is $380,000. If the total installed cost of the AKS furnace and integrated recycling system is, for example, $600,000, the simple payback period is calculated as:
- Payback Period: $600,000 (Investment) / $380,000 (Annual Savings) = ~1.58 years, or about 19 months.
This sub-two-year payback is a common outcome and presents a powerful business case for any CFO or stakeholder. The investment stops being a "cost" and is re-framed as a high-yield internal investment.
Secondary Financial Benefits: Quality, Uptime, and Maintenance
While gas savings provide the headline number, the secondary financial benefits are substantial and should not be underestimated. A highly stable and pure furnace atmosphere, which a recycling system guarantees, has a direct impact on product quality. For manufacturers of electronic components, consistent surface quality means better solderability and lower electrical resistance, leading to fewer field failures and warranty claims. For producers of decorative items, it means a consistently brilliant finish6, which commands a higher price in the market. Reducing the product rejection rate by even a few percentage points can add tens of thousands of dollars back to the bottom line annually.
Furthermore, modern, integrated systems are designed for high uptime. They feature robust components and predictive maintenance alerts that warn of potential issues before they can cause a shutdown. This contrasts sharply with older systems, where a failure in a brittle, aging component can bring the entire production line to a halt for days, leading to lost revenue and missed deadlines. The improved reliability and diagnostics of a new system contribute directly to Overall Equipment Effectiveness (OEE).
There are also savings in labor and maintenance. The automated nature of the system reduces the need for constant operator oversight. The logistics of managing gas supplies are also simplified. Instead of scheduling frequent deliveries of large hydrogen tube trailers or liquid dewars, the facility's gas needs are drastically reduced, simplifying procurement and reducing on-site storage hazards and rental fees.
Quantifying the Payback Period: A Case Study
Let’s consider a detailed case study of a "typical customer," a mid-sized manufacturer of stainless steel exhaust components for the automotive industry. They use copper as a brazing agent and require a bright finish to ensure corrosion resistance and a perfect braze. Their bogie hearth furnace was old and inefficient, using a continuous flow of a 25% H₂ / 75% N₂ gas blend.
Their initial situation was as follows:
- Gas Consumption: 80 m³/hr of the blended gas. (20 m³/hr of H₂)
- Operating Hours: 5,000 hours/year (2.5 shifts).
- Costs: Hydrogen at $2.50/m³, Nitrogen at $0.50/m³.
- Annual Gas Cost: (20 H₂ × $2.50 + 60 N₂ × $0.50) × 5,000 = $400,000
- Rejection Rate: Approximately 3% due to inconsistent surface oxidation.
They invested in a new AKS bell-type annealing furnace with an integrated hydrogen recycling system. The new system allowed them to run a superior 75% H₂ atmosphere for a better finish.
- Total Investment: $750,000 (Furnace + Recycling System).
- New H₂ Consumption: 95% reduction, now 1 m³/hr makeup.
- New N₂ Consumption: Used only for initial purging, negligible operational cost.
- New Annual Gas Cost: (1 H₂ × $2.50) × 5,000 = $12,500
- Annual Gas Savings: $400,000 - $12,500 = $387,500
- New Rejection Rate: Reduced to 0.5% due to stable, high-purity atmosphere, saving an additional $45,000 in scrap and rework costs.
The total annual savings amounted to $387,500 (gas) + $45,000 (quality) = $432,500. The payback period was therefore: $750,000 / $432,500 = 1.73 years, or just under 21 months. This clear, quantifiable return made the investment an easy decision for their management team.
Hydrogen recycling reduces gas costs by 95%True
The article demonstrates through calculations that hydrogen-recycle systems can reduce gas consumption from 50 m³/hr to just 2.5 m³/hr, achieving 95% savings.
Payback periods exceed 3 yearsFalse
Multiple case studies in the article show payback periods consistently under 2 years (19-21 months), making this claim false.
What are the best practices for implementing hydrogen-recycle systems in copper annealing processes?
Are you ready to make the switch but unsure how to ensure a smooth and successful implementation? Simply buying the equipment is not enough. Adopting best practices in integration, training, and maintenance is crucial to unlocking the full ROI and safety benefits of the technology.
Best practices for implementing hydrogen-recycle systems include ensuring proper system sizing and integration with your copper annealing furnace, providing comprehensive operator training on both operation and safety protocols, and establishing a proactive, long-term maintenance schedule to guarantee reliability and efficiency.
From my perspective, a successful implementation project is a partnership between the technology provider and the end-user. As a furnace manufacturer at AKS, we see our role as extending far beyond the point of sale. The most successful projects I've been a part of are those where the client's engineering team works closely with ours from the very beginning. This collaboration ensures that the recycling system isn't just an "add-on" but is deeply integrated into the furnace's control logic7 and physical footprint. This holistic approach prevents operational bottlenecks, simplifies maintenance access, and ensures the safety systems of the furnace and the recycler work in perfect harmony. Rushing the integration step is a common mistake that can lead to years of inefficiency and frustration.
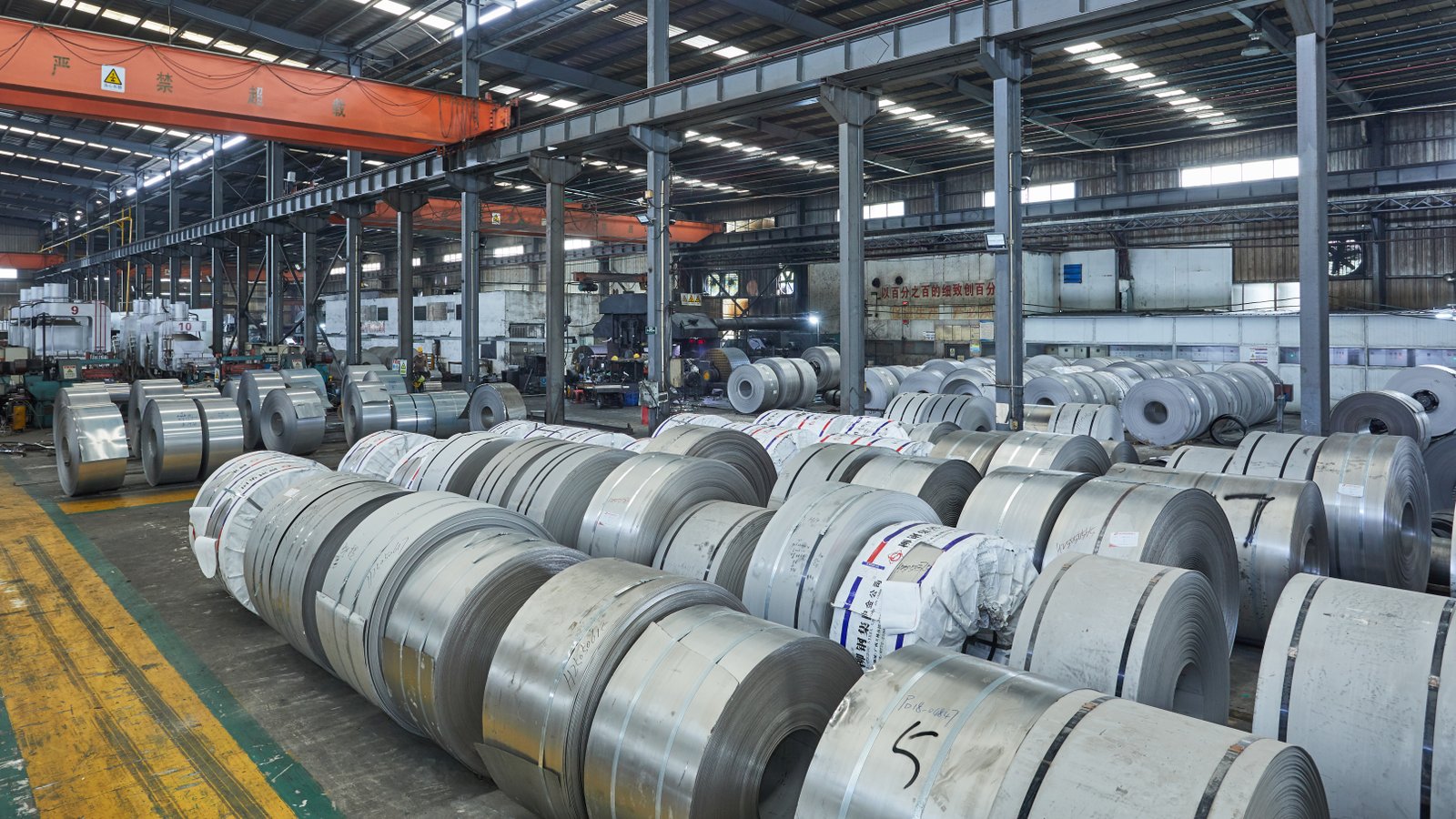
The long-term success of the system hinges on the people who interact with it every day. You can have the most advanced, automated system in the world, but if your operators and maintenance staff are not properly trained, you will never achieve its full potential. Training should not be a one-time event during commissioning. It needs to be an ongoing process, with regular refreshers and specific drills for emergency procedures. I strongly advocate for creating certified "expert users" within the client's team who can act as the first line of support and train new employees. This fosters a culture of ownership and in-house expertise, which is invaluable. A well-trained team is not only more efficient but is also your most critical safety asset. They will be the ones to spot a minor issue before it becomes a major problem.
System Sizing and Integration with the Furnace
The first best practice is to avoid a "one-size-fits-all" approach. The hydrogen recycling system must be correctly sized for the specific furnace it will serve. An undersized system will be unable to maintain the required gas purity and flow rate, leading to poor annealing results. An oversized system will be inefficient, consuming more energy than necessary and representing a higher, unjustified capital expense. The proper sizing calculation depends on several factors: the furnace's internal volume, its typical operating temperature, the expected level of air infiltration (door openings, seal quality), and the type of material being processed (which can release contaminants).
At AKS, we perform a detailed process audit before recommending a system. We analyze the customer's production cycle to determine the peak hydrogen demand, which typically occurs during the initial purge and heating phases. The recycling system—including its purifier capacity, blower speed, and cooler efficiency—is then engineered to meet this peak demand while operating efficiently during the steady-state holding phase.
Integration with the furnace's PLC is paramount. The two systems must communicate seamlessly. For example, the furnace's "door open" signal should automatically trigger the recycling system to adjust its flow to prevent contamination. Likewise, a critical alarm from the recycling system (e.g., "low H₂ purity") must be able to put the furnace into a safe hold or initiate an emergency purge. This deep level of integration creates a smart, responsive system that protects both the product and the plant.
Comprehensive Operator Training and Safety Protocols
Implementing advanced technology without investing in human capital is a recipe for failure. Training must go beyond the basic "how to start and stop the system." A comprehensive training program, compliant with standards like NFPA 86, should cover at least three key areas. First is routine operation: understanding the HMI (Human-Machine Interface), interpreting normal operating parameters, and knowing the proper startup/shutdown sequences.
Second is process theory: operators should understand why they are doing what they are doing. Why is the purge cycle so important? What happens to gas purity when a new, moist workload is introduced? This deeper understanding empowers them to make smarter decisions and troubleshoot minor issues. I once helped a client who was experiencing intermittent surface staining. Their operators, trained only on basic operation, couldn't solve it. A quick training session on how moisture from the workload affects the dew point of the atmosphere allowed them to adjust their loading procedure and solve the problem permanently.
Third, and most importantly, is safety and emergency response. This training cannot be passive. It must involve hands-on drills. What is the exact procedure if a hydrogen leak alarm sounds? Where are the emergency stops and inert gas purge buttons located? Who should be contacted? Operators should be able to execute these procedures from memory without hesitation. Regular, documented drills ensure this knowledge remains sharp and that your team is prepared to act correctly and decisively in a real emergency.
A Proactive Maintenance Schedule
A hydrogen recycling system is a sophisticated piece of equipment that requires regular, proactive maintenance to ensure its long-term safety, reliability, and efficiency. Waiting for something to break is the most expensive maintenance strategy. A well-structured preventive maintenance (PM) program is essential. This schedule should be developed in partnership with the equipment manufacturer and integrated into the plant's overall maintenance system.
The PM schedule should include daily, weekly, monthly, and annual checks. Daily checks might be as simple as a visual inspection for leaks and checking key pressure and temperature readings on the HMI. Weekly tasks could involve checking pump lubrication and inspecting filters. Monthly, the team might need to test the calibration of the hydrogen and oxygen analyzers to ensure they are providing accurate readings, as these are critical to both quality and safety.
The most critical maintenance items are typically the components of the purification train. The desiccant beds in the gas dryer, which remove moisture, have a finite lifespan and will need to be regenerated or replaced. The catalyst in the de-oxidation unit can also become fouled over time and require service. These are not tasks that should be delayed. A proactive schedule ensures they are handled before the gas purity starts to decline, preventing any negative impact on production. A well-maintained system will provide decades of safe, efficient, and reliable service.
Proper system sizing is crucialTrue
An undersized or oversized hydrogen-recycle system will lead to inefficiency and poor annealing results.
Training is a one-time eventFalse
Operator training should be an ongoing process with regular refreshers and emergency procedure drills.
Conclusion
Ultimately, adopting a hydrogen-recycle system for copper annealing is a strategic business decision. It provides a powerful, measurable ROI by dramatically reducing gas costs and improving product quality. More importantly, it fundamentally enhances plant safety by containing and controlling hydrogen gas, protecting both your profits and your people.
-
Learn why pure hydrogen ensures superior copper surface finish and process efficiency ↩
-
Understand the efficiency and safety differences between traditional and modern gas systems ↩
-
Learn about potential leak points in industrial gas piping systems ↩
-
Learn how hydrogen-recycle systems reduce risks in industrial applications ↩
-
Discover the role of recycling systems in improving flame safety ↩
-
Learn about the benefits of high-purity atmospheres for improved product finish ↩
-
Discover the benefits of integrating control systems in industrial furnaces. ↩