How Do CAPEX and OPEX Differ in the Annealing Process for New Furnace Lines?
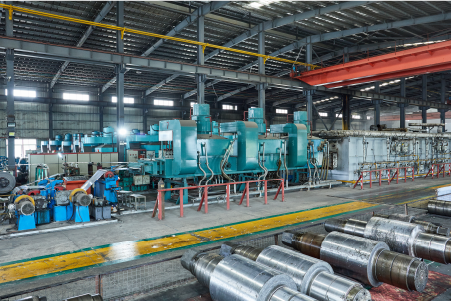
Are you finding it challenging to distinguish between the initial investment and the long-term running costs when planning for new annealing furnace lines? This confusion can lead to unexpected financial burdens. Understanding the clear differences between CAPEX and OPEX1 is fundamental for sound financial planning and operational success.
CAPEX (Capital Expenditure) represents the significant, one-time upfront investment made to acquire, deliver, and install new annealing furnace lines. In contrast, OPEX (Operational Expenditure) covers all the recurring daily, monthly, and annual costs essential for running and maintaining these furnaces effectively throughout their operational life.
Navigating the financial landscape of industrial heat treatment, especially when investing in new furnace lines, can feel like a complex maze. It’s not merely about the purchase price; it’s about the total cost of ownership and the financial health of your operations over years. By clearly dissecting Capital Expenditures (CAPEX) and Operational Expenditures (OPEX), we can illuminate the path to smarter investments and more profitable annealing processes. Let's explore these crucial financial components in detail.
The decision to invest in a new annealing furnace line is a pivotal one, carrying weight far beyond the initial invoice. It's a strategic commitment where the upfront capital outlay (CAPEX) must be critically assessed against the long-term operational viability and costs2 (OPEX). I’ve seen firsthand how an attractive, low CAPEX furnace can quickly become a financial drain if its energy consumption is high or it demands frequent, costly maintenance – a scenario particularly challenging for businesses in competitive sectors like stainless steel strip production. Conversely, a higher initial CAPEX for a technologically advanced furnace, like our AKS bright annealing lines equipped with energy-saving systems and waste heat recovery, often translates into significantly lower OPEX, a faster return on investment, and enhanced sustainability. It’s about understanding this intricate balance to ensure your heat treatment facility thrives.
What are the primary CAPEX considerations when investing in new annealing furnace lines?
Feeling overwhelmed by the sheer number of cost factors when budgeting for a new annealing furnace? Overlooking critical capital expenditure components can lead to significant budget overruns and project delays. A clear understanding of all primary CAPEX elements is crucial for a smooth investment and successful commissioning.
Key CAPEX considerations for new annealing furnace lines encompass the furnace purchase price, comprehensive installation and commissioning fees, essential site preparation and infrastructure upgrades, required auxiliary equipment like atmosphere generators or cooling systems, and initial operator and maintenance training programs.
When I sit down with clients at AKS Furnace to discuss a new annealing line project – perhaps a continuous bright annealing furnace for a stainless steel coil processor in Southeast Asia – the conversation inevitably begins with Capital Expenditure. It’s the initial financial mountain we need to map out precisely. The furnace's sticker price is just the peak; the mountain range includes shipping, intricate rigging for installation, and potentially significant site modifications like foundation strengthening or upgrades to electrical and gas supply infrastructures. Then there's the suite of auxiliary systems. For our specialized bright annealing furnaces, this often means investing in high-purity hydrogen or nitrogen atmosphere generation plants, or advanced strip cooling systems designed to achieve that perfect, mirror-like finish crucial for high-value applications. Automation and sophisticated control systems, while adding to the upfront CAPEX, are investments we strongly advocate for, as they yield substantial OPEX savings through enhanced efficiency, reduced manual intervention, and improved product consistency. Finally, and critically, initial staff training is a CAPEX component that ensures your team can operate and maintain the new asset effectively from day one, maximizing its productivity and lifespan. Addressing these multifaceted costs comprehensively upfront is the cornerstone of a strategically sound investment.
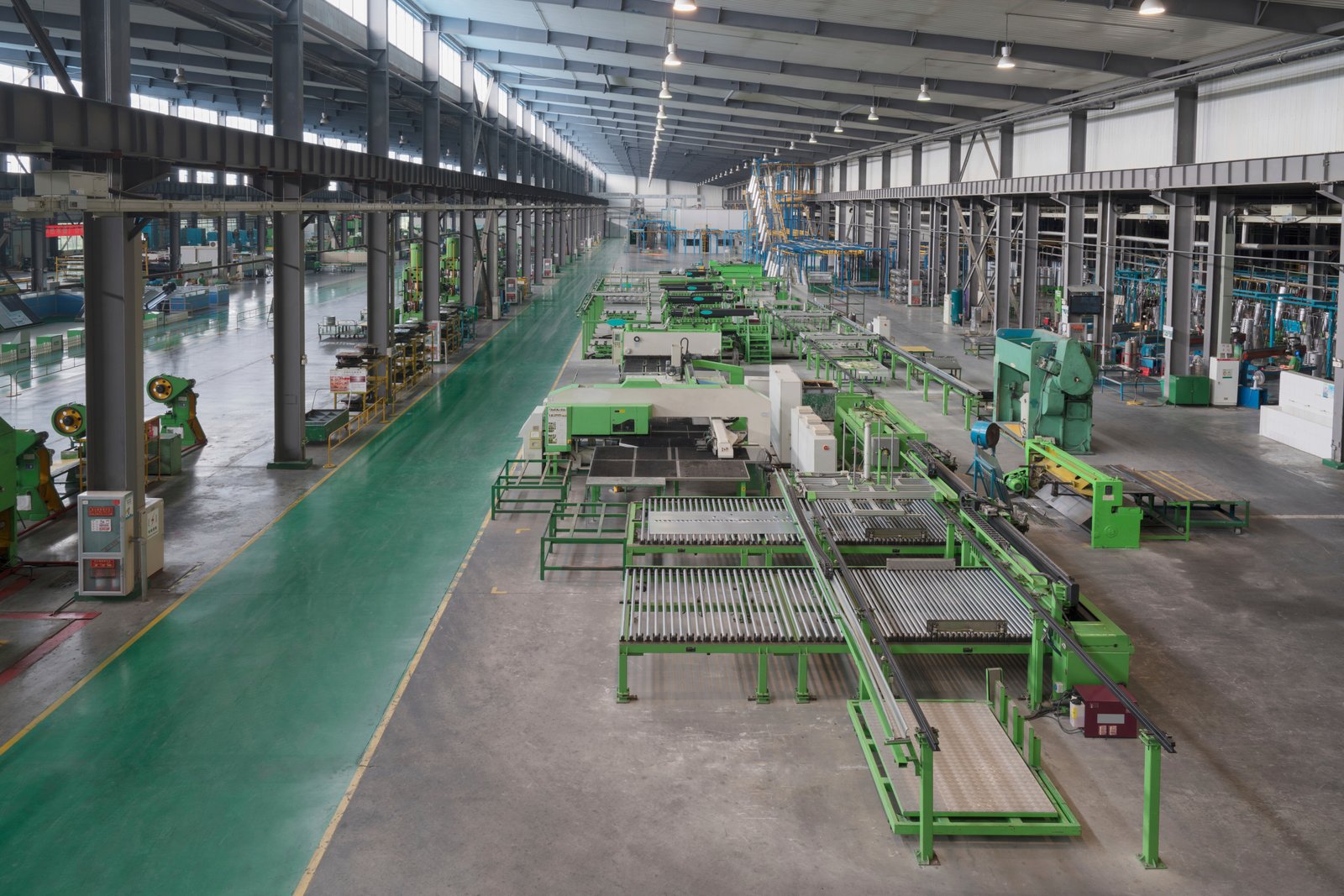
Investing in a new annealing furnace line is a significant undertaking, and understanding the full spectrum of Capital Expenditures (CAPEX) is paramount to avoid unforeseen costs and ensure the project's financial viability. It's far more than just the cost of the furnace unit itself; it's a holistic investment covering everything from ground preparation to operator proficiency. At AKS Furnace, we guide our clients through this complex landscape, ensuring every critical CAPEX component is considered. This proactive approach helps in accurate budgeting and lays the foundation for a successful, long-term operational asset. Let's break down these primary considerations further.
The Core Equipment Cost: Beyond the Sticker Price
The most apparent CAPEX component is, of course, the annealing furnace itself. For specialized equipment like a continuous bright annealing line designed for stainless steel strips, the price can vary significantly based on its processing capacity (tons per hour), the maximum operating temperature, the choice of construction materials (for instance, the muffle material, which could be a high-performance alloy like Inconel 601 or 310S stainless steel, directly impacting longevity and resistance to harsh atmospheres), and the sophistication of the automation and control systems. I recently worked with a client in India manufacturing stainless steel tubes for the automotive sector. Their primary concern was achieving a consistent, bright finish. While evaluating options, the base price of the furnace was a starting point, but we delved deeper into the cost implications of different muffle alloys and heating element types.
Opting for a furnace with a more robust and durable muffle, although carrying a higher initial cost, can significantly reduce the frequency of muffle replacements over the furnace's lifespan. Considering that a muffle replacement can cost anywhere from 15% to 30% of the original furnace's value and lead to significant downtime, the long-term CAPEX savings become evident. Industry data3 suggests that high-quality muffles can last 5-10 years depending on usage, compared to 2-4 years for lower-grade alternatives under similar aggressive conditions.
Furthermore, the choice between electric heating elements and gas-fired radiant tube heating systems also impacts the initial CAPEX. Electric systems might sometimes present a lower furnace unit cost, but this can be offset by the need for substantial upgrades to the factory's electrical infrastructure, including new transformers or switchgear, adding to the overall CAPEX. Gas-fired systems, while potentially having a slightly higher furnace cost, might leverage existing gas pipelines, though they require sophisticated combustion control for efficiency and safety. We help clients conduct a detailed analysis based on their existing infrastructure, local utility costs, and specific processing requirements to make the most economically sound decision.
Installation, Commissioning, and Site Preparation: The Hidden Giants
The costs associated with installation and commissioning are often underestimated but can represent a substantial portion of the total CAPEX, typically ranging from 10% to 20% of the furnace's purchase price. This category includes the mechanical assembly of the furnace sections, meticulous electrical wiring for power and control systems, plumbing for process gases (like hydrogen and nitrogen for bright annealing) and cooling water, and the critical phase of commissioning. Commissioning involves not just starting up the furnace but also fine-tuning all operational parameters – temperature profiles, atmosphere flow rates, conveyor speeds – to achieve the specified metallurgical properties and surface finish on the client's product. I recall a project for a copper alloy strip manufacturer where the installation site was within an existing, tightly packed facility. The complex rigging and material handling required added nearly 8% to the budgeted installation costs, highlighting the need for thorough site assessment.
Site preparation is another critical CAPEX element that precedes the furnace's arrival. This can involve significant civil engineering works, such as constructing or reinforcing concrete foundations to support the furnace's considerable weight and any associated charge cars or material handling systems. For a large bogie hearth annealing furnace we recently supplied to a manufacturer of heavy forgings, the foundation design and construction was a mini-project in itself, requiring detailed soil analysis and structural engineering to ensure long-term stability. Other site preparation costs can include trenching for utilities, ensuring adequate ventilation and exhaust systems, and modifying building structures to accommodate the furnace's dimensions.
Regulatory compliance and the installation of safety systems also fall under this CAPEX umbrella. These are non-negotiable and vary significantly by region and country. For instance, furnaces exported to European markets must carry CE marking and comply with stringent EN safety standards (e.g., EN 746-2 for combustion and fuel handling systems in industrial thermoprocessing equipment), which can influence the furnace design, control systems, and thus the CAPEX. Safety installations might include gas detection systems, emergency shutdown mechanisms, fire suppression systems, and safety interlocks, all contributing to the initial investment but crucial for safe operation.
CAPEX Component Category | Estimated % of Total Project CAPEX (Bright Annealing Line Example) | Key Considerations & Potential Variables |
---|---|---|
Furnace Core Unit & Auxiliaries | 60-75% | Capacity, materials (muffle, insulation), automation, atmosphere & cooling systems |
Installation & Commissioning | 10-20% | Site complexity, labor rates, duration, level of performance testing |
Site Preparation & Civil Works | 5-15% | Foundation, utility upgrades (power, gas, water), building modifications |
Shipping, Logistics & Local Taxes/Duties | 5-10% | Distance, mode of transport, import regulations, insurance |
Initial Training & Spares Package | 2-5% | Number of personnel, training duration, criticality of initial spares |
Auxiliary Systems and Initial Spares: Supporting the Operation
For many annealing processes, particularly those requiring controlled atmospheres like bright annealing, the auxiliary systems form a significant part of the CAPEX. This prominently includes atmosphere generation plants. For example, to produce the hydrogen-nitrogen mix (forming gas) commonly used for bright annealing stainless steel, clients might invest in an ammonia cracker or a dedicated hydrogen generator paired with a nitrogen supply (either from a PSA nitrogen generator or liquid nitrogen storage). The choice depends on the required gas purity, volume, and the relative costs of ammonia, electricity, and nitrogen in their region. A client producing high-specification stainless steel components for the electronics industry recently invested in a high-purity, on-site nitrogen generation system, which, while a notable CAPEX item, provided them with greater control over gas quality and long-term cost savings compared to purchasing bottled gas.
Advanced cooling systems are also a critical CAPEX component, especially for continuous annealing lines where achieving specific cooling rates is vital for metallurgical properties and, in the case of bright annealing, for maintaining the surface finish and ensuring strip flatness. Our AKS bright annealing furnaces often incorporate sophisticated cooling sections, which can include rapid jet cooling with recirculated protective atmosphere or controlled slow cooling zones. The design and materials of these cooling muffles, the power of the circulation fans, and the precision of the control systems all contribute to the CAPEX but are essential for producing high-quality annealed products that meet demanding specifications, thereby reducing downstream processing or rejection rates.
Finally, a prudent CAPEX plan includes an initial inventory of critical spare parts. While this might seem like an OPEX item, having essential spares on hand from day one is part of the initial project investment to ensure operational readiness and minimize potential early-life downtime. This typically includes items such as a set of heating elements, thermocouples, critical seals, a spare conveyor belt section (for mesh belt furnaces), or key components for the atmosphere control system. We always work with our clients to develop a recommended initial spares list tailored to their specific furnace type and anticipated operational intensity. For a high-throughput continuous line, the criticality of having spares like drive motors or control system modules is much higher than for a small, intermittently used batch furnace. This initial stock acts as an insurance policy against immediate disruptions.
CAPEX includes furnace installationTrue
CAPEX covers all one-time costs including furnace purchase, installation, and commissioning fees.
OPEX includes furnace purchaseFalse
Furnace purchase is a capital expenditure (CAPEX), not an operational cost (OPEX).
How does OPEX impact the overall cost-efficiency of annealing furnaces?
Are you solely focused on the initial purchase price when evaluating an annealing furnace? Ignoring the ongoing operational expenditures (OPEX) can severely undermine your furnace's long-term cost-efficiency. High OPEX can transform a seemingly economical furnace into a costly liability over its service life.
OPEX profoundly impacts the overall cost-efficiency of annealing furnaces by encompassing all recurring expenses such as energy (electricity/gas), protective atmosphere gases, labor for operation and maintenance, spare parts, and other consumables, directly influencing the final per-unit production cost.
Once your new annealing furnace is commissioned and running – that initial CAPEX hurdle cleared – the spotlight shifts squarely onto Operational Expenditure (OPEX). This is the true test of your investment's long-term economic viability. I often emphasize to my clients, particularly those in high-volume production environments like carbon steel strip or copper alloy processing, that OPEX isn't a one-time cost but a continuous stream of expenses that dictates the actual cost of every ton of material annealed. It's the sum total of energy bills, the cost of protective gases flowing day in and day out, the wages of the skilled personnel operating and maintaining the equipment, the regular replacement of wear-and-tear components, and even the lubricants that keep things moving smoothly. Imagine two furnaces with similar CAPEX; one might consume 15% less energy and 10% less protective gas due to superior design and insulation. Over a year, these efficiencies translate into substantial OPEX savings, directly boosting the profit margin on every product that passes through it. For a company annealing hundreds or thousands of tons monthly, this difference can amount to tens or even hundreds of thousands of dollars annually. Therefore, diligently tracking, managing, and optimizing these ongoing costs is not just good practice; it's fundamental to maintaining competitiveness and ensuring the sustained profitability of your heat treatment operations.
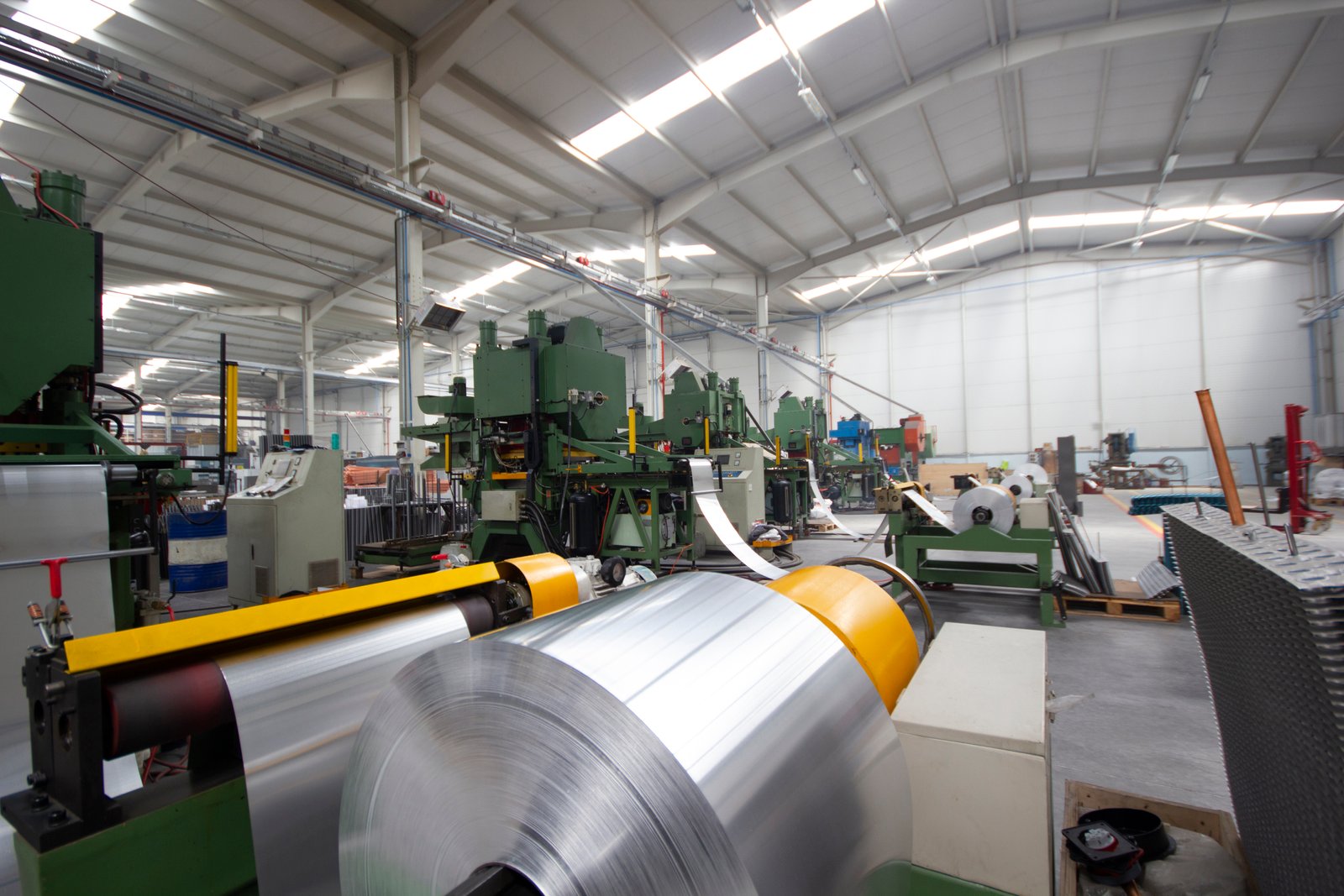
Operational Expenditure (OPEX) is the lifeblood, or potentially the slow drain, of an annealing furnace's economic performance over its lifespan. While CAPEX is the upfront investment, OPEX determines the day-to-day, month-to-month, and year-to-year cost of producing annealed materials. A furnace that is a marvel of low CAPEX can quickly become an economic burden if its OPEX is not carefully managed and optimized. At AKS Furnace, we design our systems with a keen eye on minimizing OPEX, knowing that this is where long-term value is truly created for our clients. From energy consumption to maintenance routines, every aspect of OPEX warrants close attention. Let's delve into the core components that constitute the OPEX4 of annealing furnaces and how they influence overall cost-efficiency.
Energy Consumption: The Dominant OPEX Factor
Without a doubt, energy consumption stands as the most significant component of OPEX for the vast majority of annealing furnace operations. Whether the furnace is heated electrically via resistance elements or through the combustion of natural gas, LPG, or other fuels in radiant tubes or direct-fired burners, the sheer thermal energy required to heat tons of metal to annealing temperatures (which can range from 550°C for some aluminum alloys to over 1100°C for stainless steels) and maintain these temperatures is substantial. For a continuous annealing line, like those we build for stainless steel strip, operating 24/7, energy costs can easily account for 40% to 60% of the total annual OPEX. I worked with a large-scale carbon steel processor whose monthly energy bill for their annealing department was their single largest operational cost line item before they invested in newer, more thermally efficient furnaces.
The thermal efficiency of the furnace design is paramount in controlling this major OPEX component. This encompasses several factors: the quality and thickness of the insulation materials used in the furnace walls, roof, and hearth to minimize heat losses to the ambient environment; the design and placement of heating elements or burners to ensure uniform and efficient heat transfer to the workload; and the precision of the temperature control system to prevent overheating and unnecessary energy expenditure. Our AKS furnaces, for instance, utilize multi-layer composite insulation and sophisticated PID control algorithms. For our gas-fired bright annealing furnaces, we incorporate an energy-saving system with precision control of the gas-to-air ratio, ensuring complete combustion and maximizing thermal output from the fuel consumed. Such features can lead to documented energy savings of 10-20% compared to older or less optimized designs. According to studies by organizations like the U.S. Department of Energy, optimizing furnace insulation and sealing alone can yield energy savings in the range of 5-15%.
Furthermore, the implementation of waste heat recovery systems offers a powerful avenue for reducing energy OPEX. In many annealing furnaces, a significant portion of the input energy – sometimes as much as 30-50% – is lost through hot exhaust gases. Our advanced annealing lines, particularly continuous strip annealers, often feature waste heat recovery units. These systems capture the thermal energy from the flue gases to preheat combustion air (in gas-fired furnaces) or even to preheat the incoming metal strip before it enters the main heating chamber. This direct reutilization of waste heat significantly reduces the primary energy required to reach annealing temperatures, directly cutting fuel or electricity bills. For a typical medium-sized continuous annealing line, effective waste heat recovery can reduce overall energy consumption by an additional 10-15%, making a substantial impact on the bottom line.
Consumables and Maintenance: The Ongoing Necessities
After energy, the cost of consumables, particularly protective atmosphere gases, forms the next major OPEX category, especially for processes like bright annealing or annealing of reactive metals. For bright annealing of stainless steel, a reducing atmosphere, typically a mix of hydrogen and nitrogen (forming gas) or pure hydrogen, is essential to prevent oxidation and achieve a lustrous surface finish. The continuous consumption of these gases, their purchase price (which varies by purity and supply method – e.g., bulk liquid, on-site generation, or cylinders), and the efficiency of their use are critical OPEX factors. A furnace with poor seals, inefficient muffle design, or improperly managed flow rates can lead to excessive gas consumption. I recall a client operating an older bell-type annealing furnace who discovered, after an audit, that they were losing nearly 30% of their protective gas due to deteriorated door seals and cracks in the retort – a hidden but significant OPEX drain. Our modern AKS furnaces are designed with gas-tight integrity and precise atmosphere control systems to minimize consumption. For instance, maintaining a slight positive pressure with optimized flow rates ensures atmosphere purity without excessive wastage.
Maintenance, encompassing both preventive (scheduled) and corrective (breakdown) activities, along with the associated spare parts, is another unavoidable OPEX component. This includes the regular inspection and periodic replacement of wear-and-tear items such as thermocouples (for temperature measurement), heating elements (which degrade over time), conveyor belts or rollers (in continuous furnaces), door seals, refractory linings (which can spall or crack), and components of the drive or atmosphere systems. While a comprehensive preventive maintenance program itself incurs costs (labor, lubricants, some minor parts), it is almost always more cost-effective than dealing with unplanned breakdowns. Unplanned downtime not only incurs repair costs but also leads to lost production, missed delivery schedules, and potentially compromised product quality. A client operating one of our mesh belt furnaces for sintering small metal parts found that adhering to a strict preventive maintenance schedule for belt tensioning and inspection drastically reduced instances of costly belt failures and associated production halts. Industry data suggests that effective PM can reduce overall maintenance costs by 12-18% and cut unplanned downtime by 30-40%.
Other consumables contributing to OPEX include lubricants for motors, bearings, and drive chains; cleaning supplies for furnace internals (where applicable); and potentially water treatment chemicals if the furnace employs a water-based cooling system that is prone to scaling or corrosion. While these individual costs might seem minor, they accumulate over the year and contribute to the overall operational burden. The design of the furnace can influence some of these; for example, using sealed-for-life bearings can reduce lubrication needs, or designing cooling systems with materials less prone to corrosion can lower water treatment costs.
OPEX Component | Typical % of Total Annual OPEX (Continuous Annealing Line) | Key Influencing Factors & Optimization Levers |
---|---|---|
Energy (Electricity/Gas) | 40-60% | Furnace thermal efficiency, insulation, waste heat recovery, utility rates, operational scheduling |
Protective Atmosphere Gases | 15-25% | Gas type & cost, purity, flow rate, furnace sealing integrity, atmosphere control precision |
Maintenance & Spare Parts | 10-15% | Furnace design robustness, component quality, PM program effectiveness, operating hours |
Labor (Operational & Maint.) | 10-20% | Level of automation, operator skill, maintenance team efficiency, local labor rates |
Other Consumables & Utilities | 2-5% | Lubricants, cooling water (if applicable) & treatment, miscellaneous supplies |
Labor and Downtime: The Human and Hidden Costs
Labor costs associated with the operation, supervision, and routine maintenance of annealing furnaces are a direct OPEX component. The extent of this cost is heavily influenced by the level of automation integrated into the furnace line. Modern, PLC-controlled annealing furnaces with sophisticated SCADA (Supervisory Control and Data Acquisition) systems can often operate with minimal direct supervision5, perhaps one operator overseeing multiple lines or an entire heat treatment cell. This contrasts sharply with older, more manual systems that might require dedicated operators for loading, unloading, cycle monitoring, and adjustments. When we designed a fully automated bogie hearth furnace line for a large castings manufacturer, they were able to reduce their direct operational labor per furnace by one person per shift, reallocating that skilled labor to other value-adding tasks in their facility. However, it's also important to note that highly automated systems may require more specialized and thus potentially higher-cost maintenance technicians.
The cost of downtime, while often considered an indirect or hidden cost, has a profound impact on OPEX and overall profitability. Every hour an annealing furnace is non-operational due to an unplanned breakdown represents lost production capacity, potential delays in fulfilling customer orders (which can incur penalties or damage reputation), and inefficient use of labor (operators may be idle or need to be reassigned). Furthermore, emergency repairs are typically more expensive than planned maintenance due to urgency, potential overtime pay for technicians, and expedited shipping costs for spare parts. The robustness of the furnace design, the quality of its components, and, crucially, the effectiveness of the preventive and predictive maintenance programs are key to minimizing unplanned downtime. Industry studies have shown that unplanned downtime in manufacturing can cost anywhere from a few thousand to hundreds of thousands of dollars per hour, depending on the scale and nature of the operation. Reducing this is a critical OPEX management goal.
Finally, ongoing training and skill development for both operational and maintenance personnel, while an investment, is crucial for long-term OPEX control. Well-trained operators can run the furnace more efficiently, adhere to correct procedures, and identify early warning signs of potential problems, preventing minor issues from escalating into major breakdowns. Similarly, skilled maintenance staff can perform repairs more quickly and effectively, and implement preventive measures more diligently. We at AKS Furnace always include comprehensive training as part of our furnace delivery and commissioning package, as we firmly believe that a knowledgeable and proficient team is essential for maximizing the furnace's performance, lifespan, and overall cost-efficiency.
Energy is the largest OPEX componentTrue
Energy consumption typically accounts for 40-60% of total annual OPEX for continuous annealing lines, making it the dominant cost factor.
CAPEX is more important than OPEXFalse
While CAPEX is the initial investment, OPEX determines long-term cost-efficiency and can make a seemingly economical furnace costly over time.
How can firms optimize CAPEX and OPEX for maximum return on investment in annealing systems?
Are you struggling to balance the initial investment in an annealing furnace with its long-term running costs? Making suboptimal trade-offs can severely dent your return on investment. Achieving maximum ROI requires a strategic approach to optimizing both CAPEX and OPEX effectively.
Firms optimize CAPEX and OPEX for annealing systems by conducting thorough lifecycle cost analyses, investing in energy-efficient and durable technologies, right-sizing equipment to actual needs, implementing robust predictive and preventive maintenance programs, and leveraging automation for process consistency and labor efficiency.
Securing the best possible return on investment (ROI) from your annealing system isn't simply about hunting for the lowest purchase price or indiscriminately cutting every operational cost. True optimization lies in achieving a strategic equilibrium between the initial capital expenditure (CAPEX) and the cumulative operational expenditures (OPEX) over the furnace's entire lifecycle. I've frequently observed companies becoming fixated on minimizing CAPEX, only to find themselves shackled by exorbitant energy bills, frequent breakdowns, and high maintenance costs – a classic example of short-term gain leading to long-term pain. Conversely, over-investing in an unnecessarily complex or oversized furnace inflates CAPEX without proportional OPEX benefits, thereby extending the payback period and reducing overall ROI. The path to maximum ROI is paved with a holistic, long-term vision. At AKS Furnace, we always encourage our clients to look beyond the immediate price tag. For instance, a marginally higher CAPEX for one of our bright annealing furnaces equipped with an advanced waste heat recovery system and superior insulation might seem like a larger upfront commitment. However, the resulting annual energy savings, which can be substantial, accumulate rapidly, leading to a significantly stronger and faster ROI over the typical 15 to 25-year operational life of the furnace. It's about making astute investments in quality, efficiency, and reliability that consistently yield dividends in reduced operational burdens and enhanced productivity.
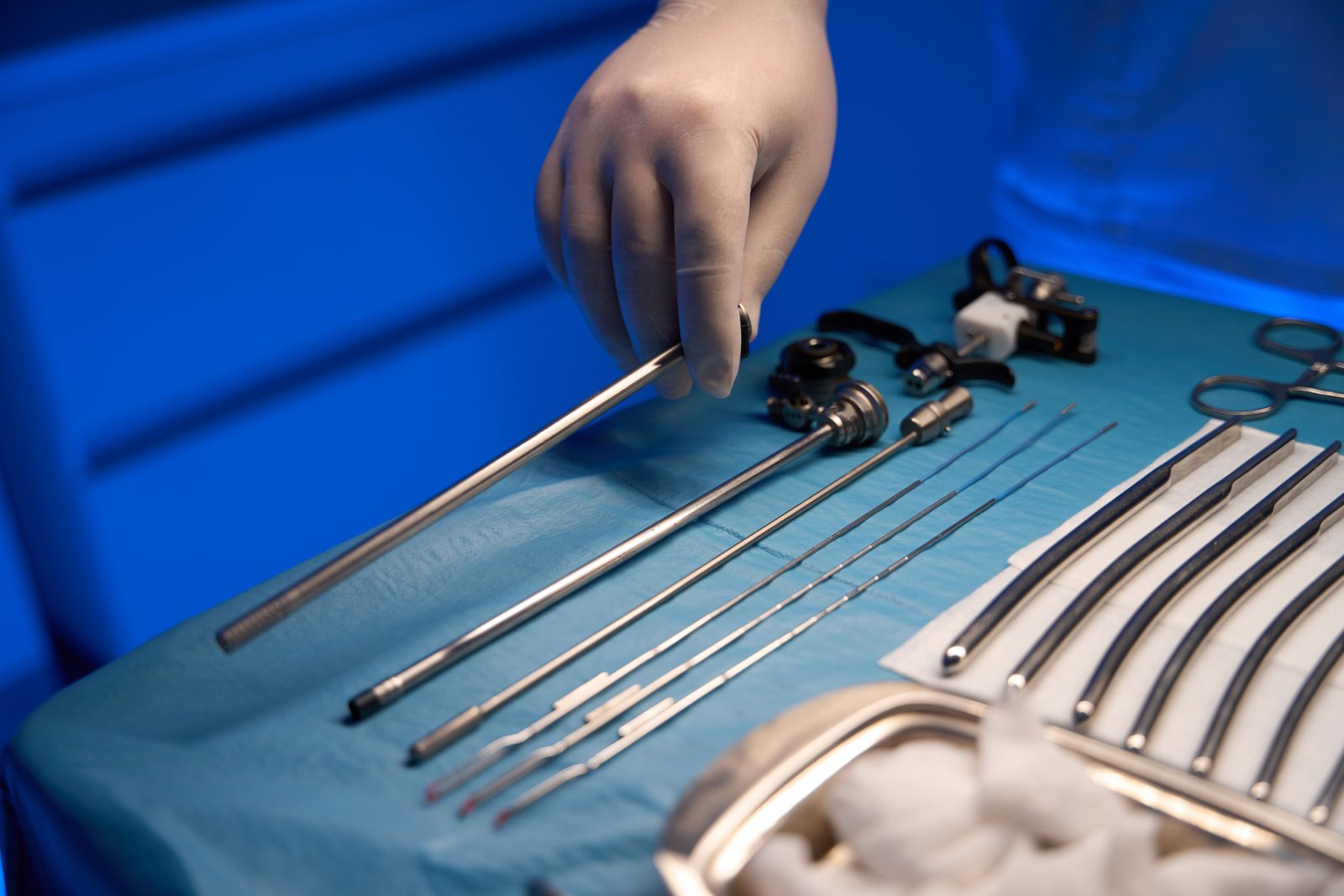
Optimizing both Capital Expenditure (CAPEX) and Operational Expenditure (OPEX) is the cornerstone of maximizing the Return on Investment (ROI) for any annealing system. It’s a delicate balancing act that requires foresight, detailed analysis, and a commitment to long-term value over short-term savings. Simply minimizing one at the expense of the other often leads to suboptimal outcomes. At AKS Furnace, our philosophy is to partner with clients to develop solutions that are not only technologically advanced but also economically sound throughout their operational life. This involves a multi-faceted strategy encompassing smart initial investments, a relentless focus on operational efficiency, and proactive management of the asset. Let's explore these strategies in more detail.
Strategic CAPEX Planning: Right-Sizing and Future-Proofing
One of the most impactful strategies for optimizing CAPEX begins with meticulous planning and "right-sizing" the annealing furnace. This involves a deep analysis of current production volumes, material types, process requirements, and realistic future growth projections. Investing in a furnace that is significantly oversized for current and medium-term needs leads to unnecessarily high upfront costs, larger installation footprints, and potentially inefficient operation if consistently run below its optimal capacity (as many furnaces have an efficiency curve that peaks at a certain throughput). I recently worked with a medium-scale manufacturer of copper alloy strips. They were initially inclined towards a very large continuous annealing line based on ambitious long-term forecasts. However, after a detailed assessment of their 5-7 year business plan and market analysis, we recommended a more appropriately sized AKS bright annealing furnace. This adjustment saved them approximately 18% on their initial CAPEX and ensured the furnace would operate closer to its peak efficiency, also positively impacting their OPEX from day one.
While avoiding over-investment is key, a degree of sensible future-proofing is also a prudent CAPEX strategy. This doesn’t mean buying excess capacity you may never use, but rather selecting a furnace design and control system architecture that allows for scalability or modular upgrades. For example, opting for a PLC and HMI system that can be easily expanded to incorporate additional heating zones, enhanced data logging, or integration with plant-wide MES (Manufacturing Execution Systems) in the future can save significant costs compared to a complete system overhaul later. Similarly, designing the furnace layout to accommodate potential future additions, like automated loading/unloading systems or an in-line quality inspection module, can be a smart move. We helped an export-oriented automotive component producer design their mesh belt furnace line with a clear provision for adding a second, parallel processing line within the same footprint, minimizing future disruption and civil work costs.
Thoroughly evaluating proposals from multiple qualified furnace suppliers, looking beyond the headline price, is another critical aspect of strategic CAPEX planning. It's essential to scrutinize the technical specifications, the quality and brand of critical components (e.g., PLCs from Siemens or Allen-Bradley, high-quality insulation materials, recognized muffle alloys), the comprehensiveness of the warranty, the supplier's track record and reputation, and the availability and cost of after-sales service and spare parts. A furnace that is 10% cheaper from a lesser-known supplier might end up costing significantly more in the long run due to lower reliability, more frequent breakdowns, or poor technical support. Industry experience shows that robust after-sales support and readily available spares can dramatically reduce downtime and protect long-term revenue streams, justifying a slightly higher initial CAPEX for a reputable supplier like AKS Furnace.
Investing in OPEX-Reducing Technologies: The Long Game
This is where the adage "you have to spend money to make money" (or in this case, save money) truly applies. Intelligently investing a bit more in CAPEX for technologies that deliver substantial and ongoing OPEX reductions is often the most effective route to maximizing ROI. Energy efficiency should be at the top of this list. This means selecting furnaces that incorporate:
- Superior Insulation: Multi-layer, low thermal conductivity insulation materials to minimize heat loss through the furnace shell.
- Efficient Heating Systems: High-efficiency gas burners with precise air-fuel ratio control, or optimally designed electric heating elements that provide uniform heat distribution.
- Advanced Process Control: PID temperature controllers with auto-tuning capabilities, and atmosphere control systems that minimize gas consumption while maintaining required purity.
- Waste Heat Recovery Systems: As emphasized by AKS Furnace, systems that capture and reutilize heat from exhaust gases to preheat combustion air or incoming charge material. For a continuous annealing line, our waste heat recovery systems can reduce annual energy bills by a documented 10-20%. If a furnace consumes $200,000 in energy annually, this translates to $20,000-$40,000 in direct OPEX savings each year, leading to a rapid payback for the additional CAPEX of the recovery system.
Automation and advanced process control, while increasing initial CAPEX, are powerful tools for OPEX reduction. Fully automated loading/unloading systems, precise recipe management via PLC/SCADA, and real-time monitoring6 of critical process parameters lead to:
- Reduced labor costs by minimizing manual intervention.
- Improved product consistency and reduced scrap/rework rates, saving material and energy.
- Optimized cycle times and energy consumption by ensuring the furnace operates exactly as programmed. A client of ours, a manufacturer of high-precision stainless steel foils for the electronics industry, invested in one of our fully automated vacuum annealing furnaces. The enhanced process control led to a 4% reduction in their product rejection rate and allowed them to reassign two operators per shift to other skilled tasks. The combined savings far outweighed the incremental CAPEX for the automation package within two years.
Choosing high-quality, durable components throughout the furnace, even if they add a premium to the CAPEX, is another vital OPEX-reducing strategy. This includes selecting robust muffle materials, long-life heating elements, durable conveyor belts or rollers, and high-quality sensors and actuators. While these may cost more initially, their extended operational life, reduced failure rates, and lower maintenance requirements translate directly into lower spare parts costs, less frequent maintenance interventions, and minimized production downtime – all significant OPEX savings. A simple cost-benefit analysis often demonstrates that the total lifecycle cost of a furnace built with superior components is lower than that of a cheaper alternative that requires more frequent part replacements.
Optimization Strategy | Primary Impact on | Secondary Impact on | Example ROI Benefit & Justification |
---|---|---|---|
Right-Sizing Equipment | Optimal CAPEX | Optimal OPEX | Avoids overspending on unused capacity; ensures efficient energy utilization from appropriate loading. |
Investment in Energy Efficiency (e.g., Waste Heat Recovery, Superior Insulation) | Higher CAPEX | Significantly Lower OPEX | Rapid payback through substantial, continuous reduction in energy bills (e.g., 10-20% fuel savings). |
Advanced Automation & Process Control | Higher CAPEX | Lower OPEX | Reduced direct labor costs, minimized human error, lower scrap rates, consistent product quality. |
Selection of High-Quality, Durable Components | Slightly Higher CAPEX | Lower OPEX | Extended component lifespan, less frequent maintenance, reduced downtime, lower spare parts consumption. |
Comprehensive Lifecycle Cost Analysis (LCCA) | Informed CAPEX Decision | Optimized OPEX | Selects furnace with best overall economic value, not just lowest initial price. |
Robust Preventive/Predictive Maintenance Program | OPEX (Investment) | Lower OPEX | Minimizes costly unplanned breakdowns, extends equipment life, optimizes maintenance scheduling. |
Lifecycle Cost Analysis and Proactive Maintenance
Adopting a Total Cost of Ownership (TCO) or Lifecycle Cost Analysis (LCCA) approach is fundamental to making truly optimized investment decisions. This methodology moves beyond the initial purchase price (CAPEX) to consider all anticipated costs over the furnace's entire operational lifespan. These costs include energy consumption, protective atmosphere gases, labor (operational and maintenance), spare parts, routine maintenance, potential major overhauls, and even decommissioning costs. When we present a proposal for an AKS furnace, we often provide clients with projected TCO figures based on their specific operational parameters (e.g., hours of operation, local utility rates, material throughput). This comprehensive financial picture frequently reveals that a furnace with a moderately higher CAPEX, but engineered for superior energy efficiency and reliability (leading to lower OPEX), offers a significantly better long-term ROI and a lower overall cost per unit of annealed product.
Implementing a robust preventive and, where feasible, predictive maintenance (PdM) program is a critical OPEX optimization strategy that also protects the initial CAPEX investment by extending the furnace's useful life. Preventive maintenance involves scheduled inspections, cleaning, lubrication, calibration, and timely replacement of components known to have a finite lifespan. This proactive approach helps to prevent unexpected failures, which are almost always more costly and disruptive. Predictive maintenance takes this a step further by using sensors (e.g., vibration, temperature, current monitors) and data analytics to monitor the condition of critical components in real-time, predicting potential failures before they occur. This allows maintenance to be scheduled precisely when needed, minimizing downtime and optimizing spare parts inventory. Industry reports from sources like McKinsey indicate that PdM can reduce maintenance costs by up to 40% and unplanned downtime by up to 50%. While PdM systems have an initial CAPEX, their ROI through OPEX reduction and increased uptime is often compelling for high-value or critical annealing operations.
Finally, investing in thorough training for operational and maintenance staff is an often-underestimated element of both CAPEX and OPEX optimization. Well-trained personnel can operate the furnace closer to its optimal efficiency points, identify early warning signs of malfunctions, perform routine maintenance tasks correctly, and troubleshoot minor issues quickly, thereby minimizing energy waste, reducing wear and tear, and preventing small problems from escalating into major, costly breakdowns. Continuous learning and skill development ensure that the team can adapt to new procedures or upgraded control features, maximizing the benefits of any technological investments made in the annealing system. This human element is crucial for unlocking the full ROI potential of the physical asset.
Waste heat recovery reduces OPEXTrue
Waste heat recovery systems can reduce annual energy bills by 10-20%, significantly lowering operational costs over time.
Minimizing CAPEX always maximizes ROIFalse
Focusing solely on minimizing initial costs often leads to higher long-term operational expenses, resulting in lower overall ROI.
What are the industry benchmarks for CAPEX vs OPEX in annealing furnace operations?
Are you unsure how your annealing furnace's financial performance stacks up against industry norms? Operating significantly outside typical CAPEX-to-OPEX ratios can indicate inefficiencies. Understanding industry benchmarks provides a valuable reference for evaluating your investments and operational effectiveness.
Industry benchmarks for annealing furnaces vary by type, capacity, and region, but generally, annual OPEX can range from 15% to 40% of the initial CAPEX. Energy consistently represents the largest OPEX share, often 40-60% of total operational costs.
When you're making a substantial investment like a new annealing furnace line, or even assessing the performance of an existing one, it's natural to seek comparators. How do your capital costs measure up? Are your ongoing operational expenses reasonable, or are they quietly eroding your profitability compared to industry peers? While establishing precise, universally applicable benchmarks for CAPEX versus OPEX in annealing is challenging due to the vast diversity in furnace technologies, scales of operation, regional economic factors like energy and labor costs, and specific process requirements, we can certainly explore some general industry observations and guidelines I’ve accumulated during my tenure at AKS Furnace. Consider these benchmarks not as rigid, unyielding rules, but as insightful reference points to stimulate internal review and identify potential areas for optimization. For instance, in the realm of continuous bright annealing lines for stainless steel, a widely observed trend is that the annual operational expenditure can often fall in the range of 15% to as high as 40% of the initial capital expenditure. This variation is significantly influenced by local energy prices, the age and efficiency of the furnace, and its utilization rate. Knowing where your operations sit within this broad spectrum can be the first step towards targeted improvements or a confirmation of efficient practices.
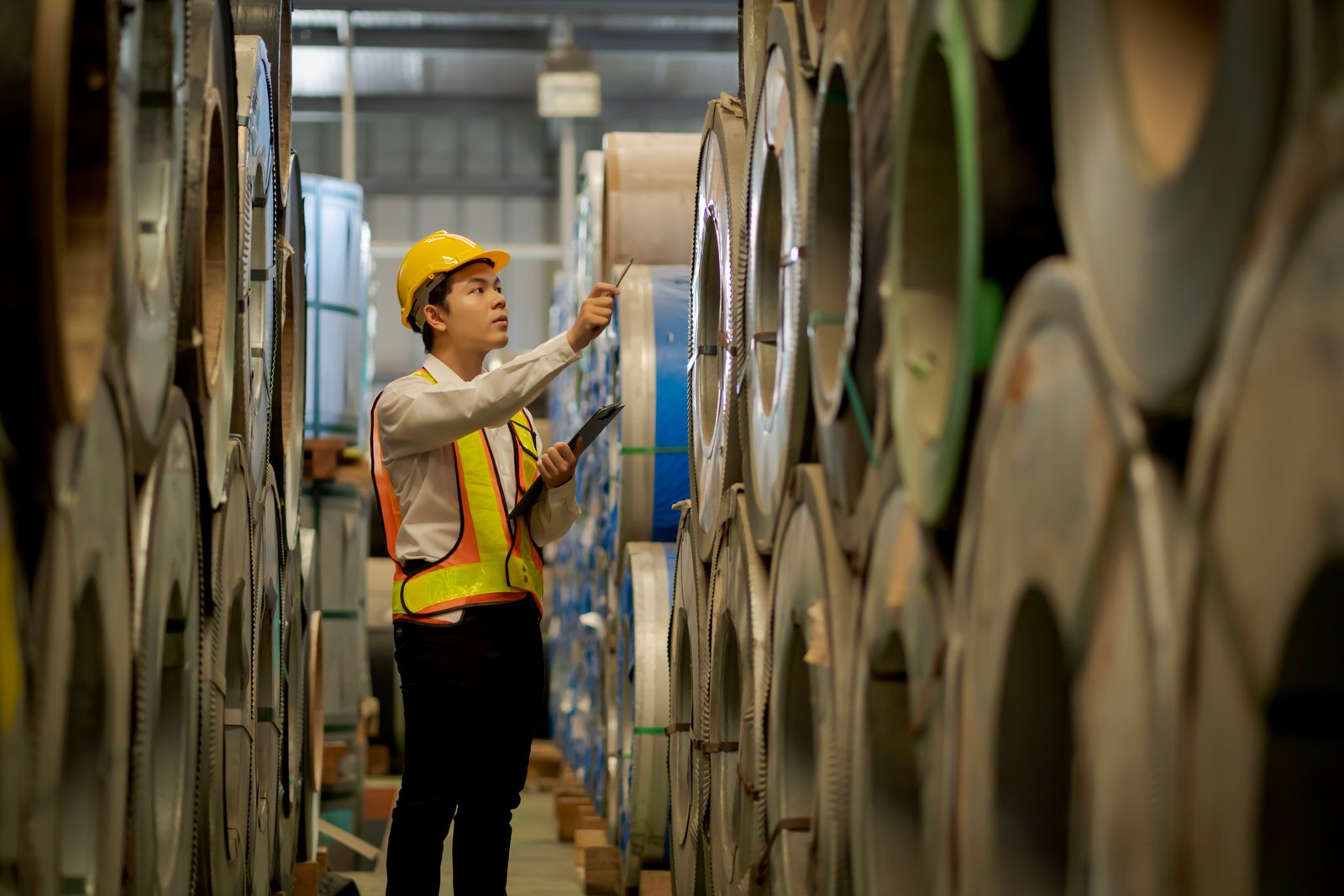
Benchmarking Capital Expenditure (CAPEX) against Operational Expenditure (OPEX) in annealing furnace operations provides a valuable, albeit general, framework for assessing investment strategies and operational efficiencies. While specific figures can fluctuate wildly based on numerous variables, understanding typical ratios and cost distributions can help businesses like yours identify outliers in their own cost structures and pinpoint opportunities for improvement. At AKS Furnace, we often discuss these indicative figures with clients to help them contextualize their investment and operational planning. It's important to remember that these are guidelines, and a deeper dive into the specifics of your operation is always necessary for true optimization.
The CAPEX/OPEX Ratio: A General Guideline
A commonly cited, though very broad, heuristic in the industrial furnace sector suggests that the annual Operational Expenditure (OPEX) for a well-utilized annealing furnace can range anywhere from 15% to 40% of its initial Capital Expenditure (CAPEX). To illustrate, if a new continuous bright annealing line required a CAPEX of $2 million, its annual OPEX might typically fall between $300,000 (15%) and $800,000 (40%). This wide range underscores the impact of variables such as:
- Regional Energy Costs: A plant in a region with low electricity or natural gas prices will naturally have a lower OPEX percentage compared to one in a high-cost energy environment.
- Furnace Technology and Age: Modern, energy-efficient furnaces with advanced automation will generally have a more favorable OPEX/CAPEX ratio than older, less efficient, or more labor-intensive designs, even if their initial CAPEX was higher.
- Utilization Rate: A furnace running 24/7 will incur higher absolute OPEX but may achieve a better OPEX percentage relative to its output and initial CAPEX if operating at peak efficiency.
- Maintenance Practices: Proactive, well-managed maintenance can keep OPEX predictable and lower over the long term compared to reactive maintenance responding to frequent breakdowns.
The type of annealing furnace also significantly influences this ratio. For instance, a highly specialized vacuum annealing furnace7, often employed for critical aerospace components or medical-grade alloys, commands a very high CAPEX due to its sophisticated vacuum pumping systems, precise temperature and atmosphere controls, and specialized chamber materials. However, its OPEX related to protective atmosphere gas consumption is virtually zero (as it operates under vacuum), though its electricity consumption for heating and maintaining vacuum remains a significant OPEX factor. Conversely, a simpler, more conventional batch-type bogie hearth annealing furnace might have a considerably lower initial CAPEX. Still, its OPEX per unit of product could be relatively higher if it's not designed for optimal energy efficiency or if it requires more manual labor for loading, unloading, and cycle management. I recall a comparative study we facilitated for a group of metal processors; those who had invested in modern continuous strip annealing lines featuring robust heat recovery systems typically saw their annual OPEX hover around 20-28% of their CAPEX. In contrast, companies operating older lines (often 15+ years old) frequently reported OPEX figures approaching or even exceeding 35-40% of their (lower) original CAPEX, clearly illustrating the lifecycle cost benefits of investing in newer, more efficient technology.
Dominance of Energy in OPEX Benchmarks
Across virtually all types of industrial annealing furnaces, energy – whether electricity for resistance heating or fuel gas (natural gas, LPG, etc.) for burner systems – consistently stands out as the single largest component of OPEX. Industry data and our own experience at AKS Furnace indicate that energy costs typically account for 40% to 60%, and sometimes even more, of the total annual operational expenditure for an annealing furnace. This makes the thermal efficiency of the furnace a paramount concern and a key benchmark. When prospective clients engage with us, one of their most pressing questions invariably revolves around the specific energy consumption figures for our furnaces – often expressed in kWh per ton of material processed, or cubic meters of gas per ton. A furnace that can demonstrate even a 5-10% improvement in energy efficiency compared to an industry average8 for a similar process offers a substantial competitive advantage through lower production costs.
For example, in the steel industry, which is a major user of annealing furnaces, energy can represent a very significant portion of the total processing cost for heat-treated products. Reports from industry associations like WorldSteel or regional bodies often highlight that energy can constitute up to 30-40% of the transformation costs for certain steel grades where heat treatment is a critical step. Therefore, when benchmarking OPEX, the energy consumption per unit of output is a far more telling metric than just the overall energy bill. Furnaces that incorporate advanced insulation, efficient combustion systems, precise temperature controls, and, crucially, effective waste heat recovery systems (like those in our AKS designs that can recover 10-20% of otherwise lost heat) will perform significantly better against such benchmarks.
The consumption of protective atmosphere gases is typically the next most significant OPEX benchmark, especially for bright annealing processes or when treating materials sensitive to oxidation or decarburization. This can account for 15-25% of the total OPEX in such applications. Benchmarks here are often measured in terms of cubic meters (or cubic feet) of gas consumed per ton of product annealed or per hour of furnace operation under specific atmosphere conditions. A well-sealed furnace muffle or retort, coupled with an optimized gas flow control system that maintains the correct positive pressure and atmosphere composition without excessive leakage or purging, will demonstrate superior performance against these benchmarks. We often help clients audit their gas consumption and identify areas for improvement, such as optimizing door curtain efficiency or ensuring muffle integrity.
Furnace Type Example | Illustrative CAPEX Range | Typical Annual OPEX as % of Initial CAPEX | Dominant OPEX Factors (% of Total OPEX) |
---|---|---|---|
Continuous Bright Annealing (Steel) | $1M - $5M+ | 20-35% | Energy (45-60%), Protective Gas (15-25%), Maintenance (10-15%), Labor (10-15%) |
Batch-Type Bogie Hearth (Castings) | $300k - $2M | 15-30% | Energy (50-65%), Labor (loading/maint.) (15-25%), Maintenance (10-20%) |
Bell-Type Annealing (Wire Coils) | $400k - $1.5M | 18-30% | Energy (40-55%), Protective Gas (20-30%), Cycle Time Efficiency (Labor/Util.) (10-20%) |
Vacuum Annealing (Specialty Metals) | $750k - $6M+ | 15-25% | Energy (electricity for heat & vacuum) (60-75%), High-Skill Labor & Maint. (20-30%) |
Mesh Belt Furnace (Small Parts) | $200k - $1.2M | 25-40% | Energy (40-55%), Belt Replacement & Maint. (20-30%), Labor (15-20%) |
(Note: These are indicative figures and can vary significantly based on specific application, location, and operational practices.)
Benchmarking Maintenance and Labor Costs
Maintenance costs, which include spare parts, lubricants, and the labor associated with both preventive and corrective repair work, typically constitute around 10% to 15% of the annual OPEX for annealing furnaces. However, this figure can be misleading if not viewed in context. A company with a robust and proactive preventive maintenance (PM) program might show slightly higher scheduled maintenance costs in its budget, but it will almost certainly experience significantly lower costs associated with unplanned downtime, emergency repairs, and premature component failure. Best-in-class operations often track Key Performance Indicators (KPIs) such as Mean Time Between Failures (MTBF) for critical components (e.g., heating elements, drive systems) and Mean Time To Repair (MTTR). These metrics, when compared against industry or supplier-provided benchmarks, offer a more nuanced view of maintenance effectiveness than just the total maintenance spend. For example, if the MTBF for radiant tubes in a particular furnace type is benchmarked at 3 years, but a facility is replacing them every 18 months, it signals an issue that needs investigation (e.g., operational parameters, material quality, or combustion tuning).
Labor costs directly attributable to furnace operation (supervision, loading/unloading, monitoring) and routine maintenance can range from 10% to 20% of total OPEX. This is highly dependent on the level of automation designed into the annealing line and the prevailing local labor rates. A modern, fully automated continuous annealing line might require only one supervisor to oversee its operation per shift, whereas older, more manual batch furnaces might need several operators for material handling and cycle management. When benchmarking labor costs, it is often more insightful to look at the labor cost per ton of material annealed or labor hours per cycle, rather than just the absolute annual labor expenditure. This normalizes for production volume and provides a better comparison of operational efficiency.
It's crucial to approach all these benchmarks with a degree of critical thinking. A company might proudly report a very low maintenance OPEX, but if this is achieved by consistently deferring necessary upkeep or using substandard spare parts, it could be a precursor to catastrophic equipment failure and much higher long-term costs, including the potential for premature CAPEX for furnace replacement. True benchmarking involves understanding the operational context behind the numbers and striving for sustainable, efficient, and reliable operations rather than just chasing a specific percentage. When we at AKS Furnace deliver a new system, we provide our clients with guidance on expected maintenance schedules, recommended spare parts consumption rates, and typical energy performance, helping them establish their own internal benchmarks rooted in best practices for that specific equipment.
Energy is the largest OPEX componentTrue
Industry data shows energy typically accounts for 40-60% of total annual operational expenditure for annealing furnaces.
All furnace types have same OPEX/CAPEX ratioFalse
The ratio varies significantly by furnace type - vacuum annealing may have 15-25% OPEX/CAPEX while mesh belt furnaces can reach 25-40%.
What strategic recommendations can reduce both CAPEX and OPEX in the annealing process?
Are you constantly under pressure to enhance cost-efficiency in your annealing operations? Merely cutting budgets can jeopardize quality and long-term viability. Effective cost reduction requires strategic interventions that thoughtfully address both initial investments and ongoing operational expenses.
Strategic recommendations to reduce CAPEX and OPEX in annealing processes include adopting modular and scalable furnace designs for phased CAPEX, investing in high-efficiency technologies and robust automation to lower OPEX, optimizing process parameters for resource conservation, and embracing predictive maintenance and strong supplier collaborations.
The quest to reduce costs in the annealing process is a universal objective for nearly every metal processor I collaborate with, from sprawling stainless steel mills in Asia to specialized automotive component manufacturers in Europe. However, the most impactful and sustainable strategies are those that don't just target one side of the cost equation in isolation. Instead, they holistically address both the initial capital outlay (CAPEX) for the furnace line and the long-term, day-to-day running costs (OPEX). It’s about cultivating a synergy where intelligent upfront investments pave the way for sustained operational savings. At AKS Furnace, our core philosophy is that genuine, lasting cost reduction stems from innovation in design, heightened efficiency, and proactive, intelligent management, rather than from merely trimming budgets or compromising on quality. For instance, consider the decision to invest slightly more CAPEX in an advanced PLC-based control system with sophisticated data logging and recipe management. This initial outlay can yield significant and ongoing OPEX benefits through optimized energy consumption, minimized protective gas usage, reduced human error leading to less scrap, and more consistent product quality. It's about identifying and implementing these "win-win" scenarios where smart planning and technological adoption lead to tangible, measurable savings across the entire lifecycle of the annealing asset, thereby bolstering not only the bottom line but also overall operational excellence and competitiveness.
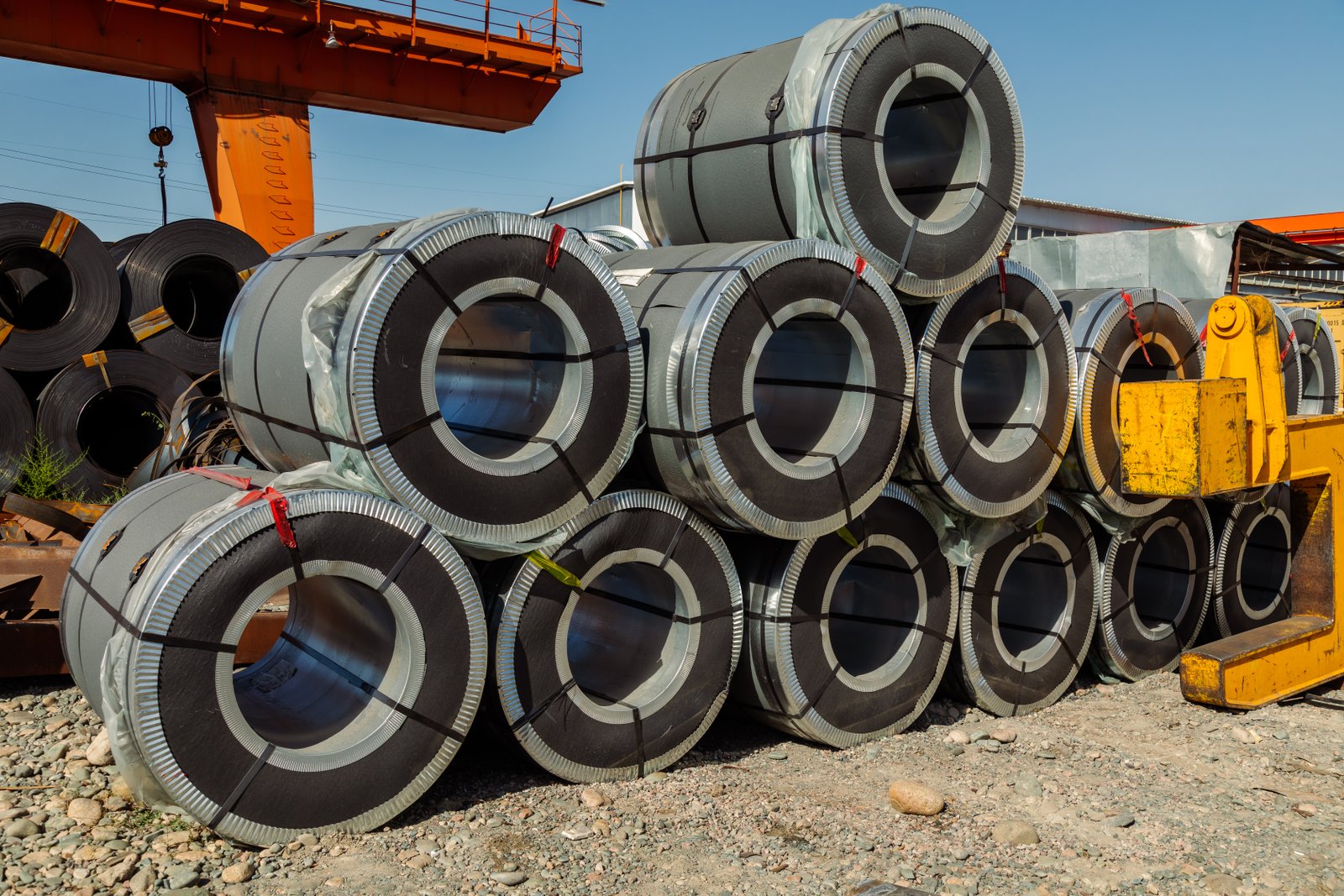
Reducing both Capital Expenditure (CAPEX) and Operational Expenditure (OPEX) in the annealing process requires a multifaceted, strategic approach rather than isolated cost-cutting measures. It’s about making intelligent, informed decisions at every stage, from initial furnace selection and design to daily operation and long-term maintenance. At AKS Furnace, we champion strategies that enhance overall value and efficiency, leading to sustainable cost reductions. These recommendations aim to create a virtuous cycle where smart investments lead to leaner operations, and efficient operations prolong the value of those investments. Let's explore some key strategic pillars for achieving this dual cost reduction.
Smart CAPEX Strategies for Initial Cost Control and Future Flexibility
One highly effective strategy for managing initial CAPEX without compromising future potential is to explore modular furnace designs and phased investment plans. Instead of a massive, upfront commitment to a line designed for peak future capacity (which may be years away or uncertain), a modular approach allows businesses to scale their investment with their growth. For example, a company might begin with a core heating and soaking section of a continuous annealing line, designed with connection points and control system architecture that readily accommodates the later addition of advanced pre-heating modules, rapid cooling sections, or enhanced automation features as production demand increases or new product specifications arise. We recently worked with an expanding manufacturer of aluminum profiles. They started with a basic AKS annealing furnace and, two years later, seamlessly integrated an additional controlled cooling zone and an automated handling system, spreading their CAPEX while ensuring their initial investment was future-proof. This approach minimizes the initial financial burden and reduces the risk associated with large, monolithic investments.
Another CAPEX consideration is thoroughly evaluating "right-sized" versus "over-specified" equipment. While some contingency for growth is wise, over-specifying a furnace far beyond foreseeable needs leads to inflated CAPEX and potentially higher OPEX due to inefficient operation at low throughput. A detailed analysis of current and projected (e.g., 3-5 year) production requirements, including material types, dimensions, and required metallurgical properties, is crucial. Sometimes, investing in two smaller, more flexible lines might offer better overall CAPEX and OPEX efficiency than one excessively large line, especially if product mixes are diverse or production schedules vary significantly. Furthermore, strategic sourcing and negotiation with reputable suppliers like AKS Furnace can yield CAPEX efficiencies. This goes beyond just the price; it includes evaluating the total package – warranty terms, included training, installation support, and the availability of local technical assistance. Bundling services or negotiating multi-unit purchases can often lead to better overall value.
Finally, actively exploring available financial incentives and grants for energy-efficient technologies can directly reduce net CAPEX. Many governments and regional authorities offer tax credits, rebates, or low-interest loans for investments in equipment that demonstrably reduces energy consumption or emissions. Modern annealing furnaces, particularly those from AKS Furnace incorporating waste heat recovery and optimized combustion systems, often qualify for such programs. We make it a point to inform our clients about these potential opportunities, as leveraging them can significantly ease the initial financial outlay.
OPEX Reduction through Technological Advancement and Process Optimization
The most significant and sustainable OPEX reductions often stem from investing in energy-efficient technologies upfront (a CAPEX decision with direct OPEX impact). Key areas include:
- Advanced Insulation and Sealing: Utilizing multi-layer, high-performance refractory and insulation materials minimizes heat loss through the furnace shell, directly reducing the energy needed to maintain temperature. Ensuring all doors, inspection ports, and muffle connections are meticulously sealed prevents heat leakage and uncontrolled air ingress (which can also increase protective gas consumption).
- High-Efficiency Heating Systems: For gas-fired furnaces, this means regenerative or recuperative burners that recover waste heat from flue gases to preheat combustion air, significantly improving fuel efficiency (our AKS systems can achieve 15-25% fuel savings this way). For electric furnaces, it involves optimally designed heating elements (e.g., silicon carbide, molybdenum disilicide) and power control systems (e.g., thyristor-based, phase-angle firing) that maximize heat transfer and minimize electrical losses.
- Precise Process Control and Automation: Sophisticated PLC/SCADA systems allow for precise control over temperature profiles, ramp rates, soak times, and atmosphere composition. This not only ensures consistent product quality but also optimizes energy and gas consumption by avoiding over-processing or excessive purging. Automated recipe management reduces the chance of human error. I recall a client in the white goods sector who, after upgrading to an AKS bright annealing line with advanced process control, reduced their natural gas consumption per ton of steel by 12% and their reject rate due to inconsistent annealing by 3%.
Process parameter optimization is another critical lever for OPEX reduction. This involves systematically analyzing and fine-tuning annealing cycles for each specific alloy and product type to achieve the desired metallurgical properties using the minimum necessary energy, time, and protective atmosphere. This can be achieved through Design of Experiments (DOE), leveraging historical production data, or using simulation tools. For example, reducing soak times by even a few minutes per cycle, if metallurgically permissible, can lead to substantial energy savings and increased throughput over a year. Similarly, optimizing protective gas flow rates to the minimum required to maintain atmosphere integrity without wastage is key.
Implementing a robust predictive maintenance (PdM) strategy, potentially augmented by IoT sensors and AI-driven analytics, can drastically cut OPEX associated with unplanned downtime, emergency repairs, and inefficient reactive maintenance. Instead of relying solely on fixed-schedule preventive maintenance or waiting for components to fail, PdM monitors the real-time health and performance of critical furnace components (e.g., motors, fans, heating elements, vacuum pumps). By detecting subtle anomalies or degradation patterns, it can predict impending failures, allowing maintenance to be scheduled proactively at the most convenient time, with necessary parts already on hand. While PdM systems require an initial CAPEX (for sensors, software, and integration), studies by leading consultancies like Deloitte and PwC have shown they can reduce overall maintenance costs by 25-30%, cut unplanned downtime by up to 70%, and extend equipment life by 20-40%.
Strategic Recommendation | Primary Impact Area | Secondary Impact Area(s) | Example Implementation & Benefit |
---|---|---|---|
Modular/Scalable Furnace Design | CAPEX Reduction | Phased OPEX, Future Agility | Start with core unit, add modules (e.g., advanced cooling) as demand grows; avoids over-investment. |
Investment in High-Efficiency Technologies (Waste Heat Recovery, Advanced Burners/Elements, Superior Insulation) | OPEX Reduction (Energy) | CAPEX (Slight Increase Potential), Environmental | Significant (10-25%) annual energy savings, faster ROI, reduced carbon footprint. |
Advanced Automation & Process Control | OPEX Reduction (Labor, Materials, Energy) | Quality Improvement, Throughput | Minimized human error, reduced scrap, optimized cycle times, consistent product. |
Comprehensive Process Parameter Optimization | OPEX Reduction (Energy, Gas, Time) | Throughput, Quality | Data-driven fine-tuning of cycles for specific alloys, minimizing resource use per unit. |
Shift from Preventive to Predictive Maintenance (PdM) | OPEX Reduction (Maintenance, Downtime) | CAPEX (Initial for System), Asset Life | AI/IoT monitors equipment health, predicts failures, optimizes maintenance, drastically cuts unplanned stops. |
Strong Supplier Partnerships & Collaboration | CAPEX/OPEX Synergy | Support, Innovation | Favorable terms, bundled services, ongoing technical support, shared insights for continuous improvement. |
Leveraging Partnerships and a Culture of Continuous Improvement
Forging strong, collaborative, long-term partnerships with knowledgeable equipment suppliers like AKS Furnace can yield significant benefits for both CAPEX and OPEX. Beyond the initial transaction, a true partner provides ongoing technical support, shares best practices, offers insights on process optimization, and keeps clients informed about relevant technological advancements or upgrade opportunities. We often work with our clients well past the commissioning phase, helping them analyze their furnace performance data, troubleshoot operational challenges, and identify further efficiency gains. This collaborative approach can lead to preferential terms for future investments or spare parts, access to specialized expertise, and a more responsive service when issues arise, all contributing to better lifecycle cost management.
Cultivating an internal culture of continuous improvement (Kaizen) within your own operational and maintenance teams is equally vital. Empowering employees at all levels to identify inefficiencies, suggest improvements, and participate in problem-solving can uncover a wealth of small but cumulative savings. This could range from optimizing furnace loading patterns to improve heat transfer in batch operations, to meticulously checking for and sealing minor air leaks in atmosphere piping or furnace seals, to suggesting modifications in maintenance procedures that reduce time or resource consumption. Regular training, clear communication channels for suggestions, and recognition for implemented improvements are key to fostering such a culture.
Finally, regularly reviewing and benchmarking your annealing process performance against established internal targets, historical data, and (where possible) anonymized industry best practices is crucial for sustained cost reduction. This involves consistently tracking Key Performance Indicators (KPIs) such as:
- Energy consumption per ton of product (kWh/ton or m³ gas/ton).
- Protective gas consumption per ton or per cycle.
- Furnace uptime and availability.
- Mean Time Between Failures (MTBF) and Mean Time To Repair (MTTR).
- Scrap or rework rates attributable to annealing issues.
- Total maintenance cost as a percentage of asset replacement value. By setting ambitious but achievable targets for these KPIs and continuously striving to meet or exceed them through targeted initiatives, companies can systematically drive down both CAPEX (by making more informed decisions for future upgrades or replacements based on proven needs) and OPEX (through ongoing operational excellence and efficiency gains). This holistic, data-driven approach ensures that cost reduction efforts are not one-off projects but an embedded part of the organizational DNA, contributing directly to enhanced competitiveness and profitability.
Modular designs reduce CAPEXTrue
Modular furnace designs allow phased investments, spreading CAPEX over time while maintaining future expansion capabilities.
Over-specifying saves OPEXFalse
Over-specified equipment often leads to higher OPEX due to inefficient operation at low throughput levels.
Conclusion
Successfully navigating annealing furnace investments hinges on clearly differentiating CAPEX's initial outlay from OPEX's recurring costs. Strategic planning, embracing energy-efficient technologies, optimizing processes, and proactive maintenance are crucial for balancing these expenditures, thereby maximizing ROI and ensuring robust, long-term operational performance in heat treatment.
-
Learn about the financial impacts of upfront versus ongoing costs ↩
-
Understand the economic advantage of higher CAPEX with reduced OPEX ↩
-
Discover the lifespan and maintenance frequency of furnace components ↩
-
Understand factors influencing ongoing operational expenses ↩
-
Discover how automation reduces human-related operational expenses ↩
-
Discover the advantages of real-time monitoring for operational efficiency ↩
-
Understand the sophisticated technology and benefits of vacuum annealing furnaces ↩
-
Learn how your furnace's energy efficiency compares to industry standards ↩