How Is AI-Enabled Predictive Maintenance Transforming Copper Annealing Processes?
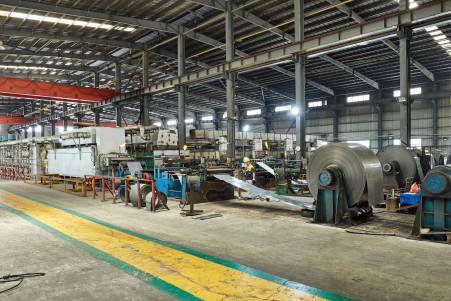
Is unexpected furnace downtime disrupting your copper annealing operations and inflating costs? The constant worry over production delays and material waste can be overwhelming. AI-enabled predictive maintenance offers a powerful solution, transforming your reactive repair cycle into a proactive strategy for seamless, continuous production.
AI-enabled predictive maintenance is revolutionizing copper annealing by leveraging machine learning to analyze real-time sensor data from furnaces. This approach accurately predicts potential equipment failures, optimizes maintenance schedules, minimizes unplanned downtime, and enhances the final product's quality and consistency, driving significant operational improvements.
This shift from a "fix it when it breaks" model to a "predict and prevent" paradigm is more than just a technological upgrade; it's a fundamental change in how we manage our most critical production assets. But how does this technology actually work within the harsh environment of a furnace? We're about to explore the core components of this transformation—from intelligent sensors to edge computing1—and reveal how they are becoming indispensable for modern copper producers.
The move towards predictive maintenance is driven by the convergence of the Industrial Internet of Things (IIoT), affordable high-fidelity sensors, and sophisticated AI algorithms. For copper producers, where temperature precision and atmospheric integrity are paramount, this isn't merely an option—it's a strategic necessity. The cost of a single unplanned shutdown can easily run into tens of thousands of dollars in lost output and emergency labor. Traditional preventive maintenance, based on fixed schedules, often leads to replacing parts too early or, worse, failing to catch a component that degrades faster than expected. AI-driven predictive maintenance provides a dynamic, data-informed approach, ensuring that every action is justified and every potential failure is anticipated.
How is AI integrated into copper annealing for predictive maintenance?
The thought of integrating a complex AI system into your tried-and-true annealing furnaces can seem overwhelming. You might be concerned about compatibility with existing machinery, the high cost, and whether the return on investment is truly justifiable for your specific copper processing line.
AI is integrated into copper annealing through the deployment of advanced sensors that collect real-time operational data like temperature, vibration, and gas composition. Machine learning models then process this data to identify patterns preceding equipment failure, automatically generating precise maintenance alerts and optimizing furnace parameters.
This integration is far less about a complete overhaul and more about a strategic enhancement of your existing assets. It's not a matter of simply bolting on a new piece of technology, but rather of giving your furnace a "nervous system" that can feel, interpret, and react to its own health in real time. The process begins with identifying the most critical components and common failure points within your furnace—be it the heating elements, circulation fans, or conveyor mechanisms. From there, we map the key data signatures that indicate good health versus impending trouble. For instance, we once helped a client in Southeast Asia who was battling inconsistent annealing results and frequent heater burnouts in their continuous strip line. Their journey into AI began not with a massive investment, but with a targeted project to monitor the electrical current and thermal signatures of their heating elements. This practical, problem-solving approach demystifies AI, showing it as a powerful tool to address tangible production challenges. It's about building a digital replica of your furnace's core systems, allowing AI to predict outcomes and prescribe actions, turning abstract data into concrete operational value.
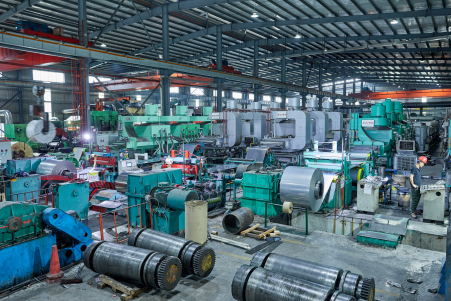
The integration of AI into the demanding environment of copper annealing is a multi-layered process that transforms raw data into actionable intelligence. It builds upon the foundations of modern industrial automation, adding a predictive analytical layer that elevates furnace management from reactive to prescriptive. This journey involves three core stages: establishing a robust data foundation, deploying intelligent analytical models, and translating predictions into concrete maintenance actions. Each stage is critical to building a system that not only foresees problems but actively contributes to operational excellence and a stronger bottom line. The ultimate goal is to create a closed-loop system where the furnace can, in some cases, even self-adjust to prolong its own operational life while awaiting maintenance.
The Foundational Layer: Data Acquisition and Sensor Fusion
The first step in any successful AI integration is comprehensive data acquisition. In a copper annealing furnace, this means going beyond basic temperature readouts. We install a suite of sensors to capture a holistic view of the machine's health. This includes vibration sensors on fan motors and gearboxes, acoustic sensors to detect gas leaks or mechanical stress, thermal imaging cameras to map heat distribution, and high-precision gas analyzers to monitor the integrity of the protective atmosphere. Each sensor provides a single stream of data, but the real power comes from a concept called "sensor fusion."
Sensor fusion is the process of combining data from multiple disparate sources to create a more accurate and insightful picture than any single sensor could provide. For example, an AI model might correlate a minor increase in a fan motor's vibration (from a vibration sensor) with a subtle 2°C temperature fluctuation in a specific heating zone (from a thermal camera) and a slight change in power consumption (from an electrical monitor). Individually, these signals might be dismissed as normal operational noise. Fused together, however, they create a clear signature that points to an impending bearing failure, allowing maintenance to be scheduled weeks in advance.
This approach has delivered tangible results. A client of ours producing high-conductivity copper wire for the electric vehicle (EV) market was struggling with microscopic surface imperfections that impacted the wire's final performance. Their traditional PID controllers couldn't respond to the subtle atmospheric fluctuations within their Bright Annealing Furnace. By integrating high-sensitivity oxygen sensors with our AI platform, the system could predict atmospheric imbalances up to 15 minutes before they occurred, allowing for proactive adjustments. According to their internal reports, this single application of sensor fusion reduced their product defect rate by 8%.
The Analytical Core: Machine Learning Models at Work
Once the data is flowing, the next step is analysis. This is where machine learning (ML), a subset of AI, comes into play. The system isn't programmed with fixed rules; instead, it learns from the data. We typically employ several types of ML models. Anomaly detection algorithms constantly watch for data patterns that deviate from the established "normal operation" baseline. Regression models are used to predict the "remaining useful life" (RUL) of a component, such as a heating element or a conveyor belt. Classification algorithms can diagnose a specific type of fault once an anomaly is detected, telling technicians whether the issue is electrical, mechanical, or chemical.
The effectiveness of these models hinges on the quality and quantity of the data used to "train" them. Initially, the AI is trained on historical data from the furnace, including past failure records, maintenance logs, and quality control reports. The more data the model processes, the more accurate its predictions become. Over time, the system continuously learns from new, live data, refining its understanding of the furnace's unique operational characteristics. This is why a company's own historical data is so valuable—it captures the specific nuances of their machines and processes.
The impact of this analytical power is well-documented. Leading industry analysts like Deloitte have found that AI-driven predictive maintenance can increase equipment uptime by 10-20% and reduce overall maintenance costs by 5-10%. In our own AKS Furnace
installations equipped with these systems, we have consistently seen clients achieve up to a 15% reduction in unplanned downtime within the first year of implementation, a direct and significant boost to their production capacity.
The Actionable Output: From Prediction to Prescription
The final and most important stage is turning analytical insights into clear, actionable instructions. A prediction is useless if the maintenance team doesn't know what to do with it. A mature AI system moves beyond prediction to prescription. Instead of a vague alert like "High Vibration Detected," the system generates a detailed work order: "Warning: Fan motor bearing in Cooling Zone 3 shows a vibration signature consistent with 85% wear. Recommend replacement during the next scheduled production stop. Part Number: XYZ-123."
This level of detail allows maintenance teams to plan their work efficiently, order parts in advance, and schedule repairs during planned downtime, eliminating the chaos and high cost of emergency interventions. To visualize the difference, consider the following comparison:
Aspect | Traditional Maintenance (Preventive/Reactive) | AI-Enabled Predictive Maintenance |
---|---|---|
Timing | Fixed schedule or after failure occurs | Real-time, based on actual equipment condition |
Decision Basis | Manual inspection, generic manufacturer guidelines | Data-driven algorithms, historical performance |
Outcome | Unnecessary parts replacement or unexpected downtime | Optimized maintenance, maximized uptime |
Cost | High costs from downtime and premature replacements | Lower total cost through efficiency and prevention |
The ultimate evolution of this process is the self-optimizing furnace. In our most advanced Bright Annealing Furnace models, the AI can take temporary corrective actions autonomously. For example, if it predicts that a heating element is degrading, it might slightly reduce the line speed and adjust the power in adjacent zones to maintain the copper's heat treatment profile, prolonging the component's life until a scheduled repair can be performed—all without compromising the quality of the final product. This represents a true closed-loop, intelligent manufacturing system.
AI predicts furnace failuresTrue
AI analyzes sensor data to identify patterns that precede equipment failures, enabling proactive maintenance.
AI replaces all furnace partsFalse
AI optimizes maintenance schedules but doesn't automatically replace parts - technicians still perform the actual maintenance.
What role do AI sensors play in improving copper annealing processes?
Your standard furnace sensors provide basic operational data, but they often miss the subtle changes that precede a drop in quality or a mechanical failure. This leaves you operating partially blind, forced to react to problems like surface oxidation only after a valuable batch is compromised.
AI sensors play a pivotal role by capturing high-fidelity, real-time data on furnace conditions, including thermal distribution, acoustic signatures, vibration, and atmospheric purity. This granular data feeds machine learning models to not only predict maintenance but also to actively optimize the annealing process for superior copper quality.
Think of the difference between a simple thermometer and a full-body thermal imaging scan. A standard thermocouple gives you a single temperature reading, but an AI-enabled thermal imaging sensor maps the entire heating chamber in real-time, identifying hotspots or cold spots that lead to uneven annealing and internal stresses in the copper strip. This level of insight transforms the furnace from a passive heating box into an active, intelligent environment. We worked with a major copper foil manufacturer whose primary challenge was achieving absolute uniformity in ductility for their electronics-grade products. By retrofitting their Bell-Type Annealing Furnace2 with an array of our acoustic and vibration sensors, the AI system could literally "hear" and "feel" the subtle changes in the main circulation fan that correlated with temperature non-uniformity across the coil. This capability went far beyond simple maintenance; it became a live quality control tool. The rich data streams from these advanced sensors unlock a new frontier of process control, enabling adjustments so precise that they were previously impossible. We will now explore the specific sensor types that are making this happen.
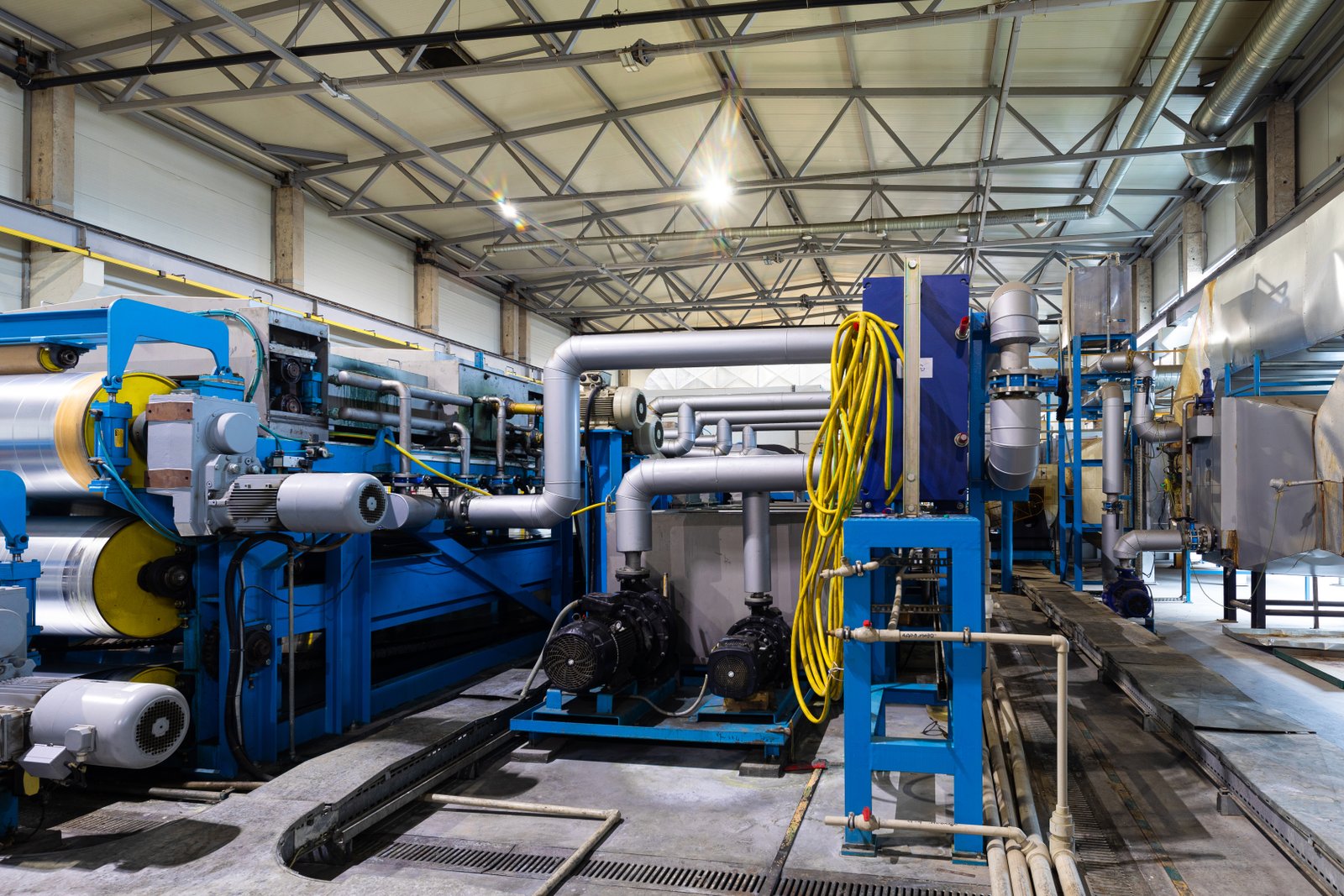
The integration of AI-powered sensors3 is arguably the most critical element in modernizing the copper annealing process. These devices are the sensory organs of the furnace's "brain"—the AI model—and their precision determines the quality of the insights generated. Unlike their traditional counterparts that provide simple, often lagging, data points, AI-ready sensors deliver high-frequency, multi-dimensional data streams. This rich information allows for the detection of not just impending failures but also subtle process deviations that impact the metallurgical properties of the final product. By focusing on three key areas—thermal and acoustic uniformity, atmospheric integrity, and mechanical health—these sensors provide a comprehensive, real-time understanding of the entire annealing ecosystem.
Beyond Temperature: Thermal and Acoustic Sensing for Uniformity
Achieving a uniform grain structure and consistent mechanical properties in copper requires exceptionally stable and uniform heating. Traditional single-point thermocouples provide an incomplete picture. We now utilize advanced thermal imaging cameras that create a detailed, real-time heat map of the entire copper strip as it moves through a continuous annealing furnace. The AI analyzes this thermal data, pixel by pixel, to detect temperature deviations of less than a degree. This allows the system to automatically adjust power to individual heating elements in different zones, ensuring a perfectly consistent thermal profile across the strip's width.
This technology has proven invaluable for our clients in high-stakes industries. A customer in Taiwan producing ultra-thin copper foils for 5G-grade printed circuit boards (PCBs) used this system in their Bright Annealing Furnace. For their application, even a 1-2°C temperature variance across the foil could negatively impact the performance of the final electronic component. Our integrated thermal imaging system, driven by an AI control loop, enabled them to maintain a cross-strip temperature deviation of less than ±0.5°C. This directly led to a measurable increase in their A-grade product yield and a reduction in customer rejections.
Furthermore, we employ acoustic sensors that act like digital stethoscopes, continuously listening to the furnace's operational sounds. These sensors can distinguish the normal hum of a healthy motor from the high-frequency whine of a bearing that's beginning to fail or the distinct sound signature of a gas leak. This auditory data provides an early warning system for issues that vibration sensors alone might miss, adding another layer of predictive capability to the system.
Gas and Atmosphere Integrity: The Key to a Bright Finish
For applications requiring a flawless, mirror-like surface, the protective atmosphere inside the furnace is critical. In a bright annealing process, a carefully controlled mixture of hydrogen and nitrogen is used to prevent any oxidation on the copper's surface. Even trace amounts of oxygen or moisture can cause discoloration and tarnish, rendering the product useless for decorative or high-tech applications. Traditional systems might measure the overall gas flow, but they can't provide a real-time analysis of the atmosphere's composition inside the chamber.
To solve this, we use AI-powered laser gas analyzers. These sensors provide instantaneous, highly accurate measurements of the gas composition, detecting contaminants like oxygen and water vapor at parts-per-million (ppm) levels. Industry standards dictate that for a true bright finish on copper, oxygen levels must be kept below 5 ppm. Our AI systems continuously monitor this, correlating any slight increase with operational events. For instance, the AI can learn to differentiate between a brief oxygen spike caused by the furnace door opening and a gradual, persistent increase that indicates a developing micro-crack in the furnace muffle or a failing seal.
This isn't just a quality control tool; it's a powerful maintenance predictor. By pinpointing the likely source and severity of an atmospheric leak, the system directs maintenance crews to the exact location of the problem, saving hours of diagnostic guesswork. It ensures that the bright finish promised to the customer is delivered with every single batch.
Mechanical Health: Vibration and Stress Monitoring
The mechanical systems of an annealing furnace, from the conveyor belts in a Mesh Belt Furnace to the tension rollers in a continuous strip line, are subjected to immense thermal and mechanical stress. A sudden failure in these systems is often catastrophic, leading to costly damage and extended downtime. AI-powered vibration sensors are the frontline defense against such events. Attached to motors, gearboxes, and roller bearings, these sensors measure vibration across multiple axes at a high frequency.
The AI model is trained on the unique vibration signature of each component when it's operating in a healthy state. It then watches for any deviation from this baseline. The specific changes in frequency and amplitude can tell a detailed story, allowing the AI to distinguish between a simple misalignment, a lubrication issue, or the final stages of bearing degradation. This allows for precise planning of repairs. Below is a breakdown of how different sensors contribute to the overall process.
Sensor Type | Data Monitored | Predictive Capability | Impact on Copper Quality |
---|---|---|---|
Thermal Imaging Camera | Full surface temperature map | Predicts heating element failure, identifies hotspots | Ensures uniform grain structure and ductility |
Acoustic Sensor | Machine sound frequencies | Detects gas leaks, early mechanical wear | Prevents surface defects from atmospheric issues |
Laser Gas Analyzer | O₂, H₂O, H₂, N₂ composition (ppm) | Predicts seal/muffle integrity failure | Guarantees a bright, non-oxidized surface finish |
Vibration Sensor | Motor/bearing frequency & amplitude | Predicts mechanical failure in drives/fans | Prevents strip marks from jerky conveyor movement |
A client producing copper tubing for HVAC systems utilized our Bogie Hearth Annealing Furnace for large batch treatments. They had previously been plagued by unexpected failures of the bogie's drive mechanism, which would scrap entire multi-ton loads. After installing our predictive maintenance system with integrated vibration sensors, they received a 4-week warning before a critical gearbox was projected to fail. This allowed them to schedule the repair during a planned holiday shutdown, saving an estimated $80,000 in lost product and emergency repair costs.
AI sensors detect subtle process deviationsTrue
AI sensors capture high-fidelity data to identify minor variations in thermal distribution, acoustic signatures, and atmospheric conditions that traditional sensors miss.
Standard thermocouples provide complete thermal dataFalse
Traditional single-point thermocouples only give localized temperature readings, while AI thermal imaging maps the entire heating chamber for uniform annealing.
How does edge data enhance the efficiency of predictive maintenance in copper annealing?
Sending colossal streams of sensor data to a distant cloud for analysis sounds slow, expensive, and insecure. You're right to worry that the network lag could cause you to miss a critical failure alert, and that your sensitive production data is vulnerable off-site.
Edge data processing dramatically enhances predictive maintenance efficiency by analyzing raw sensor data directly at the furnace. This approach minimizes latency for real-time alerts, reduces data transmission costs, improves data security by keeping it on-premises, and allows the system to function even without an internet connection.
Let's use a simple analogy. Cloud computing is like a large, central public library; to get an answer, you must send your book (your data) there, wait for the librarian to read it, and send the summary back. Edge computing, on the other hand, is like having an expert librarian sitting right next to your bookshelf who reads the book instantly and just tells you the most important findings. For time-sensitive industrial processes like copper annealing, this speed is not a luxury—it's a requirement. Imagine a critical pressure spike inside a Vacuum Annealing Furnace4. Sending that data point to the cloud for analysis might introduce a delay of a few seconds. In that brief window, a catastrophic failure could occur. An edge device processes that spike in milliseconds, triggering an immediate shutdown protocol or pressure release. I recall a client in a region with unstable internet who was hesitant about AI. We implemented an edge-first strategy where over 90% of the analytics happened on a small industrial computer right on the furnace. This gave them the full power of AI without dependency on the outside world.
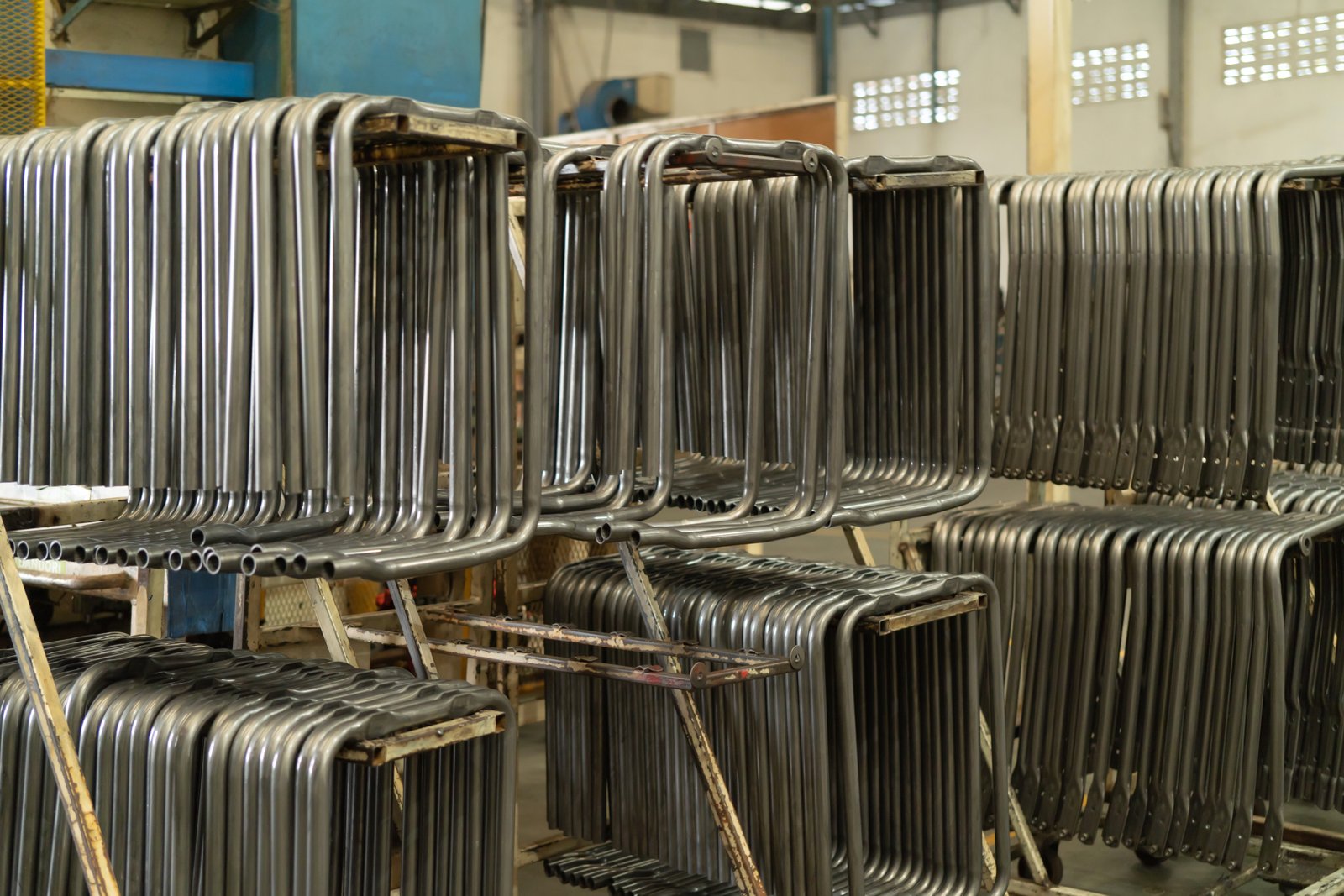
The adoption of edge computing is a pivotal evolution in the architecture of industrial AI systems. It addresses the inherent limitations of a purely cloud-based model in a high-speed, high-stakes manufacturing environment. For copper annealing, where milliseconds matter, processing data at the "edge"—that is, locally, on or near the furnace itself—provides a faster, more secure, and more resilient solution. This localized intelligence ensures that the predictive maintenance system is not just a powerful analytical tool, but a responsive and reliable guardian of the production line. By focusing on real-time processing, enhanced data security, and operational resilience, the edge computing paradigm transforms how data is handled and leveraged for maximum efficiency.
The Need for Speed: Real-Time Processing and Reduced Latency
In manufacturing, latency—the delay between when data is captured and when a decision is made—is the enemy of efficiency and safety. Consider a modern continuous annealing line where a copper strip might be moving at 100 meters per minute. A 2-second delay in detecting a surface defect or a mechanical anomaly means over 3 meters of potentially scrap material has already been produced. A cloud-centric model, which involves sending data over a network, processing it in a remote data center, and sending a command back, inherently introduces latency.
Edge devices are small, ruggedized, and powerful industrial computers located right next to the furnace's control panel. They run optimized, "lightweight" versions of the AI models. These devices pre-process the torrent of raw data from the sensors, filtering out the operational noise and performing the initial analysis on the spot. This allows them to identify critical events and trigger immediate responses in milliseconds, not seconds. This is crucial for applications like controlling the precise gas-to-air ratio for our energy-saving combustion systems or making micro-adjustments to the cooling system to ensure perfect strip flatness.
The numbers clearly show this industry trend. According to extensive research from Gartner5, it is projected that by 2025, a staggering 75% of all enterprise-generated data will be created and processed outside of a traditional centralized data center or cloud. This monumental shift is driven by the absolute necessity for real-time insights in smart manufacturing. Within our own furnace control systems, we've benchmarked our edge processing modules as reducing the decision-making loop time from several seconds in a cloud model to under 50 milliseconds.
Enhancing Data Security and Reducing Costs
Your production data is one of your most valuable assets. It contains your intellectual property—the unique parameters and processes that give you a competitive edge. Transmitting this sensitive data to an external cloud server, no matter how secure, inherently introduces risk. It can be vulnerable to interception during transit or cyber-attacks on the data center. For our clients who manufacture components for sensitive sectors like aerospace, defense, or medical devices, data security is non-negotiable. Edge computing keeps this critical operational data on-premises, within the secure confines of the factory network.
Beyond security, there are significant cost implications. High-frequency sensors, such as those used for vibration analysis, can generate gigabytes of data every hour. Continuously streaming this volume of data to the cloud incurs substantial data transmission and storage costs. Edge computing offers a more economical model. The edge device analyzes the raw data locally and only transmits small, relevant packets of information—such as summary reports, key performance indicators, or critical failure alerts—to a central server or cloud dashboard for long-term storage and high-level analysis.
Factor | Cloud-Centric Computing | Edge Computing |
---|---|---|
Data Bandwidth Costs | High due to constant raw data streaming | Low, as only key insights/alerts are sent |
Latency | High (seconds), network dependent | Extremely Low (milliseconds), independent of network |
Data Security | Potential vulnerabilities in transit/cloud | High, as sensitive data stays on-premise |
Offline Functionality | None; requires constant internet connection | Full; system remains operational during outages |
For a medium-sized copper strip mill running three annealing lines, the savings on cloud bandwidth and storage costs from adopting an edge strategy can easily amount to thousands of dollars annually, providing a rapid return on the investment in edge hardware.
Building a Resilient and Autonomous System
What happens to a cloud-dependent predictive maintenance system when the factory's internet connection inevitably goes down? It stops working. The flow of data ceases, the analytics halt, and the furnace is effectively blind until the connection is restored. This is an unacceptable point of failure for any critical manufacturing operation. An edge-powered system, however, is designed for resilience. Because the processing happens locally, it can continue to monitor, analyze, and protect the furnace completely autonomously, even with zero internet connectivity.
This capability was a crucial selling point for a customer operating one of our Bogie Hearth Annealing Furnaces6 in a remote industrial park in India where internet service was notoriously unreliable. The edge computing module we installed ensured their predictive maintenance and process control systems functioned flawlessly 24/7. The device continued to log all data, monitor equipment health, and display real-time alerts on the local operator panel. Once internet connectivity was restored, it seamlessly synchronized a compressed summary of the event logs with their central management dashboard.
This level of autonomy is the foundational building block for the fully interconnected "smart factory" of Industry 4.0. As edge devices become even more powerful, they will enable inter-machine communication directly on the factory floor. Imagine the annealing furnace autonomously communicating with the upstream rolling mill and the downstream slitting line to self-optimize the entire production flow for maximum efficiency and quality. This is the resilient, intelligent, and efficient future that edge computing makes possible.
Edge computing reduces latencyTrue
Edge devices process data locally, enabling millisecond response times compared to cloud's second-long delays.
Cloud is more secure than edgeFalse
Edge computing keeps sensitive data on-premises, eliminating cloud transmission vulnerabilities and external attack surfaces.
What are the benefits of using AI-enabled predictive maintenance in the copper industry?
You're constantly under pressure to increase output and improve quality while keeping a close eye on your budget. Sticking with traditional, reactive maintenance methods feels like you're leaving money on the table, constantly one step behind the next unexpected breakdown.
The primary benefits of AI-enabled predictive maintenance in the copper industry are a significant reduction in unplanned downtime, enhanced product quality and consistency, improved operational safety, and lower overall maintenance and energy costs. This technology drives profitability by optimizing asset performance and resource utilization.
Adopting this forward-thinking strategy is not just about preventing failures; it's about unlocking new levels of operational excellence across your entire production process. By transforming maintenance from a costly, reactive necessity into a data-driven, strategic advantage, you can gain a significant competitive edge. For copper producers, where margins can be tight and quality standards are exacting, these benefits translate directly into a healthier bottom line and greater customer satisfaction. We’ve seen firsthand how our clients leverage this technology to move beyond simply producing copper to mastering the art of high-efficiency, high-quality copper manufacturing. The tangible returns are seen in everything from higher asset utilization rates to lower energy bills per ton of product. Let's now break down these key benefits into concrete, measurable advantages that impact your daily operations and long-term success.
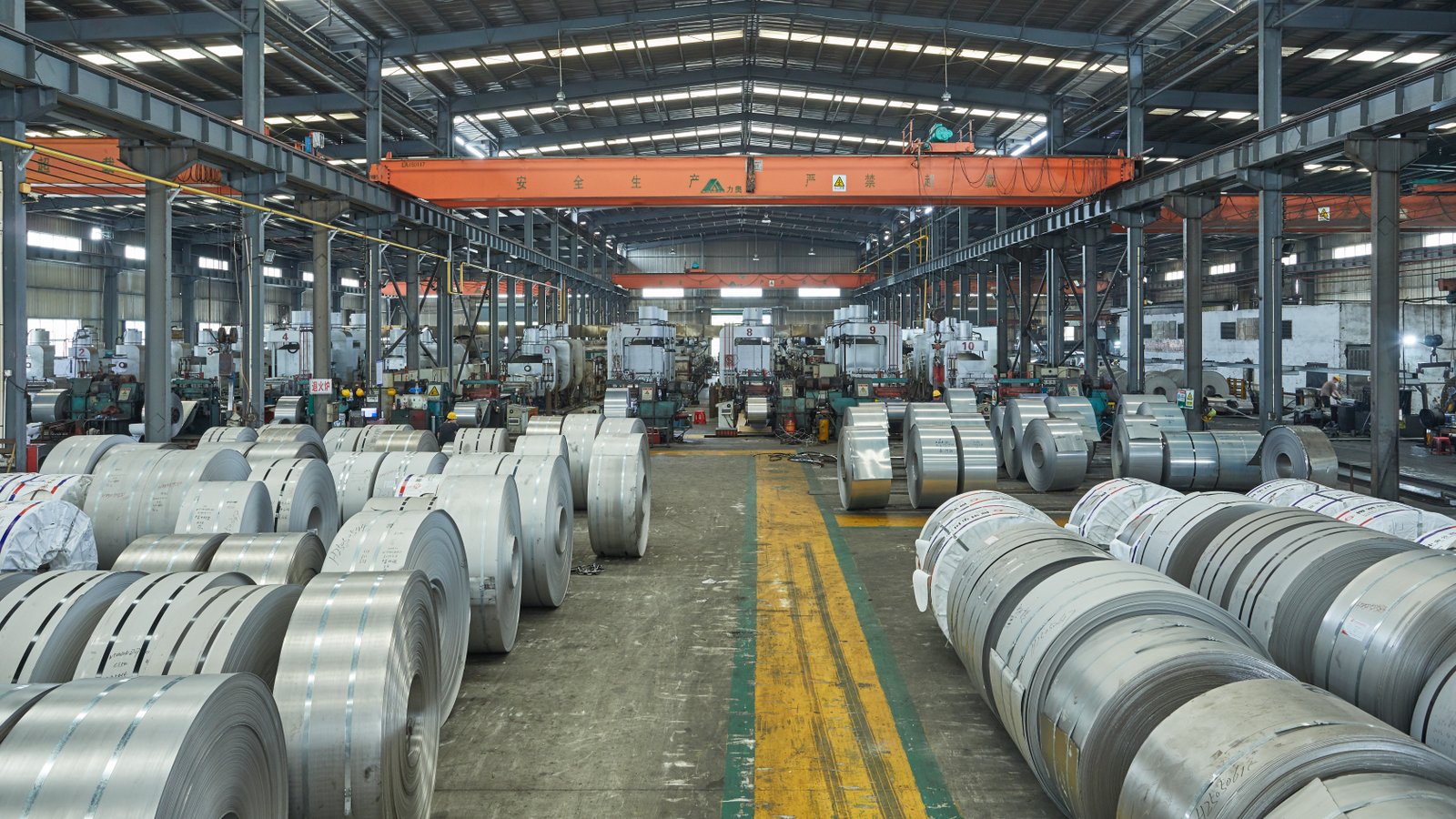
The implementation of an AI-driven predictive maintenance program delivers a cascade of benefits that permeate every facet of a copper annealing operation. It fundamentally re-engineers the relationship between man, machine, and process, shifting the focus from crisis management to strategic optimization. The value proposition extends far beyond simply fixing things before they break; it creates a more productive, predictable, and profitable manufacturing environment. By examining the four pillars of its benefits—maximized uptime, superior product quality, enhanced safety, and significant cost reduction—we can appreciate why this technology is becoming the new industry standard.
Maximized Uptime and Production Throughput
The most immediate and impactful benefit of predictive maintenance is the drastic reduction in unplanned downtime. In the copper industry, a single unexpected furnace shutdown can halt the entire production line, leading to massive losses. A reactive maintenance approach means that when a critical component like a circulation fan or a conveyor motor fails, the line stops dead. This is followed by a chaotic scramble for diagnoses, sourcing parts, and scheduling emergency repairs, all while production targets are being missed.
Predictive maintenance turns this scenario on its head. By analyzing data from vibration, thermal, and acoustic sensors, the AI can forecast a component failure weeks or even months in advance with a high degree of accuracy. For example, our system might alert a plant manager: "Main circulation fan motor in Furnace #2 shows a 90% probability of bearing failure within the next 250 operating hours." This foresight is transformative. It allows the maintenance team to order the necessary parts ahead of time and schedule the replacement during a planned shutdown, such as a weekend or a holiday.
The results speak for themselves. Industry studies, including those by the U.S. Department of Energy, have shown that a properly implemented predictive maintenance program can reduce unplanned outages by as much as 50%. For a medium-sized copper strip processor, this can equate to hundreds of extra production hours per year, directly increasing throughput and revenue without any additional capital investment in new machinery.
Superior Product Quality and Metallurgical Consistency
In copper annealing, consistent quality is paramount. Deviations in temperature, heating time, or atmospheric conditions can lead to inconsistent grain size, poor ductility, surface oxidation, or other defects that render the product out-of-spec. AI-enabled sensors and controls play a crucial role in moving beyond simple failure prediction to active quality assurance. The same sensors that predict maintenance needs also monitor the precise conditions of the annealing process in real time.
For instance, a traditional system might not flag a slight degradation in a door seal. However, an AI system using a sensitive gas analyzer will detect the minute amount of oxygen leaking into the furnace. It understands that while this won't cause an immediate breakdown, it will compromise the bright finish of the copper. The system can then alert operators to the quality risk or, in advanced setups, automatically increase the flow of the protective gas to compensate until a repair can be made. This ensures that every coil of copper strip meets the exact metallurgical specifications required by the customer.
A client manufacturing copper components for the electronics sector provides a compelling case. They used our AI system on their Mesh Belt Furnace7 to ensure uniform heat treatment of small, delicate parts. The AI's ability to maintain temperature uniformity across the belt to within ±1°C virtually eliminated batch-to-batch variations in hardness, increasing their acceptance rate with a major international customer by 12%.
Enhanced Operational Safety and Risk Mitigation
Industrial furnaces operate at extreme temperatures and often use combustible gases, making safety a top priority. Predictive maintenance significantly enhances workplace safety by identifying potentially hazardous conditions long before they escalate into dangerous incidents. A failing component, such as an overheating motor or a leaking gas valve, is not just a production issue; it's a safety risk.
The AI system serves as a vigilant, 24/7 safety watch. For example, acoustic sensors can detect the unique ultrasonic signature of a high-pressure gas leak that would be inaudible to the human ear. Vibration analysis can identify severe mechanical stress in a rotating part that could lead to a catastrophic failure and flying debris. By providing early warnings for these conditions, the system allows for proactive intervention, protecting personnel and assets from harm.
Consider the following table which contrasts the risk profiles of different maintenance strategies:
Risk Category | Reactive Maintenance | Preventive Maintenance (Scheduled) | Predictive Maintenance (AI-Driven) |
---|---|---|---|
Mechanical Failure | High risk of sudden, catastrophic failure | Risk reduced, but unexpected failures still occur | Lowest risk, as degradation is tracked |
Gas Leak/Fire | High risk, detection only after the event | Moderate risk, relies on periodic manual checks | Lowest risk, continuous monitoring detects anomalies |
Operator Safety | High exposure during emergency repairs | Moderate exposure during scheduled downtime | Lowest exposure, planned and controlled interventions |
By reducing the number of emergency repair situations, which are often rushed and performed under high-pressure conditions, predictive maintenance creates a safer, more controlled, and less stressful work environment for the maintenance staff.
Significant Cost Reduction and Energy Efficiency
While implementing an AI system requires an initial investment, the long-term cost savings are substantial. These savings come from multiple areas. Firstly, maintenance labor is used far more efficiently. Instead of reacting to emergencies, technicians work on planned, scheduled tasks. Secondly, spare parts inventory can be optimized. There's no need to stockpile expensive components "just in case," because the system provides ample warning to order parts as needed. This reduces carrying costs and prevents waste from obsolete parts.
Most importantly, predictive maintenance directly contributes to energy efficiency, a core feature of our AKS Furnaces. An optimally running furnace is an energy-efficient furnace. For example, the AI can detect if heating elements are becoming inefficient or if heat is escaping due to seal degradation. By flagging these issues early, the system helps maintain the furnace's peak thermal efficiency, reducing gas or electricity consumption per ton of copper produced. Our Waste Heat Recovery systems become even more effective when the core furnace operation is kept at its optimal state by the AI.
A case study from one of our European clients using a Bright Annealing Furnace8 for stainless steel (a similar high-energy process) showed that after implementing our AI predictive maintenance module, they achieved a 6% reduction in their annual energy consumption for that line. This was attributed to the AI's ability to identify and correct inefficiencies in the heating and atmospheric systems long before they would have been caught by traditional methods.
Predictive maintenance reduces unplanned downtimeTrue
AI-enabled predictive maintenance can forecast equipment failures weeks in advance, allowing for planned repairs and reducing unexpected shutdowns by up to 50%.
Predictive maintenance increases energy costsFalse
Actually, predictive maintenance improves energy efficiency by identifying and correcting inefficiencies in furnace operations, leading to reduced energy consumption per ton of product.
How can copper annealing companies implement AI sensors and edge data effectively?
You understand the benefits of AI and edge computing, but the path to implementation seems complex and uncertain. You're wondering where to start, what technology to choose, and how to ensure the project delivers real value without disrupting your current operations.
Effective implementation involves a phased approach: start with a strategic audit of critical assets and failure points, launch a targeted pilot project on a single furnace to prove ROI, and then scale the solution across the facility while focusing on continuous data-driven improvement and team training.
Successfully integrating this technology is not a one-time event, but a strategic journey. It’s about building a culture of data-driven decision-making, not just installing new hardware. The goal is to start small, demonstrate clear and measurable wins, and then build momentum for a wider rollout. I always advise our clients to avoid a "boil the ocean" approach. Instead of trying to connect every sensor on every machine at once, we identify the single most painful problem—the one that causes the most downtime or quality issues—and we solve that first. This creates a powerful success story that gets buy-in from everyone, from the plant floor operators to the executive team. This focused, methodical approach de-risks the investment and ensures that each step forward is built on a solid foundation of proven results. The following phases provide a clear roadmap for any copper producer looking to embark on this transformative path.
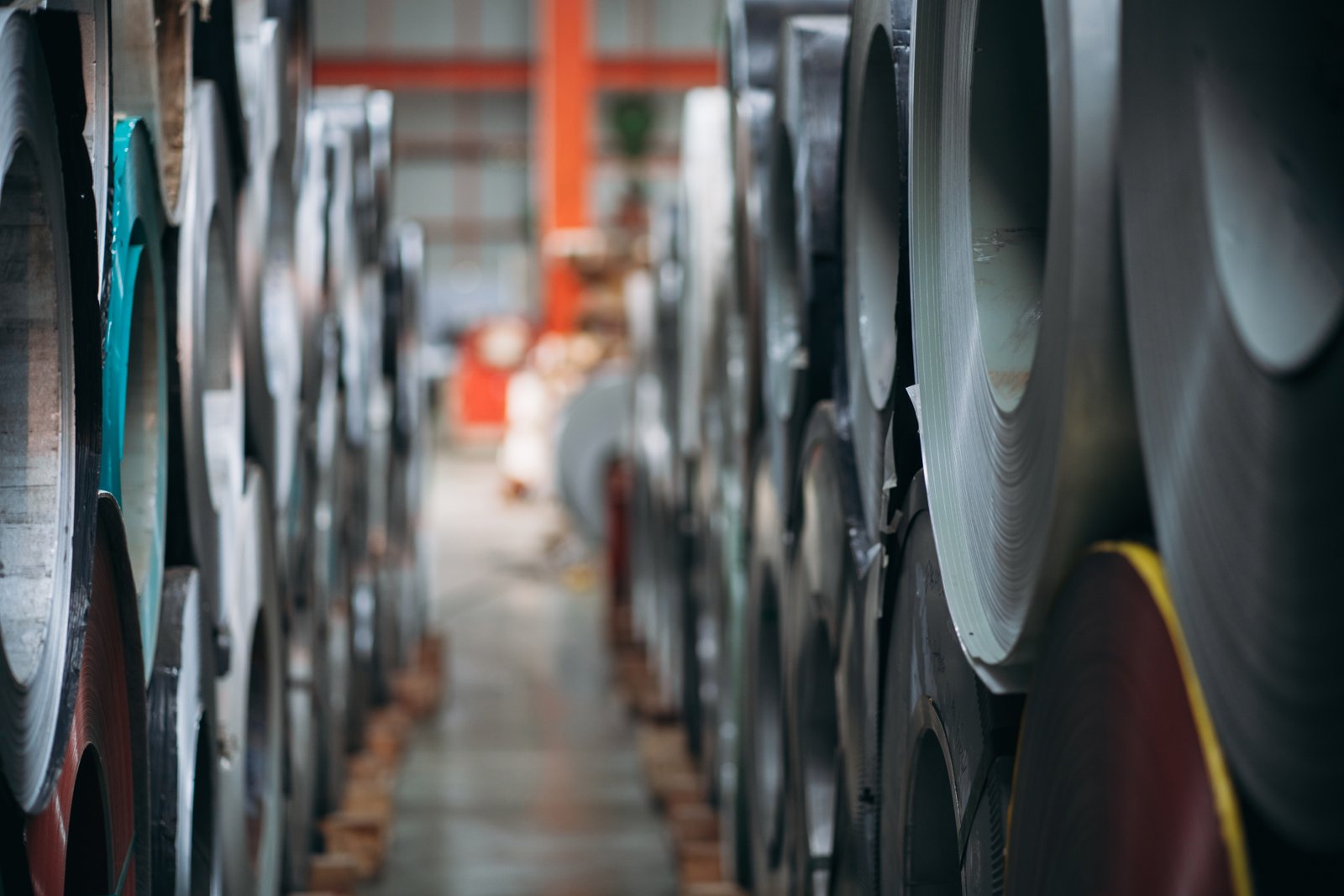
Deploying an AI-driven predictive maintenance system9 powered by smart sensors and edge computing requires a clear, structured methodology. A haphazard approach can lead to wasted investment, unreliable results, and disillusionment with the technology. At AKS, we guide our clients through a three-phase implementation framework designed to be pragmatic, scalable, and value-focused. This roadmap—encompassing a strategic audit, a controlled pilot program, and an intelligent scaled deployment—ensures that the solution is tailored to the unique challenges of each facility and delivers a tangible return on investment at every stage. It transforms the implementation from a daunting technological overhaul into a manageable and rewarding business initiative.
Phase 1: Strategic Audit and Opportunity Assessment
The first and most critical phase is to understand where to focus your efforts. Not all equipment failures have the same impact. The goal of this phase is to identify the "low-hanging fruit"—the assets where predictive maintenance will deliver the biggest and fastest return. This process begins with a collaborative workshop involving plant managers, maintenance supervisors, and furnace operators. We work together to conduct a Failure Modes and Effects Analysis (FMEA)10 for the key annealing furnaces. We ask critical questions: Which components fail most frequently? Which failures cause the most significant downtime? Which issues are most detrimental to copper quality?
Based on this analysis, we create a prioritized list of assets and failure modes to target. For a client with a continuous Bright Annealing Furnace, this might be the main drive motor for the conveyor system. For a company running multiple Bell-Type Annealing Furnaces, it might be the circulation fans that are critical for temperature uniformity. Alongside identifying the physical assets, we audit the existing data infrastructure. What sensors are already in place? What data is being collected in the existing SCADA or PLC systems? What are the network capabilities?
This audit results in a clear strategic roadmap. It defines the primary business objective (e.g., "Reduce unplanned downtime on Line 1 by 10% within 6 months"), specifies the target equipment, and outlines the necessary sensors and data points required. For example, the plan might state: "Install vibration and temperature sensors on the gearbox of the primary decoiler and feed data into an edge device to predict bearing failures." This clarity is essential for defining the scope and success criteria of the subsequent pilot project.
Phase 2: Pilot Program and Technology Selection
With a clear strategy in place, the next step is to prove the concept with a limited-scope pilot project. This is where theory meets practice. The pilot should be focused on the top-priority asset identified in Phase 1. This approach minimizes initial investment and risk while providing a real-world environment to test the technology and validate the business case. During this phase, we select and install the appropriate AI-ready sensors (vibration, acoustic, thermal, etc.) and the edge computing hardware.
The focus here is on data collection and model training. For the first few weeks, the system operates in a "listening mode," collecting baseline data on the healthy operation of the target component. This data is used to train the initial machine learning model. Once the model is trained, it begins to generate predictive insights. The key is to run the new predictive system in parallel with existing maintenance practices. The maintenance team can then compare the AI's predictions with their own inspections and findings, building trust and confidence in the system's accuracy.
We implemented a pilot program with a client in the Middle East for their Bogie Hearth Annealing Furnace. The target was the furnace's main exhaust fan, which had a history of unpredictable failures. Within two months, the pilot system provided a three-week advance warning of an impending motor failure. The maintenance team was initially skeptical but performed an inspection and confirmed the advanced wear. The successful, verified prediction provided the indisputable proof of value needed to secure management approval for a full-scale deployment.
Phase 3: Scaled Deployment and Continuous Improvement
Once the pilot project has successfully demonstrated its value and delivered a clear ROI, the final phase is to scale the solution. This can involve rolling out the system to other critical assets, other production lines, or even other facilities. The lessons learned during the pilot phase—regarding sensor placement, model tuning, and integration with workflow—are invaluable for ensuring a smooth and efficient expansion. A key part of this phase is integrating the AI's outputs into the company's existing Computerized Maintenance Management System (CMMS)11. This automates the process of generating work orders, making the insights directly actionable for the maintenance team.
However, implementation doesn't end with installation. The most successful AI systems are those that are part of a continuous improvement loop. The AI models should be periodically retrained with new data to adapt to changes in equipment, processes, or environmental conditions. Operator and technician feedback is crucial. Are the alerts clear? Is the interface easy to use? Are the insights leading to the right actions? This feedback loop ensures the system evolves and continues to deliver value over the long term.
A key aspect of this phase is training and cultural adoption. We provide comprehensive training to ensure that the maintenance and operations teams understand how to interpret the data and trust the system's recommendations. The goal is to shift the culture from reactive firefighting to proactive, data-driven problem-solving. This long-term vision of a continuously learning and improving system is what truly transforms an operation and secures a lasting competitive advantage.
Implementation Phase | Key Activities | Primary Outcome |
---|---|---|
Phase 1: Audit | FMEA, identify critical assets, audit existing data infrastructure | A prioritized roadmap with clear business objectives |
Phase 2: Pilot | Select & install hardware, collect data, train & validate AI model | Proven ROI on a single asset, team buy-in |
Phase 3: Scale | Roll out to more assets, integrate with CMMS, train staff, establish a continuous improvement loop | Plant-wide operational efficiency and a data-driven culture |
Start with a strategic auditTrue
The article emphasizes beginning with a Failure Modes and Effects Analysis (FMEA) to identify critical assets before implementation.
Install sensors on all equipment firstFalse
The recommended approach is to start with a targeted pilot on the most critical asset, not blanket sensor deployment.
Conclusion
Ultimately, adopting AI-powered predictive maintenance, driven by smart sensors and responsive edge computing, is no longer a futuristic vision. It is a practical, achievable strategy for transforming copper annealing operations, moving them from a reactive footing to a proactive, intelligent, and highly efficient model.
-
Understand how sensors and edge computing enhance operational efficiency ↩
-
Learn how these sensors improve temperature uniformity and maintenance predictions. ↩
-
Discover how AI sensors improve process control and product quality. ↩
-
Learn how Vacuum Annealing Furnaces prevent oxidation and improve metal quality ↩
-
Understand how Gartner views the growing trend of edge computing in industries ↩
-
Discover how Bogie Hearth Annealing Furnaces benefit industrial manufacturing ↩
-
Learn about uniform heat treatment techniques used in copper manufacturing. ↩
-
Explore the benefits of Bright Annealing Furnaces in metal processing and energy efficiency. ↩
-
Learn how predictive maintenance systems can save time and costs using AI technology ↩
-
Understand FMEA's role in identifying and prioritizing potential risks in industrial processes ↩
-
Explore benefits of CMMS in improving efficiency and maintenance scheduling ↩