What Questions Should You Ask Before Purchasing an Annealing Furnace?
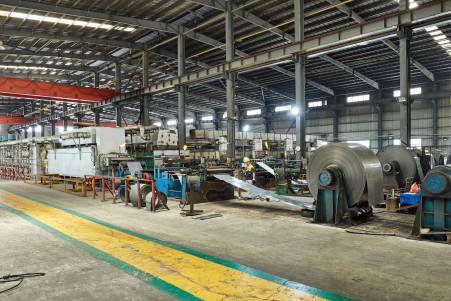
Are you struggling with inconsistent product quality and high operating costs from your current heat treatment process? The problem often lies in using a furnace that isn't tailored to your specific needs, leading to wasted energy and subpar results. Imagine achieving perfect material properties with every cycle.
The most critical questions to ask before purchasing an annealing furnace revolve around your material specifications, production volume, a supplier's technical expertise, the furnace's long-term operational costs, after-sales support, and the availability of customization to ensure the equipment perfectly aligns with your unique process requirements.
Making the right furnace investment can feel overwhelming. With so many technical specifications and suppliers to choose from, how do you ensure you're making a decision that will benefit your operations for years to come? This guide will walk you through the essential questions that separate a smart investment from a costly mistake.
I've spent my career at AKS Furnace helping clients navigate this exact challenge. The difference between success and failure often comes down to asking the right questions upfront. It’s not just about the initial price tag; it's about the total cost of ownership, reliability, and the quality of the final product. A furnace is a long-term asset, and a hasty decision can lead to years of operational headaches and financial strain. We will delve into the critical factors that demand your attention, from defining your process needs to evaluating a supplier's commitment to your success, ensuring you are equipped to choose a furnace that drives efficiency and profitability.
Why is it important to understand the specific annealing requirements for your operations?
Are you finding that your metal products suffer from inconsistent hardness or poor surface finish after annealing? This is often a direct result of a mismatch between the furnace's capabilities and your material's specific needs. A one-size-fits-all approach simply doesn't work in precision heat treatment.
Understanding your specific annealing requirements is crucial because factors like material type (e.g., stainless steel, copper), thickness, required metallurgical properties, and desired surface finish directly dictate the necessary furnace type, atmosphere control, and temperature profile for achieving consistent, high-quality results and operational efficiency.
Defining your needs with precision is the foundational step in selecting the right annealing furnace. It’s a conversation I have daily with potential clients. Many come to us with a general need for "an annealing furnace," but the real progress begins when we start dissecting the specifics. Are you processing thin stainless steel strips for automotive parts that require a bright, oxide-free surface? Or are you annealing heavy carbon steel components where achieving a specific grain structure is the primary goal? Each scenario demands a different solution. For instance, a Bright Annealing Furnace1 with a hydrogen-nitrogen protective atmosphere is ideal for the former, while a robust Bogie Hearth Furnace might be better suited for the latter. Without this initial clarity, you risk investing in a machine that either underperforms, leading to defects and rework, or is over-specified, causing you to pay for features you’ll never use. This initial due diligence doesn't just guide your purchase; it shapes the future of your production quality and efficiency.
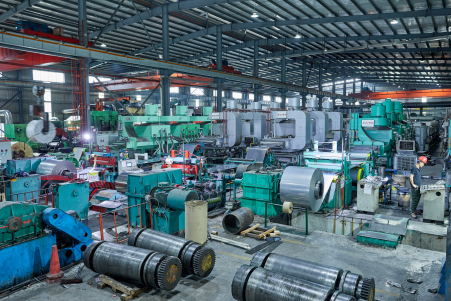
Understanding your requirements goes beyond just the material type. It involves quantifying your production goals. How many tons per hour do you need to process? What are the dimensions of your coils, strips, or parts? Answering these questions helps determine the physical size and throughput capacity of the furnace. I recall a client in the electronics industry who manufactured small copper connectors. They were using a batch-style furnace and struggling to keep up with demand. Their primary requirement wasn't just the annealing quality but also the production rate. By quantifying their throughput needs, we identified that our Mesh Belt Furnace was the perfect solution. It allowed for continuous processing of small parts, dramatically increasing their output while maintaining the precise metallurgical properties required for their high-end connectors. This transition was only possible because they first took the time to clearly define their operational volumes and process flow. Ignoring these details can lead to a bottleneck in your production line, negating the benefits of even the most advanced furnace. The goal is to find a solution that integrates seamlessly into your entire manufacturing ecosystem, and that starts with a detailed operational blueprint.
Understanding Your Material's Metallurgical Goals
The first step in defining your annealing needs is to look at the material itself. Different metals and alloys have unique thermal conductivity, chemical compositions, and crystalline structures, all of which dictate the ideal annealing cycle. For example, annealing 304 stainless steel2 to achieve a bright, corrosion-resistant surface requires a very different process than annealing high-carbon steel to achieve maximum softness for subsequent stamping operations. The former requires a furnace with precise atmosphere control (typically a mix of hydrogen and nitrogen) to prevent any surface oxidation, making a Continuous Bright Annealing Furnace the ideal choice. The latter focuses more on a controlled cooling rate to produce a specific pearlitic or spheroidized microstructure, where a Bell-Type Furnace might offer the necessary control over the cooling cycle.
I remember working with a client in India who was producing stainless steel kitchenware. They were experiencing "sugaring" (sensitization) on their products, which compromised corrosion resistance. Their existing furnace lacked the rapid cooling capabilities needed to bypass the critical 500-800°C range quickly enough for austenitic stainless steels. By first understanding their specific metallurgical goal—maintaining the steel's austenitic structure and chromium content in solution—we were able to recommend a furnace with an advanced cooling system. This system uses high-velocity, controlled airflow to ensure the material cools rapidly and evenly, completely eliminating the defect.
This illustrates that a deep understanding of your material's metallurgy is non-negotiable. You must be able to articulate the desired final grain size, hardness level (e.g., Rockwell or Vickers), and any specific microstructural features. Providing a potential supplier with this data allows them to engineer a solution that guarantees repeatable, high-quality results, moving you from a process of guesswork to one of scientific precision.
Quantifying Production Volume and Process Flow
Once the metallurgical requirements are clear, the next critical step is to quantify your production needs. This isn't just about your current output but also about your projected growth. A furnace is a significant long-term investment, and it must be able to support your business ambitions for the next 10-15 years. Key metrics to define include the required throughput in tons per hour or parts per day, the physical dimensions of the materials being processed (e.g., strip width and thickness, coil diameter, part size), and the overall process flow, including loading and unloading logistics. These factors directly influence the furnace type and configuration.
For instance, a high-volume stainless steel strip processor will benefit immensely from a continuous line like our Bright Annealing Furnace. Its design is optimized for non-stop production, integrating seamlessly with uncoilers and recoilers. In contrast, a manufacturer producing large, heavy, and varied components, such as castings or forged parts, would find a batch-style Bogie Hearth Annealing Furnace far more practical. The ability to load and unload large, cumbersome items with an overhead crane makes it a more flexible solution for non-uniform production schedules.
A client of ours, a manufacturer of automotive components, initially requested a quote for a large continuous furnace based on their peak production forecast. However, after we analyzed their typical monthly production data, we realized their workflow was characterized by frequent product changeovers with varying annealing specifications. A large continuous furnace would have incurred significant downtime and energy waste during these changeovers. Instead, we proposed a solution with two smaller, more agile Mesh Belt Furnaces. This not only met their total throughput requirement but also provided the flexibility to run different annealing cycles simultaneously, drastically improving their operational agility and reducing energy consumption during periods of lower demand. This highlights the importance of a data-driven approach to quantifying your needs, ensuring the chosen solution matches your real-world operational dynamics.
Defining Surface Finish and Atmospheric Requirements
The final piece of the puzzle is defining the required surface quality of your annealed product. This single factor often has the most significant impact on the complexity and cost of the furnace. Is a simple stress relief with some surface oxidation acceptable, or do you require a mirror-bright, oxide-free surface ready for immediate use or plating? The answer determines the type of furnace atmosphere required, which can range from open-air firing to highly controlled inert or reducing atmospheres.
For products like electronic connectors, high-end kitchenware, or medical devices, a bright finish is non-negotiable. This necessitates a furnace, such as a Bell-Type or Bright Annealing Furnace, that can maintain a positive pressure with a protective atmosphere. This atmosphere, typically a blend of nitrogen (N₂) and hydrogen (H₂), actively prevents oxygen from coming into contact with the hot metal surface. The purity of this atmosphere is paramount; even trace amounts of oxygen or water vapor can cause discoloration. Our furnaces at AKS are designed with gas-tight chambers and advanced atmosphere control systems to ensure pristine surface quality.
Consider the case of a Southeast Asian manufacturer of decorative stainless steel tubing. They were struggling with inconsistent brightness and occasional blueing, leading to high rejection rates. Their problem was traced back to poor atmosphere control in their outdated furnace. After upgrading to an AKS Bright Annealing Furnace with a precision gas mixing station and oxygen sensor feedback loop, they were able to achieve a consistently brilliant finish. This not only reduced their scrap rate to nearly zero but also allowed them to command a higher price for their premium-quality products. This demonstrates that investing in the right atmosphere control technology is not just a cost; it's a direct investment in the market value of your products.
Material type dictates furnace choiceTrue
Different metals like stainless steel vs copper require completely different furnace types and atmosphere controls for proper annealing.
All annealing furnaces are interchangeableFalse
A bright annealing furnace for stainless steel cannot be used for carbon steel annealing as they have fundamentally different metallurgical requirements.
How does a supplier's experience and expertise impact the quality of their annealing furnaces?
Have you ever purchased equipment that looked good on paper but failed to perform in a real-world production environment? The issue often stems from a supplier's lack of deep, hands-on experience. A spec sheet can't capture the nuances of furnace design that only come from years of practice.
A supplier's experience directly impacts furnace quality through proven design principles, metallurgical knowledge for process optimization, and robust construction. An experienced supplier like AKS Furnace translates years of solving real-world challenges into more reliable, efficient, and durable equipment tailored to specific industry needs.
Choosing a supplier is as critical as choosing the furnace itself. An experienced partner has encountered and solved a vast array of heat treatment challenges across different industries. This accumulated knowledge translates into smarter design choices, more reliable components, and a deeper understanding of how to optimize a furnace for a specific material and application. When you partner with an experienced supplier, you're not just buying a piece of machinery; you're gaining access to a wealth of engineering expertise that ensures your furnace will deliver on its promises from day one and for years to come.
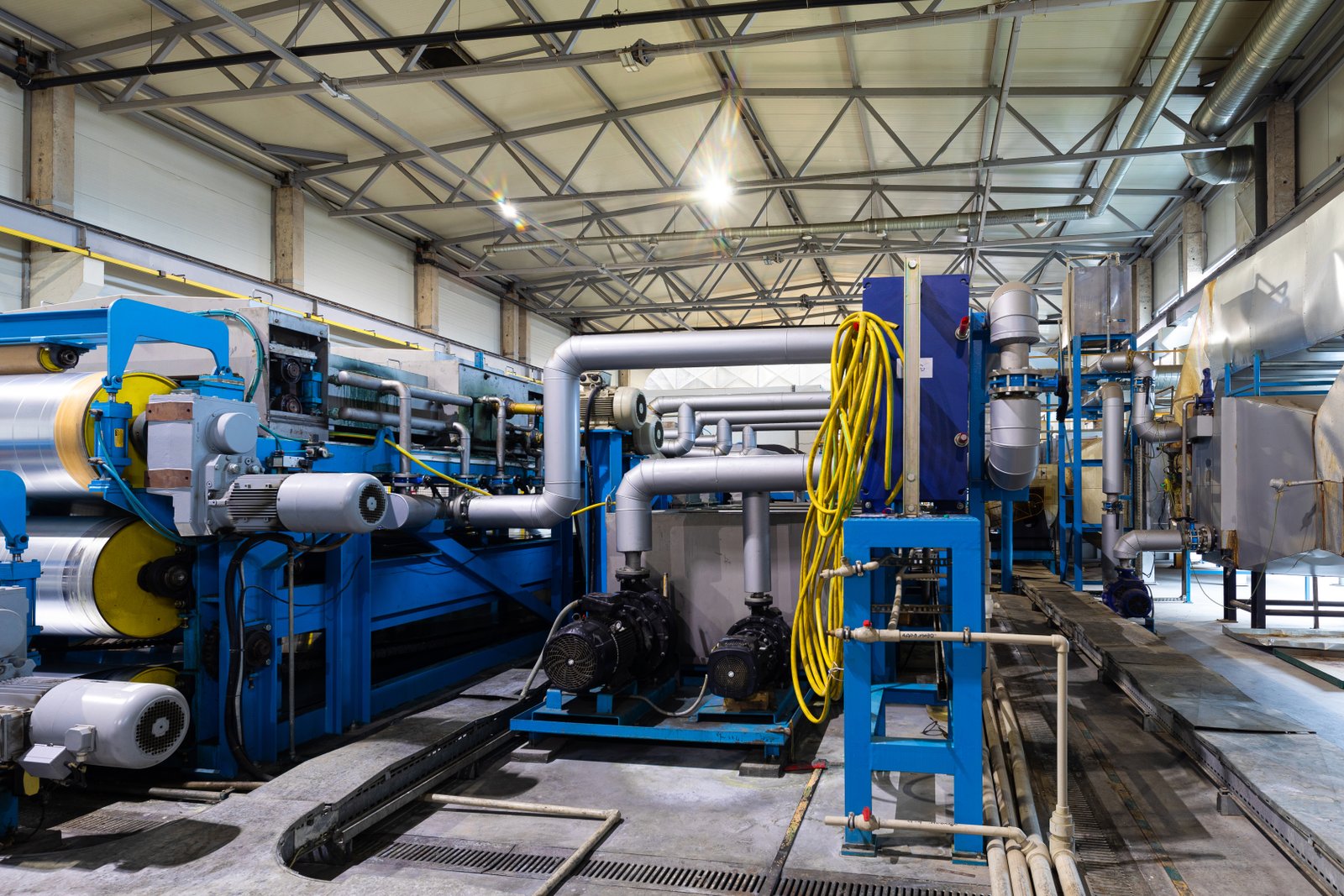
At AKS, our experience is embedded in every furnace we build. It’s in the way we design our muffle chambers3 for uniform heat distribution, the specific insulation materials we choose to minimize thermal loss, and the control logic we program into our PLCs for precise cycle replication. I’ve personally seen how this expertise makes a tangible difference for our clients. For example, a carbon steel strip processor came to us with a problem of inconsistent mechanical properties across the width of their strips. Our engineers, drawing on decades of experience with heat transfer dynamics, identified that the issue was not just about temperature but about the uniformity of heat application. We designed a custom furnace with a multi-zone heating system and strategically placed convection fans. This wasn't a standard feature on a checklist; it was a solution born from a deep understanding of thermodynamics and process metallurgy. The result for the client was a dramatic improvement in product consistency, which opened up new markets for their high-quality steel. This is the kind of value-add that only comes from a supplier whose expertise goes far beyond simple assembly and manufacturing.
Proven Design and Engineering Prowess
A supplier's experience is most evident in the sophistication and reliability of their furnace designs. A furnace is a complex system where thermal, mechanical, and chemical processes must work in perfect harmony. An experienced manufacturer has a library of proven designs4 and has refined them over hundreds of installations. This refinement process eliminates common points of failure, optimizes energy consumption, and enhances user safety. For instance, the design of a furnace muffle or radiant tube heating system is critical for temperature uniformity. An inexperienced supplier might use a generic design, resulting in hot and cold spots within the chamber, leading to inconsistent annealing.
At AKS, our engineering team leverages finite element analysis (FEA) and computational fluid dynamics (CFD) modeling during the design phase. However, these powerful tools are guided by decades of real-world data and practical experience. We know how different alloys behave under heat, how protective atmospheres flow within a chamber, and how structural components expand and contract over thousands of thermal cycles. This expertise allows us to design features like our dual-layer furnace chamber with integrated heat exchange. This isn't just a theoretical concept; it's an engineered system we've perfected over time to maximize waste heat recovery, directly lowering our clients' energy bills.
A client in the automotive sector, producing stainless steel exhaust components, chose us specifically because of our proven track record with bright annealing applications. They had previously worked with a less experienced supplier and suffered from frequent muffle warping and cracking, leading to costly downtime and atmosphere leaks. Our design incorporated high-grade alloys for the muffle construction and a unique support system that accommodates thermal expansion without inducing mechanical stress. This experienced-based design has resulted in over five years of uninterrupted operation for the client, a testament to how engineering prowess translates directly into operational reliability and profitability.
Deep Metallurgical and Process Knowledge
Beyond mechanical design, a top-tier supplier possesses deep knowledge of metallurgy and process control5. They understand that the furnace is just one part of a larger manufacturing process. Their expertise extends to how pre-treatment, annealing, and post-treatment interact to produce the desired final product. This holistic understanding allows them to act as true consultants, not just equipment vendors. They can advise on the optimal time-temperature cycles, the most effective protective atmosphere compositions, and the ideal cooling rates for your specific material and application.
For example, a customer processing copper-beryllium alloys for electronics required both softening and age-hardening capabilities in a single solution. This requires a furnace capable of extremely precise and repeatable temperature control for both the high-temperature solution annealing and the lower-temperature aging process. Drawing on our experience with specialty alloys, we engineered a Vacuum Annealing Furnace with a multi-step programming interface and a high-performance quenching system. We also provided detailed process recipes as a starting point for their R&D team.
This collaborative approach is a hallmark of an experienced supplier. We recently assisted a carbon steel strip producer who was struggling to achieve the specific spheroidized microstructure needed for a deep-drawing application. Their existing process was inconsistent. Our process metallurgists worked with their team, analyzed their material, and helped them fine-tune their annealing cycle using one of our Bell-Type Annealing Furnaces. The precise atmosphere and temperature control of our furnace allowed them to consistently achieve a 95%+ spheroidization rate, drastically reducing tool wear in their stamping presses and improving the quality of their final product. This level of process optimization is a service that simply cannot be offered by a supplier who only knows how to build the box but doesn't understand the science that happens inside it.
Robust Manufacturing and Quality Control
ly, a supplier's experience is reflected in their manufacturing standards and quality control (QC) processes. Building a durable industrial furnace requires expertise in high-temperature material welding, refractory installation, and electrical system integration. An established manufacturer has mature supply chains for high-quality components and rigorous QC checkpoints throughout the entire production process. This ensures that every weld is sound, every inch of insulation is properly installed, and every control panel is wired to international standards.
Feature Comparison | Experienced Supplier (e.g., AKS) | Inexperienced Supplier |
---|---|---|
Muffle/Chamber Material | High-grade, certified alloys (e.g., 310S, Inconel) with full traceability. | Uncertified or lower-grade materials to cut costs. |
Welding Standards | Certified welders, X-ray/ultrasonic testing on critical seams. | Visual inspection only, higher risk of leaks or cracks. |
Control System | Siemens/Mitsubishi PLC with custom, process-optimized logic. | Generic PLC with basic, inflexible programming. |
Refractory/Insulation | Multi-layer ceramic fiber modules with staggered joints for minimal heat loss. | Single-layer or poorly fitted insulation, leading to energy waste. |
Post-Sale Support | Established global network for service and spare parts. | Limited or non-existent support, long wait times for parts. |
This table illustrates the tangible differences in quality. We had a client from the Middle East who had purchased a furnace from a newer, low-cost supplier. Within two years, they faced significant refractory degradation and insulation collapse, causing their energy consumption to skyrocket. When they came to us for a replacement, we showed them our manufacturing facility and our QC procedures. They could see the difference in the quality of the raw materials, the precision of the construction, and the thoroughness of our final testing, which includes a 72-hour hot-fire test before any furnace is shipped. Investing in a furnace from an experienced manufacturer like AKS means investing in a product that is built to last, perform efficiently, and deliver a reliable return on investment for years to come.
Experience improves furnace designTrue
Experienced suppliers like AKS use real-world data to optimize furnace components and thermal performance.
All furnaces perform equallyFalse
The article shows how inexperienced suppliers often produce furnaces with hot/cold spots and reliability issues.
What should you consider regarding the furnace's energy efficiency and operational cost?
Are your energy bills eating into your profit margins? An inefficient furnace is often a hidden drain on your company's finances, consuming far more gas and electricity than necessary. This waste directly impacts your bottom line and your environmental footprint, making cost control a daily battle.
When considering an annealing furnace, you must evaluate its energy efficiency factors by examining insulation quality, burner technology, and waste heat recovery systems. These factors, along with maintenance needs and consumable usage, determine the total operational cost, which is crucial for long-term profitability.
The initial purchase price of a furnace is only a fraction of its total cost of ownership. Over a furnace's lifespan of 15-20 years, energy consumption analysis6 can represent the single largest expense. Therefore, prioritizing energy efficiency isn't just an environmental choice; it's a critical financial decision. At AKS, we engineer our furnaces with advanced energy-saving systems, because we know that reducing our clients' operational costs is key to their success. A furnace that saves you money every hour it runs is a far better investment than a cheaper alternative that guzzles energy.
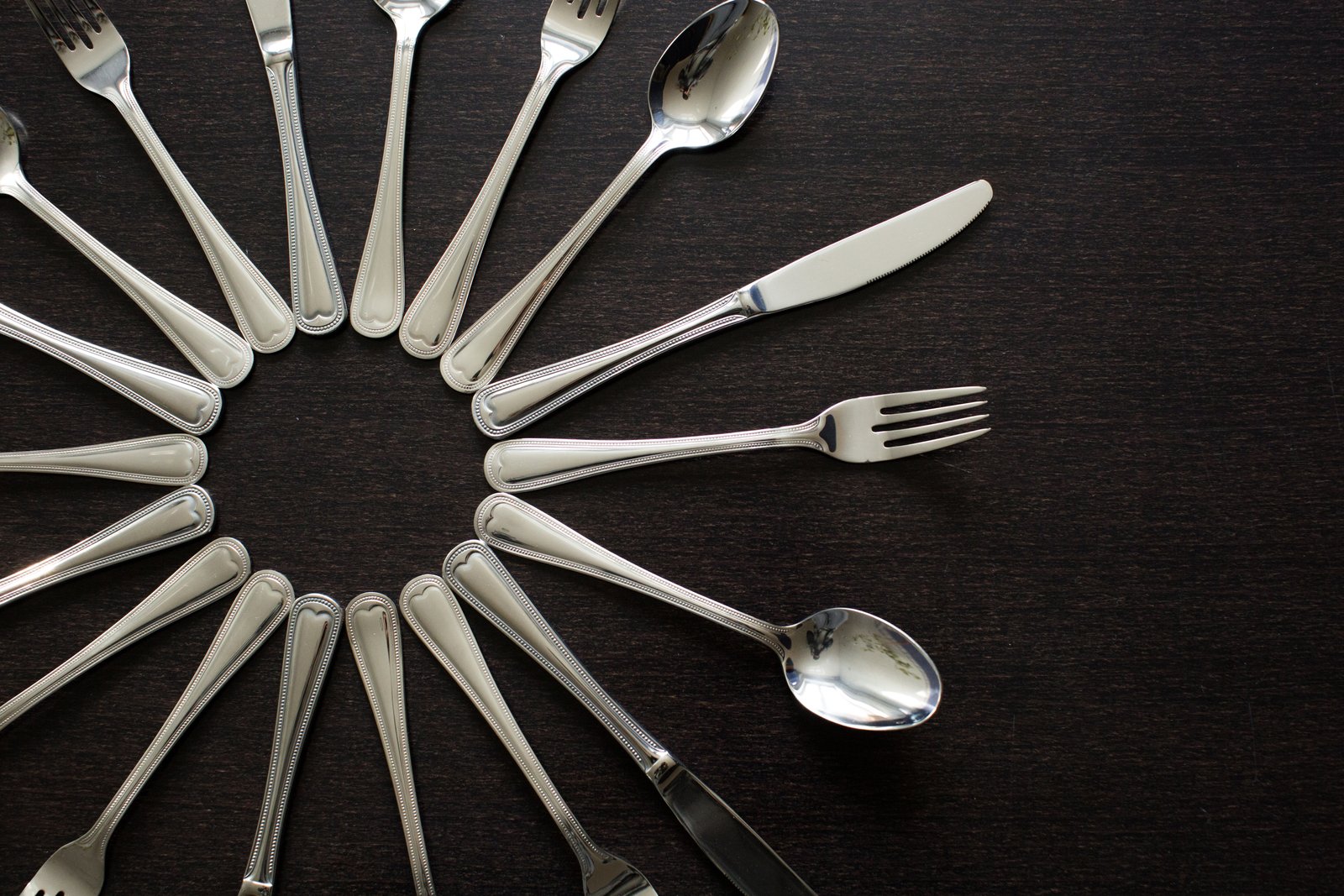
Thinking about long-term costs requires a shift in perspective. Instead of asking "What is the price?", the better question is "What is the cost per ton of annealed product?". This calculation includes energy, atmosphere gases, spare parts, and labor. I worked with a large steel coil processor who was operating older furnaces. They were hesitant to invest in a new line, focusing solely on the capital expenditure. We conducted a comprehensive audit of their existing operations and compared their energy consumption per ton to what they could achieve with our modern Bright Annealing Furnace. Our furnace, equipped with a waste heat recovery system to preheat combustion air and a precision gas-to-air ratio control system, demonstrated a potential energy saving of over 30%. When they saw the five-year projection of these savings, the decision became clear. The new furnace wasn't a cost; it was an investment with a definable payback period. This is why a thorough analysis of operational costs is not just recommended—it's essential for making a strategically sound financial decision.
Analyzing Key Energy-Saving Technologies
The core of an energy-efficient furnace lies in its technology. Three primary areas make the biggest impact: insulation, combustion control, and heat recovery. High-quality insulation, typically multi-layered ceramic fiber, is the first line of defense against thermal loss. A well-insulated furnace requires less energy to maintain its target temperature. Look for designs with minimal thermal bridging and tightly sealed doors and openings. The second critical technology is the combustion system. Modern furnaces utilize precision control of the gas-to-air ratio, ensuring that fuel is burned completely and efficiently. This prevents both energy waste from unburned fuel and process issues from an oxidizing atmosphere.
The most advanced systems, however, incorporate waste heat recovery. The exhaust gases from a furnace can be extremely hot—often exceeding 800°C. Venting this heat directly into the atmosphere is like watching money disappear into thin air. At AKS, our furnaces feature a dual-layer chamber design with an integrated heat exchanger. This system captures the high-temperature exhaust and uses it to preheat the incoming combustion air. By preheating the air, the burners require significantly less fuel to reach the same flame temperature. This single feature can reduce overall gas consumption by 15-30%, representing a massive operational saving over the furnace's lifetime.
A case in point is a client of ours in the aluminum strip industry. Aluminum annealing is a lower-temperature process, but it still consumes significant energy. By retrofitting their existing line with our external waste heat recovery unit, they were able to cut their natural gas consumption by 22%. This project paid for itself in less than 18 months and continues to deliver savings every day, demonstrating the powerful ROI of investing in proven energy-saving technology.
Calculating the Total Cost of Ownership (TCO)
The purchase price is just the tip of the iceberg. A true evaluation of a furnace's cost-effectiveness must consider its Total Cost of Ownership (TCO). TCO is a comprehensive financial model that includes not only the initial capital investment but also all direct and indirect costs over the asset's lifecycle. Key components of TCO include energy consumption (gas and electricity), protective atmosphere gas usage (nitrogen, hydrogen), consumable parts (heating elements, thermocouples), routine maintenance costs, and potential downtime costs.
To calculate TCO, you must request specific data from the supplier. Ask for the furnace's rated energy consumption per hour at typical operating temperatures and its expected consumption of atmosphere gases. An experienced supplier should be able to provide these figures based on real-world operational data from similar installations. For example, our team can provide a detailed projection for a Bright Annealing Furnace, estimating the kilowatt-hours and cubic meters of hydrogen and nitrogen required to process one ton of 304 stainless steel.
Let's consider a practical example. A medium-sized metal processing factory was comparing two furnaces. Furnace A had a lower purchase price by $50,000. However, its rated energy consumption was 25% higher than our AKS Furnace B, which was equipped with waste heat recovery. The factory operates 6,000 hours per year. By calculating the annual energy cost difference, they discovered that Furnace B, despite its higher initial cost, would save them over $30,000 per year in energy alone. Over a 10-year period, the TCO for Furnace B was significantly lower. This analysis shifted their focus from short-term savings to long-term profitability and made the choice clear. Always insist on the data needed to perform a TCO calculation before making a final decision.
The Impact of Maintenance and Consumables
Often overlooked in the initial assessment, maintenance requirements and the cost of consumable parts can have a substantial impact on a furnace's operational budget. A well-designed furnace minimizes the need for frequent maintenance and uses durable, long-lasting components. Key areas to inquire about include the expected lifespan of critical components like heating elements, radiant tubes, muffles, and conveyor belts. Ask the supplier about the materials used for these parts. For example, are the heating elements made from a high-quality alloy like Nikrothal or Kanthal, known for their long service life at high temperatures?
At AKS, we focus on building low-maintenance furnaces. We use high-grade alloys like 310S stainless steel or Inconel for our muffles and radiant tubes, which offer superior resistance to high-temperature corrosion and thermal cycling stress. This extends their lifespan and reduces the frequency of costly replacements. Furthermore, we design our furnaces with maintenance accessibility in mind. Components that require periodic inspection or replacement, like thermocouples and drive motors, are placed in easily accessible locations to minimize the time and labor required for service.
I recall a client who operated a Mesh Belt Furnace from another manufacturer for sintering small metal parts. They were experiencing frequent belt stretching and warping, leading to almost monthly shutdowns for repairs and replacement, which was a significant hidden cost. When they upgraded to an AKS furnace, they were impressed by the robust construction of our conveyor belt and the variable speed drive system that minimizes stress on the belt during startup and shutdown. Their unscheduled downtime dropped by over 90%, and their annual spending on replacement belts was cut in half. This highlights the importance of scrutinizing the design and material quality of a furnace's wearable components as a critical part of evaluating its true long-term operational cost.
Energy efficiency impacts operational costsTrue
The article clearly states that energy consumption represents the largest expense over a furnace's lifespan, making efficiency crucial for long-term profitability.
Purchase price determines total costFalse
The text emphasizes that initial price is only a fraction of total ownership costs, with energy, maintenance and consumables being more significant factors.
How can you assess a supplier's customer support and after-sales service offerings?
What happens when your new, expensive furnace experiences a technical issue during a critical production run? If your supplier is unresponsive or lacks a robust support system, you face costly downtime and broken promises to your own customers. The quality of after-sales service is a crucial, yet often overlooked, factor.
To assess a supplier's customer support, you should evaluate their installation and training processes, the availability and responsiveness of their technical support team, their spare parts logistics, and the scope of their long-term warranty and maintenance programs. These elements ensure minimal downtime and long-term reliability.
A furnace is a complex piece of equipment that will inevitably require service and support throughout its long life. A supplier's commitment doesn't end when the invoice is paid; in many ways, it's just beginning. A strong after-sales support structure is your insurance policy against unforeseen problems. It ensures that you have a knowledgeable partner ready to assist with troubleshooting, provide necessary parts, and help you maintain peak performance, safeguarding your investment and your production schedule.
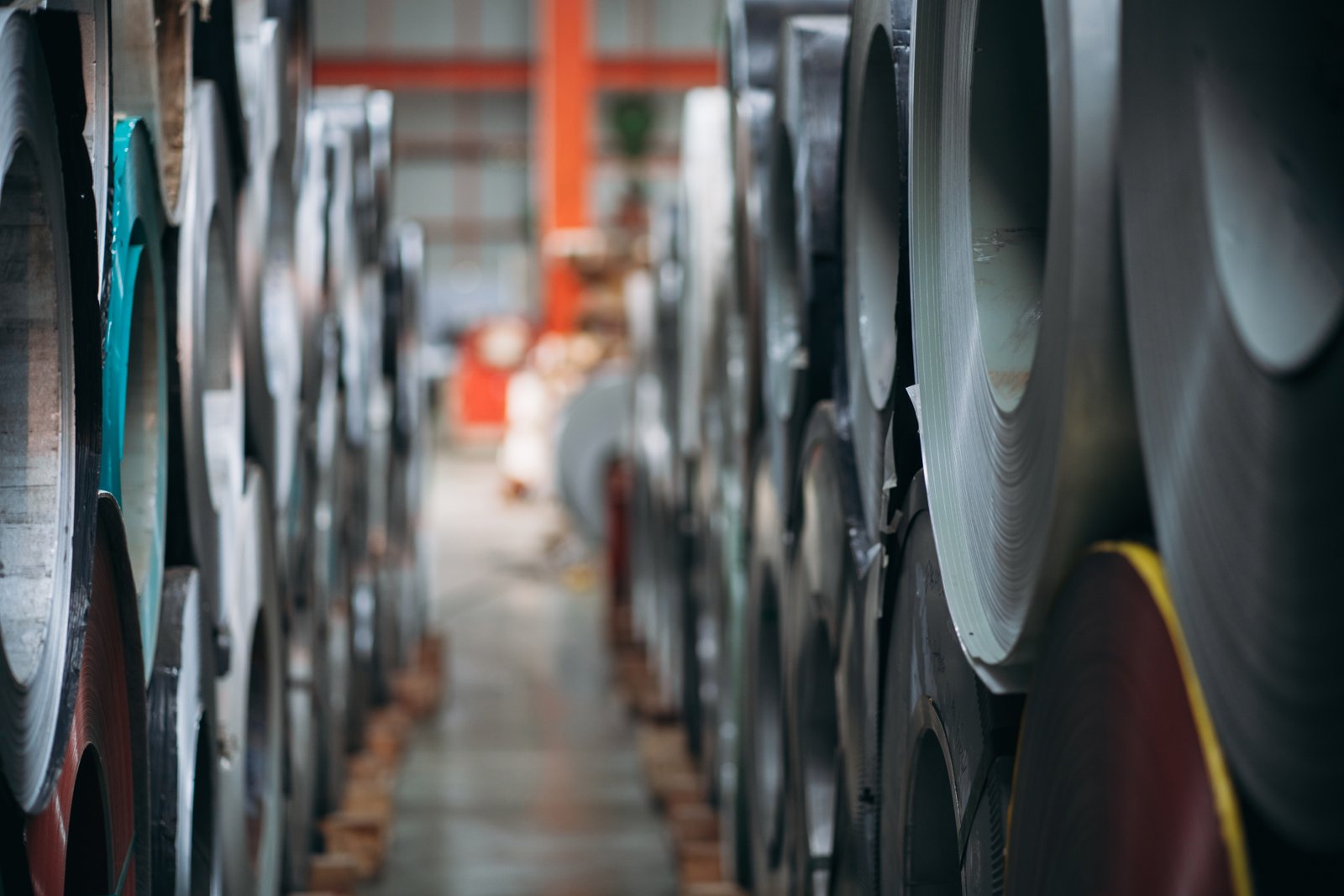
From my position at AKS, I see after-sales support as a cornerstone of our business model. We are not just selling a product; we are entering a long-term partnership with our clients. I remember a situation with a customer in Southeast Asia whose furnace operator accidentally misconfigured a critical heating parameter, causing the system to fault. It was the middle of their night shift. They contacted our 24/7 support line, and our engineers were able to remotely access the furnace's PLC via a secure internet connection. Within an hour, they had diagnosed the incorrect setting, guided the local operator through the correction process, and brought the furnace back online. This rapid response7 saved the client from losing an entire night's production. This is the kind of responsive, technologically enabled support that separates a great supplier from a good one. It's the peace of mind that comes from knowing an expert is always on call, ready to help you overcome any challenge.
Evaluating Installation, Commissioning, and Training
The journey with a new furnace begins with its installation and commissioning. A professional supplier will not simply ship a crate to your door. They should offer comprehensive support to ensure the equipment is installed correctly, integrated with your existing utilities, and commissioned to perform exactly as specified. This process should be managed by experienced field engineers who understand both the furnace's mechanics and your facility's unique environment. Inquire about the scope of their installation service: does it include leveling, utility hook-up supervision, and a full range of hot and cold testing?
Equally important is the training provided to your operators and maintenance staff. A furnace's performance and longevity are highly dependent on how it is operated and maintained. A thorough training program is essential. At AKS, our commissioning process includes multi-day, hands-on training for the client's team. We cover everything from routine startup and shutdown procedures to programming annealing cycles, understanding alarm codes, and performing preventative maintenance tasks. We don't leave until your team is confident and competent in managing their new asset.
I recently oversaw a project for a large carbon steel processor in Europe. Their team was skilled but unfamiliar with the specific Siemens PLC interface we use. Our field engineer spent an extra two days with their lead operators and electricians, creating custom cheat sheets and running through various simulated fault scenarios. This investment in comprehensive training empowered their team to handle minor issues independently, fostering self-sufficiency and reducing their reliance on external support for day-to-day operations. When evaluating a supplier, ask for a detailed training agenda and inquire about the qualifications of their field engineers.
Assessing Technical Support and Responsiveness
When an issue arises, the speed and quality of the supplier's technical support are paramount. Every hour of downtime can translate into thousands of dollars in lost production. Before you buy, you must assess the supplier's support infrastructure. Do they offer 24/7 support? What are their guaranteed response times? Do they have a multi-lingual team to support your local operators? A key differentiator in the modern era is the availability of remote diagnostics. Furnaces equipped with industrial IoT capabilities allow supplier engineers to securely log into the control system from anywhere in the world to diagnose problems, analyze performance data, and guide on-site staff through solutions.
This is a standard feature on all AKS furnaces. We understand that our clients are located all over the globe, in different time zones. Our remote support system is our commitment to being there for them, anytime. For a client in Mexico running a Mesh Belt Furnace for small automotive fasteners, this capability proved invaluable. They experienced an unusual temperature fluctuation in one of their heating zones. Instead of waiting for an engineer to fly in, our team logged in remotely, analyzed the trend data from the past 48 hours, and identified a failing thermocouple that was beginning to send erratic signals. We guided their maintenance team to the exact component, which they were able to replace from their stock of spare parts. The entire issue was resolved in under two hours.
When speaking with potential suppliers, ask them to walk you through their support process. Present them with a hypothetical problem and ask how they would handle it. Their answer will reveal a lot about their internal processes, technical capabilities, and overall commitment to minimizing your downtime.
Availability of Spare Parts and Long-Term Warranty
A furnace is an assembly of many components, some of which will naturally wear out over time. A critical aspect of after-sales service is the supplier's ability to provide replacement parts quickly and efficiently. A supplier with a well-organized logistics network and a policy of maintaining stock of critical spares can significantly reduce your potential downtime. Before purchasing, you should request a list of recommended critical spare parts to keep on-site. Also, inquire about the supplier's standard delivery times for parts that you don't stock. Do they have regional distribution centers or partners to expedite shipping to your location?
The warranty offered is another indicator of a supplier's confidence in their product's quality and durability. A standard warranty should cover at least 12-18 months and clearly define what is included. At AKS, we provide a comprehensive warranty and work with clients to develop long-term service agreements (LSAs) for preventative maintenance. These agreements ensure that the furnace is regularly inspected by our certified technicians, who can identify potential issues before they become critical failures, further enhancing the equipment's reliability and lifespan.
Consider the case of a Bogie Hearth Furnace we supplied to a heavy components manufacturer. The furnace's main circulation fan is a critical component for temperature uniformity. As part of their recommended spares package, they purchased a spare fan motor. Three years into operation, the original motor failed on a Friday afternoon. Because they had the spare part on-site, and their team had been trained on the replacement procedure, they were able to swap it out and be back in production within a few hours, averting a weekend shutdown. This demonstrates the power of a proactive approach to maintenance, guided by a supplier who is invested in your long-term operational success.
After-sales support prevents costly downtimeTrue
Robust customer support systems like 24/7 technical assistance and remote diagnostics help quickly resolve issues, minimizing production losses.
Training is optional for furnace operatorsFalse
Comprehensive operator training is essential as furnace performance and longevity directly depend on proper operation and maintenance procedures.
What role do customization options play in meeting your specific annealing process needs?
Are you trying to fit your unique production process into a standard, off-the-shelf furnace? This often leads to compromises in efficiency, quality, and workflow. Forcing a square peg into a round hole can create persistent bottlenecks and prevent you from achieving optimal results in your facility.
Customization is vital because it allows a furnace to be tailored to your specific material dimensions, production throughput, facility layout, and unique process requirements. This ensures seamless integration, maximizes efficiency, and guarantees the furnace is a perfect fit for your operational needs, not a compromise.
No two manufacturing facilities are exactly alike. Space constraints, loading and unloading methods, material flow, and specific process parameters all vary. A supplier that offers deep customization capabilities can engineer a solution that fits your world perfectly. This goes beyond changing the paint color; it involves fundamental design modifications to dimensions, heating systems, atmosphere controls8, and material handling to create a truly bespoke piece of industrial equipment that enhances your entire production line.
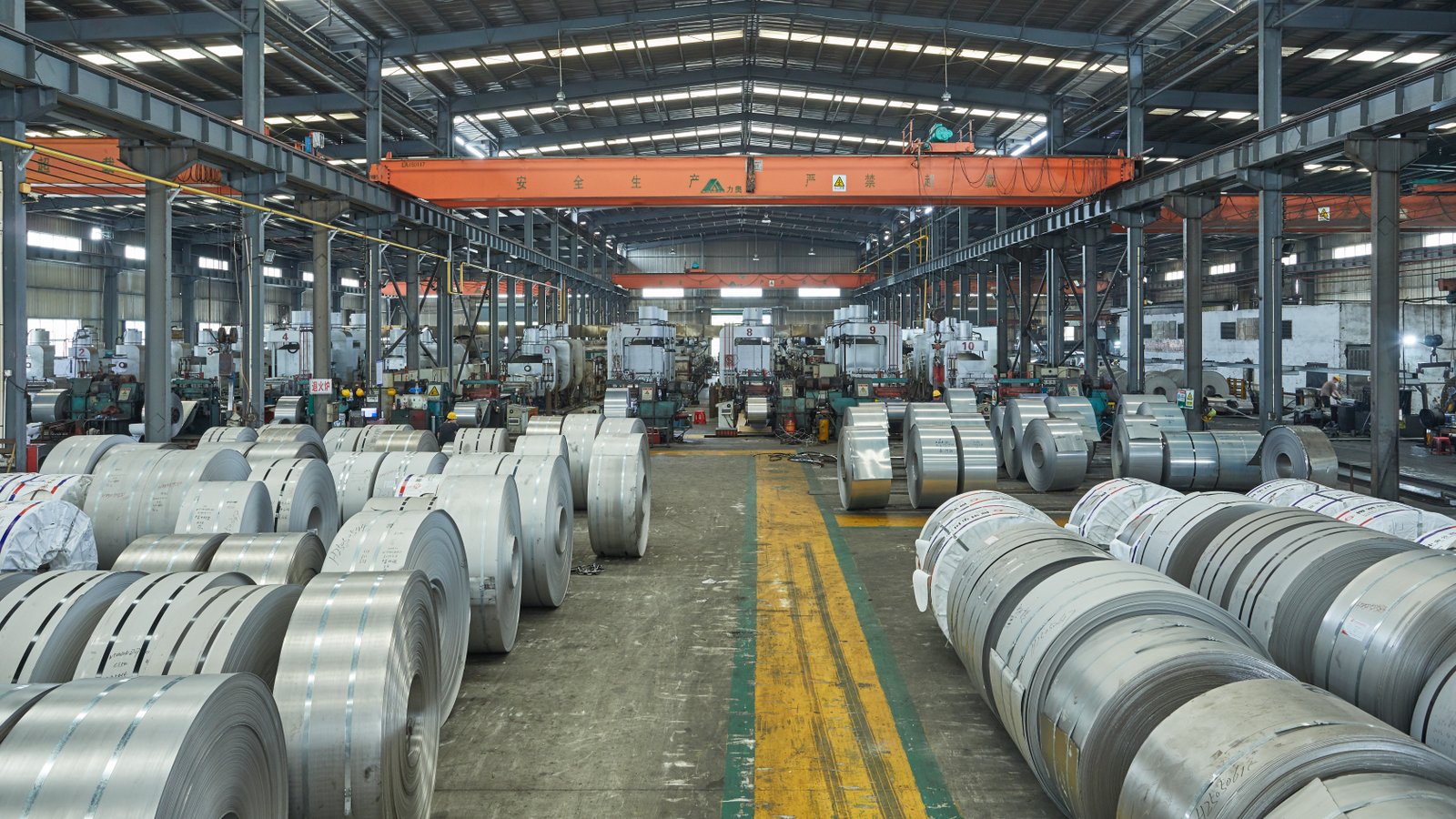
At AKS, we pride ourselves on our ability to engineer custom solutions. We see ourselves as partners in problem-solving, not just furnace builders. I recall a project with a manufacturer of high-end aluminum foil. They needed a furnace to anneal very wide coils, but their factory had a low ceiling height, which ruled out standard vertical-style furnaces. Furthermore, their workflow was optimized for crane loading. Instead of telling them it was impossible, our engineering team designed a custom-wide Bogie Hearth Annealing Furnace with a very low profile. We modified the door mechanism to a cantilevered lift-and-swing design to accommodate the overhead crane access. This custom solution integrated perfectly into their existing facility and workflow, a feat that would have been impossible with a standard furnace. It’s this flexibility and willingness to adapt the equipment to the client's reality that defines the true value of customization.
Tailoring Furnace Dimensions and Layout
One of the most fundamental aspects of customization is adapting the furnace's physical dimensions and layout to your facility. Standard furnace sizes might not fit within your available floor space, or their loading height may not align with your existing material handling equipment like forklifts, coil cars, or overhead cranes. An experienced supplier can re-engineer the furnace's structural frame, chamber dimensions, and overall footprint to overcome these limitations. This can involve creating a wider and shorter chamber to fit under a low ceiling, or designing a pass-through configuration9 to match an in-line production flow.
We worked with a stainless steel wire producer who needed to install a new continuous annealing line in a very narrow bay in their plant. A standard straight-line furnace was simply too long. Our solution was to design a U-shaped furnace layout. The furnace effectively doubled back on itself, with the pay-off and take-up equipment located adjacent to each other. This custom layout cut the required linear space in half and allowed the client to install a high-capacity line without having to undertake costly building modifications.
Furthermore, customization extends to ergonomic and safety features. We can modify the placement of control panels, emergency stops, and maintenance access doors to better suit your operators' workflow and your company's specific safety protocols. This level of physical adaptation ensures that the furnace is not an obstacle in your plant but a natural and efficient part of your production ecosystem.
Customizing Heating and Cooling Systems
Beyond physical size, the heart of furnace customization lies in tailoring the thermal processing systems to your specific metallurgical requirements. A standard heating package may not provide the precise temperature uniformity or ramp rates needed for sensitive alloys. A flexible supplier can offer a range of heating options, from traditional radiant tubes10 to advanced open-flame systems with regenerative burners, and can customize the number and placement of control zones within the furnace. For particularly demanding applications, we can design systems with high-velocity convection fans to improve heat transfer and uniformity.
The cooling section is equally critical and often requires significant customization. The rate of cooling after annealing determines the final microstructure and mechanical properties of the material. For some processes, a slow, controlled cool is needed, while for others, like annealing austenitic stainless steels11, a rapid quench is essential to prevent sensitization. We can design cooling systems ranging from simple air-cooled tunnels to sophisticated jet coolers that use high-pressure, recirculated protective atmosphere to extract heat rapidly and evenly.
For a client processing thin gauge carbon steel strips for razor blades, achieving a very specific, fine-grained microstructure was essential for sharpness and durability. This required a highly controlled, multi-stage cooling profile. We engineered a custom cooling tunnel with four distinct zones, each with its own independent temperature control and variable-speed fans. This allowed them to program a precise cooling curve that delivered the exact metallurgical properties they needed, a level of control that was impossible with any standard furnace on the market.
Integrating Automation and Material Handling
To maximize efficiency and reduce labor costs, a modern annealing furnace should be seamlessly integrated with your plant's automation and material handling systems. This is where customization plays a pivotal role in creating a truly "hands-off" operation. A supplier with strong automation expertise can design and build integrated systems for loading, transferring, and unloading your products. This could include automated coil cars for a Bell-Type Furnace, robotic loading for a Bogie Hearth Furnace, or synchronized conveyors for a Mesh Belt Furnace.
The control system itself can be customized to interface with your central plant management software (e.g., SCADA or MES). This allows for centralized recipe management, data logging for quality assurance, and real-time monitoring of furnace status from a central control room. We can program the furnace's PLC to communicate with upstream and downstream equipment, ensuring the entire production line operates as a single, cohesive unit.
A prime example is a project we completed for a large automotive parts manufacturer. They wanted to fully automate their heat treatment cell. We designed a solution around our Bogie Hearth Furnace that included an automated transfer car to move parts from the pre-heating station to the furnace and then to the cooling station. The furnace doors were automated, and the entire sequence was controlled by a central PLC that received commands from their production scheduling system. This custom-integrated solution reduced manual handling by 90%, significantly improved process consistency, and enhanced operator safety. This level of automation is only achievable when the furnace supplier has the engineering capability to look beyond the furnace itself and design a complete, integrated system.
Customization improves furnace efficiencyTrue
Tailoring furnace dimensions and systems to specific needs eliminates bottlenecks and optimizes workflow.
Standard furnaces fit all facilitiesFalse
Every facility has unique space constraints and material handling requirements that standard furnaces can't accommodate.
Conclusion
Ultimately, purchasing an annealing furnace requires a thorough investigation into your own process needs, the supplier's experience, the unit's long-term operating costs, available after-sales support, and customization flexibility. Asking these critical questions ensures you acquire a high-performing asset, not just a piece of equipment.
-
Understand how a Bright Annealing Furnace benefits specific processes ↩
-
Discover annealing benefits for 304 stainless steel ↩
-
Learn how muffle chambers help achieve uniform heat distribution in furnaces ↩
-
Discover how proven designs enhance furnace reliability and energy efficiency ↩
-
Explore the role of metallurgy in optimizing furnace design and process control ↩
-
Discover how energy consumption drives long-term costs and profitability ↩
-
Understand how remote support can resolve technical issues swiftly to avoid production halts. ↩
-
Discover how atmosphere controls improve annealing efficiency and material quality ↩
-
Learn the advantages of pass-through designs for streamlined production ↩
-
Understand the working and benefits of radiant tubes in thermal processing ↩
-
Gain insight into the metallurgical benefits of rapid quenching ↩